In the new pattern of the manufacturing industry, where global competition and personalized demands are intertwined, leading metal stamping enterprises are reconstructing the industrial value chain through in – depth customized services. Centered around technological innovation, this article analyzes how modern metal stamping enterprises build precise customized solutions for customers in multiple fields through materials engineering, process optimization, and digital services.
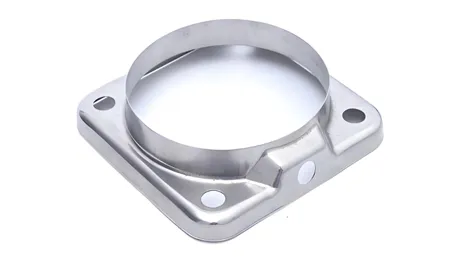
The core competitiveness of top – tier metal stamping enterprises starts with the precise control and innovative research of material properties:
- High – strength and lightweight customization: Develop aluminum – silicon – coated steel sheets (with a tensile strength of 1500MPa) for new energy vehicle enterprises, achieving a 30% weight reduction of the battery tray while meeting collision safety standards.
- Functional composite innovation: Customize copper – graphene composite heat sinks for 5G base stations, with a thermal conductivity of 580W/m·K, a 45% increase compared to traditional solutions.
- Breakthrough in special scenarios: In the medical field, adopt titanium – alloy – polymer laminated stamping technology to achieve dual optimization of biocompatibility and structural strength for implantable devices.
Based on the technology roadmaps of industry – leading enterprises, modern customized services form three core modules:
- Flexible Mold System
- Modular combined molds can complete model changeovers within 72 hours and are compatible with materials with a thickness of 0.1 – 12mm.
- The service life of self – lubricating nano – coated molds exceeds 5 million stamping strokes, reducing maintenance costs by 40%.
- Dynamic Forming Technology
- The multi – axis linkage system driven by servo motors enables intelligent adjustment of the stamping speed from 0.01 – 1500mm/s, and the forming accuracy of complex curved surfaces is ±0.02mm.
- The laser real – time compensation system automatically corrects springback errors, increasing the first – piece qualification rate to 98.5%.
- Composite Process Integration
- The integrated production line of stamping – welding – surface treatment shortens the delivery cycle of automotive structural parts by 60%.
- Micro – connection point technology enables the automatic sorting of progressive dies, reducing the production cost of small – batch orders by 35%.
- New Energy Vehicle Field
- Integrated motor housing stamping: Use multi – station transfer die technology, with a deep – drawing ratio of 3:1 for 8 – mm – thick aluminum alloy, reducing the welding process by 85%.
- Battery module connectors: Precision stamping of ultra – thin copper alloy (0.08mm), with a resistivity ≤ 1.7μΩ·cm, improving temperature rise control by 30%.
- Consumer Electronics Field
- Folding – screen hinge components: 18 precision stamping processes achieve a 0.01 – mm – level matching accuracy and pass 200,000 folding tests.
- Smart wearable device antennas: The LDS laser – forming stamping process increases integration by 70% compared to traditional solutions.
- Industrial Equipment Field
- Semiconductor vacuum chambers: Mirror stamping technology achieves a surface accuracy of Ra ≤ 0.05μm and a cleanliness level of Class 1.
- Robot reducer components: The progressive stamping hardening process enables a fatigue life of more than 30,000 hours.
- Intelligent Interaction Platform
- Online process simulation system: Upload a 3D model to automatically generate a feasibility report and provide a prototype cost estimate within 48 hours.
- AR remote collaboration system: Allows customers to view the production line status in real – time and participate in process reviews.
- Data – driven Optimization
- A million – level stamping parameter database: AI automatically matches the optimal process plan, shortening the debugging time by 80%.
- Blockchain – based quality traceability: Each stamping part can be queried for the full – process process data and inspection reports.
- Sustainable Customized Solutions
- Waste recycling system: The metal recovery rate is 99.3%, reducing the carbon footprint by 40%.
- Water – based lubrication process: Achieves zero VOC emissions and reduces cleaning water consumption by 90%.
To improve the efficiency of customers’ technological decision – making, industry – leading enterprises have built three enabling systems:
- Agile prototyping center: Supports rapid sample – making within 72 hours, with a minimum order quantity reduced to 50 pieces.
- Technology sharing platform: Opens more than 200 industry – solution documents such as the “New Energy Vehicle Stamping Technology White Paper”.
- Full – life – cycle management: Provides closed – loop technical services from material selection to scrapping and recycling.
(Note: The technical parameters in this article are quoted from the technical reports of the International Stamping Association and enterprise engineering verification data. Feasibility demonstrations need to be carried out according to specific projects for implementation.)