In the field of modern industrial manufacturing, surface treatment technology plays a crucial role in the performance, lifespan, and appearance of parts. The deep integration of CNC (Computer Numerical Control) technology and anodizing process provides an innovative solution for customizing high – precision and high – reliability metal parts. This article will systematically analyze the technical logic and engineering value of custom CNC anodized parts from dimensions such as technical advantages, materials engineering, processing techniques, quality control, and industry applications.
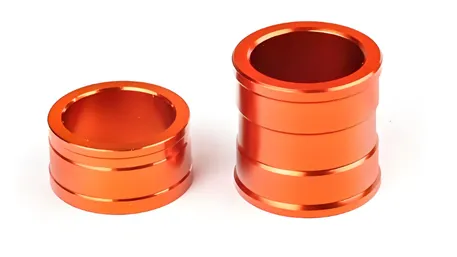
The combination of CNC technology and anodizing process brings three core values to metal parts:
- The positioning accuracy of CNC machine tools can reach ±0.005mm, the repeat positioning accuracy is ±0.01mm, and the surface roughness Ra≤0.8μm, ensuring the precise structure of parts.
- The anodizing process forms a dense oxide film (thickness 5 – 50μm) on the metal surface. The hardness can reach HV300 – 500, and the corrosion resistance is improved by more than 10 times. It can pass a 1000 – hour salt – spray test without rust.
- Five – axis linkage CNC equipment can process spatial curved surfaces, thin – wall structures (wall thickness ≤ 0.5mm), and micro – features that are difficult to achieve with traditional processes, such as the special – shaped terminals of electronic connectors.
- The anodizing process can evenly cover the complex surfaces processed by CNC, ensuring the consistency of the film layer and avoiding local corrosion or wear.
- CNC processing realizes the personalized structural design of parts. The anodizing process meets the appearance requirements through coloring processes (such as black, blue, gold), and the film thickness can be customized to optimize insulation or wear resistance.
Material selection is the basis of customizing anodized parts and needs to be combined with the anodizing effect and working – condition requirements:
- 6061 Aluminum Alloy: It has excellent comprehensive properties. After anodizing, the film layer is uniform, which is suitable for mechanical structural parts and automotive parts.
- 7075 Aluminum Alloy: It has high strength (tensile strength ≥ 572MPa), and the oxide film has high hardness, which is suitable for high – load scenarios such as aerospace.
- 1060 Pure Aluminum: With a purity of ≥ 99.6%, the oxide film has high transparency and is often used for mirror anodizing of optical instrument parts.
- Titanium Alloy (TC4): Anodizing can form a colored film layer and improve corrosion resistance at the same time, which is suitable for medical implants.
- Magnesium Alloy (AZ31): The oxide film can enhance corrosion resistance and is used for lightweight electronic device housings.
- Milling Processing: Five – axis linkage milling of complex curved surfaces, such as the fin structure of aluminum alloy heat sinks. The dimensional tolerance is ±0.01mm, and the surface roughness Ra≤0.8μm.
- Turning Processing: Processing of shaft – type parts, such as aluminum alloy screws. The roundness error is ≤ 0.003mm, providing a high – quality base for subsequent anodizing.
- Drilling and Tapping: Precision hole processing (hole diameter tolerance ±0.01mm) ensures the sealing and wear resistance of threads after anodizing.
- Pretreatment: Degreasing and pickling are carried out to remove surface oil and oxide layers, ensuring the adhesion of the film layer.
- Anodizing: An electric current is applied in a sulfuric acid electrolyte, and the voltage and time are controlled to form an oxide film of a predetermined thickness (such as a hard – anodized film thickness of 50μm).
- Coloring and Sealing: Color customization is achieved through electrolytic coloring or organic dyeing, and sealing treatment (such as boiling – water sealing) is carried out to improve the weather resistance of the film layer.
- A coordinate measuring machine (CMM) is used to detect key dimensions. For example, the hole – position tolerance of an aluminum alloy bracket is ≤ ±0.01mm.
- Geometric tolerance detection: flatness ≤ 0.02mm/m, perpendicularity ≤ 0.01mm, ensuring the assembly accuracy of parts.
- Film Thickness Detection: An eddy – current thickness gauge is used to measure the oxide film thickness, with an error of ≤ ±2μm.
- Hardness Test: A micro – hardness tester is used to detect the film hardness. The hardness of a hard – anodized film is ≥ HV300.
- Corrosion – Resistance Test: Verified by a neutral salt – spray test (NSS). For example, an oxidized 316L stainless – steel part needs to pass a 1000 – hour test without rust.
- A colorimeter is used to detect the coloring consistency, with ΔE≤1.0.
- Insulation Test: The insulation resistance of the oxide film is ≥ 10^10Ω·cm, which is suitable for electronic parts.
- Custom – made aluminum alloy (6061) electronic housings are milled by CNC and black – anodized. The film thickness is 15μm, improving corrosion resistance and presenting an upscale appearance, which is suitable for mobile phones and tablets.
- Copper – alloy connector terminals are anodized after precision CNC processing. The film thickness is 8μm, the insertion and extraction life reaches more than 5000 times, and the contact resistance is ≤ 5mΩ.
- 7075 aluminum alloy automotive wheels are milled by CNC and anodized, reducing the weight by 30%. The film thickness is 25μm, and the weather resistance reaches more than 10 years, combining lightweight and aesthetics.
- Titanium – alloy aerospace fasteners are anodized. The film thickness is 10μm, and the fatigue – resistance performance is doubled, ensuring flight safety.
- Pure aluminum (1060) optical brackets are processed by CNC and transparently anodized. The film thickness is 5μm, and the light transmittance is ≥ 90%, ensuring the stability of optical components.
- Magnesium – alloy medical device housings are anodized. The film thickness is 12μm, and they can resist salt – water corrosion for 500 hours, meeting the requirements of the medical environment.
- How to choose the thickness of the anodized film?
It needs to be determined according to the use: the film thickness for ordinary decorative anodizing is 5 – 15μm, for hard anodizing is 25 – 50μm, and for insulating anodizing is 10 – 20μm.
- What colors can anodizing achieve?
Common colors include black, blue, red, gold, etc. A variety of colors can be customized through electrolytic coloring or organic dyeing. For special requirements, Pantone color matching can be provided.
- How about the wear – resistance of the oxide film?
The hardness of the hard – anodized film can reach HV500, and the wear – resistance is 3 – 5 times that of untreated metals, which is suitable for moving parts or high – wear scenarios.
- Will anodizing after CNC processing affect the dimensional accuracy?
The thickness of the anodized film is controllable. By reserving a margin of 0.02 – 0.05mm during processing, the final dimensions can be ensured to meet the tolerance requirements.
- Which metals are suitable for anodizing?
Mainly aluminum and its alloys, followed by metals such as titanium and magnesium. Materials such as steel require special treatment and are usually not directly anodized.
Inquire now and get a customized solution!
Whether it is the precision housings of electronic devices, the lightweight parts of automobiles, or the high – reliability parts of aerospace, our professional team will rely on the high – precision processing of CNC technology and the surface – treatment advantages of anodizing to provide you with a full – process customization service from design, processing to inspection. Click to leave a message, and let us, with a rigorous technical system and innovative process solutions, customize high – performance and high – appearance anodized parts for your project, helping you stand out in the market competition!