The automotive transmission bracket, a crucial component of the vehicle’s drivetrain, plays vital roles in supporting, damping vibrations, and transmitting power. As the automotive industry evolves towards lightweight and high-reliability designs, die castings have become the mainstream choice for manufacturing transmission brackets due to their superior forming accuracy and comprehensive performance. This article will provide an in-depth analysis of the customization technology for automotive transmission bracket die castings from a professional perspective, offering you a glimpse into the charm of precision manufacturing.
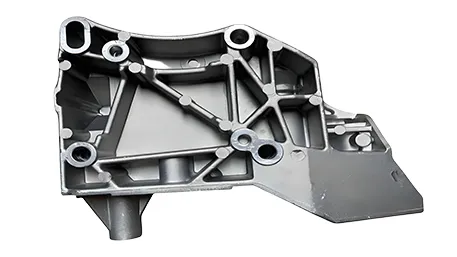
- Automotive Transmission Bracket Die Castings: The “Stable Foundation” of Vehicle Drivetrains
- Custom Material Selection: Precise Matching of Material Properties and Working Conditions
- Precision Manufacturing Processes: The Transformation from Liquid Metal to High-Precision Parts
- Core Technological Breakthroughs: Overcoming Complex Structural and Performance Challenges
- Stringent Quality Control: Ensuring the Reliable Quality of Every Product
- Custom Service Process: Full-Cycle Guarantee to Meet Diverse Needs
- Frequently Asked Questions: Professional Interpretation of Automotive Transmission Bracket Die Castings
During vehicle operation, the automotive transmission bracket bears the weight of the engine and transmission, the torque generated by power transmission, as well as the impact and vibration from road bumps. Thanks to the advantage of integrated molding, die castings can meet the requirements of complex structural designs while ensuring the strength, stiffness, and dimensional stability of parts. This effectively reduces noise and vibration, enhancing the driving experience and vehicle reliability. Statistics show that using die-cast transmission brackets can reduce the vibration amplitude of the drivetrain by 20% – 30%, significantly extending the service life of key vehicle components.
- High Strength and Lightweight: With a tensile strength of 300 – 350MPa and a density of only 2.6 – 2.8g/cm³, compared with traditional cast iron materials, it can reduce the weight of parts by 30% – 40%. This effectively reduces the vehicle’s curb weight and improves fuel economy. For example, after an electric vehicle adopted an aluminum alloy die-cast transmission bracket, its cruising range increased by about 5%.
- Good Thermal Conductivity: The thermal conductivity is 180 – 237W/(m·K), which can quickly dissipate the heat generated during the operation of the transmission, preventing performance degradation caused by overheating and ensuring the stable operation of the drivetrain.
- Excellent Corrosion Resistance: After surface treatments such as anodizing and electrophoretic coating, it can maintain good corrosion resistance in harsh environments such as humidity and acid-base conditions, extending the service life of parts.
- Extreme Lightweight: With a density as low as 1.74 – 1.85g/cm³, it is one of the lightest metallic structural materials applied in the automotive field. Transmission brackets die-cast from magnesium alloys can further reduce vehicle weight, especially suitable for high-performance sports cars and electric vehicles with extremely high lightweight requirements, helping to improve vehicle acceleration performance and reduce energy consumption.
- Good Damping Performance: It can effectively absorb vibration energy, reducing drivetrain noise and enhancing in-vehicle quietness. Test data shows that magnesium alloy brackets can reduce transmission vibration noise by 10 – 15 decibels.
- High Specific Strength and Specific Stiffness: While ensuring lightweight, it meets the high-strength and high-rigidity requirements of the bracket, ensuring reliable performance under complex working conditions.
- 3D Modeling and Simulation Analysis: Using CAD/CAM/CAE software, 3D models are created based on the structural characteristics and performance requirements of the transmission bracket. Mold flow analysis (Moldflow) is employed to simulate the filling and solidification processes of the molten metal, predicting potential defects such as shrinkage holes, gas holes, and deformation. This optimizes the mold structure and gating system design. For example, by adjusting the position and size of the ingate, the filling time of the molten metal can be shortened by 15% – 20%, effectively reducing problems such as cold shuts and short shots.
- High-Precision Mold Machining: Advanced processes such as five-axis CNC machining centers and electrical discharge machining are used to manufacture molds. The key dimensional accuracy is controlled within ±0.01mm, and the surface roughness of the mold is Ra≤0.4μm, ensuring the dimensional accuracy and surface quality of die castings. High-quality H13 steel is selected as the mold material, and through heat treatment processes such as quenching, tempering, and nitriding, the hardness, wear resistance, and service life of the mold are improved. Generally, the mold life can reach 500,000 – 1,000,000 shots.
- Cold Chamber Die Casting Process: Due to the large size and complex structure of automotive transmission brackets, cold chamber die casting machines are usually used for production. The injection speed can reach 5 – 10m/s, and the injection pressure is 80 – 150MPa, ensuring that the molten metal fills the mold cavity quickly and evenly to form a dense internal structure. At the same time, by controlling the mold temperature (150 – 250°C for aluminum alloy die casting and 180 – 280°C for magnesium alloy die casting) and the pouring temperature of the molten metal (620 – 720°C for aluminum alloy and 640 – 680°C for magnesium alloy), the molding quality of the castings is optimized.
- Vacuum Die Casting Technology: A vacuum system is introduced during the die casting process to evacuate the gas in the mold cavity, making the vacuum degree reach 50 – 100mbar. This effectively reduces defects such as gas holes and porosity inside the castings, improving the density and mechanical properties of the castings. Tests show that for transmission brackets produced by vacuum die casting, the internal porosity can be reduced to less than 0.5%, and the tensile strength is increased by 10% – 15%.
- Deburring and Surface Cleaning: Processes such as sandblasting, shot blasting, and vibratory finishing are used to remove burrs, flash, and oxide scale on the surface of die castings, making the surface smooth and flat, providing a good foundation for subsequent processing and surface treatment.
- Machining and Dimensional Correction: CNC machining centers are used to perform machining operations such as drilling, milling, and boring on die castings, precisely correcting the dimensions and geometric tolerances of parts to meet assembly requirements. The key dimensional accuracy can reach ±0.03mm, and the flatness is ≤0.05mm/100mm.
- Surface Treatment: According to the use environment and performance requirements, surface treatments such as anodizing, electrophoretic coating, and powder coating are applied to die castings to enhance the corrosion resistance, wear resistance, and aesthetics of the parts. For example, the electrophoretic coating has a uniform thickness (usually 15 – 25μm) and strong adhesion, enabling the bracket to withstand 1000 hours of salt spray testing without corrosion.
- Topology Optimization: Using topology optimization software such as Altair Inspire, based on the stress distribution of the bracket, the part structure is optimized under the premise of meeting strength and stiffness requirements, removing redundant materials to achieve the lightweight goal. After optimization, the weight of the transmission bracket can be reduced by 15% – 20% without sacrificing performance.
- Rib and Reinforcement Structure Design: By reasonably arranging ribs and reinforcing structures, the anti-deformation ability and stability of the bracket are improved. For example, adding arc-shaped ribs in the stress-concentrated area of the bracket can reduce the stress concentration in this area by 30% – 40%.
- Datum Surface Design and Machining: The datum surface of the part is determined during the mold design stage. After die casting, high-precision machining is used to ensure the flatness and surface roughness of the datum surface, providing an accurate positioning reference for subsequent assembly. The flatness of the datum surface is controlled within ±0.01mm, ensuring the precise assembly of the bracket with components such as the transmission and engine.
- Precision Control of Location Pins and Mounting Holes: The dimensional accuracy and position accuracy of location pin holes and mounting holes directly affect the assembly quality and service performance of the bracket. High-precision processing equipment and detection means are used to control the dimensional tolerance of the holes within ±0.02mm and the position tolerance within ±0.03mm, ensuring the installation accuracy and reliability of the bracket.
- Finite Element Analysis (FEA): Using finite element analysis software such as ANSYS and ABAQUS, the stress, strain, vibration, etc. of the transmission bracket under different working conditions are simulated and analyzed to evaluate the performance and reliability of the parts, guiding design optimization. For example, by simulating working conditions such as sudden acceleration and sudden braking of the vehicle, potential weak points of the bracket can be discovered in advance and improved.
- Fatigue Life Prediction: Combining the fatigue characteristics of materials and actual working conditions, fatigue analysis software is used to predict the fatigue life of the bracket, providing a basis for product maintenance and replacement. Test verification shows that the error between the predicted result and the actual service life can be controlled within 10%.
- Chemical Composition Analysis: Spectral analyzers are used to detect the chemical composition of each batch of aluminum alloy and magnesium alloy raw materials, ensuring that the alloy composition meets national standards and customer requirements. For example, the content deviation of elements such as Si, Fe, and Cu in aluminum alloys is controlled within ±0.1%, and the content deviation of elements such as Al, Mn, and Zn in magnesium alloys is controlled within ±0.05%.
- Mechanical Property Testing: Mechanical property tests such as tensile tests and hardness tests are carried out on the raw materials to ensure that their strength, hardness, and other indicators meet production requirements. The tensile strength of aluminum alloys should be ≥300MPa, and the elongation should be ≥3%; the tensile strength of magnesium alloys should be ≥220MPa, and the elongation should be ≥2%.
- Real-Time Monitoring of Key Parameters: During the die casting production process, key parameters such as injection pressure, injection speed, mold temperature, and molten metal temperature are monitored and recorded in real-time to ensure the stability and controllability of the production process. When the parameters fluctuate beyond the set range, the system will automatically alarm and stop the machine for adjustment.
- First Article Inspection and Routine Inspection: Before each batch of production, a first article inspection is carried out, and a comprehensive inspection of the dimensions, appearance, and internal quality of the parts is conducted. Production can only proceed after passing the inspection. During the production process, regular routine inspections are carried out, and 5 – 10 products are sampled every hour to promptly detect and correct quality problems.
- Dimensional Accuracy Inspection: Coordinate measuring machines are used to accurately measure the key dimensions of finished parts, including length, width, height, hole diameter, geometric tolerances, etc., to ensure that the dimensional accuracy meets the requirements of the drawings.
- Internal Quality Inspection: Non-destructive testing techniques such as X-ray inspection and ultrasonic inspection are used to detect internal defects such as gas holes, shrinkage porosity, and cracks in the castings. For important parts, sectional metallographic analysis will also be carried out to observe the microstructure of the castings and evaluate their quality.
- Mechanical Property Testing: Mechanical property tests such as tensile tests, impact tests, and fatigue tests are carried out on the finished parts to verify whether their strength, toughness, fatigue life, and other indicators meet the use requirements. For example, the fatigue life of the bracket should reach more than 1 million cycles.
- In-Depth Communication by Technical Team: Professional technical personnel communicate in detail with customers to understand the working conditions, performance requirements, assembly dimensions, and other information of automotive transmission brackets, clarifying customer needs.
- Custom Solution Development: Based on customer needs, combined with material properties and manufacturing processes, personalized design solutions are developed, including material selection, structural design, surface treatment, etc. 3D models and technical documents are provided for customer confirmation.
- Mold Design and Manufacturing: Mold design and manufacturing are carried out according to the confirmed design solution, and strict control is exercised over mold quality to ensure mold accuracy and reliability. The mold development cycle is generally 4 – 8 weeks.
- Sample Production and Testing: Samples are produced using the mold, and comprehensive tests are carried out on the samples, including dimensional accuracy, appearance quality, mechanical properties, etc. According to the test results, the mold and process are optimized and adjusted until the samples fully meet customer requirements. The sample production cycle is generally 1 – 2 weeks.
- Efficient Production Organization: According to the order quantity and delivery date, a production plan is reasonably arranged, and advanced production equipment and automated production lines are used to ensure product quality and production efficiency. The mass production cycle depends on the order quantity, generally 2 – 4 weeks.
- Strict Packaging and Transportation: Professional packaging is carried out for the finished products, with anti-collision, moisture-proof, and anti-rust measures to ensure that the products are not damaged during transportation. A reliable logistics partner is selected to deliver the products to customers on time and safely.
- Rapid Response to Quality Issues: A perfect after-sales service system is established. For quality problems feedback by customers, a response is given within 24 hours, and a solution is provided within 48 hours. Take corresponding responsibilities for losses caused by product quality problems.
- Technical Training and Consultation: Provide customers with technical training and consultation services on product use, maintenance, and repair, helping customers use the products better. Regularly visit customers, collect customer opinions and suggestions, and continuously improve product and service quality.
A: The transmission structures, installation dimensions, and performance requirements of different vehicle models vary. Customized production can be designed and manufactured according to specific needs, ensuring a perfect match between the bracket and the vehicle’s drivetrain, giving full play to its performance advantages. At the same time, it can meet special requirements such as lightweight and high reliability.
A: Through advanced mold manufacturing processes and precision machining technologies, the key dimensional accuracy of automotive transmission bracket die castings can reach ±0.03mm, and the geometric tolerance is controlled within ±0.05mm, meeting the requirements of high-precision assembly.
A: Every link, from raw material quality control, precise production process management to strict finished product inspection, adheres to high-standard quality requirements. At the same time, simulation technology is used to predict and optimize the performance and life of parts, ensuring that die castings can work reliably under various working conditions for a long time.
A: The production cycle mainly depends on factors such as product complexity and order quantity. Generally, the mold development cycle is 4 – 8 weeks, the sample production cycle is 1 – 2 weeks, and the mass production cycle depends on the order quantity, usually 2 – 4 weeks. We will reasonably arrange the production plan according to customer needs to minimize the delivery cycle.
Are you looking for more durable and precise automotive transmission bracket die castings? Our customized services integrate cutting-edge technology and craftsmanship. From material selection to quality inspection, every link is designed for superior performance. Don’t hesitate! Leave a message now and let us inject professional strength into your project to create exclusive precision solutions!