In the ever – evolving landscape of modern manufacturing, custom CNC titanium alloy parts have emerged as a cornerstone for high – performance applications across diverse industries. Combining the remarkable properties of titanium alloys with the precision of CNC (Computer Numerical Control) machining, these parts offer unparalleled strength – to – weight ratios, exceptional corrosion resistance, and heat tolerance. This article delves into the technical capabilities, customization process, material selection, quality control, and industry applications of custom CNC titanium alloy parts, highlighting their significance in driving innovation and performance.
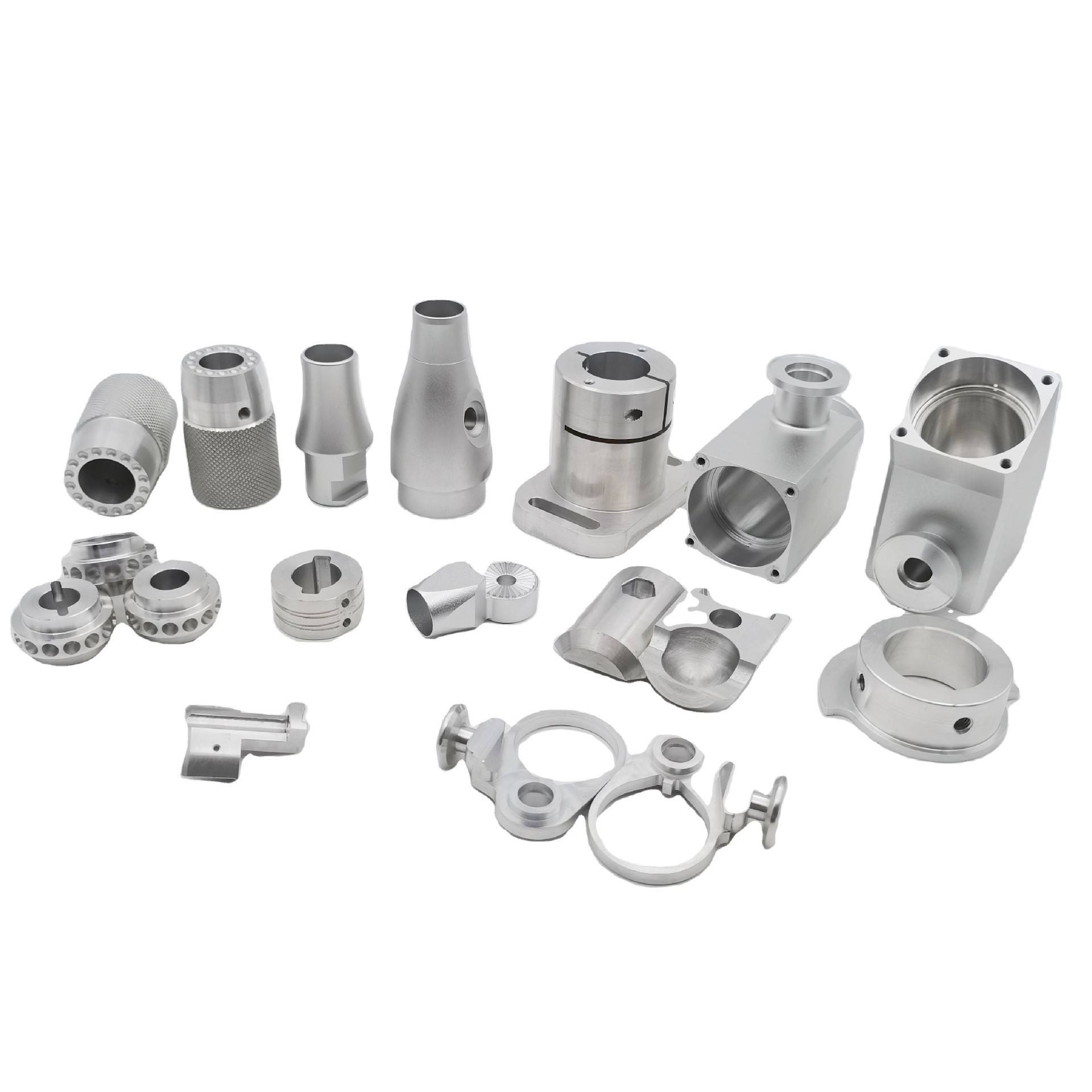
I. Technical Prowess: Redefining Machining Precision
(A) Ultra – High Dimensional Accuracy
CNC machining systems are meticulously calibrated to achieve extraordinary dimensional accuracy in the production of titanium alloy parts. With positioning accuracy reaching ±0.002mm and repeat positioning accuracy of ±0.003mm, we can fabricate parts with extremely tight tolerances. For instance, when manufacturing critical components for aerospace engines, the diameters, lengths, and intricate internal geometries can be maintained within these precise tolerances. This level of accuracy ensures a perfect fit within complex assemblies, minimizing clearances and enhancing the overall reliability and performance of the final product.
(B) Complex Geometry Machining
Five – axis CNC machining technology empowers the creation of titanium alloy parts with highly complex geometries. Whether it’s parts with intricate internal channels for fluid flow, organic – shaped components for ergonomic designs, or parts with multi – angled surfaces for optimized aerodynamics, the five – axis system can execute these designs with precision. Compared to traditional machining methods, five – axis CNC machining reduces setup – related errors from ±0.01mm to within ±0.003mm. Moreover, it boosts production efficiency by over 60%, enabling the rapid production of custom titanium alloy parts even with the most challenging designs.
(C) Advanced Machining Techniques for Titanium Alloys
Titanium alloys present unique machining challenges due to their high strength, low thermal conductivity, and tendency to work – harden. To overcome these, we employ advanced machining techniques optimized by CNC control. Specialized cutting tools with specific geometries and coatings are used to reduce friction and heat generation during machining. High – speed machining and cryogenic cooling methods are also utilized to maintain the integrity of the titanium alloy and ensure consistent surface finish quality. These techniques, combined with CNC – controlled process parameters, result in parts with superior surface finishes and extended tool life.
II. End – to – End Customization: Tailoring Parts to Your Exact Requirements
(A) In – Depth Requirement Analysis and Design Conceptualization
When you approach us with your titanium alloy part requirements, our experienced engineering team engages in detailed discussions to understand your application, performance expectations, and design preferences. We consider factors such as the operating environment (temperature, humidity, corrosive conditions), the mechanical loads the part will endure, and any specific functional or aesthetic requirements. Using state – of – the – art CAD/CAM software, we generate multiple design concepts. We then collaborate closely with you, refining the designs until they perfectly align with your vision, whether it’s a minor modification to a standard part or a completely new design for a specialized project.
(B) Strategic Material Selection and Cost Analysis
Based on the finalized design, we recommend the most suitable titanium alloys for your custom parts. Different titanium alloys offer varying combinations of properties. For example, Ti – 6Al – 4V is one of the most widely used titanium alloys, known for its excellent strength – to – weight ratio, good corrosion resistance, and weldability. It has a tensile strength of up to 1000 MPa and is commonly used in aerospace, medical, and automotive applications. For applications requiring higher heat resistance, alloys like Ti – 6242 can be selected. Simultaneously, we conduct a detailed cost analysis, factoring in material costs, machining complexity, and production volume, to provide you with a transparent and competitive quote.
(C) Precision Manufacturing and Order Tracking
Once you approve the design and quote, production commences. You can monitor the progress of your order in real – time through our dedicated online tracking platform. Our skilled technicians adhere to strict manufacturing standards, using advanced CNC turning, milling, and EDM (Electrical Discharge Machining) machines to produce titanium alloy parts that meet the highest quality benchmarks. We keep you informed at every stage of the production process, from raw material procurement to the final inspection.
(D) Rigorous Quality Assurance and Timely Delivery
After production, each custom titanium alloy part undergoes a rigorous quality inspection. Only parts that meet our exacting standards are shipped to you. We perform dimensional inspections using coordinate measuring machines (CMMs) to ensure that all critical dimensions are within ±0.002mm. Surface finish measurements are taken to ensure that the surface meets the required roughness specifications for optimal functionality and aesthetics. In addition, we conduct mechanical tests, such as tensile strength testing, fatigue testing, and hardness testing, to validate the performance of the parts. We also offer comprehensive after – sales support, addressing any concerns you may have during the product’s lifecycle.
III. Strategic Material Selection: Choosing the Right Titanium Alloy for Optimal Performance
(A) Ti – 6Al – 4V (Grade 5)
Ti – 6Al – 4V is the workhorse of the titanium alloy industry. Comprising 6% aluminum and 4% vanadium, it offers a balanced combination of strength, lightness, and corrosion resistance. Its low density of 4.43 g/cm³, coupled with high strength, makes it ideal for applications where weight reduction is crucial without sacrificing structural integrity. It is widely used in aerospace components such as engine parts, airframe structures, and landing gear, as well as in medical implants due to its biocompatibility.
(B) Ti – 6242
Ti – 6242, with its composition of 6% aluminum, 2% tin, 4% zirconium, and 2% molybdenum, is specifically designed for high – temperature applications. It can maintain its mechanical properties at temperatures up to 500°C, making it suitable for parts in jet engines, gas turbines, and other high – heat environments. The alloy’s excellent creep resistance and fatigue strength ensure reliable performance even under extreme operating conditions.
(C) Titanium – Nickel (Nitinol) Alloys
Nitinol alloys are known for their shape – memory and superelastic properties. These unique characteristics make them suitable for applications such as medical stents, where the ability to return to a pre – defined shape after deformation is essential. In addition to their functional properties, Nitinol alloys also offer good corrosion resistance and biocompatibility, making them a popular choice in the medical device industry.
IV. Stringent Quality Control: Ensuring Top – Tier Part Quality
(A) Raw Material Inspection
All incoming raw materials for titanium alloy parts are subject to strict quality checks. We use spectroscopic analysis to verify the chemical composition of the alloys, ensuring that they meet the required standards. For example, when using Ti – 6Al – 4V, we confirm that the aluminum, vanadium, and other trace elements are within the specified ranges. Additionally, hardness testing, tensile testing, and microstructure analysis are performed to ensure the material’s integrity and suitability for the intended application.
(B) In – Process Monitoring
Throughout the manufacturing process, we employ statistical process control (SPC) techniques to monitor key manufacturing parameters. Regular sampling and data collection help us identify and correct any potential issues promptly. We monitor parameters such as cutting speeds, feed rates, tool wear, and coolant flow during machining. In the case of heat – treatment processes, we closely control temperature, time, and cooling rates. If any parameter deviates from the set values, we can adjust the process in real – time to ensure consistent product quality.
(C) Final Product Validation
Before shipping, each part undergoes a comprehensive inspection. We use CMMs to verify dimensional accuracy, ensuring that all critical dimensions are within ±0.002mm. Surface roughness measurements are taken to ensure that the surface finish is optimized for the part’s intended function. Non – destructive testing methods, such as ultrasonic testing and dye penetrant inspection, are used to detect any internal or surface – breaking defects. Only parts that pass all these tests are considered ready for delivery.
V. Diverse Industry Applications: Transforming Performance Across Sectors
(A) Aerospace Industry
In the aerospace industry, custom CNC titanium alloy parts are indispensable. From lightweight engine components that improve fuel efficiency to high – strength airframe structures that enhance safety, titanium alloys play a crucial role. The low density and high strength – to – weight ratio of titanium alloys reduce the overall weight of aircraft, leading to significant fuel savings. Additionally, their excellent corrosion resistance makes them suitable for use in harsh environments, such as those encountered during flight at high altitudes.
(B) Medical Industry
In the medical field, titanium alloy parts are widely used for implants and surgical instruments. Their biocompatibility ensures that they do not cause adverse reactions in the human body, making them ideal for long – term implants such as hip and knee replacements. The precision of CNC machining allows for the creation of complex geometries that conform to the patient’s specific anatomy, improving the fit and functionality of the implants. Titanium alloy surgical instruments are also highly valued for their strength, durability, and corrosion resistance.
(C) Automotive Industry
The automotive industry benefits from the use of titanium alloy parts in high – performance vehicles. Components such as engine valves, connecting rods, and suspension parts made from titanium alloys offer reduced weight, which improves vehicle acceleration, handling, and fuel efficiency. The high strength and fatigue resistance of titanium alloys also contribute to the longevity and reliability of these components, even under the extreme conditions of high – performance driving.
(D) Energy Industry
In the energy sector, custom titanium alloy parts are used in applications such as power generation and oil and gas exploration. In power plants, titanium alloys are used for components in steam turbines and heat exchangers due to their high – temperature resistance and corrosion resistance. In the oil and gas industry, titanium alloy parts are used in subsea equipment, where their resistance to corrosion from seawater and harsh chemicals is essential for reliable operation.
VI. Frequently Asked Questions (FAQ)
(A) What is the typical precision of custom CNC titanium alloy parts?
Our CNC machining can achieve a dimensional tolerance of ±0.002mm, ensuring precise fit and optimal performance in your applications.
(B) How do I choose the right titanium alloy for my parts?
The choice depends on your application’s specific requirements, such as the operating temperature, mechanical loads, and environmental conditions. Our experts can assess your needs and recommend the most suitable alloy to meet your performance and cost expectations.
(C) What is the lead time for custom titanium alloy parts?
Lead times vary depending on the complexity of the design and order quantity. Simple designs can be completed in 3 – 5 days, while more complex ones may take 7 – 10 days. Rush orders are available upon request.
(D) Can CNC machining handle complex titanium alloy part designs?
Yes, our five – axis CNC machines are capable of fabricating titanium alloy parts with intricate geometries, including complex internal structures, organic shapes, and multi – angled surfaces, to meet even the most demanding design requirements.
(E) How much does it cost to customize titanium alloy parts?
Costs are determined by factors such as material, design complexity, precision requirements, and production volume. While small – batch customization may be relatively costly, economies of scale can significantly reduce per – unit costs for larger orders.
VII. Customer Testimonials
An aerospace company approached us to develop custom titanium alloy parts for their new aircraft engine. Our team utilized advanced CNC machining and material selection techniques to create parts that met the strict aerospace standards. The new parts not only reduced the weight of the engine by 15% but also improved its overall efficiency and reliability. The company was highly satisfied with the performance and quality of the custom parts, leading to a long – term partnership.
A medical device manufacturer needed custom titanium alloy implants for a new line of orthopedic products. We designed and manufactured implants with precise geometries tailored to the patient’s anatomy. The use of high – quality Ti – 6Al – 4V alloy and advanced CNC machining ensured the implants’ biocompatibility, strength, and fit. The customer reported a significant increase in patient satisfaction and a reduction in post – surgical complications, validating the success of our custom – made parts.
Reach Out Now for Your Custom CNC Titanium Alloy Parts!
Regardless of your industry or application, our team of experts is ready to collaborate with you. We offer a seamless end – to – end service, from design to delivery. Contact us today to discuss your project requirements and take the first step towards getting top – quality custom CNC titanium alloy parts that will enhance the performance and innovation of your products.