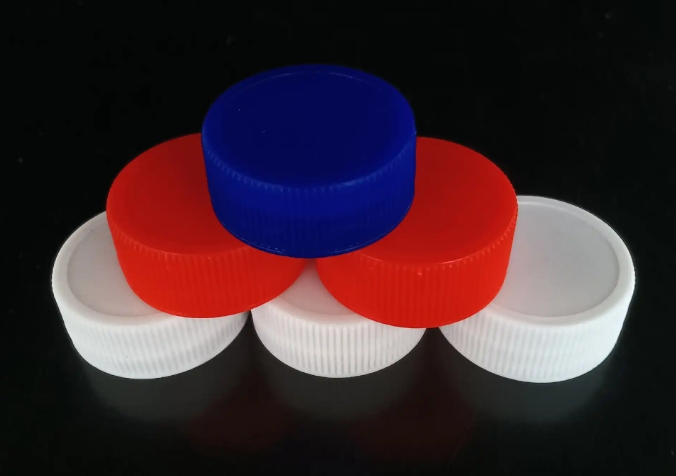
I. Core Material Properties and Application Advantages
(A) Comparison of Mainstream Material Properties
Material Type
|
Density (g/cm³)
|
Temperature Range (°C)
|
Core Advantages
|
Typical Certifications
|
Polypropylene (PP)
|
0.89–0.91
|
-20 to 120
|
Oil resistance, easy welding, low cost
|
FDA Food Contact Certification
|
Polyethylene (PE)
|
0.91–0.96
|
-40 to 60
|
Impact resistance, low-temperature tolerance, excellent sealing
|
EU 10/2011 Food-Grade Certification
|
Polyethylene Terephthalate (PET)
|
1.33–1.38
|
-40 to 60
|
High transparency, carbonic acid resistance
|
USP665 Pharmaceutical Packaging Certification
|
Acrylonitrile Butadiene Styrene (ABS)
|
1.03–1.07
|
-20 to 80
|
High strength, easy coloring, flame retardancy
|
UL94 V-2 Flame Retardant Certification
|
(B) Driving Forces of Customization Core Requirements
- Sealing Performance: The beverage industry requires a leakage rate ≤ 0.005mL/min (60kPa pressure test), while pharmaceutical caps must meet USP<671> airtightness standards.
- Opening Torque: Child-resistant caps require an opening force ≥ 15N·m (for adults) and ≤ 5N·m (child misopening rate ≤ 5%).
- Environmental Resistance: Cosmetic caps must pass 200 hours of 50°C/90%RH humidity testing without deformation; chemical caps must resist swelling after 48 hours of immersion in 95% ethanol.
II. Analysis of Three Core Processing Technologies
(A) Injection Molding: High-Precision Multi-Functional Cap Machining
- Technical Advantages:
-
- Dimension accuracy ±0.05mm, thread fitting accuracy up to ISO 4042 Class 5H, supporting integrated molding of anti-counterfeit teeth and tamper-evident rings.
-
- Multi-cavity mold design (64–128 cavities per mold), production efficiency of 5,000–10,000 pieces/hour, suitable for caps with 38–130mm diameters.
- Process Parameters:
-
- Injection pressure 100–180MPa, mold temperature 40–70°C, cooling time 8–15 seconds.
-
- Shrinkage control: 1.2%–1.8% for PP, 0.2%–0.6% for PET, ensuring bottle mouth sealing compatibility.
(B) Compression Molding: Thin-Wall Lightweight Cap Production
Process Type
|
Wall Thickness Range
|
Weight Deviation
|
Typical Application Scenarios
|
Hot Compression Molding
|
0.3–1.0mm
|
≤±1%
|
Mineral water caps (weight <1g)
|
Cold Compression Molding
|
1.0–3.0mm
|
≤±0.5%
|
Lubricant caps (high-strength requirements)
|
- Technical Highlights:
-
- Thin-wall design (minimum 0.25mm) reduces weight by 30% compared to injection molding, material utilization ≥98%.
-
- In-mold labeling technology completes label application synchronously with position accuracy ±0.5mm, suitable for high-speed filling lines (≥600 bottles/minute).
(C) Special Processes: Functional Cap Customization
- Anti-Counterfeit Design:
-
- Laser Engraving: 0.1–0.3mm deep anti-counterfeit codes with 300dpi resolution, supporting traceable code customization.
-
- Breakable Tamper-Evident Ring: Connection bridge strength 10–15N·m, producing a distinct breaking sound when opened, anti-counterfeit rate ≥99%.
- Sealing Structures:
-
- Double-Seal Design: Primary + secondary seals, gas permeability ≤5mL/(m²·24h) (50kPa pressure difference).
-
- Induction Sealing: Aluminum foil gasket thermally bonded with sealing strength ≥5N/cm, suitable for pharmaceutical moisture-proof packaging.
III. Full-Process Customization Solutions
(A) Design and Material Engineering
- Multi-Dimensional Design Support:
- Structural Optimization: Moldflow simulation analyzes filling pressure and cooling efficiency to ensure thread demolding force ≤8N, reducing bottle mouth deformation rate to ≤0.3%.
- Functional Customization:
-
- Measuring Caps: Built-in 0.5–50mL scales with ±2% measurement accuracy, ideal for cosmetic detergents.
-
- Ventilated Caps: One-way valve design with air permeability 5–500mL/min to prevent internal pressure buildup (e.g., fermented food packaging).
- Precise Material Selection:
- Carbonated Beverages: PET material with anti-static additives, surface resistance ≤10⁹Ω to avoid dust adsorption.
- Pharmaceutical Packaging: USP Class VI certified PP with heavy metal migration ≤0.01ppm and microbial residue ≤10CFU/100cm².
- Pre-Processing Technology:
- Raw Material Modification: Adding slip agents to reduce friction coefficient to <0.3 for high-speed filling line sorting.
- Color Matching: Pantone color matching accuracy ΔE ≤0.8, supporting pearlescent/fluorescent effects for brand visual identity.
(B) Production and Quality Control
- Flexible Manufacturing Capability:
- Rapid Prototyping: 3D printed samples delivered in 24 hours, aluminum mold development cycle 7–10 days (20–30 days for conventional steel molds).
- Mass Production:
-
- High-Speed Injection Line: Equipped with Krones high-speed robots, daily output 300,000–500,000 pieces per machine (50-cavity mold).
-
- Compression Molding Line: German Kautex equipment supports 1–5g ultra-light cap production with cycle time ≤1.2 seconds/piece.
- Full-Range Testing System:
- Physical Properties:
-
- Torque Tester: Opening torque variation ≤±5% (target 10–20N·m).
-
- Sealing Tester: Bubble method detects leakage rate with 0.001mL/min precision.
- Environmental Testing:
-
- Thermal Shock: -40°C–70°C cycling 50 times without cracking, suitable for cold chain packaging.
-
- Aging Test: QUV-A irradiation for 1,000 hours with color difference ΔE ≤2 to ensure outdoor storage stability.
IV. Multi-Industry Application Scenarios
(A) Food & Beverage Industry
- Carbonated Drinks: PET tamper-evident caps with serrated rings (break force 12–15N·m), CO₂ permeability ≤10mL/(L·24h).
- Edible Oil: PP leak-proof caps with inner silicone seals compressed 20%–25%, no leakage after 24-hour inversion at 50°C.
(B) Pharmaceutical Industry
- Oral Preparations: Child-resistant caps with dual-lock structure (pressure + rotation to open), child misopening rate <1%, compliant with ASTM D3475.
- Injectable Packaging: Sterile caps treated with EO sterilization, initial bioburden ≤10CFU/piece, inner surface particles (≥5μm) ≤20 per 100cm².
(C) Cosmetics & Chemicals
- Shampoo: ABS dispensing foam caps with spring return force 3–5N, foam output error ≤±3%, suitable for automatic filling lines.
- Industrial Solvents: Solvent-resistant caps with PVC + fluoroelastomer seals, passing IMDG Code 3.1 packaging tests for corrosion resistance.
(D) Special Applications
- Sports Water Bottles: PE dust-proof flip caps with hinge fatigue resistance ≥100,000 cycles without breakage, sealing up to IP68 (1m water immersion for 30 minutes).
- Reagent Packaging: Aluminum-plastic composite caps (PP body + aluminum foil seal), puncture force ≤8N, ideal for laboratory micro-reagent storage.
V. Technology Selection Guide
Requirement Type
|
Preferred Technology
|
Diameter Range (mm)
|
Functional Features
|
Delivery Cycle
|
Small Batch Customization
|
Injection Molding
|
15–150
|
Anti-counterfeit codes, multi-color co-injection
|
Prototype in 3 days, batch in 15 days
|
Ultra-Light High-Speed Production
|
Compression Molding
|
28–53
|
Thin-walled (<1g), in-mold labeling
|
Prototype in 5 days, batch in 20 days
|
Special Functionality
|
Composite Processes
|
38–110
|
Child resistance, induction sealing
|
Prototype in 7 days, batch in 25 days
|