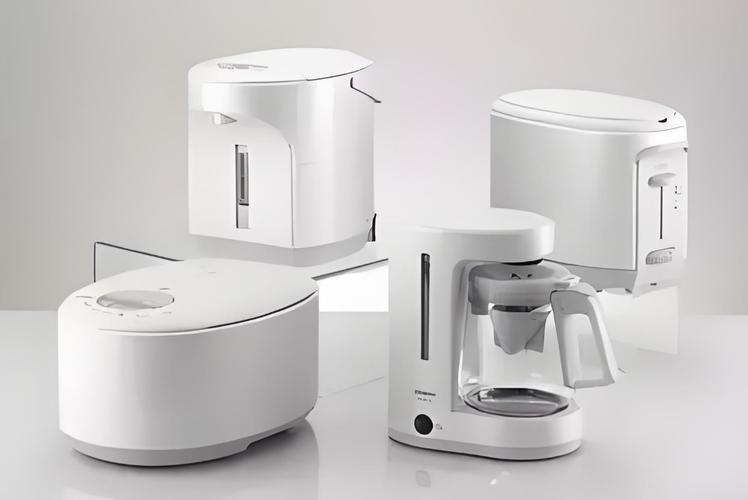
I. Core Material Properties and Application Advantages
(A) Comparison of Mainstream Material Properties
Material Type
|
Density (g/cm³)
|
Temperature Range (℃)
|
Core Advantages
|
Typical Certifications
|
Acrylonitrile Butadiene Styrene (ABS)
|
1.03–1.07
|
-20 to 80
|
Easy moldability, high toughness, easy electroplating
|
UL94 V-0 Flame Retardant Certification
|
Polypropylene (PP)
|
0.89–0.91
|
-30 to 120
|
Chemical corrosion resistance, low density, cost-effective
|
LFGB Food Contact Certification
|
Polycarbonate (PC)
|
1.20–1.22
|
-40 to 130
|
Impact resistance, high transparency, dimensional stability
|
UL746C Material Certification
|
Polyvinyl Chloride (PVC)
|
1.3–1.45
|
-15 to 60
|
Good flame retardancy, weather resistance
|
IEC 60754-1 Halogen Test Certification
|
PC/ABS Alloy
|
1.12–1.20
|
-30 to 120
|
Balanced high strength and temperature resistance
|
RoHS Environmental Certification
|
(B) Driving Forces of Customization Requirements
1. Safety and Durability
- Kitchen appliance casings must pass UL94 V-0 certification (1.6mm thickness), resisting ignition in glow wire tests (750℃).
- Washing machine casings must withstand 200 hours of 90%RH/50℃ humidity testing without deformation or discoloration.
2. Aesthetics and Fitment
- Surface gloss controlled at 40–80GU (60° angle measurement), supporting matte, high-gloss, and metallic finishes.
- Mounting hole positioning accuracy ±0.1mm for seamless assembly with internal appliance components.
3. Environmental Adaptability
- Refrigerator casings require low-temperature resistance (-40℃ impact strength ≥20kJ/m²) and resistance to refrigeration oil corrosion.
- Air conditioner casings must have UV resistance grade 4 (QUV-A irradiation for 1000 hours, color difference ΔE ≤3).
II. Analysis of Four Core Processing Technologies
(A) Injection Molding: High-Precision Structural Processing
- Technical Advantages:
-
- Enables one-step molding of complex curves (e.g., curved casings, embedded handles) with dimensional accuracy ±0.05mm.
-
- Large-scale mold design (1–8 cavities per mold), suitable for 500–5000g casings, production efficiency 200–800 pieces/hour.
- Process Parameters:
-
- Injection pressure 100–160MPa, mold temperature 50–90℃, cooling time 15–30 seconds.
-
- Shrinkage control: 0.4%–0.7% for ABS, 1.0%–1.5% for PP, ensuring assembly tolerance ≤0.03mm.
(B) In-Mold Decoration (IMD): Integrated Aesthetic Molding
Process Type
|
Typical Application Scenarios
|
Technical Highlights
|
In-Mold Roller (IMR)
|
Metallic brushed surfaces for high-end appliances
|
Pattern accuracy ±0.1mm, friction resistance ≥500 cycles without wear
|
Two-Color Co-Injection
|
Transparent windows + main structure
|
Optical-grade PC transmittance ≥92%, bonding strength with ABS ≥18MPa
|
- Technical Advantages:
-
- Paint-free process reduces 90% VOC emissions, compliant with EU environmental standards.
-
- Surface hardness ≥3H, resistant to detergent corrosion (5% laundry liquid immersion for 72 hours without discoloration).
(C) Blow Molding: Custom Hollow Component Production
- Process Advantages:
-
- Suitable for hollow structures like washing machine inner drums and air conditioner guide covers, wall thickness uniformity ≥95%.
-
- Multi-layer co-extrusion integrates wear-resistant/color/UV-resistant layers, extending service life by 30%.
- Key Parameters:
-
- Extrusion speed 5–15m/min, mold temperature 40–70℃, suitable for PP/PVC materials.
-
- Dimensional accuracy ±0.3mm, adaptable to large casings (width ≤1000mm).
(D) Surface Treatment Technologies
- Functional Treatments:
-
- Antibacterial treatment: Silver-ion additives (bacteriostasis rate ≥99%), ideal for kitchen appliance casings.
-
- Antistatic treatment: Surface resistance ≤10⁹Ω, reducing dust adsorption (e.g., refrigerator casings).
- Decorative Treatments:
-
- Electroplating: Chrome layer thickness 5–10μm, salt spray test ≥500 hours without rust.
-
- Wood grain transfer: Texture reduction ≥95%, adapting to high-end home design styles.
III. Full-Process Customization Solutions
(A) Design and Material Engineering
- Multi-Dimensional Design Support:
-
- Structural Optimization: ANSYS simulation analyzes handle stress distribution to ensure 100,000-time grip fatigue resistance without fracture.
-
- Functional Customization:
-
-
- Modular casings: Support quick-release structures (disassembly time ≤1 minute) for easy maintenance.
-
-
-
- Noise reduction design: Sound-absorbing textures on inner walls (0.5–1.0mm depth), noise reduction ≥10dB.
-
- Precise Material Selection:
-
- Kitchen Appliances: PP + 30% talc, resistant to cooking oil corrosion (swelling rate ≤1% after 72-hour immersion).
-
- High-End Refrigerators: PC/ABS alloy, low-temperature impact resistance (-30℃ without cracking), electroplated surface for premium texture.
- Pre-Processing Technology:
-
- Raw material drying: PC moisture content controlled ≤0.02% to avoid bubbles in transparent components.
-
- Color matching: Pantone color accuracy ΔE ≤0.8, supporting custom brand color systems.
(B) Production and Quality Control
- Flexible Manufacturing Capability:
-
- Rapid Prototyping: 3D printed samples delivered in 48 hours, aluminum mold development cycle 10–15 days (steel mold 30–45 days).
-
- Mass Production:
-
-
- High-speed injection lines: Haitian servo injection machines (clamping force 1000–5000 tons), daily output 5000–20,000 pieces.
-
-
-
- Automated production lines: Integrated machine vision inspection, appearance defect recognition rate ≥99.8%.
-
- Comprehensive Testing System:
-
- Physical Properties:
-
-
- Drop test: 1.0m drop to concrete, breakage rate ≤0.5% (200-piece sample).
-
-
-
- Impact resistance: 500g steel ball drop from 500mm height without surface cracks.
-
-
- Environmental Performance:
-
-
- Weather resistance: QUV-A irradiation for 2000 hours, color difference ΔE ≤2, strength retention ≥85%.
-
-
-
- Chemical resistance: 5% hydrochloric acid/sodium hydroxide immersion for 48 hours without surface corrosion.
-
-
- Certification Support: Provides UL, CE, GB 4706, and other certification reports for global market access.
IV. Multi-Scenario Application Solutions
(A) Kitchen Appliances
- Microwave Oven Casings: ABS + flame retardant, UL94 V-0 certified, resistant to long-term 100℃ operation.
- Rice Cooker Casings: PP material + IMR technology, wood grain surface, fingerprint resistance (cleaning cycles ≥1000 times).
(B) Large Appliances
- Washing Machine Casings: Moisture-resistant PP, waterproof grade IPX4, internal rib design supporting ≥50kg load.
- Refrigerator Casings: PC/ABS alloy + UV-resistant coating, -40℃ to 70℃ thermal cycling 50 times without deformation.
(C) Small Appliances
- Air Purifier Casings: ABS + antibacterial treatment, filter installation accuracy ±0.1mm, compatible with HEPA filters.
- Vacuum Cleaner Casings: Lightweight PP material, wall thickness 1.5–2.0mm, 15% lighter than traditional designs.
(D) High-End Appliances
- Built-In Oven Casings: High-temperature resistant PC (long-term 150℃), ceramic coating for easy cleaning (oil residue ≤5%).
- Smart Appliance Casings: IMD technology for integrated touch panels, capacitive sensing accuracy ±0.05mm.
V. Technology Selection Guide
Requirement Type
|
Preferred Technology
|
Weight Range
|
Core Indicators
|
Delivery Cycle
|
Personalized Small Batches
|
3D Printing + Injection Molding
|
200–2000g
|
Rapid prototyping, irregular structures
|
Prototype in 3 days, batch in 15 days
|
High-End Aesthetic Customization
|
IMD + PC/ABS
|
500–3000g
|
High gloss, superior weather resistance
|
Prototype in 7 days, batch in 25 days
|
Large-Scale Standardized Production
|
Injection Molding + PP
|
1000–5000g
|
Low cost, high chemical resistance
|
Prototype in 5 days, batch in 20 days
|