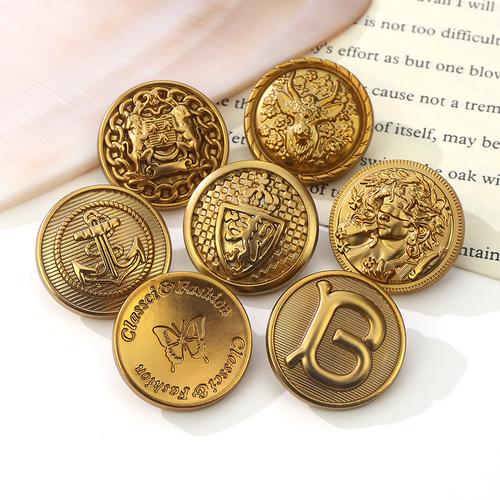
I. Core Material Properties and Application Advantages
(A) Comparison of Mainstream Material Properties
Material Type
|
Density (g/cm³)
|
Tensile Strength (MPa)
|
Hardness (HV)
|
Core Advantages
|
Typical Certifications
|
Copper Alloy (Brass)
|
8.4 – 8.8
|
200 – 400
|
60 – 150
|
Easy to process, beautiful luster, oxidation resistance
|
EN 1811 Nickel Release Test
|
Zinc Alloy
|
6.6 – 6.7
|
220 – 450
|
70 – 120
|
Low cost, good fluidity, diverse shapes
|
ASTM B696 Standard Certification
|
Stainless Steel (304)
|
7.93
|
520 – 720
|
130 – 180
|
High strength, corrosion resistance, strong rust prevention
|
ISO 14644 Cleanroom Certification
|
Aluminum Alloy (6061)
|
2.7
|
124 – 207
|
35 – 65
|
Lightweight, excellent corrosion resistance
|
GB/T 3190 Alloy Standard
|
Titanium Alloy
|
4.5
|
895 – 1100
|
250 – 350
|
Ultra-high strength, good biocompatibility
|
ASTM F136 Medical Standard
|
(B) Driving Forces of Customization Requirements
1. Decorative Requirements
- Surface treatments should achieve diverse effects such as mirror finish (roughness Ra ≤ 0.2μm) and brushing (pattern uniformity error ≤ 5%).
- Color requirements must precisely match Pantone color cards with a color difference ΔE ≤ 1.0.
2. Functional Requirements
- Buckle components should withstand a pulling force of ≥ 50N and have an opening and closing lifespan of over 5,000 times.
- Buttons for outdoor products should pass the salt spray test (≥ 24 hours without rust).
3. Safety Requirements
- For buttons in contact with skin, the nickel release amount should be ≤ 0.5μg/cm²/week, complying with EU REACH regulations.
- Buttons for children’s products should pass the small parts test to prevent choking hazards.
II. Analysis of Four Core Processing Technologies
(A) Stamping Forming: High-Precision Component Processing
- Technical Advantages
-
- The progressive die process enables continuous stamping of multiple processes, increasing production efficiency by 60%.
-
- Dimensional accuracy can reach ± 0.02mm, meeting the processing requirements for buttons with complex shapes.
- Process Parameters
-
- Stamping speed: 80 – 120 times/minute; stamping force is adjusted from 5 to 50 tons according to the material.
-
- The die clearance is controlled at 8% – 12% of the material thickness to ensure cross-sectional quality.
(B) Surface Treatment Technologies
Process Type
|
Typical Application Scenarios
|
Technical Highlights
|
Electroplating
|
Gold, silver, and other metallic luster buttons
|
Plating thickness: 1 – 3μm; adhesion ≥ 4B grade
|
PVD Vacuum Coating
|
High-end scratch-resistant and wear-resistant buttons
|
Coating hardness ≥ 2000HV; salt spray resistance ≥ 72 hours
|
Enameling
|
Colorful artistic buttons
|
High color saturation; wear resistance ≥ 500 friction times
|
Laser Engraving
|
Personalized pattern buttons
|
Engraving precision ± 0.01mm; patterns are permanently preserved
|
- Technical Advantages
-
- PVD coating enhances wear resistance and is environmentally friendly, complying with international environmental standards.
-
- Enameling achieves long-lasting, non-fading colors through high-temperature firing.
(C) Die Design and Manufacturing
- Design Key Points
-
- 3D modeling using CAD/CAM technology shortens the design cycle by 30%.
-
- The assembled die structure facilitates local replacement of worn parts, reducing maintenance costs.
- Manufacturing Process
-
- Die material: Cr12MoV, with a hardness of HRC58 – 62 after heat treatment.
-
- Wire electrical discharge machining accuracy reaches ± 0.005mm, ensuring die surface accuracy.
(D) Secondary Processing: Functional Enhancement Treatment
- Riveting Process
-
- A spin riveting machine is used for shank riveting, with a riveting strength ≥ 80N to ensure a firm connection between the button and the fabric.
-
- The surface is flat after riveting, without burrs or deformation.
- Polishing Treatment
-
- Vibration polishing makes the button surface roughness Ra ≤ 0.4μm, achieving a mirror finish.
-
- Magnetic polishing can process complex inner holes and grooves, ensuring comprehensive polishing.
III. Full-Process Customization Solutions
(A) Design and Material Engineering
1. Multi-Dimensional Design Support
- Creative Design: Provide various design schemes such as hand-drawn renderings and 3D visualizations according to customer requirements.
- Structural Optimization: Optimize the buckle structure through finite element analysis (FEA) to enhance mechanical performance.
- Functional Customization
-
- Magnetic buttons have a magnetic force of ≥ 20N for convenient opening and closing.
-
- Waterproof buttons have a sealing performance of IP65, suitable for outdoor equipment.
2. Precise Material Selection
- Buttons for Clothing Decoration: Select zinc alloy or copper alloy to balance aesthetics and cost.
- Buttons for High-End Bags: Use stainless steel or titanium alloy to enhance product texture and durability.
3. Pre-treatment Process
- Level the metal sheet with a flatness error ≤ 0.1mm.
- Remove oil and rust from the surface to ensure subsequent processing quality.
(B) Production and Quality Control
1. Flexible Manufacturing Capability
- Rapid Prototyping: 3D printed samples are delivered within 3 days, and the die development cycle is 7 – 15 days.
- Mass Production
-
- Automated stamping production lines with a daily output of 50,000 – 100,000 pieces.
-
- Equipped with a CCD visual inspection system, achieving a dimensional detection accuracy of ± 0.01mm and a defect recognition rate of ≥ 99.8%.
2. Comprehensive Inspection System
- Physical Properties
-
- Tensile Test: Use an electronic universal testing machine with a test force error ≤ ± 1N.
-
- Wear Test: Conduct tests with a Taber abraser, and the surface wear amount after testing should be ≤ 0.05mm.
- Appearance Inspection
-
- Color Difference Detection: Use a spectrophotometer to ensure color consistency.
-
- Defect Detection: Combine manual visual inspection with machine vision to ensure no scratches, pits, or other defects.
- Certification Support: Provide international certification reports such as REACH, RoHS, and EN 71 to meet global market requirements.
IV. Multi-Scenario Application Solutions
(A) Clothing Field
- Suit Buttons: Adopt brass electroplating and surface polishing, with a gloss of 80 – 90GU, enhancing the grade of the clothing.
- Denim Buttons: Made of zinc alloy with an aged treatment, presenting a retro style, and the buckling force ≥ 60N for long-lasting use.
(B) Bag Field
- Luggage Decorative Buttons: Made of stainless steel with PVD rose gold plating, passing the salt spray test for ≥ 48 hours, resistant to wear and scratches.
- Backpack Adjustment Buttons: Made of aluminum alloy, designed for lightweight, reducing weight by 40% compared to traditional buttons, and capable of bearing ≥ 10kg.
(C) Special-Purpose Field
- Military and Police Uniform Buttons: Made of titanium alloy with ultra-high strength (tensile strength ≥ 900MPa), meeting the requirements of harsh environments.
- Children’s Clothing Buttons: Pass the EN 71 – 3 heavy metal test and adopt anti-detachment designs to ensure children’s safety.
V. Technology Selection Guide
Requirement Type
|
Preferred Technology
|
Size Range (mm)
|
Core Indicators
|
Delivery Cycle
|
Personalized Small Batches
|
3D Printing + Stamping
|
Φ5 – Φ30
|
Fast response, creative design
|
Prototype in 3 days, batch production in 15 days
|
High-End Quality Requirements
|
PVD Coating + Stainless Steel
|
Φ8 – Φ40
|
High wear resistance, oxidation resistance
|
Prototype in 7 days, batch production in 25 days
|
Large-Scale Standardized Production
|
Progressive Die Stamping + Zinc Alloy
|
Φ6 – Φ25
|
Low cost, high efficiency
|
Prototype in 5 days, batch production in 20 days
|