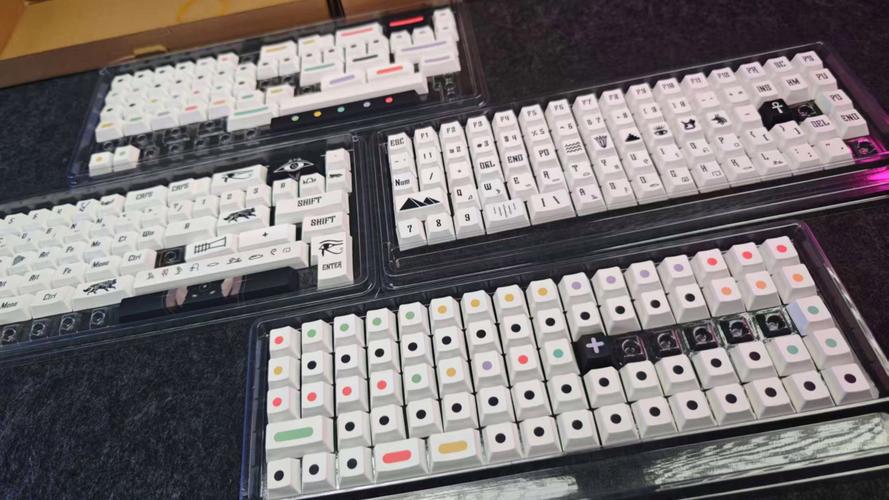
I. Core Material Properties and Application Advantages
(A) Comparison of Mainstream Material Properties
Material Type
|
Density (g/cm³)
|
Shore D Hardness
|
Temperature Range (℃)
|
Core Advantages
|
Typical Surface Treatments
|
Acrylonitrile Butadiene Styrene (ABS)
|
1.05
|
80–90
|
-20~80
|
Easy moldability, cost-effective, good light transmittance
|
Spray painting, electroplating, silk screening
|
Polybutylene Terephthalate (PBT)
|
1.31
|
85–95
|
-40~150
|
High wear resistance, low hygroscopicity
|
Sublimation, laser engraving
|
Polycarbonate (PC)
|
1.20
|
75–85
|
-40~130
|
High light transmittance, impact resistance
|
UV coating, water transfer printing
|
Nylon (PA)
|
1.15
|
70–80
|
-40~180
|
Self-lubrication, fatigue resistance
|
Double-shot molding, anodizing
|
Thermoplastic Polyurethane (TPU)
|
1.20
|
40–90 (Shore A)
|
-50~80
|
Elastic touch, anti-slip
|
Epoxy coating, texture molding
|
(B) Driving Forces of Customization Requirements
1. Personalized Design Needs
- Support complex pattern customization (e.g., anime characters, mechanical textures) with a minimum line precision of 0.3mm.
- Pantone color matching accuracy ΔE ≤ 0.8, enabling special effects like gradients and transparency.
2. Functional Performance Requirements
- Character wear resistance ≥ 1000 friction cycles (ISO 1518-2 standard); light uniformity of translucent keycaps ≥ 90%.
- Uniform wall thickness (tolerance ±0.1mm) to ensure pressing stability (Shaking amplitude ≤0.5mm).
3. Ergonomic Requirements
- Curvature compliant with OEM/Cherry/SA height standards; finger contact area roughness Ra ≤ 1.6μm.
- Weight control at 3–8g per keycap (size-dependent) to reduce long-term typing fatigue.
II. Analysis of Four Core Processing Technologies
(A) Injection Molding: High-Precision Basic Keycap Processing
- Technical Advantages
-
- Double-shot molding integrates characters with the keycap body, increasing wear life by 5x.
-
- Multi-cavity molds (64–128 cavities per mold) achieve production efficiency of 2000–5000 pieces/hour, compatible with 87/104/60% layouts.
- Process Parameters
-
- Injection pressure 80–120MPa, mold temperature 50–80℃, cooling time 8–15 seconds.
-
- Shrinkage control: 0.5%–0.8% for ABS, 1.0%–1.5% for PBT, ensuring height tolerance ±0.2mm.
(B) Surface Treatment Technologies
Process Type
|
Typical Application Scenarios
|
Technical Highlights
|
Sublimation Transfer
|
PBT keycap pattern customization
|
200℃ high-temperature penetration, weather resistance ≥3 years, edge precision ±0.1mm
|
Silk Screening
|
Low-cost character marking
|
Minimum font height 1.5mm, ink adhesion ≥4B (cross-cut test)
|
Laser Engraving
|
Backlit character carving for translucent keycaps
|
Laser precision ±0.05mm, supports 0.5mm ultra-fine lines, light transmittance ≥85%
|
Water Transfer Printing
|
Complex curved texture molding
|
360° full-coverage patterns, texture reduction ≥95%, friction resistance ≥500 cycles
|
(C) 3D Printing: Personalized Prototype Production
- Process Advantages
-
- Rapid prototyping for irregular keycaps (e.g., spherical, concave-convex surfaces), with resin samples delivered in 3 days.
-
- Nylon 12 material offers 80MPa strength for functional testing (press life ≥50,000 cycles).
- Technical Parameters
-
- Layer thickness 0.05–0.1mm, dimensional accuracy ±0.1mm, supports 2mm minimum diameter hollow structures.
-
- Compatible with Cherry MX, TTC, Gateron and other 主流轴体 (mainstream switch axes), clip fit tolerance ≤0.05mm.
(D) Secondary Processing: Functional Enhancement
- Touch Optimization
-
- Sandblasting (roughness Ra 3.2–6.3μm) improves anti-slip performance, ideal for intense gaming.
-
- Skin-friendly coating (5–10μm thickness) reduces surface tension, cutting fingerprint residue by 70%.
- Structural Reinforcement
-
- Inner rib design (rib thickness 0.8–1.2mm) increases anti-deformation capacity by 30% (press test deformation ≤0.3mm).
-
- Metal insert molding (e.g., brass bushings) extends service life to over 100,000 cycles.
III. Full-Process Customization Solutions
(A) Design and Material Engineering
1. Multi-Dimensional Design Support
- Creative Design
-
- Services include CAD modeling, hand-drawn conversion, and 3D scanning reverse design, supporting custom key heights (e.g., XDA/SA/DSA profiles).
-
- Structural optimization via ANSYS stress analysis ensures keycap center press offset ≤0.2mm.
- Functional Customization
-
- Translucent keycaps: PC material with light guide design, backlight uniformity ≥90% (integrating sphere test).
-
- Silent keycaps: TPU lining structure reduces typing noise by 15dB (compared to traditional ABS keycaps).
2. Precise Material Selection
- Mass Production Keycaps: ABS + double-shot molding balances cost and light transmittance (unit price ≤$0.3, 1000-piece MOQ).
- High-End Customization: PBT + sublimation for non-greasy long-term use (wear resistance ≥Grade 4).
- Extreme Translucency: Full-transparent PC + laser-engraved characters for RGB backlighting (transmittance ≥92%).
3. Pre-Processing Technology
- Raw material drying: PBT moisture content controlled ≤0.05% to avoid surface water marks.
- Color calibration: Datacolor spectrophotometer ensures batch color consistency (ΔE ≤1.0).
(B) Production and Quality Control
1. Flexible Manufacturing Capability
- Rapid Prototyping
-
- 3D printed samples delivered in 48 hours; injection molding first samples completed in 7 days (including simple mold processing).
-
- Supports single-key customization (e.g., unique ESC keys, spacebars), minimum order quantity 1 piece.
- Mass Production
-
- Automated production lines with Fanuc robots, daily capacity 100,000 pieces (~1200 sets of 87-key standard kits).
-
- Smart warehousing: QR code key data entry supports mixed shipping (key matching accuracy 100%).
2. Comprehensive Testing System
- Physical Properties
-
- Insertion/extraction force: 3–5N (Cherry axis standard), looseness ≤0.1mm after 5000 cycles.
-
- Compression test: 50N pressure for 10 seconds, recovery deformation ≤0.1mm (ISO 6892 standard).
- Appearance Inspection
-
- Character offset: Vision system detects 偏差 ≤0.3mm; burrs ≤0.1mm.
-
- Light uniformity: Integrating sphere test shows brightness difference ≤5% (center vs. edge).
- Certification Support: Provides RoHS and REACH environmental certifications, ensuring safety (heavy metal migration ≤0.1ppm).
IV. Multi-Scenario Application Solutions
(A) Mechanical Keyboard Enthusiasts
- Gaming Keycaps: ABS double-shot + skin-friendly coating, anti-slip textures on WASD keys (friction coefficient +40%), macro key special markings.
- Custom Kits: PBT sublimation + metal counterweights, inner ribs on large keys (space/Shift) to reduce wobble (amplitude ≤0.3mm).
(B) Designers and Office Users
- High-Translucent Keycaps: PC material + laser-engraved backlit characters for customizable RGB effects (transmittance ≥90%), ideal for nighttime design work.
- Quiet Typing Kits: TPU soft keycaps + noise reduction structure, typing noise ≤45dB (office standard), ergonomic curvature increasing finger contact area by 20%.
(C) Collectibles and Cultural Creation
- Limited Edition Keycaps: Zinc alloy/resin hybrid + enamel coloring, hand-inlaid gems/nameplates with unique serial numbers, supporting small batches (50–500 sets).
- IP Co-Branded Kits: Water transfer printing for anime/game IP patterns, aged edge treatment (wear simulation ≥90%), themed packaging included.
V. Technology Selection Guide
Requirement Type
|
Preferred Technology Combination
|
Material Choice
|
Core Indicators
|
Delivery Cycle
|
Single Creative Customization
|
3D Printing + Laser Engraving
|
Resin/ABS
|
Personalized patterns, fast delivery
|
Prototype in 3 days, delivery in 7 days
|
High-End Wear-Resistant Kits
|
Double-Shot Molding + Sublimation
|
PBT
|
Character life ≥5 years, non-greasy
|
Prototype in 7 days, batch in 25 days
|
Large-Scale Mass Production
|
Injection Molding + Silk Screening
|
ABS
|
Low cost, high consistency
|
Prototype in 5 days, batch in 20 days
|
Extreme Translucent Backlighting
|
Full-Transparent Injection + Laser Engraving
|
PC
|
Transmittance ≥90%, uniform lighting
|
Prototype in 7 days, batch in 30 days
|