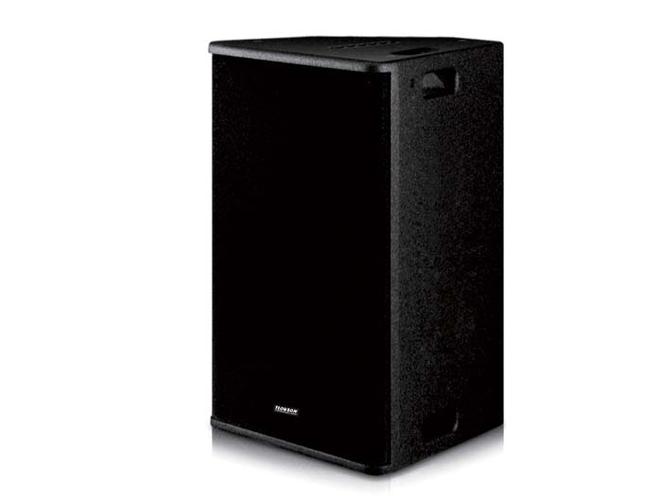
I. Core Material Properties and Application Advantages
(A) Comparison of Mainstream Material Properties
Material Type
|
Density (g/cm³)
|
Temperature Range (°C)
|
Impact Strength (kJ/m²)
|
Acoustic Damping Characteristics
|
Core Advantages
|
Typical Certifications
|
Acrylonitrile Butadiene Styrene (ABS)
|
1.05
|
-20 ~ 80
|
18 – 24
|
Moderate
|
Easy to mold, cost-effective, excellent surface treatability
|
UL94 V-0 Flame Retardant Certification
|
Polycarbonate (PC)
|
1.20
|
-40 ~ 130
|
60 – 80
|
Low
|
High impact resistance, high transparency, dimensional stability
|
ISO 7625 UV Resistance Certification
|
Polybutylene Terephthalate (PBT)
|
1.31
|
-40 ~ 150
|
8 – 12
|
High
|
Low hygroscopicity, chemical resistance, high rigidity
|
IEC 60243 Dielectric Strength Certification
|
Polypropylene (PP)
|
0.90 – 0.91
|
-30 ~ 120
|
10 – 16
|
Moderate-Low
|
Lightweight, good weather resistance, cost-effective
|
LFGB Food Contact Certification
|
PC/ABS Alloy
|
1.12 – 1.20
|
-30 ~ 120
|
30 – 45
|
Moderate
|
Balanced high strength and toughness
|
RoHS Environmental Certification
|
(B) Driving Forces of Customization Requirements
1. Acoustic Performance Requirements
- Shells need to have appropriate acoustic damping to reduce resonance, keeping the fluctuation range of the frequency response curve within ±3dB.
- For closed – type speaker shells, the air leakage rate should be ≤0.01m³/h to ensure sufficient low – frequency extension.
2. Durability Requirements
- Outdoor speaker shells must pass the salt spray test (≥72 hours without corrosion) and maintain a color difference of ΔE≤3 after 1000 hours of UV exposure.
- Withstand the impact of a 500g steel ball dropped freely from a height of 1m, with no surface cracks or internal structural damage.
3. Appearance and Function Requirements
- Support personalized appearance design, with surface treatments capable of achieving effects such as mirror finish (roughness Ra≤0.2μm) and brushing (pattern accuracy ±0.1mm).
- Precisely reserved installation positions for speakers, circuit boards, and interfaces, with dimensional tolerances controlled within ±0.05mm.
II. Analysis of Four Core Processing Technologies
(A) Injection Molding: High-Precision Shell Processing
- Technical Advantages
-
- Utilize large – scale injection molding machines to form large – sized speaker shells weighing up to 5kg, with dimensional accuracy of ±0.1mm.
-
- Multi – cavity mold design (2 – 4 cavities per mold) enables a production efficiency of 300 – 600 pieces per hour, suitable for different speaker specifications.
- Process Parameters
-
- Injection pressure: 120 – 180MPa, mold temperature: 60 – 90°C, cooling time: 15 – 30 seconds.
-
- Shrinkage control: ABS 0.4% – 0.7%, PC 0.5% – 0.8%, ensuring assembly gaps ≤0.2mm.
(B) Surface Treatment Technologies
Process Type
|
Typical Application Scenarios
|
Technical Highlights
|
Painting
|
Colored shells, special texture surfaces
|
Coating thickness: 15 – 25μm, adhesion ≥4B grade
|
Electroplating
|
Decorative parts of high – end speakers
|
Chrome plating thickness: 8 – 12μm, salt spray test ≥500 hours
|
Water Transfer Printing
|
Complex patterns such as wood grain and marble
|
Pattern reduction ≥95%, 360° full coverage
|
Laser Engraving
|
Brand logos, translucent character carving
|
Engraving precision ±0.05mm, depth 0.1 – 0.3mm
|
(C) Secondary Processing: Functional Enhancement
- Structural Reinforcement
-
- Internal rib design with rib thickness of 1.5 – 2.5mm enhances shell rigidity, reducing the resonance frequency by 20%.
-
- Injection molding with metal inserts, with a pull – out force ≥100N, ensures the stable installation of speakers, brackets, and other components.
- Sealing Treatment
-
- Adopt ultrasonic welding technology with a welding strength ≥25MPa, combined with silicone seals to achieve an IPX5 waterproof rating.
-
- Control the gap width within 0.3mm to prevent dust from entering the speaker interior.
(D) 3D Printing: Rapid Prototyping and Small-Batch Customization
- Process Advantages
-
- Quickly verify the design of irregular speaker shells, with samples delivered within 48 hours, shortening the R & D cycle by 40%.
-
- Nylon 12 3D – printed parts with a strength of 80MPa can be used for acoustic testing and structural verification.
- Application Scenarios
-
- Custom high – end speaker shells (order quantity ≤300 pieces), with a 50% reduction in delivery cycle.
-
- Reverse development of shells for obsolete speaker models (3D scanning error ≤0.08mm).
III. Full-Process Customization Solutions
(A) Design and Material Engineering
1. Multi-Dimensional Design Support
- Acoustic Design
-
- Optimize the shell structure using acoustic simulation software (such as CST, COMSOL) to reduce standing wave effects.
-
- Design the port with a tapered diameter to increase the low – frequency response efficiency by 15%.
- Functional Customization
-
- Reserve precise positions for microphones, speakers, and cooling holes in smart speakers, with hole position accuracy of ±0.03mm.
-
- Design hidden handles for outdoor speakers, capable of bearing a load of ≥5kg and with an opening and closing life of 10,000 times.
- Appearance Design
-
- Provide design solutions such as hand – drawn renderings and 3D visualizations, supporting personalized shapes like curved surfaces and streamline forms.
-
- Color schemes precisely match Pantone color cards, with a color difference of ΔE≤0.8.
2. Precise Material Selection
- Home Speakers: Select ABS materials to balance cost and appearance quality, meeting daily usage requirements.
- Professional Monitor Speakers: Use PBT materials, whose high strength and low hygroscopicity ensure acoustic stability.
- Outdoor Portable Speakers: Choose PP or PC/ABS alloys, which offer weather resistance and drop resistance.
3. Pre-treatment Process
- Raw material drying: Control the moisture content of PC materials ≤0.02% to prevent bubbles and silver streaks after molding.
- Mold polishing: Achieve a surface roughness of Ra≤0.4μm to ensure the smoothness of the shell surface.
(B) Production and Quality Control
1. Flexible Manufacturing Capability
- Rapid Prototyping
-
- 3D printed samples are delivered within 24 hours, with an aluminum mold development cycle of 10 – 15 days (30 – 40 days for steel molds).
-
- Support minimum order quantities of 50 pieces to meet small – and medium – batch customization needs.
- Mass Production
-
- Automated production lines equipped with ABB robots, with a daily production capacity of 3000 pieces per line.
-
- Intelligent inspection systems use visual recognition and laser measurement, with dimensional detection accuracy of ±0.03mm and a defect recognition rate of ≥99.6%.
2. Comprehensive Inspection System
- Acoustic Performance
-
- Frequency response test: Conducted in an anechoic chamber, the frequency response range meets design requirements, with fluctuations within ±3dB.
-
- Sealing test: Use a helium mass spectrometer leak detector, with an air leakage rate ≤0.01m³/h.
- Physical Performance
-
- Impact test: Withstand a 1m drop test at – 20°C without damage.
-
- Wear resistance test: Pass 500 cycles of the Taber abrasion test with no obvious scratches on the surface.
- Environmental Performance
-
- High – low temperature cycling: – 40°C ~ 70°C for 50 cycles, with a dimensional change rate ≤0.1%.
-
- Chemical resistance test: Immerse in 5% acid – base solution for 24 hours, with no surface corrosion or discoloration.
- Certification Support: Provide CE, FCC, RoHS, and other certification reports to ensure global market access.
IV. Multi-Scenario Application Solutions
(A) Home Speaker Applications
- Bookshelf Speaker Shells: Injection – molded from ABS materials, with surface painting treatment, offering a variety of color options. The precisely positioned installation holes are well – adapted to various speaker units, and the optimized internal structure reduces resonance, providing users with a clear and pure sound experience.
- Smart Speaker Shells: Made of PC/ABS alloy, with reserved positions for microphone arrays, speakers, cooling holes, etc. Support the integration of LED light strips, and brand logos and operation buttons are engraved by laser engraving, achieving a perfect combination of aesthetics and functionality.
(B) Professional Speaker Applications
- Studio Monitor Speaker Shells: Manufactured from PBT materials, featuring high strength and stable acoustic performance. The internal reinforcement rib design effectively suppresses resonance, ensuring accurate sound reproduction and meeting the stringent requirements of professional recording, mixing, and other scenarios.
- Stage Performance Speaker Shells: Made of high – strength PC materials, with impact resistance and wear resistance. The surface electroplating treatment improves texture and durability, and the designed convenient hoisting and handling structures adapt to frequent performance usage.
(C) Outdoor Speaker Applications
- Portable Bluetooth Speaker Shells: Made of PP materials with silicone protective covers, achieving IPX7 waterproof, dustproof, and drop – proof performance. Weighing as little as 300g, it is easy to carry. The stylish appearance design supports personalized pattern customization, meeting the needs of outdoor leisure and entertainment.
- Outdoor Public Address Speaker Shells: Made of PC/ABS alloy, through anti – UV and anti – aging treatments, it can work stably in the environment of – 30°C ~ 60°C for a long time, with a protection level of IP66, adapting to various harsh outdoor environments.
(D) High-End Customization Applications
- Hi-Fi Speaker Shells for Audiophiles: Use customized PC/ABS alloys, combined with exquisite surface treatment processes (such as piano baking paint, wood grain water transfer printing). The internal structure is carefully designed by acoustic experts, pursuing ultimate sound quality and luxurious appearance to meet the personalized needs of high – end audio enthusiasts.
- Art Concept Speaker Shells: Utilize 3D printing technology to achieve unique 造型 designs, combined with special materials and surface processes, turning speakers into home decorations with both audio functions and artistic values, providing users with a unique audio – visual experience.
V. Technology Selection Guide
Requirement Type
|
Preferred Technology
|
Material Selection
|
Core Indicators
|
Delivery Cycle
|
Creative Design Verification
|
3D Printing + Laser Engraving
|
PC/Nylon
|
Rapid prototyping, personalized appearance
|
Prototype in 3 days, small batch in 15 days
|
High Sound Quality Requirements
|
Injection Molding + PBT
|
PBT
|
Low resonance, stable acoustic performance
|
Prototype in 7 days, batch in 25 days
|
Large-Scale Mass Production
|
High-Speed Injection Molding + ABS
|
ABS
|
Low cost, high efficiency
|
Prototype in 5 days, batch in 20 days
|
Outdoor Protection Requirements
|
Injection Molding + PC/ABS
|
PC/ABS Alloy
|
Waterproof, dustproof, anti – aging
|
Prototype in 7 days, batch in 30 days
|