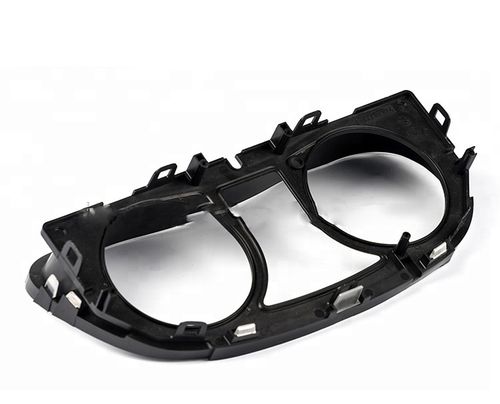
I. Core Material Properties and Application Advantages
(A) Comparison of Mainstream Material Properties
Material Type
|
Density (g/cm³)
|
Temperature Resistance (℃)
|
Haze (%)
|
Flammability Rating (UL94)
|
Core Advantages
|
Typical Certifications
|
Polycarbonate (PC)
|
1.20
|
-40~130
|
≤1.5
|
V-2
|
High transparency, impact resistance, dimensional stability
|
ISO 179 Impact Resistance Certification
|
Acrylonitrile Butadiene Styrene (ABS)
|
1.05
|
-20~80
|
≤3.0
|
V-0 (1.6mm)
|
Easy molding, cost-effective, easy electroplating
|
UL 746C Material Certification
|
Polybutylene Terephthalate (PBT)
|
1.31
|
-40~150
|
≤2.0
|
V-0 (0.8mm)
|
Low hygroscopicity, chemical resistance
|
IEC 60695-2-11 Glow Wire Test Certification
|
PC/ABS Alloy
|
1.15
|
-30~120
|
≤2.5
|
V-0
|
Balanced high strength and temperature resistance
|
RoHS Environmental Certification
|
Thermoplastic Polyurethane (TPU)
|
1.20
|
-50~80
|
≤5.0
|
HB
|
Elastic touch, low-temperature impact resistance
|
SAE J2005 Weather Resistance Certification
|
(B) Driving Forces of Customization Requirements
1. Safety and Reliability
- High-temperature Resistance: No deformation after long-term use at 120℃, heat deflection temperature ≥130℃ (HDT test).
- Flammability Requirement: Dashboard body material flammability rating ≥UL94 V-0 (3.0mm thickness) to prevent fire spread.
- Impact Resistance: Impact strength ≥50kJ/m² at -40℃, complying with FMVSS 201 vehicle safety standards.
2. Display and Interaction Performance
- Optical Performance: Transmittance ≥85% (display area), haze ≤2% to ensure clear visibility.
- Surface Hardness: ≥3H (pencil hardness test), resistant to 1000 friction cycles without obvious scratches.
- Sensor Integration: Pre-installed slots for cameras/radars with dimensional tolerance ±0.05mm to guarantee signal accuracy.
3. Environmental Adaptability
- Weather Resistance: QUV-A aging test for 2000 hours, color difference ΔE≤3, strength retention ≥80%.
- Chemical Resistance: Resistance to common automotive liquids (e.g., windshield washer fluid, sunscreen) for 72 hours without swelling/discoloration.
II. Analysis of Five Core Processing Technologies
(A) Injection Molding: High-Precision Structural Processing
- Technical Advantages
-
- Enables one-step molding of complex curved surfaces (e.g., arched dashboard shells, embedded display slots) with dimensional accuracy ±0.03mm.
-
- Large-scale molds (1-2 cavities per mold) suitable for 10-15kg dashboard assemblies, production efficiency 100-200 pieces/hour.
- Process Parameters
-
- Injection pressure 150-200MPa, mold temperature 80-120℃ (for PC), cooling time 25-40 seconds.
-
- Shrinkage control: PC 0.5%-0.8%, PC/ABS 0.6%-1.0%, ensuring assembly gap ≤0.1mm.
(B) Surface Treatment Technologies
Process Type
|
Typical Application Scenarios
|
Technical Highlights
|
In-Mold Decoration (IMD)
|
High-end dashboard matte/metallic finishes
|
Pattern precision ±0.05mm, weather resistance increased by 30%
|
Anti-Glare Coating
|
Display protective covers
|
Haze control 5%-15%, reflectance ≤5% (60° angle measurement)
|
Electroplating
|
Decorative buttons/bezels
|
Chrome plating thickness 8-12μm, salt spray test ≥500 hours
|
Laser Texturing
|
Anti-slip control areas
|
Surface roughness Ra 1.6-3.2μm, friction coefficient increased by 25%
|
(C) 3D Printing: Rapid Prototyping and Small-Batch Customization
- Process Advantages
-
- Rapid validation of irregular structures (e.g., curved dashboards, hidden air vents), samples delivered in 3 days.
-
- Nylon 12CF material strength up to 150MPa, supporting functional tests (e.g., clip fatigue testing).
- Technical Parameters
-
- Layer thickness 0.05mm, dimensional accuracy ±0.1mm, suitable for high-precision sensor slot validation.
-
- Supports transparent/translucent material printing for display optical performance testing.
(D) Secondary Processing: Functional Integration
- Structural Reinforcement
-
- Metal insert molding (e.g., copper mounting nuts), pull-out force ≥200N to ensure secure dashboard-vehicle connection.
-
- Ultrasonic welding strength ≥30MPa for seamless multi-component bonding (e.g., dashboard body and sun visor).
- Intelligent Integration
-
- Integrated capacitive touch areas with response time ≤10ms, position accuracy ±0.2mm.
-
- Light guide strip embedding technology for uniform ambient lighting (brightness difference ≤5%).
(E) Thermoforming: Curved Glass Bonding Technology
- Technical Advantages
-
- Achieves 2.5D/3D curved glass bonding with plastic substrates, bonding accuracy ±0.1mm.
-
- Temperature resistance up to 130℃ for long-term use in high-temperature dashboard environments.
- Key Parameters
-
- Bonding pressure 5-10N/cm², bubble rate ≤0.1% (area ≥1mm²).
-
- Edge bonding strength ≥50N/mm to prevent glass detachment.
III. Full-Process Customization Solutions
(A) Design and Material Engineering
1. Multi-Dimensional Design Support
- Optical Design
-
- Display area uses PC material with optimized transmittance up to 90%, paired with anti-glare coatings to reduce reflection.
-
- Analog dashboard scale accuracy ±0.5°, ensuring reading error ≤1%.
- Structural Optimization
-
- Moldflow simulation analyzes shrinkage rate, rib thickness designed at 1.5-2.5mm, deformation ≤0.2mm.
-
- Lightweight design: Micro-foam injection technology reduces weight by 15%-20% compared to traditional designs.
- Intelligent Integration
-
- Pre-installed slots for ADAS sensors (e.g., cameras, radars) with position accuracy ±0.03mm.
-
- Integrated tactile feedback modules with key travel 3-4mm and feedback force 15-25N.
2. Precise Material Selection
- Economy Passenger Vehicles: ABS + 20% flame retardant, balancing cost and basic performance (V-0 flame retardancy, 80℃ temperature resistance).
- High-End Models: PC/ABS alloy + IMD process for high-gloss surfaces and 120℃ long-term temperature resistance.
- New Energy Vehicles: PBT + 30% glass fiber for battery compartment heat resistance (150℃ short-term tolerance) and EMI shielding.
3. Pre-Processing Technology
- Raw material drying: PC moisture content controlled ≤0.02% to avoid post-molding optical defects.
- Color calibration: Datacolor spectrophotometer ensures Pantone color matching accuracy ΔE≤0.8.
(B) Production and Quality Control
1. Flexible Manufacturing Capability
- Rapid Prototyping
-
- 3D printed samples delivered in 48 hours, aluminum mold development cycle 15-20 days (steel mold 40-50 days).
-
- Supports minimum order quantity of 50 pieces for new vehicle R&D needs.
- Mass Production
-
- Automated production lines: KUKA robots handle bonding and inspection, daily capacity 500-1000 pieces per line.
-
- Intelligent warehousing: QR code traceability ensures batch qualification rate ≥99.2%.
2. Comprehensive Inspection System
- Optical Performance
-
- Transmittance/haze test: Complies with ISO 13468, display area transmittance ≥85%.
-
- Color difference detection: Spectrophotometer measurement, ΔE≤1.0 (matching vehicle interior).
- Mechanical Performance
-
- Vibration test: 10-2000Hz sweep, 5g acceleration, no looseness/deformation (SAE J1455 standard).
-
- Fatigue test: Key life ≥50,000 cycles, clip insertion force decay ≤10%.
- Environmental Performance
-
- Thermal shock: -40℃~85℃ cycling 50 times, dimensional change rate ≤0.15%.
-
- Chemical resistance: 5% NaOH solution immersion for 24 hours, surface hardness retention ≥95%.
- Certification Support: Provides IATF 16949, UL, ECE R118, and other certification reports.
IV. Multi-Scenario Application Solutions
(A) Passenger Vehicle Sector
- Traditional Fuel Vehicle Dashboards
-
- Uses ABS/PC alloy with IMD process for wood/metal 拉丝 (brushed) finishes, 120℃ temperature resistance for engine bay heat conduction.
-
- Integrates mechanical gauges and LCD displays, mounting hole accuracy ±0.1mm for seamless center console integration.
- New Energy Vehicle Full-LCD Dashboards
-
- High-transparency PC material with 2.5D curved glass, anti-glare coating reduces sunlight reflection, edge radius R≥5mm for improved visual appeal.
-
- Lightweight design (weight ≤1.5kg), micro-foam structure reduces plastic usage by 20% for battery range optimization.
(B) Commercial Vehicle Sector
- Truck Dashboards
-
- PBT + 30%GF material, 150℃ temperature resistance for cab high-temperature environments, anti-vibration design (natural frequency ≥200Hz).
-
- Laser-textured large button areas with wet-hand friction coefficient ≥0.6 for enhanced driving safety.
- Bus Dashboards
-
- TPU elastic frame + PC body, no brittle fracture under -40℃ impact, IP54 dust/water resistance for complex road conditions.
(C) Smart Cockpit Sector
- AR-HUD Dashboards
-
- Optical-grade PC material, transmittance ≥92% and birefringence ≤5% to ensure distortion-free AR images.
-
- High-precision mold forming (tolerance ±0.02mm) for HUD projector installation.
- Touch-Integrated Dashboards
-
- Capacitive touch areas using PC/ABS alloy with surface hardening (hardness ≥4H), supports gloved operation (response sensitivity ≥80%).
V. Technology Selection Guide
Requirement Type
|
Preferred Technology Combination
|
Material Selection
|
Core Indicators
|
Delivery Cycle
|
New Vehicle R&D Validation
|
3D Printing + IMD
|
PC/ABS Alloy
|
Rapid prototyping, optical performance verification
|
Prototype in 5 days, small batch in 20 days
|
High-End Appearance Customization
|
Thermoforming + Electroplating
|
PC
|
Curved glass bonding, high weather resistance
|
Prototype in 7 days, mass production in 30 days
|
Large-Scale Standardized Production
|
High-Speed Injection Molding + ABS
|
ABS
|
Low cost, high production efficiency
|
Prototype in 5 days, mass production in 25 days
|
New Energy High-Temperature Demand
|
Micro-Foam Injection + PBT
|
PBT
|
Lightweight, 150℃ long-term temperature resistance
|
Prototype in 7 days, mass production in 35 days
|