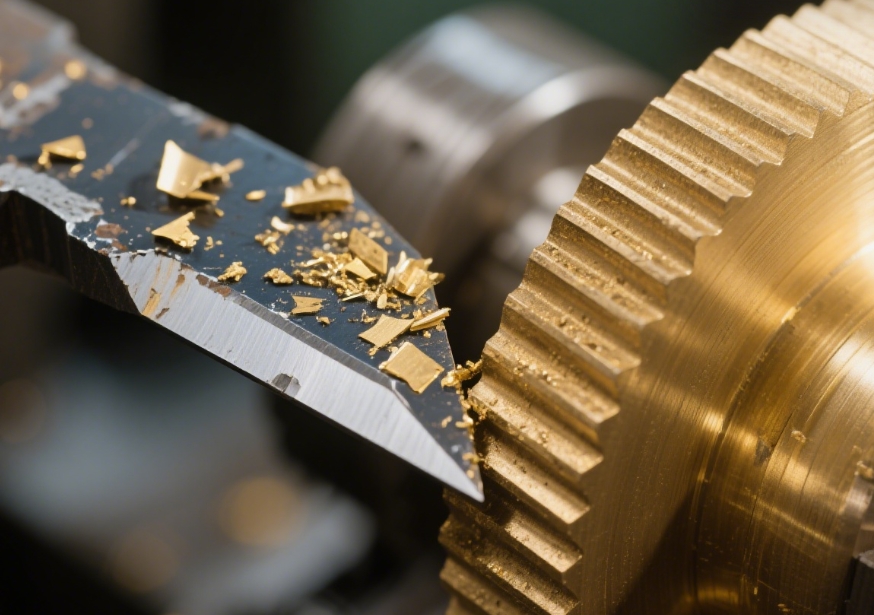
Answer:
CNC milling (Computer Numerical Control) automatically controls the movement of the cutting tool through a computer program, eliminating the need for continuous manual operation. It can achieve high – precision and complex – trajectory machining, making it suitable for mass production. Manual milling relies on the operator to manually adjust the handle to control the movement of the cutting tool. The precision is greatly affected by human factors, and it is suitable for machining simple parts or in small – batch production. The core differences between the two lie in the degree of automation, precision control, and production efficiency.
CNC milling (Computer Numerical Control) automatically controls the movement of the cutting tool through a computer program, eliminating the need for continuous manual operation. It can achieve high – precision and complex – trajectory machining, making it suitable for mass production. Manual milling relies on the operator to manually adjust the handle to control the movement of the cutting tool. The precision is greatly affected by human factors, and it is suitable for machining simple parts or in small – batch production. The core differences between the two lie in the degree of automation, precision control, and production efficiency.
Extended Answer
- Control System and Degree of Automation
CNC Milling
Control Method: Generate a machining program through G – code or CAD/CAM software and input it into the machine tool control system (such as FANUC, SIEMENS). The computer automatically controls the movement of the X/Y/Z – axis motors according to the program without real – time manual intervention.
Automation Advantages:
It can be repeatedly executed after one – time programming, reducing human errors.
Supports multi – axis linkage (such as 4 – axis, 5 – axis), enabling the machining of complex trajectories like spirals and curved surfaces.
Manual Milling
Control Method: The operator directly drives the movement of the worktable through a handwheel or handle and needs to observe the machining status in real – time and adjust parameters such as feed rate and rotational speed.
Limitations:
Complex trajectories (such as arcs and three – dimensional contours) rely on templates or form – followers, making machining difficult.
Precision may fluctuate due to fatigue during long – term operation. - Operation Mode and Skill Requirements
CNC Milling
Operation Process:
Programming (manual programming or generating a program with software);
Clamping the workpiece and tool setting;
Running the program, and the machine tool processes automatically while the operator only needs to monitor.
Skill Requirements: Master programming software (such as UG, Mastercam), the operation panel of the machine tool, and troubleshooting. It requires a high level of mechanical principles and mathematical modeling ability.
Manual Milling
Operation Process:
Manually adjust the spindle speed and feed rate;
Precisely control the position of the cutting tool through the handwheel (for example, to move the X – axis by 0.1 mm, turn the handwheel by 1 grid);
Judge the cutting state based on experience (such as the color of the chips and the vibration of the machine tool).
Skill Requirements: Rely on the operator’s feel and experience. Be proficient in using measuring tools (such as dial indicators, micrometers) to calibrate the workpiece. It is suitable for traditional mechanical processing craftsmen. - Machining Precision and Repeatability
CNC Milling
Precision Level:
The positioning accuracy can reach ±0.01 mm, and the repeat positioning accuracy can reach ±0.005 mm (for high – end machine tools), which is suitable for precision parts in aerospace and medical equipment.
Example: When machining the hole system of an automotive engine block, CNC can ensure that the hole – distance error is less than 0.03 mm.
Repeatability: The dimensional consistency of parts is high when the same program is run multiple times, which is suitable for mass production.
Manual Milling
Precision Level:
The precision of an ordinary operator is about ±0.05 mm, and a senior craftsman can reach ±0.02 mm, but it is difficult to maintain stably.
Example: When machining the grooves of ordinary mechanical parts, the width error may be within ±0.1 mm.
Repeatability: There may be fluctuations in the dimensions of parts in different batches, and multiple measurements and adjustments are required, which is not suitable for high – precision mass production. - Production Efficiency and Batch Adaptability
CNC Milling
Efficiency Advantages:
High – speed cutting (the spindle speed can reach 10,000 – 40,000 rpm) combined with automatic tool change reduces downtime.
During mass production, after programming, there is no need for repeated debugging. The preparation time for 100 parts is the same as that for 1 part.
Application Scenarios:
Mass production (such as 3C product casings, with a single batch of more than 1000 pieces);
One – step forming of complex parts (such as unmanned aerial vehicle frames, which require multi – process composite machining).
Manual Milling
Efficiency Bottleneck:
The manual feed speed is slow (usually less than 100 mm/min), and operations such as tool change and tool setting require manual operation. The single – piece machining time is 3 – 5 times that of CNC.
Application Scenarios:
Small – batch production (such as sample trial – production, with a quantity of less than 10 pieces);
Maintenance scenarios (such as on – site repair and fitting of parts, without the need for complex programming). - Machining Complexity and Cost
CNC Milling
Complex Machining Ability:
Supports structures that are impossible to complete manually, such as three – dimensional surfaces (such as mold cavities) and variable – cross – section contours (such as turbine blades).
Example: When machining an aero – engine impeller with a 5 – axis CNC, the cutting tool can cut in from any angle to fit the complex surface.
Cost Characteristics:
The equipment investment is high (a three – axis CNC milling machine costs about 100,000 – 500,000 yuan), but the unit cost is low during mass production.
Manual Milling
Machining Limitations:
Can only machine straight lines, simple arcs, or two – dimensional contours, and multi – axis linkage is not achievable.
Example: When machining a grooved part with an inclined angle, the worktable needs to be manually tilted, and the precision is difficult to guarantee.
Cost Characteristics:
The equipment cost is low (an ordinary manual milling machine costs about 50,000 – 100,000 yuan), but the labor cost is high, making it suitable for low – cost and small – batch scenarios. - Programming Requirements and Production Flexibility
CNC Milling
Necessity of Programming:
It is necessary to write a machining program according to the part drawing. Programming for complex parts may take several hours to several days.
Advantages: When changing products, only the program needs to be modified without re – adjusting the mechanical structure, which is suitable for flexible production of multiple varieties in small batches.
Manual Milling
Flexibility Characteristics:
No programming is required, and the operator can adjust the machining path improvised based on experience, which is suitable for non – standard parts or repair and fitting (such as making parts according to physical objects).
Disadvantages: When changing production types, manual debugging is required again, resulting in low efficiency.
In conclusion, CNC milling has core advantages in automation, high precision, and mass – production capabilities, making it suitable for complex and precise parts in modern manufacturing. Manual milling, on the other hand, relies on experience and is suitable for simple parts or small – batch scenarios. The two coexist in industrial production according to different requirements.