CNC machining allowance refers to the amount of material intentionally left on a workpiece before final machining operations. It acts as a buffer to ensure that after processes like cutting, grinding, or turning, the part meets precise dimensional requirements, surface finish standards, and tolerance specifications.
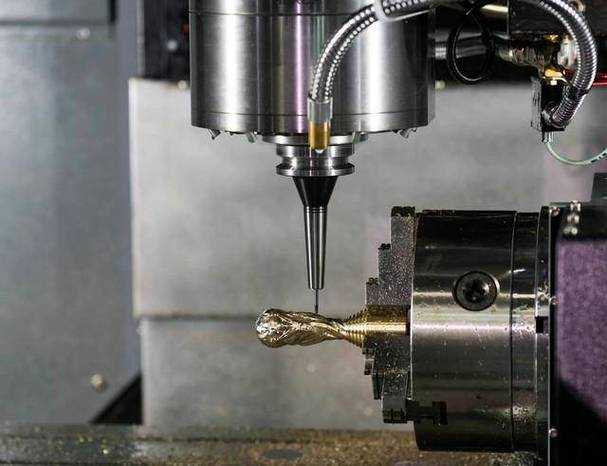
Why is machining allowance necessary?
Machining allowance serves several critical purposes:
- Compensating for material imperfections: Raw workpieces (e.g., castings, forgings, or bar stock) often have irregularities like surface defects, warping, or uneven dimensions. The allowance ensures these flaws are removed during machining.
- Achieving tight tolerances: Even with advanced CNC equipment, minor variations in tool wear, machine vibration, or thermal expansion can affect precision. A reserved allowance allows for fine adjustments to hit exact measurements (e.g., ±0.001 inches).
- Improving surface finish: Rough machining (e.g., removing large chunks of material) may leave tool marks or burrs. A final pass with a smaller allowance smooths the surface to meet standards (e.g., Ra 1.6 for cosmetic parts).
How is machining allowance determined?
The amount of allowance depends on several factors:
- Material type: Harder materials (e.g., titanium, tool steel) require larger allowances to account for increased tool wear and the need for more aggressive cutting. Softer materials (e.g., aluminum, plastic) often need smaller allowances.
- Initial workpiece condition: Forged or cast parts typically have more surface irregularities than pre-cut bar stock, so they demand larger allowances (e.g., 2–5 mm) compared to 0.5–1 mm for bar stock.
- Processing stages: Allowance is often divided across multiple steps:
-
- Roughing: A large allowance (e.g., 1–3 mm) is removed quickly to shape the workpiece close to its final form, prioritizing speed over precision.
-
- Semi-finishing: A smaller allowance (e.g., 0.1–0.5 mm) refines dimensions, preparing the part for the final pass.
-
- Finishing: A minimal allowance (e.g., 0.05–0.1 mm) achieves the final tolerance and surface finish.
- Tolerance requirements: Parts with strict tolerances (e.g., aerospace components) need more generous allowances to ensure that after final machining, there’s no risk of falling below the minimum dimension.
Examples of typical allowances
- For a steel forging destined for a precision gear: 3–5 mm for roughing, 0.5–1 mm for semi-finishing, and 0.1–0.2 mm for finishing.
- For an aluminum bar stock used in a simple bracket: 1 mm for roughing and 0.2–0.3 mm for finishing.
What happens if allowance is incorrect?
- Too little allowance: Insufficient material may leave defects (e.g., cracks, residual casting flaws) on the final part, or make it impossible to reach the required tolerance, resulting in scrap.
- Too much allowance: Excess material increases machining time, tool wear, and energy consumption, raising production costs. It can also introduce unnecessary stress on the machine, affecting accuracy.
In summary, CNC machining allowance is a carefully calculated buffer that bridges the gap between raw material and a high-quality, precision part. Its proper selection is key to balancing efficiency, cost, and performance in CNC manufacturing.