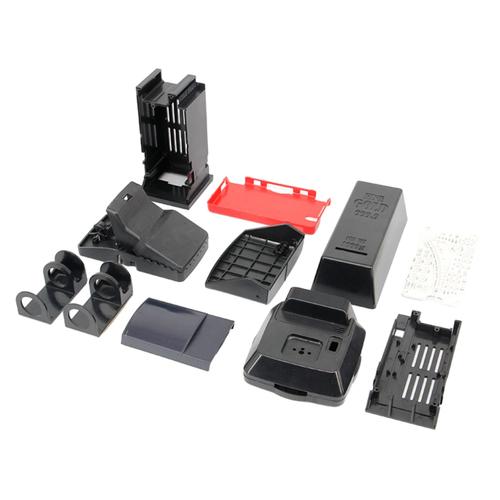
1. Why Custom Electronic Device Plastic Parts
2. Electronic Device Plastic Parts Processing Technologies
- Injection Molding: Melts plastic resin and injects it into precision molds under high pressure, producing parts with complex geometries, tight tolerances (±0.02mm), and consistent wall thickness. Ideal for high-volume production of housings, connectors, and structural components.
- CNC Machining: Uses computer-controlled tools to shape parts from solid plastic blocks, suitable for low-volume production or prototypes requiring intricate details (threaded holes, precise cutouts). Enables quick design modifications.
- 3D Printing: Builds parts layer-by-layer from plastic filaments (ABS, PC) or resins, perfect for rapid prototyping or complex geometries (internal lattices, custom brackets) that are difficult to mold.
- Ultrasonic Welding: Joins plastic components by vibrating them at high frequency, creating strong, seamless bonds without adhesives—ideal for assembling casings or enclosures in devices like headphones.
- Thermoforming: Heats plastic sheets and forms them over molds, cost-effective for large, shallow parts (TV bezels, monitor housings) in medium-volume production runs.
3. Electronic Device Plastic Parts Processing Flow
- Design & Engineering: Collaborate with clients to define part specifications (dimensions, tolerances, functionality) and device requirements (heat output, assembly needs). Use CAD software and FEA simulations to optimize structural integrity and fit.
- Material Selection: Choose plastics based on performance needs—ABS for impact resistance, PC for heat tolerance, POM for low friction, or LCP for high-temperature stability in connectors.
- Mold Fabrication: Create precision steel molds for injection molding, incorporating features like cooling channels and ejector pins to ensure consistent part quality. Molds are designed to replicate intricate details (textured surfaces, micro-features).
- Production: For high volumes, use injection molding; for prototypes or small batches, employ 3D printing or CNC machining. Process parameters (temperature, pressure, cooling time) are optimized for the selected material to prevent warping or defects.
- Finishing: Trim excess material, deburr edges, and apply surface treatments (painting, plating, or texturing) to enhance aesthetics and functionality. Add features like adhesive backings or conductive coatings as needed.
- Assembly Integration: Test parts with other components (circuit boards, metal frames) to ensure proper fit and functionality. Make adjustments to tolerances or design if necessary.
- Quality Testing: Conduct dimensional inspections using CMMs, mechanical testing (impact resistance, tensile strength), and environmental testing (temperature cycling, humidity resistance) to verify performance.
4. Electronic Device Plastic Parts Materials
- ABS (Acrylonitrile Butadiene Styrene): Offers a balance of impact resistance, rigidity, and ease of processing, making it ideal for housings (laptops, gaming consoles) and structural components.
- PC (Polycarbonate): Provides exceptional impact resistance, transparency, and heat tolerance (up to 120°C), suitable for smartphone screens, LED light covers, and high-temperature components.
- POM (Polyoxymethylene): Boasts low friction and high wear resistance, used for moving parts like gears, sliders, and hinge mechanisms in printers and cameras.
- LCP (Liquid Crystal Polymer): Exhibits high thermal stability (up to 260°C) and excellent electrical insulation, perfect for connectors and components in high-frequency devices (5G modems, radar sensors).
- PP (Polypropylene): Features chemical resistance and flexibility, used for battery casings, cable insulation, and lightweight structural parts in portable electronics.
- TPU (Thermoplastic Polyurethane): Offers elasticity and durability, ideal for protective components like phone cases, gaskets, and shock absorbers in wearable devices.
5. Electronic Device Plastic Parts Applications
- Consumer Electronics: Housings for smartphones, laptops, and tablets; buttons, bezels, and battery covers for wearables (smartwatches, fitness trackers); and structural parts for gaming consoles.
- Industrial Electronics: Enclosures for control panels, sensor housings, and cable management clips in factory automation systems; heat-resistant components for power supplies.
- Medical Electronics: Casings for diagnostic devices (blood pressure monitors, ultrasound probes), battery compartments for portable medical tools, and biocompatible parts for patient-worn sensors.
- Automotive Electronics: Connectors, housing for infotainment systems, and sensor brackets in ADAS (Advanced Driver-Assistance Systems); heat-resistant parts for engine control units.
- Aerospace & Defense: Lightweight structural parts for avionics displays, EMI-shielded enclosures for communication devices, and flame-resistant components for cockpit electronics.
- Telecommunications: Router housings, fiber optic connectors, and antenna mounts in 5G infrastructure; cooling fans and vent covers for data center equipment.
6. Electronic Device Plastic Parts Performance Additions
- EMI/RFI Shielding: Apply conductive coatings (nickel, copper) or incorporate metal particles into plastic to block electromagnetic interference, critical for sensitive components like circuit boards and antennas.
- Flame Resistance: Use flame-retardant additives (halogen-based or halogen-free) to meet UL94 V-0 standards, preventing fire spread in devices like power adapters and industrial controllers.
- Thermal Management: Integrate heat-dissipating ribs, graphite films, or metal inserts to improve heat transfer, preventing overheating in high-performance devices (gaming laptops, processors).
- Chemical Resistance: Select materials or coatings that resist oils, solvents, and cleaning agents, ensuring durability in medical devices or industrial electronics.
- Surface Finishes: Apply matte textures to reduce fingerprints, glossy coatings for aesthetics, or anti-scratch treatments (hard coats) to extend part life in consumer devices.
- Adhesive Integration: Pre-apply pressure-sensitive adhesives for easy assembly, eliminating the need for screws or fasteners in slim devices like smartphones and tablets.
7. Electronic Device Plastic Parts Common Questions
Which material is best for high-temperature electronic parts?
LCP (Liquid Crystal Polymer) and PPS (Polyphenylene Sulfide) perform well at temperatures up to 260°C and 200°C respectively, making them ideal for components near heat sources (processors, LEDs). PC (Polycarbonate) works for moderate temperatures (up to 120°C) in housings and structural parts.
Can custom plastic parts be made with tight tolerances?
Yes—injection molding achieves tolerances as tight as ±0.02mm for small parts, suitable for precision components like connectors or sensor mounts. CNC machining can achieve even tighter tolerances (±0.01mm) for critical fits.
Are custom plastic parts cost-effective for small production runs?
For small batches (100–1,000 units), CNC machining or 3D printing avoids expensive mold costs, making them cost-effective. For larger runs (10,000+ units), injection molding becomes more economical as per-unit costs decrease significantly.
How do plastic parts contribute to device lightweighting?
Plastics like ABS and PC weigh 30–50% less than metal alternatives while maintaining sufficient strength, reducing overall device weight—critical for portable electronics (laptops, wearables) and battery-powered devices.
Can plastic parts be recycled?
Many can—ABS, PC, and PP are recyclable in most systems. We offer recycled-content plastics and design for recyclability (mono-material construction) to support sustainability goals.