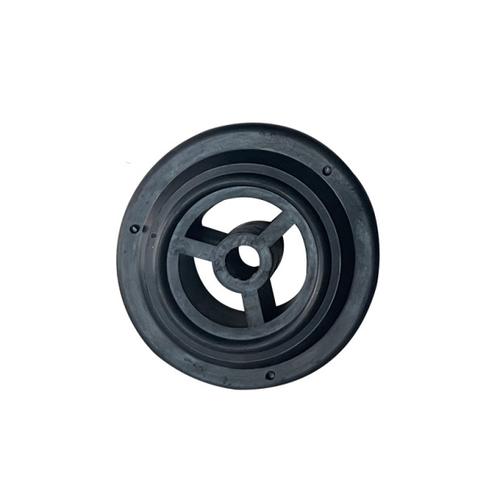
1. Why Custom Rubber Pad Molds
2. Rubber Pad Mold Processing Technologies
- CNC Milling: Shapes mold cavities and cores with precise dimensions (±0.02mm), creating flat surfaces, grooves, or simple 3D features. Ideal for low-to-medium volume production and molds with basic textures.
- EDM (Electrical Discharge Machining): Produces intricate details (fine textures, micro-grooves, or complex patterns) in hardened steel, ensuring sharp edges that transfer clearly to rubber surfaces during molding.
- Laser Engraving: Creates detailed surface textures (grid patterns, logos) with high precision, suitable for molds requiring consistent, repeatable branding or functional textures.
- Compression Mold Fabrication: Constructs molds with two mating plates (top and bottom) that compress rubber material, ideal for thick pads or those with irregular shapes.
- Injection Mold Tooling: Designs molds with runners and gates to inject molten rubber into cavities, suitable for high-volume production of small to medium-sized pads with tight tolerances.
3. Rubber Pad Mold Processing Flow
- Design & Engineering: Collaborate with clients to define pad specifications (size, thickness, hardness) and functional requirements (temperature resistance, chemical compatibility). Use CAD software to design mold cavities, incorporating features like draft angles (1–3°) for easy part ejection.
- Material Selection: Choose mold materials based on production volume and rubber type—tool steel (P20, H13) for high-volume runs, aluminum for low-volume or prototype molds, or stainless steel for molds exposed to corrosive rubber compounds.
- Mold Base Construction: Fabricate the mold frame, including alignment pins, clamping holes, and (for injection molds) runner systems to distribute rubber evenly.
- Cavity Machining: Use CNC milling or EDM to shape the mold cavity, adding textures, grooves, or holes as specified. Ensure uniform wall thickness to prevent rubber curing inconsistencies.
- Heat Treatment: Harden tool steel molds to 50–55 HRC through quenching and tempering, enhancing wear resistance for prolonged use with abrasive rubber compounds.
- Surface Finishing: Polish mold surfaces to Ra 0.8μm or better for smooth rubber pads, or apply textured finishes (sandblasting) to create anti-slip patterns.
- Testing & Calibration: Conduct trial moldings with the target rubber material to verify pad dimensions, hardness, and surface quality. Adjust mold tolerances or heating/cooling parameters as needed.
4. Rubber Pad Mold Materials
- P20 Tool Steel: A pre-hardened alloy steel (30–35 HRC) offering good machinability and durability. Ideal for medium-volume production (10,000–100,000 pads) using natural rubber or EPDM.
- H13 Tool Steel: A heat-resistant steel (50–55 HRC) suitable for high-volume production (100,000+ pads) or molds used with high-temperature rubber (silicone, Viton). Resists thermal fatigue from repeated curing cycles (150–300°C).
- Aluminum (6061, 7075): A lightweight option for low-volume runs or prototypes, enabling faster machining and reduced energy use. Best for non-abrasive rubber types and short production cycles.
- Stainless Steel (304, 420): Used for molds exposed to corrosive rubber additives or cleaning agents, preventing rust and ensuring long-term dimensional stability in humid environments.
5. Rubber Pad Mold Applications
- Automotive Industry: Molds for door seals, dashboard pads, and under-hood heat shields, using EPDM or silicone rubber for temperature and chemical resistance.
- Industrial Machinery: Molds for anti-vibration pads, machine feet, and conveyor belt buffers, producing thick, durable pads (natural rubber or SBR) to absorb shocks and reduce noise.
- Consumer Products: Molds for furniture pads, floor mats, and tool handles, incorporating anti-slip textures and custom sizes to fit specific products.
- Medical Devices: Molds for silicone pads used in patient beds, surgical tools, and diagnostic equipment, meeting biocompatibility standards and requiring precise hardness (50–70 Shore A).
- Aerospace & Defense: Molds for high-performance rubber pads (Viton, fluorocarbon) used in aircraft seals, missile components, and military vehicles, withstanding extreme temperatures and pressure.
6. Rubber Pad Mold Performance Additions
- Texture Optimization: Laser-etched or EDM-machined patterns (diamond grids, raised dots) that enhance friction, making pads suitable for anti-slip applications (workstation mats, ladder feet).
- Heating/Cooling Channels: Integrated channels in injection or compression molds to control curing temperature (150–200°C for most rubbers), reducing cycle times by 20–30% and ensuring uniform material properties.
- Ventilation Systems: Microscopic vents (0.01–0.05mm) to release trapped air during molding, preventing defects like bubbles or incomplete filling in thick pads.
- Interchangeable Inserts: Modular mold components that allow quick changes to pad dimensions or textures, reducing downtime for manufacturers producing multiple pad variants.
- Hardness Control Features: Precision-machined cavity depths and uniform pressure distribution systems that ensure consistent rubber hardness across large or multi-cavity molds.
7. Rubber Pad Mold Common Questions
What is the typical lifespan of a rubber pad mold?
Lifespan depends on material and usage: H13 steel molds last 500,000–1,000,000 cycles; P20 steel molds 100,000–500,000 cycles; aluminum molds 10,000–50,000 cycles. Abrasive rubber compounds (filled with silica or carbon) may reduce lifespan by 20–30%.
Can one mold produce pads with different hardness levels?
No—hardness is determined by rubber compound formulation, not mold design. However, molds can be used with different rubber types (e.g., EPDM for 60 Shore A, silicone for 40 Shore A) as long as material flow properties are compatible.
How do molds accommodate thick rubber pads (20mm+)?
Thick pads require compression molding with slow curing cycles to prevent internal bubbles. Molds for such pads include extra ventilation, gradual pressure application systems, and heating channels distributed evenly across the cavity.
What is the lead time for a custom rubber pad mold?
Simple molds (flat pads, basic textures) take 2–4 weeks; complex molds (intricate textures, multi-cavity designs) require 6–8 weeks. Rush options are available for prototypes or urgent orders, reducing lead time by 30–50%.
How are molds tested for quality?
Trial runs produce sample pads that are inspected for dimensional accuracy (using calipers or CMMs), hardness (Shore durometer), and surface defects. Molds are adjusted if samples fail to meet specifications, ensuring consistent production quality.