With 26 years of expertise in automotive-grade plastic processing, Xiamen Goldcattle specializes in custom automotive plastic parts—tailored for interior trim, exterior components, engine bay parts, and electronic enclosures. Leveraging advanced injection molding, 3D printing, and precision machining technologies, we deliver parts that meet strict automotive standards for durability, safety, and aesthetics. Backed by ISO/TS 16949 certification, IATF 16949 compliance, and partnerships with 20+ global automakers, we support low-volume prototypes to mass production (100,000+ units/month) with ±0.02mm dimensional tolerance.
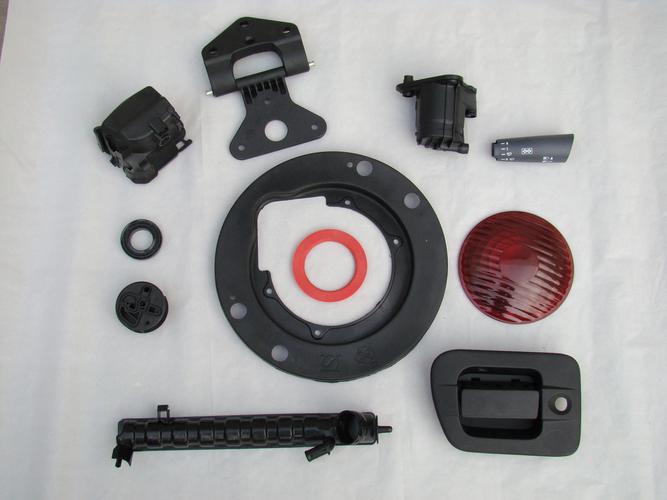
Core Processing Technologies: Engineering for Automotive Excellence
Automotive plastic parts demand precision beyond standard manufacturing—Goldcattle integrates cutting-edge technologies to meet the industry’s rigorous requirements for temperature resistance, impact strength, and long-term reliability.
1. High-Precision Injection Molding for Complex Components
-
Multi-cavity & high-speed injection: Equipped with 50+ automotive-grade injection molding machines (20-500 tons clamping force), including Engel e-motion and Fanuc Roboshot models. Our 16-cavity molds achieve cycle times as low as 15 seconds, producing interior trim parts (e.g., dashboard panels, door handles) with consistent dimensional accuracy (±0.03mm).
- Gas-assisted injection molding: For thick-walled parts (e.g., steering wheel covers, gear shift knobs), this technology reduces warpage by 40% and cuts material usage by 15% by injecting nitrogen gas to create hollow sections without compromising strength.
- Insert molding: Integrates metal inserts (e.g., screws, bushings) into plastic parts during molding, eliminating post-assembly steps and improving structural integrity—ideal for engine bay brackets and electronic connectors.
-
Overmolding technology: Bonds two or more materials (e.g., rigid PP with soft TPE) in a single process, creating parts like ergonomic grab handles (hard core for strength, soft outer layer for grip) and weatherstripping (rigid base with flexible sealing edges).
2. Advanced Mold Manufacturing & Tooling
- Precision mold design: Using CAD/CAE software (UG NX, Moldflow), our engineering team simulates filling, cooling, and warpage to optimize mold structure. For example, in dashboard panel molds, we design 3D-printed conformal cooling channels that reduce cooling time by 25% and improve part flatness to ≤0.5mm/m.
- High-wear resistance molds: Adopts H13 tool steel with nitriding treatment (surface hardness ≥60HRC) for molds, ensuring a lifespan of 1 million+ shots—critical for high-volume production of exterior parts (e.g., bumper covers, fender liners).
- Rapid prototyping molds: Aluminum alloy prototype molds (5-7 day turnaround) support low-volume testing (100-500 units), allowing automakers to validate fit, form, and function before investing in mass production tooling.
3. Surface Treatment & Functional Coating
- Automotive-grade painting: In-house paint shop with 3-stage pretreatment (degreasing, phosphating, passivation) and electrostatic spraying. Offers matte, glossy, or metallic finishes with UV resistance (ΔE ≤1 after 3,000 hours of xenon lamp testing), suitable for exterior parts like mirror housings and pillar trims.
- Texturing & graining: Mold texturing (Ra 0.8-3.2μm) creates leather-like or carbon fiber patterns on interior parts (door panels, center consoles), enhancing tactile feel and hiding scratches—meeting OEM standards for luxury and mainstream vehicles.
- Plating for plastic: Electroless nickel plating on ABS parts (e.g., door handles, grille accents) provides corrosion resistance (500 hours salt spray test) and a metallic appearance, replacing heavier metal components to reduce vehicle weight.
4. Strict Quality Control & Automotive Certifications
- TS 16949-compliant processes: Implements APQP (Advanced Product Quality Planning) and PPAP (Production Part Approval Process) to ensure parts meet customer-specific requirements (e.g., Ford Q1, GM GP-12).
- Dimensional inspection: Uses Zeiss Contura G2 coordinate measuring machines (CMM) with ±0.001mm accuracy to inspect critical dimensions—such as mounting holes for engine sensors (position tolerance ≤0.1mm) and gap/flush for exterior panels (≤0.5mm).
- Material testing: In-house lab conducts tensile strength (≥30MPa for PP parts), impact resistance (≥20kJ/m² for -40℃ cold impact), and VOC (volatile organic compounds) testing (≤50μgC/g, meeting China GB/T 27630 and EU VDA 278 standards for interior parts).
- Environmental durability: Tests include:
- UV aging (3,000 hours, no cracking or color fading)
- Thermal cycling (-40℃ to 80℃, 500 cycles, no deformation)
- Chemical resistance (resistance to engine oil, gasoline, and cleaning agents for 24 hours)
Material Expertise: Matching Plastics to Automotive Applications
Automotive parts face diverse environments—from extreme temperatures in engine bays to high-touch interior surfaces. Goldcattle’s material science team selects and modifies plastics to meet specific performance demands:
Material | Modified Formulations | Application Scenarios | Key Technical Properties |
---|---|---|---|
PP (Polypropylene) | Glass fiber-reinforced (20-30% GF), heat-stabilized | Interior trim (dashboard, door panels), underhood covers | Low cost, high impact resistance (-40℃), VOC compliance, density 0.9-1.1g/cm³ (reduces vehicle weight). |
ABS (Acrylonitrile Butadiene Styrene) | Flame-retardant (UL94 V0), weather-resistant | Instrument panels, exterior mirror housings, grille components | Excellent surface finish for painting/plating, impact strength ≥25kJ/m², heat resistance up to 80℃. |
PA (Nylon) | Glass fiber-reinforced (30-50% GF), mineral-filled | Engine bay parts (oil pans, coolant reservoirs), structural brackets | High temperature resistance (120-150℃), chemical resistance to oils/fluids, tensile strength ≥80MPa. |
POM (Acetal) | Low-friction, wear-resistant | Door lock components, window regulators, gear parts | Self-lubricating, high fatigue resistance (10⁷ cycles), dimensional stability (moisture absorption ≤0.2%). |
PC/ABS Blend | Impact-modified, UV-stabilized | Exterior body parts (fender extensions), electronic enclosures | Balances PC’s heat resistance (120℃) and ABS’s processability, suitable for parts requiring both strength and aesthetics. |
Customization Capabilities: From Prototype to Mass Production
Automotive projects require flexibility—whether you need 100 prototype parts or 1 million production units, Goldcattle delivers tailored solutions:
- Design engineering support: Our DFM (Design for Manufacturability) team reviews 3D models (STEP/IGS files) to optimize wall thickness (uniform 2-3mm to avoid sink marks), draft angles (≥1.5° for easy demolding), and rib design (height ≤3×thickness to prevent warpage).
- Rapid prototyping: Uses SLA 3D printing (0.1mm layer thickness) and CNC machining to produce functional prototypes in 2-3 days, ideal for fit-checks and assembly testing.
- Low-volume production: 1,000-10,000 units via aluminum molds or 3D printing, suitable for niche vehicles, aftermarket parts, or pre-production validation.
- Mass production: 100,000+ units/month with multi-cavity steel molds, supported by automated production lines (robotic part removal, vision inspection) to ensure 99.9% yield.
- OEM/ODM collaboration: Partner with automakers and Tier 1 suppliers on new vehicle development, providing mold flow analysis, material selection, and cost optimization from the concept stage.
Case Studies: Solving Automotive Manufacturing Challenges
-
Lightweight engine cover for a new energy vehicle (NEV) brand:
Challenge: The client needed a lightweight engine cover (target weight reduction 30% vs. metal) with heat resistance up to 120℃ and noise reduction.
Solution: Goldcattle selected 30% glass fiber-reinforced PA6, optimized the rib structure via FEA simulation, and added a foam layer for sound absorption. Result: Weight reduced by 35% (from 2.8kg to 1.8kg), passed 1,000-hour 120℃ heat aging test, and noise reduction of 5dB. -
Low-VOC interior door panel for a luxury automaker:
Challenge: Meet strict EU VDA 278 standards (VOC ≤30μgC/g) while maintaining texture and impact resistance.
Solution: Used modified PP with low-odor additives, optimized injection parameters (lower melt temperature 180-200℃), and added a water-based coating. Result: VOC content 22μgC/g, passed customer audit, and tactile feel rated 4.8/5 in user testing.
Why Choose Goldcattle for Automotive Plastic Parts?
- 26 years of automotive focus: Trusted by 20+ global automakers and Tier 1 suppliers (e.g., Bosch, Magna) for consistent quality.
- Integrated manufacturing: From material compounding to final assembly, in-house processes reduce lead times by 20% and ensure quality control.
- Cost optimization: Design-to-cost engineering reduces material usage by 10-15% without compromising performance.
- Global compliance: Parts meet standards including ISO/TS 16949, EU REACH, RoHS, and China GB standards.
Start Your Automotive Plastic Parts Project Today
Whether you’re developing a new vehicle model or upgrading existing parts, Goldcattle’s precision, expertise, and flexibility ensure your automotive plastic components meet the highest standards.
Contact our automotive team: Send your 3D drawings or specifications to [email], and receive a DFM report + sample quote within 24 hours. Let’s drive innovation together.
“Goldcattle’s attention to detail on our dashboard panel project was impressive—their mold flow analysis prevented warpage issues we’d faced with previous suppliers, and the low-VOC material met our luxury brand’s standards.” — Procurement Manager, a European premium automaker