Poor surface finish in CNC parts can be resolved by optimizing tool selection, adjusting cutting parameters, enhancing coolant systems, and refining material handling. Key steps include using sharp, coated tools, controlling feed rates and spindle speeds, ensuring effective chip evacuation, and post-processing (polishing, deburring) to achieve desired Ra values, critical for both functional and aesthetic requirements.
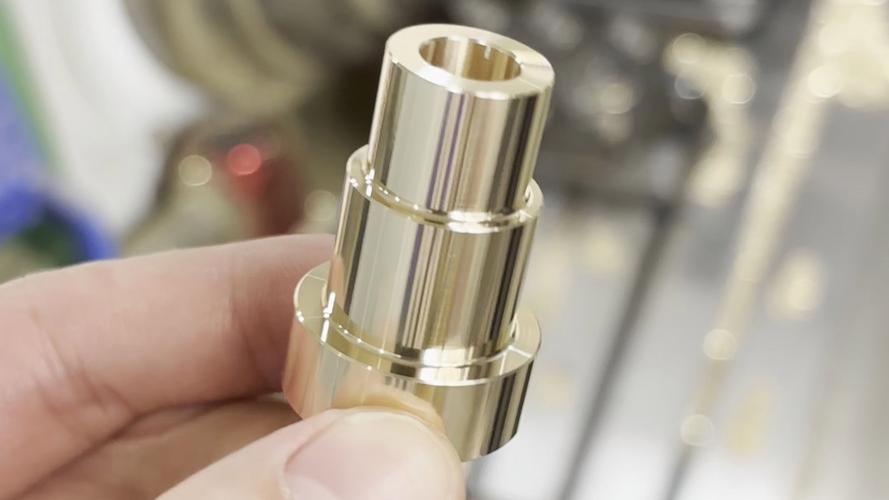
Detailed Analysis of Resolving CNC Surface Finish Issues
1. Tool Selection & Geometry
The right tooling directly impacts surface smoothness by minimizing friction and chip adhesion:
-
Tool Material & Coating:
- Carbide Tools: Superior to high-speed steel (HSS) for hard materials (steel, titanium) due to higher hardness (90–95 HRA). Coated with TiAlN (titanium aluminum nitride) or AlCrN (aluminum chromium nitride), they reduce heat and friction, achieving Ra 0.8–1.6μm on steel parts—ideal for hydraulic components requiring leak-free seals.
- Diamond Tools: Polycrystalline diamond (PCD) tools excel with non-ferrous materials (aluminum, brass), producing Ra <0.05μm for optical or decorative parts (e.g., smartphone frames). Their extreme hardness prevents edge wear, critical for high-volume production.
- Geometry Optimization: Tools with sharp cutting edges (relief angle 5–10°) and polished flutes reduce material tearing. For finishing, ball-nose end mills with large radii (10–20mm) minimize scallop height (the step between tool paths) to <0.005mm, improving surface uniformity on curved parts (e.g., mold cavities).
-
Tool Maintenance: Dull tools cause material smearing or tearing, increasing Ra values. Implement tool wear monitoring (via in-process probing) and replace tools when edge rounding exceeds 0.02mm—critical for maintaining consistency in medical parts (e.g., surgical instrument handles) where smoothness prevents tissue damage.
2. Cutting Parameter Optimization
Precise control of spindle speed, feed rate, and cutting depth minimizes surface defects:
-
Spindle Speed: Higher speeds reduce cutting forces and heat buildup, improving finish. For aluminum (6061), 15,000–30,000 RPM with carbide tools produces Ra 0.4–0.8μm; for steel (4140), 8,000–15,000 RPM balances tool life and finish. Too low a speed (e.g., <3,000 RPM for aluminum) causes built-up edge (BUE), leaving rough, uneven surfaces.
-
Feed Rate: Lower feed rates (0.01–0.05 mm/rev) for finishing reduce tool marks. For example, a feed rate of 0.02 mm/rev on a 10mm carbide end mill achieves Ra 0.8μm on brass, while 0.1 mm/rev increases Ra to 3.2μm. However, excessively slow feeds waste time—optimize based on material: use 0.03 mm/rev for titanium (avoiding work hardening) and 0.05 mm/rev for plastic (preventing melting).
-
Cutting Depth: Finish passes with minimal depth (0.1–0.3mm) avoid distorting the workpiece. For thin-walled parts (e.g., 0.5mm aluminum brackets), a 0.1mm finish cut removes residual tool marks from roughing without causing vibration-induced chatter.
3. Coolant & Chip Evacuation
Effective cooling and chip removal prevent re-cutting and heat-induced defects:
-
Coolant Type & Application:
- Flood Cooling: Uses high-pressure (70–100 bar) coolant to flush chips and reduce tool temperature. For steel, oil-based coolants (with EP additives) minimize friction; for aluminum, water-soluble coolants (5–10% concentration) prevent corrosion and BUE.
- Mist Cooling: Ideal for high-speed machining of titanium, where fine mist (air + coolant) improves chip evacuation in deep slots or holes, avoiding chip entanglement that scratches surfaces.
-
Chip Breaking: Use tools with chip breakers (e.g., grooved inserts for turning) to fragment chips, preventing long strings from dragging across the workpiece. For example, turning brass with a 35° rake angle insert breaks chips into small pieces, leaving a smooth Ra 0.8μm surface vs. Ra 2.0μm with a straight insert.
4. Material-Specific Strategies
Different materials require tailored approaches to surface finish:
-
Metals:
- Aluminum & Brass: Soft and ductile, prone to BUE. Use sharp tools, high speeds, and coolant to prevent smearing. For mirror finishes (Ra <0.02μm), follow machining with vibratory polishing (ceramic media + compound) for 1–2 hours.
- Steel & Titanium: Harder materials need coated carbide tools and moderate speeds. Post-machining, abrasive flow machining (AFM) can refine internal surfaces (e.g., hydraulic valve bores) to Ra 0.05μm, critical for fluid flow efficiency.
-
Plastics & Composites:
- ABS & PC: Prone to melting at high speeds. Use low spindle speeds (3,000–5,000 RPM) and uncoated carbide tools to avoid heat-induced burrs. For a matte finish (Ra 1.6μm), lightly sand with 400-grit paper post-machining.
- Carbon Fiber Reinforced Polymers (CFRP): Fibers can fray, creating rough surfaces. Use PCD tools with negative rake angles (5–10°) and low feeds (0.01–0.03 mm/rev) to shear fibers cleanly, achieving Ra 1.6μm for aerospace panels.
5. Process & Tool Path Optimization
Refining machining sequences and tool paths reduces surface irregularities:
-
Machining Order: Always rough first (removing 70–80% of stock) to avoid stress-induced distortion, then semi-finish (0.5mm stock) to smooth roughing marks, and finish with a light pass (0.1–0.3mm). This sequence ensures the final cut works with a stable, low-stress workpiece—critical for complex parts like turbine blades.
-
Tool Path Strategy:
- Climb Milling: The tool cuts into the workpiece, reducing chatter and leaving finer finishes than conventional milling. Use this for flat surfaces (e.g., mold bases) to achieve Ra 0.8μm vs. 1.6μm with conventional milling.
- Continuous Contact: For 3D surfaces (e.g., automotive body panels), 5-axis machining maintains constant tool contact, minimizing scallop height. A 20mm barrel cutter with a 10mm radius reduces scallops to <0.005mm, far better than a 6mm ball-nose end mill.
6. Post-Processing for Enhanced Finish
Secondary operations address residual defects:
-
Deburring: Remove micro-burrs from edges using abrasive flow machining (AFM) or robotic brushing. For medical tools (e.g., scalpels), AFM polishes edges to Ra <0.02μm, preventing tissue damage.
-
Polishing:
- Mechanical Polishing: Use progressively finer abrasives (120→400→800 grit) for metals, followed by buffing with rouge compound for mirror finishes (Ra <0.05μm) on decorative parts (e.g., jewelry components).
- Electropolishing: For stainless steel parts (e.g., food processing equipment), this electrochemical process dissolves surface irregularities, achieving Ra 0.02–0.05μm and improving corrosion resistance.
7. Industry-Specific Requirements
Different sectors demand tailored surface finishes, driving targeted solutions:
-
Aerospace: Engine components (e.g., fuel injectors) require Ra <0.4μm to minimize drag and fuel consumption. Use 5-axis machining with PCD tools and in-process laser scanning to verify finish.
-
Medical Devices: Surgical instruments need Ra <0.02μm to prevent bacterial adhesion. Post-machining, electropolish critical surfaces and inspect with white light interferometers.
-
Automotive: Transmission gears require Ra 0.8–1.6μm for smooth operation. Hobbed gears are finish-ground with vitrified CBN wheels to achieve precise tooth profiles and surface texture.
-
Electronics: Connector pins (brass) need Ra <0.1μm to ensure reliable electrical contact. Finish with diamond turning (20,000 RPM) and ultrasonic cleaning to remove residual particles.
8. Troubleshooting Common Surface Defects
-
Chatter Marks: Caused by vibration. Fix by increasing spindle speed, using shorter tool overhangs, or adding damping fixtures. For example, reducing tool overhang from 50mm to 25mm on a 10mm end mill eliminates chatter on aluminum.
-
Built-Up Edge (BUE): Forms when material adheres to the tool. Solve with coolant, sharper tools, or higher speeds—e.g., increasing aluminum machining speed from 5,000 to 20,000 RPM dissolves BUE.
-
Scratches/Scuffs: Caused by loose chips or dirty coolant. Use high-pressure coolant to flush chips, and filter coolant to 5μm to remove abrasive particles.
By integrating tool optimization, parameter tuning, material-specific strategies, and post-processing, CNC machining can consistently achieve precise surface finishes, meeting functional and aesthetic demands across industries.