Keywords: 3D Printing, Five – axis CNC, Topology Optimization“Can you make parts exactly the same as the concept drawings?” – This is the most frequently asked question by customers.
Reverse Engineering Scanning: A handheld 3D scanner (with an accuracy of ±0.02mm) quickly captures prototype data and generates a CAD model in 10 minutes.
Simulation Verification: ANSYS is used to simulate extreme working conditions (such as the deformation of a turbine blade at 200°C), detecting design flaws in advance.
Innovative Process: Metal 3D printing (SLM technology) enables the creation of hollow structures that cannot be processed by traditional CNC. It reduces weight by 30% while improving heat dissipation efficiency.
Case: A modified car brand redesigned the suspension arm using topology optimization algorithms, increasing strength by 20% and reducing material usage by 15%.
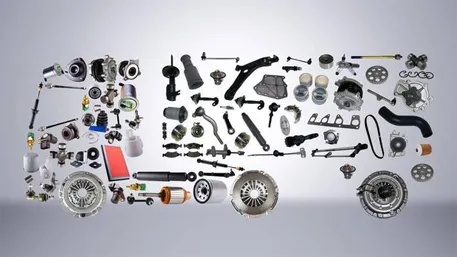
Keywords: Carbon Fiber, 7075 Aviation Aluminum, PA6 – GF30
“Is this material crash – resistant? Will it deform at high temperatures?” – Choosing the wrong material could lead to failure.
Metals:
- 6061 – T6 Aluminum Alloy: The first choice for lightweighting, with good machining performance, but its fatigue strength is inferior to 7075.
- Titanium Alloy TC4: Used for high – performance exhaust manifolds, 40% lighter than stainless steel and can withstand temperatures up to 800°C.
Non – metals:
- Carbon Fiber Woven Pre – impregnated Material: Tensile strength of 5000MPa, but the inter – laminar shear strength is a weak point.
- Special Engineering Plastics: PEI (Polyetherimide) is used for engine covers, remaining undeformed after long – term use at 180°C.
Pitfall Avoidance Guide: Don’t use ordinary aluminum alloy for modified brake calipers – mismatched thermal expansion coefficients could lead to brake failure!
Demand Communication: Clearly define the usage scenario (track racing or urban commuting?)
DFM Analysis: Use Geomagic Control to check if the wall thickness is uniform (recommended to be ≥2.5mm)
Prototype Verification: Road – test the 3D – printed prototype on the vehicle and collect vibration data to correct the design
Mass Production Control: Sample and inspect every 50 pieces, and conduct full – size comparison with a coordinate measuring machine
Lesson Learned: A customer skipped the prototyping stage and directly opened the mold. As a result, the oil pan interfered with the transmission, resulting in a loss of 120,000 yuan in mold costs!
Five – axis CNC: The DMG MORI DMU series from Germany, with a curved – surface processing accuracy of ±0.01mm
2000 – ton Die – casting Machine: Reduces the production time of aluminum alloy wheels from 12 hours per piece to 20 minutes
Vacuum Carburizing Furnace: The surface hardness of gears reaches HRC60, while the core maintains HRC38 toughness
Industry Truth: Many small factories pretend to use five – axis machining with three – axis machine tools – you can tell by checking if the tool marks are continuous!
Fatigue Test: The steering wheel skeleton needs to pass 500,000 torsion tests (the national standard only requires 100,000 times)
Salt Spray Test: Plated parts should not rust in a 5% NaCl fog for 500 hours
Destructive Sampling Inspection: Randomly select 1 piece from each batch for cutting and metallographic analysis
Data Speaks: The connecting rod we made for a racing team withstood a torque of 1200N·m in the bench test (the original part breaks at 800N·m).
Laser Texturing: Etch 0.1mm – deep textures on the mold to give plastic parts a metal brushed effect
Micro – arc Oxidation: Generate a 10μm ceramic layer on the surface of magnesium – alloy wheels, increasing scratch resistance by 5 times
Variable – thickness Coating: Coat an infrared – reflecting film on the inner side of the headlight lens, with a light transmittance of 92% compared to 85% for ordinary parts
Cutting – edge Technology Alert: The plasma electrolytic polishing technology under trial can make the inner – wall roughness of stainless – steel exhaust pipes Ra≤0.1μm, increasing exhaust efficiency by 8%!
Price Composition Example (Aluminum Alloy Pedal Set)
Project |
Proportion |
Description |
Materials |
15% |
6061 aluminum bar stock |
Processing |
40% |
Five – axis CNC labor cost |
Surface Treatment |
20% |
Hard anodizing + laser engraving |
Inspection |
15% |
X – ray flaw detection + dynamic balance test |
Profit |
10% |
|
Cost – saving Tips:
- When the batch size reaches 100 pieces, the die – casting process can be used to reduce costs by 35%.
- Booking 2 months in advance can enjoy an off – season discount (up to 15%).
Service Classification:
- Basic Customization: LOGO engraving, color change (delivered in 3 days)
- In – depth Customization: Structural modification (requires re – opening the mold, 4 – 8 weeks)
- Joint R & D: Development of a vehicle’s aerodynamic kit (starting from 6 months)
User Participation: Through the VR virtual assembly system, customers can adjust the installation angle of parts in real – time, achieving a “what you see is what you get” experience.
Q1: How long does it take to customize a part?
- Simple modified parts: 3 – 7 days (such as engraved license plate frames)
- Complex functional parts: 4 – 8 weeks (such as custom – made turbocharger housings)
Q2: What is the minimum order quantity?
- 3D printing: 1 piece
- CNC machining: Usually 5 pieces
- Die – casting: More than 100 pieces
Q3: How to ensure compatibility with the original vehicle?
- Provide the original parts or the vehicle’s VIN code.
- Use a FARO measuring arm to obtain chassis data (with an accuracy of ±0.025mm).
Q4: Will rainy days affect carbon – fiber parts?
Ordinary resin – based carbon fiber is afraid of moisture. It is recommended to choose:
- Aviation – grade cyanate ester resin (moisture – and heat – resistant)
- Spray a polyurethane clear coat on the surface.
Q5: Are modified custom parts legal?
In China, they need to pass:
- GB/T 24545 – 2023 “Technical Requirements for Automobile Modification Safety”
- Submit a change registration (file with the vehicle management office)
For exports to Europe and the US, they need to comply with:
- EU ECE R110 (for gas system modifications)
- US DOT certification (for lighting components)
Customizing auto parts is a game between technology and art. From the material laboratory to the processing workshop, every link requires obsessive rigor. But when you hold the exclusive steering wheel and listen to the tailor – made exhaust sound, you’ll understand – extreme personalization is never just cold metal and plastic. It’s a dialogue between engineers and car enthusiasts, jointly composed.