Aluminum has a low density, approximately one – third that of iron or copper, making it extremely lightweight. However, its strength is not low. The strength of some aluminum alloys can be comparable to that of high – quality steel. For example, 6061 aluminum alloy is commonly used in fields such as new energy vehicle bodies, ships, and rail transit, where high requirements are placed on strength, weldability, and corrosion resistance. 7075 aluminum alloy is often used in aerospace fields such as aircraft structure manufacturing.
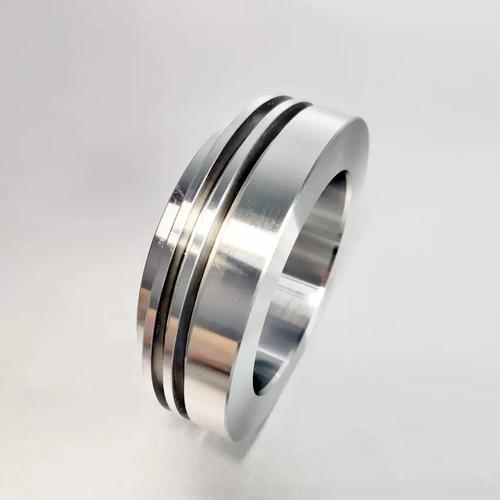
Material Characteristics in CNC Aluminum Machining
As we just mentioned, 6061 and 7075 aluminum alloys are quite common in CNC aluminum machining. 6061 aluminum alloy has a high alloy content, good hardness, and excellent comprehensive performance, making it suitable for various processing scenarios that require a certain level of strength. 7075 aluminum alloy, as a super – hard aluminum alloy, has extremely high strength and is a “regular” in the aerospace field, where requirements for material strength, hardness, and flatness are almost demanding. However, aluminum alloys also have weaknesses. They have low hardness and large thermal deformation. During the machining process, they are prone to deformation due to factors such as cutting heat and machining stress, which is also a key problem to be overcome during processing.
Technical Principle of CNC Aluminum Machining
The core of CNC aluminum machining is CNC (Computer Numerical Control) technology. Simply put, by writing a numerical control program, the computer controls the movement of each axis of the machine tool, such as the X, Y, Z axes, and the rotary axes, etc., thereby precisely controlling the relative position and movement trajectory between the tool and the workpiece. For example, if we want to machine an aluminum part with a complex shape, we first draw the 3D model of the part in computer – aided design (CAD) software, and then use computer – aided manufacturing (CAM) software to generate CNC machining codes. After the machine tool reads these codes, it can command the tool to perform a series of machining operations such as milling, drilling, boring, and tapping. Moreover, the entire process has a high degree of automation, which can greatly improve processing efficiency and accuracy.
Process of CNC Aluminum Machining
Pre – processing Preparation
After receiving the part drawing, the engineer first needs to analyze the technical requirements of the part, such as its shape, dimensional accuracy, and surface roughness. Based on these, select the appropriate aluminum alloy material and determine the processing process route. For example, decide which surface to machine first, what tool to use, and how to set the cutting parameters. At the same time, the machine tool needs to be adjusted to ensure that all its accuracy indicators meet the requirements, and the corresponding fixtures need to be prepared to clamp and fix the aluminum workpiece.
Machining Stage
Import the prepared numerical control program into the machine tool control system and start the machine tool. The tool begins to cut the aluminum workpiece according to the path set in the program. In the case of milling, the tool rotates at high speed and gradually removes the excess aluminum material to mill the workpiece into the shape required by the design. When drilling, the drill bit drills holes with qualified accuracy at the specified positions. Tapping is to machine threads in the existing holes. During the machining process, the operator should always pay attention to the running status of the machine tool, the cutting sound, the shape of the chips, etc., to ensure the normal progress of the machining.
Post – processing Treatment
After the machining is completed, remove the part from the machine tool, remove impurities such as cutting fluid and chips remaining on the surface of the part. Then, conduct a dimensional accuracy inspection on the part. Use measuring tools such as calipers, micrometers, and coordinate measuring machines to check whether the actual dimensions of the part are within the tolerance range specified in the drawing. If there are dimensional deviations, rework may be required. For parts with surface quality requirements, surface treatment processes such as grinding, polishing, and anodizing may also be necessary to improve the appearance quality and corrosion resistance of the part.
Characteristics of CNC Aluminum Machining
High Precision
The numerical control system can accurately control the movement trajectory of the tool. The machining accuracy can easily reach ±0.01mm or even higher, which can meet the extremely high requirements for part accuracy in industries such as aerospace and automotive manufacturing. For example, the aluminum alloy cylinder block of an automobile engine has a complex internal structure and high dimensional accuracy requirements. CNC aluminum machining can complete the machining task well and ensure the stable performance of the engine.
High Efficiency
Compared with traditional manual machining or machining on ordinary machine tools, CNC aluminum machining can achieve automated continuous machining. One machine tool can complete multiple processes simultaneously, reducing the number of workpiece clamping times and auxiliary time. Moreover, parameters such as the spindle speed and feed rate of the machine tool can be adjusted quickly according to the processing requirements, greatly shortening the processing cycle. For example, when mass – producing aluminum alloy radiators, a CNC machining center can quickly complete processes such as milling fins and drilling for installation, significantly improving production efficiency.
Ability to Machine Complex Shapes
With the multi – axis linkage function, CNC aluminum machining can machine various complex curved surfaces and special – shaped structures. For example, the aluminum alloy impeller of an aero – engine has blades with complex spatial curved surfaces. Through five – axis linkage CNC machining, the tool can cut the impeller from different angles to accurately machine the shape that meets the design requirements.
Common Machining Problems in CNC Aluminum Machining and Solutions
Deformation Problem
As mentioned before, aluminum alloys have large thermal deformation and are prone to deformation during the machining process due to factors such as cutting heat and clamping force. Solutions include using appropriate fixtures to clamp the workpiece evenly and avoid excessive local stress; optimizing cutting parameters, reducing the cutting speed and feed rate to reduce the cutting force, and at the same time increasing the flow rate of the cutting fluid to fully cool and carry away the cutting heat; adopting a symmetric machining method to balance the machining stress.
Fast Tool Wear
Aluminum alloys have low hardness but high viscosity. During machining, chips are prone to adhere to the tool, accelerating tool wear. Carbide tools, especially coated carbide tools such as TiAlN – coated tools, can be selected to improve tool wear resistance; reasonably select the geometric parameters of the tool, such as increasing the rake angle of the tool to make the cutting more brisk; adopt a high – pressure cooling system to spray the cutting fluid directly onto the cutting edge of the tool to wash away the chips, reduce the tool temperature, and reduce tool wear.
Poor Surface Quality
Problems such as failure to meet the required surface roughness, tool marks, and ripples may occur. At this time, adjust the cutting parameters, select appropriate cutting speed, feed rate, and cutting depth to make the cutting process more stable; check whether the tool is worn and replace the worn tool in a timely manner; optimize the tool path to avoid frequent start – stop and reversal of the tool to ensure the continuity of the machined surface.
Applications of CNC Aluminum Machining in Various Fields
Aerospace Field
Many components of aircraft, such as fuselage frames, wings, and engine parts, are made of aluminum alloys. CNC aluminum machining can machine aluminum alloy parts with high precision, high strength, and complex shapes, meeting the strict requirements of the aerospace industry for part lightweight and high – performance. For example, the aluminum alloy landing gear of an aircraft is processed by CNC to ensure its strength and dimensional accuracy, ensuring the safety of aircraft take – off and landing.
Automotive Manufacturing Field
Automotive engine blocks, cylinder heads, wheels, and body structural parts, etc., widely use aluminum alloy materials. CNC aluminum machining helps automobiles achieve lightweight, reduce fuel consumption, and at the same time improve the accuracy and quality of automotive parts, enhancing the overall performance of the vehicle. For example, aluminum alloy wheels can be manufactured into products with beautiful shapes and high strength through CNC machining.
Electronic Equipment Field
The casings and radiators of electronic devices such as mobile phones, tablets, and laptops often use aluminum alloy materials. CNC aluminum machining can machine aluminum alloy parts that are thin, have an exquisite appearance, and good heat dissipation performance, meeting the dual requirements of electronic devices for appearance and performance. For example, the aluminum alloy casing of a mobile phone, after processing procedures such as CNC milling, grinding, and anodizing, not only has a comfortable hand – feel but also has good wear – resistance and corrosion – resistance.
Skills and Key Points of CNC Aluminum Machining
Tool Selection
Select tools according to the characteristics of the aluminum alloy material and the processing technology. For rough machining, a carbide – coated end – mill can be selected to improve processing efficiency; for finish machining, a diamond – coated tool can be selected to ensure surface quality. The cutting edge of the tool should be sharp, and the geometric parameters such as the rake angle and clearance angle should be reasonable to reduce cutting force and cutting heat.
Optimization of Cutting Parameters
The three cutting parameters of cutting speed, feed rate, and cutting depth are interrelated. They should be determined comprehensively according to factors such as the hardness of the aluminum alloy material, the tool material and size, and the processing technology requirements. Generally, when machining aluminum alloys, the cutting speed can be appropriately increased, the feed rate should not be too large, and the cutting depth should be reasonably selected according to the machining allowance of the part. Through multiple tests, find the best parameter combination to ensure both processing efficiency and processing quality.
Chip Handling
The chips generated during the machining of aluminum alloys are relatively sticky and are prone to winding around the tool and the workpiece, affecting the machining. High – pressure air blowing or large – flow cutting fluid flushing can be used to remove the chips. At the same time, optimize the tool path to ensure the smooth discharge of chips and avoid secondary cutting of the chips from damaging the machined surface.
Potential Problems in the CNC Aluminum Machining Process
Deformation Problem
Aluminum alloys themselves have low hardness and large thermal deformation. During the machining process, the cutting heat will cause the local temperature of the material to rise, resulting in thermal expansion. For example, during high – speed milling, the temperature in the cutting area can reach several hundred degrees. After the material expands and then cools and shrinks, it is prone to deformation. At the same time, if the clamping force of the fixture is unevenly distributed and the local stress is too large, the workpiece will also undergo plastic deformation. For example, when machining thin – walled aluminum parts, if the clamping force is not properly controlled, the parts are likely to deform, affecting the dimensional accuracy.
Fast Tool Wear
Although aluminum alloys have low hardness, they are relatively viscous. During the cutting process, chips are prone to adhere to the cutting edge and the rake face of the tool, forming a built – up edge. The built – up edge will change the cutting angle of the tool, increase the cutting force, and accelerate tool wear. Moreover, as the machining progresses, the built – up edge continuously falls off and regenerates, repeatedly impacting the tool, resulting in wear, chipping, etc. on the tool surface. Especially during long – term continuous machining, the tool wear problem will be more obvious.
Poor Surface Quality
If the cutting parameters are not selected reasonably, for example, if the cutting speed is too fast, the cutting force and cutting heat will increase sharply, causing defects such as burns and cracks on the workpiece surface; if the feed rate is too large, obvious tool marks will be left on the machined surface, increasing the surface roughness. In addition, after the tool is worn, the cutting edge is no longer sharp, and the cutting process is unstable, which will also cause problems such as ripples and vibration marks on the machined surface. When machining aluminum parts with high surface quality requirements, such as the casings of electronic devices, these problems will seriously affect the appearance and performance of the product.
Dimensional Accuracy Deviation
During the machining process, factors such as the accuracy error of the machine tool, the control error of the numerical control system, as well as tool wear and thermal deformation, will affect the dimensional accuracy of the part. For example, if there is a pitch error in the lead screw of the machine tool, the actual movement distance of the tool will not match the programming instruction; after the tool is worn, the tool diameter becomes smaller, and the machined hole diameter, groove width, etc. will be smaller than the design requirements. Moreover, the vibration during the machining process will also cause the tool to deviate from the predetermined machining path,resulting in dimensional accuracy deviation.
Chip Winding
The chips generated during the machining of aluminum alloys are usually in the form of strips or debris. Their high viscosity makes them prone to winding around the tool and the workpiece. Chip winding not only hinders the normal cutting of the tool and increases the cutting force but may also scratch the machined surface, affecting the surface quality. At the same time, the wound chips will also affect the operator’s observation and measurement, posing certain safety hazards. Chip winding problems are more common in machining processes such as drilling and milling.