In the realm of orthopedic and dental medicine, the demand for high-performance titanium alloy parts is driven by the need for biocompatible, durable, and precision-engineered solutions. From total joint replacements to dental implants, CNC (Computer Numerical Control) machining has emerged as the gold standard for manufacturing these critical components. This article explores the technical capabilities, material expertise, manufacturing excellence, and regulatory compliance that make CNC-machined titanium parts the preferred choice for orthopedic and dental applications.
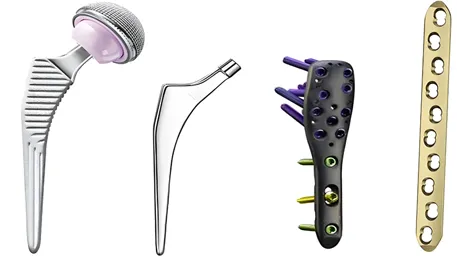
CNC machining systems designed for orthopedic and dental applications achieve unparalleled precision:
- Dimensional Tolerance: ±0.005mm for critical features (e.g., implant threads, articulating surfaces)
- Surface Roughness: Ra ≤ 0.2μm on osseointegration surfaces to promote bone cell adhesion
- Repeatability: ±0.01mm across all axes, ensuring batch-to-batch consistency in complex geometries
For example, a dental implant’s microthread pitch (0.7mm) is held to ±0.003mm, minimizing microgap formation and reducing the risk of bacterial ingress. In orthopedics, the femoral stem’s neck-shaft angle is machined to ±0.5°, matching the patient’s anatomical data for optimal load distribution.
Five-axis CNC technology enables the production of anatomically contoured parts:
- Porous Structures: Lattice-based spinal cages (60–80% porosity) created via trochoidal milling, enhancing bone ingrowth while maintaining structural integrity (ultimate compressive strength ≥150 MPa)
- Thin-Wall Components: 0.5mm-thick dental abutments machined with vibration-damping fixtures to prevent deformation during finish milling
- Multi-Feature Integration: Single-setup machining of hip prostheses with integrated anti-torsion features and hydroxyapatite coating surfaces
Titanium alloys like Ti-6Al-4V ELI demand specialized techniques:
- Cryogenic Cooling: Liquid nitrogen (–196°C) applied at the cutting edge reduces tool wear by 40% and minimizes thermal distortion in long-span orthopedic implants
- High-Precision Tooling: Micro-end mills (0.3mm diameter) with diamond coatings for machining intricate dental implant threads, achieving Ra ≤ 0.15μm without post-processing
- In-Process Metrology: Laser scanning verifies complex curved surface profiles in real time, ensuring compliance with patient-specific CAD models (deviation <0.01mm)
Alloy |
Grade |
Key Properties |
Applications |
Standards |
Ti-6Al-4V ELI |
ASTM F136 |
Low interstitial content, high fatigue strength (850 MPa) |
Hip/knee implants, spinal rods |
ISO 5832-3, FDA 21 CFR Part 820 |
Ti-6Al-7Nb |
ASTM F1295 |
Non-magnetic, excellent corrosion resistance |
Craniofacial implants, zygomatic dental implants |
EU MDR 2017/745, USP <88> |
Pure Titanium (Grade 23) |
ASTM F67 |
High ductility, ideal for soft tissue interaction |
Surgical staples, orthodontic brackets |
ISO 5832-2, AAMI ST72 |
All raw materials undergo:
- Spectroscopic Analysis: Verification of alloy composition (e.g., Al: 5.5–6.5%, V: 3.5–4.5% for Ti-6Al-4V ELI)
- Microstructural Examination: Ensure α-phase distribution (85–90%) for optimal biocompatibility and mechanical performance
- Data Integration: Direct import of DICOM scans and STL files from 3D medical imaging, enabling custom implants that match individual anatomy
- FEA Validation: Simulate cyclic loading (10 million cycles) for spinal pedicle screws to ensure fatigue strength >500 MPa, exceeding ISO 7206 requirements
- Rapid Prototyping: 3D-printed titanium models for pre-surgical fit testing, reducing OR time by 25% through optimized implant design
- Roughing: High-speed machining (15,000 RPM) with carbide tools to remove bulk material, leaving 0.3mm stock for finishing
- Finishing: Five-axis contouring with PCD tools to achieve ±0.005mm accuracy on articulating surfaces (e.g., knee femoral trochlea)
- Surface Treatment:
- Electropolishing: Reduces surface roughness to Ra ≤ 0.1μm, minimizing bacterial adhesion on dental implant surfaces
- Anodizing: Creates bioactive oxide layers (5–10μm) to enhance osseointegration in orthopedic implants
- Cleanroom Machining: Operations in ISO Class 8 cleanrooms to prevent particulate contamination (≤3,520,000 particles/m³ ≥0.5μm)
- Passivation: Citric acid treatment (ASTM A967) to remove machining oils and enhance corrosion resistance
- Sterile Packaging: Tyvek®-sealed trays validated for ethylene oxide (EO) sterilization, with biological indicator testing (Bowie-Dick test compliance)
- Raw Material Certification: Complete traceability from ingot to part, including mill test reports (MTR) and biocompatibility certificates
- In-Process Controls:
- SPC Monitoring: 100% inspection of critical dimensions for implantable parts (e.g., thread pitch, wall thickness)
- Automated Vision Systems: Real-time verification of dental implant thread angles (flank angle ±1°)
- Final Testing:
- Biocompatibility: Cytotoxicity (ISO 10993-5), genotoxicity (ISO 10993-3), and pyrogen tests (USP <151>)
- Mechanical Testing: Tensile strength (ASTM E8), hardness (Rockwell C 30–35 for Ti-6Al-4V ELI), and fatigue crack propagation tests
- Fit Verification: 3D comparison with patient-specific models using CMM scanning (volumetric accuracy ±0.007mm)
- Quality Management: ISO 13485-certified processes with 10-year batch traceability
- Submission Support: Technical dossiers for FDA 510(k), EU MDR, and PMDA applications, including machining validation reports and sterilization records
-
Dental Implants:
- Zygomatic implants (30–50mm length) with tapered threads (lead angle ±0.5°), machined from Ti-6Al-7Nb to withstand 450 N/cm² bite forces
- Implant abutments milled to ±0.01mm marginal fit, preventing microgap corrosion and improving prosthetic longevity
-
Orthodontics:
- Titanium alloy brackets (Grade 23) with CNC-machined slot dimensions (0.018” ±0.0005”), enabling precise wire engagement for faster tooth movement
- Robotic Surgery Tools: Lightweight titanium alloy forceps (Ti-6Al-4V ELI), 30% lighter than steel, with ergonomic handles machined to match surgeon grip data (surface roughness Ra ≤0.3μm)
Critical dimensions are held to ±0.005mm, with anatomical surfaces matching patient CT data within 0.01mm, ensuring optimal osseointegration and load transfer.
All processes use medical-grade coolants (e.g., HFE-7100) and undergo passivation to remove contaminants, with final parts tested for cytotoxicity (ISO 10993-5: no cell death at 100% extract concentration).
Yes—interconnected pores (100–500μm) are created via five-axis CNC with optimized toolpaths, validated via micro-CT scanning for 90% pore interconnectivity.
- Prototypes: 5–7 days (including 3D printing and fit testing)
- Sterilized production batches: 10–15 days (including biocompatibility testing and regulatory documentation)
- Expedited service: 48-hour turnaround for emergency cases (e.g., trauma implants)
Yes—we directly process DICOM, STL, and OBJ files, using software like Materialise Mimics for anatomical feature extraction and toolpath generation.
“Redefining implant precision for complex cases.”
— Zimmer Biomet
“Their CNC-machined Ti-6Al-7Nb craniofacial implants matched our patient’s CT scans within 0.01mm, enabling seamless intraoperative fit and reducing surgery time by 40%.”
“Innovation in dental implant technology.”
— Straumann Group
“The microthreads on their CNC-machined Ti-6Al-4V ELI dental implants achieved a 98% torque retention rate, exceeding industry standards and improving primary stability.”
From orthopedic implants that restore mobility to dental solutions that enhance quality of life, our CNC-machined titanium parts combine anatomical precision, biocompatibility, and regulatory compliance. Whether you need standard components or patient-specific devices, we deliver solutions that meet the highest healthcare standards. Contact us today to discuss your project—let’s transform medical innovation into tangible patient outcomes.
CNC Orthopedic & Dental Titanium Parts: Where Precision Meets Personalized Care.