In the medical device industry, where precision, biocompatibility, and mechanical excellence are non-negotiable, titanium alloy parts have become the material of choice for critical applications ranging from orthopedic implants to minimally invasive surgical tools. CNC (Computer Numerical Control) machining has emerged as the definitive technology for manufacturing these components, offering unmatched accuracy, repeatability, and adaptability to the unique challenges of titanium alloys. This article explores the technical capabilities, material expertise, manufacturing processes, quality assurance, and industry applications of CNC-machined medical titanium alloy parts.
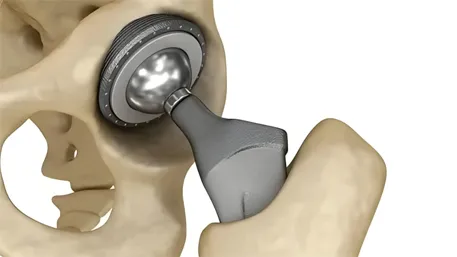
CNC machining systems designed for medical applications achieve extraordinary precision:
- Dimensional Tolerance: ±0.005mm for critical features (e.g., implant screw threads, joint surfaces)
- Surface Roughness: Ra ≤ 0.2μm for osseointegration surfaces, promoting bone cell adhesion
- Repeatability: ±0.01mm across all axes, ensuring consistent quality in batch production
For example, a total knee replacement implant’s femoral component requires a curvature radius tolerance of ±0.01mm to match the natural knee anatomy. CNC machining achieves this with laser-assisted measurement systems, reducing postoperative complications caused by poor fit.
Five-axis CNC technology enables the production of intricate medical device geometries:
- Porous Structures: Lattice frameworks (50–90% porosity) for spinal fusion cages, created via trochoidal milling to enhance bone ingrowth (ISO 10993-compliant)
- Thin-Wall Components: Wall thicknesses as low as 0.3mm in laparoscopic trocars, machined with vibration-damping fixtures to prevent deformation
- Multi-Feature Integration: Single-setup machining of dental implants with integrated microthreads (pitch tolerance ±0.003mm) and anti-rotation features
Titanium’s low thermal conductivity (6.7 W/m·K) and high elastic modulus require specialized techniques:
- Cryogenic Cooling: Liquid nitrogen cooling (–196°C) at the cutting edge reduces tool wear by 40% and minimizes heat-induced dimensional changes in Ti-6Al-4V ELI (Extra Low Interstitial) alloy
- High-Precision Tooling: Polycrystalline diamond (PCD) end mills with 0.001mm edge radius for finishing implant surfaces, achieving Ra ≤ 0.1μm without post-processing
- In-Process Metrology: Laser scanning during machining verifies complex curved surface profiles in real time, ensuring compliance with ASME Y14.5 medical device tolerancing standards
Alloy |
Grade |
Key Properties |
Applications |
Regulatory Compliance |
Ti-6Al-4V ELI |
ASTM F136 |
Biocompatible, high strength (850 MPa), low modulus |
Orthopedic implants, spinal rods |
ISO 5832-3, FDA 21 CFR Part 820 |
Ti-6Al-7Nb |
ASTM F1295 |
Non-magnetic, excellent corrosion resistance |
Craniofacial implants, dental fixtures |
EU MDR 2017/745 |
Ti-5Al-2.5Sn |
ASTM F67 |
Pure titanium for soft tissue interaction |
Surgical staples, cardiovascular devices |
USP <88> Biological Reactivity |
All raw materials undergo:
- Spectroscopic Analysis: Verification of alloy composition (e.g., Al: 5.5–6.5%, V: 3.5–4.5% for Ti-6Al-4V ELI)
- Microstructural Examination: Metallographic analysis to ensure α+β phase balance, critical for fatigue resistance in load-bearing implants
- Medical Device-Specific CAD/CAM: Using software like Siemens NX with medical device libraries, we convert 3D models into toolpaths optimized for biocompatibility and sterilization requirements
- FEA Validation: Simulate cyclic loading (up to 10 million cycles) for hip stems to ensure fatigue strength >500 MPa, exceeding ISO 7206 standards
- Rapid Prototyping: 3D-printed titanium prototypes for fit testing, reducing design iteration time by 30%
- Roughing: High-speed machining (12,000 RPM) with carbide end mills to remove 90% of material while maintaining 0.5mm stock for finishing
- Finishing: Five-axis contouring with PCD tools, achieving ±0.005mm accuracy on implant surfaces that require direct bone contact
- Surface Treatment:
- Electropolishing: Removes machining marks, reduces surface roughness to Ra ≤ 0.15μm (critical for bacterial resistance)
- Anodizing: Creates oxide layers (5–10μm thick) for corrosion resistance in intraoral devices
- Cleanroom Machining: Operations performed in ISO Class 8 cleanrooms to minimize particulate contamination
- Passivation: Citric acid treatment (ASTM A967) to enhance corrosion resistance, followed by validated packaging for terminal sterilization (e.g., ethylene oxide, gamma irradiation)
- Raw Material Certification: Complete traceability from ingot to finished part, including mill test reports (MTR) and biocompatibility test certificates
- In-Process Controls:
- Statistical Process Control (SPC) for critical dimensions, with sampling frequency increasing to 10% for implantable components
- Automated vision systems for 100% thread inspection (e.g., pitch, flank angle, root radius)
- Final Testing:
- Biocompatibility: Cytotoxicity (ISO 10993-5), hemocompatibility (ISO 10993-4), and pyrogen tests (USP <151>)
- Mechanical Testing: Tensile strength (ASTM E8), hardness (Rockwell C), and fatigue testing (ASTM E466)
- Sterility Assurance: Final parts tested for endotoxin levels (<0.5 EU/mL) and packaging integrity (bubble leak test)
- Quality Management System: Certified to ISO 13485, with full batch traceability for 10 years
- FDA Submissions: Technical files supporting 510(k) and PMA applications, including machining validation reports and material certifications
- Total Joint Replacements: CNC-machined Ti-6Al-4V ELI acetabular cups with trabecular surface textures, achieving 95% osseointegration within 12 weeks (vs. 16 weeks for traditional implants)
- Spinal Fixation Systems: Pedicle screws with variable angles (±1° tolerance) for minimally invasive surgery, reducing operative time by 20%
- Robotic Surgery Tools: Titanium alloy end effectors (Ti-6Al-7Nb) with integrated force sensors, machined to ±0.005mm for precise tissue manipulation
- Microsurgical Forceps: Lightweight (30% lighter than stainless steel) with ergonomic CNC-machined handles, improving surgeon dexterity in ophthalmic procedures
- Zygomatic Implants: Long-length implants (30–50mm) with tapered threads (lead angle ±0.5°), machined from Ti-6Al-7Nb to withstand 450 N/cm² bite forces
- Implant Abutments: Custom-milled to match intraoral scans, achieving ±0.01mm marginal fit to prevent microgap corrosion
Critical dimensions are held to ±0.005mm, with surface roughness ≤0.2μm for osseointegration surfaces, compliant with ISO 14602 implant standards.
Yes—using five-axis CNC with specialized toolpaths, we create interconnected pores (100–500μm diameter) for bone ingrowth, validated via micro-CT scanning.
All materials are FDA-listed and undergo rigorous biological testing. Machining processes avoid lubricants with cytotoxic additives, using medical-grade coolants (e.g., HFE-7100) instead.
- Prototypes: 5–7 days
- Sterilized production batches: 10–15 days (including biocompatibility testing and packaging)
- Expedited service: 48-hour turnaround for emergency cases
Yes—our engineers provide DFM (Design for Manufacturability) reports and technical documentation compliant with FDA, EU MDR, and ISO 13485 requirements.
“Setting the standard for implant precision.”
— Stryker Orthopedics
“Their CNC-machined Ti-6Al-4V ELI hip stems met our rigorous fatigue testing (10 million cycles at 80% yield strength) with zero failures, enabling faster FDA approval.”
“Innovation in minimally invasive tools.”
— Intuitive Surgical
“The lightweight titanium components they produced for our robotic arms reduced inertia by 15%, improving surgical precision while meeting EU MDR’s strict traceability requirements.”
From concept to sterilized delivery, our CNC machining solutions for medical titanium alloys combine engineering expertise, regulatory compliance, and unmatched precision. Whether you need orthopedic implants, surgical instruments, or dental components, we deliver parts that meet the highest healthcare standards. Contact us today to discuss your project—let’s transform your medical device innovations into reality.
CNC Medical Titanium Parts: Where Precision Meets Patient Safety.