In industrial manufacturing and consumer sectors, ABS plastic stands out as a premier material for customized parts due to its excellent comprehensive properties and processing flexibility. This article systematically explores the core advantages of custom ABS plastic parts, covering material characteristics, processing technologies, application scenarios, and quality control, to provide efficient and precise customized solutions for enterprises.
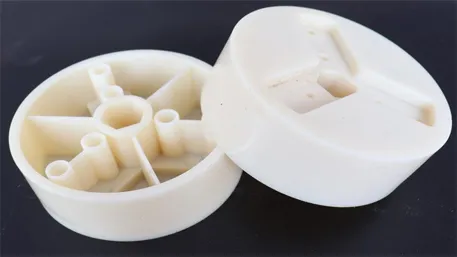
Property |
Typical Parameters |
Core Advantages |
Application Value |
Tensile Strength |
40-55 MPa |
Stable structure, resistant to daily mechanical loads |
Load-bearing components like electronic housings and mechanical structures |
Impact Strength |
15-25 kJ/m² |
High collision resistance, reducing accidental damage |
High-impact scenarios such as children’s toys and sports equipment |
Heat Deflection Temperature |
90-110℃ |
Suitable for normal temperature ranges, preventing high-temperature softening |
Home appliance components and industrial parts in non-extreme environments |
Melt Flow Rate |
2-8 g/10min |
Excellent fluidity for complex structure molding |
Precision gears, multi-snap connectors, and detailed designs |
- Electroplating: Chemical roughening ensures coating adhesion ≥5N/cm², achieving metallic finishes (e.g., chrome, nickel plating) to enhance product elegance.
- Color Spraying: Compatible with acrylic and polyurethane paints, achieving color reduction ≥95% for personalized aesthetics in consumer electronics and toys.
- In-Mold Decoration (IMD): One-step pattern/texture forming, with 500-cycle wear resistance testing showing no peeling, ideal for complex designs in high-end products.
- High Cost Performance: Material cost is 1/3 of PC and 1/20 of PEEK, making it ideal for mass production.
- Recycling-Friendly: Recycled ABS retains ≥80% of original properties, compliant with EU RoHS/REACH directives for green manufacturing.
- Mold Flow Analysis (Moldflow): Simulates melt flow to predict defects like short shots and sink marks, controlling warpage within 0.1mm/m and stabilizing critical dimension tolerance at ±0.05mm.
- Mold Precision Control: Uses S136 tool steel (HRC52 hardness) with 5-axis CNC machining, achieving cavity surface roughness Ra≤0.4μm for precise forming of 0.1mm thin walls and 0.3mm fine pillars.
- Intelligent Production Parameters: Injection temperature 220±5℃, holding pressure 60MPa, with a daily capacity of 10,000 pieces (4-cavity mold), 30% more efficient than traditional processes.
- Two-Shot Injection Molding: Forms hard-soft composite structures (e.g., ABS body + TPE anti-slip layer), increasing grip force by 20% for tool handles and electronic housings.
- Insert Molding: Precisely embeds metal embedded part (e.g., screw posts, conductive sheets) with position tolerance ≤0.02mm, meeting high-precision assembly requirements for electronic connectors.
- Technical Alignment: Clarifies part usage (structural/aesthetic), environmental conditions (temperature/corrosion), and precision levels (IT8 tolerance or free tolerance).
- Solution Design: Provides material certifications (e.g., FDA compliance for food-grade ABS), process routes (injection molding/CNC/3D printing), and cost proposals within 3 days.
- 3D Modeling: Uses UG/NX for structural optimization, increasing rib density by 30% to enhance anti-deformation while controlling wall thickness uniformity ≤±0.1mm.
- Rapid Prototyping:
- 3D Printing (SLA): Delivers prototypes in 3 days for assembly verification.
- Silicone Mold Small Batch (50-piece minimum): Replicates final material properties for functional testing.
- Process Control: Full-size first-piece inspection (CMM accuracy ±0.01mm) for each shift, real-time monitoring of injection pressure/temperature (deviation ≤2%), ensuring CPK≥1.33.
- Inspection System:
| Inspection Item | Standard Requirements | Equipment/Method | Pass Criteria |
| Dimensional Accuracy| Critical dimensions ±0.02mm| Coordinate Measuring Machine| 100% pass rate |
| Surface Defects | ≤1 bubble >0.2mm per piece | Visual inspection + AI recognition | Defect rate <0.1% |
| Coating Adhesion | No peeling in cross-cut test| ISO 2409 grid test | Grade 0 (excellent)|
- Device Housings: ABS electroplated housings with 3H hardness resist 48-hour salt spray testing, suitable for consumer electronics like phones and routers, balancing aesthetics and protection.
- Precision Components: 0.5mm ultra-thin connectors use IMD technology with surface resistance ≤10^8Ω, meeting signal shielding requirements for 5G equipment.
- Interior Parts: Dashboard brackets certified to VDA 6.5, resisting deformation after 500 hours of 85℃ aging, with embossed textures for improved touch comfort.
- Exterior Accessories: Rearview mirror housings pass 3000-hour UV weathering testing (ΔE≤2), with 20% better color stability than competitors.
- Toy Manufacturing: ABS toy parts compliant with GB 6675, featuring rounded corners ≥2mm and ≤5% breakage rate in 1.5m drop tests.
- Medical Equipment: Antibacterial ABS trays (bacterial inhibition rate ≥99%) with smooth surfaces for easy cleaning, conforming to ISO 13485 medical quality management systems.
- High-Performance Enhancement: Glass fiber-reinforced ABS (GF-ABS) increases tensile strength to 70MPa, suitable for automotive load-bearing parts.
- Functional Customization: Antistatic ABS (surface resistance ≤10^6Ω) becomes the preferred material for electronic component packaging.
- Digital Twin Design: AI-driven mold flow analysis reduces trial molds by 50%, shortening mold development cycles to 20 days.
- Intelligent Factory: MES systems track production data in real time, with anomaly response <10 minutes and capacity utilization increased by 25%.
Q1: Can small batches support complex structures?
A: Yes. 3D-printed molds (100-piece minimum) or silicone molds (500-piece minimum) enable complex structures like snaps and side holes with dimensional accuracy ±0.1mm.
Q2: How to ensure coating adhesion for electroplated parts?
A: A three-step pretreatment process (roughening-sensitizing-activating) ensures grid test grade 0 adhesion, resistant to 50 cycles of thermal shock (-20℃~60℃).
Q3: What certifications are needed for food-contact ABS?
A: Requires FDA 21 CFR 177.1040 and EU 10/2011 compliance, with heavy metal migration ≤0.1ppm and potassium permanganate consumption ≤10mg/L.
“Collaborating with the team for 50,000 ABS decorative strips for home appliances, the project was delivered in just 35 days. Parts met ±0.03mm dimensional accuracy, 72-hour salt spray resistance, and color difference ΔE<1—exceeding expectations. Proactive mold runner optimization increased yield from 92% to 97%. We’ll continue partnering for future projects!” ——A Leading White Goods Manufacturer
Whether for the delicate aesthetics of consumer electronics or the high-strength requirements of automotive parts, we leverage material expertise and advanced processes to deliver end-to-end solutions. Contact us for a tailored proposal and transform every part into a symbol of quality and efficiency!