Goldcattle, with 26 years in high-precision manufacturing, specializes in custom aerospace and defense parts—covering aircraft structural components, missile guidance system parts, satellite brackets, and engine turbine components (titanium/Inconel/ aluminum materials). Using 5-axis CNC machining and precision casting, we deliver ±0.0005mm tolerance parts, backed by AS9100D and Nadcap certifications. From prototypes to 10,000+ units/year, our parts ensure extreme temperature resistance, high tensile strength, and compliance with ITAR regulations for 40+ global defense contractors and aerospace OEMs.
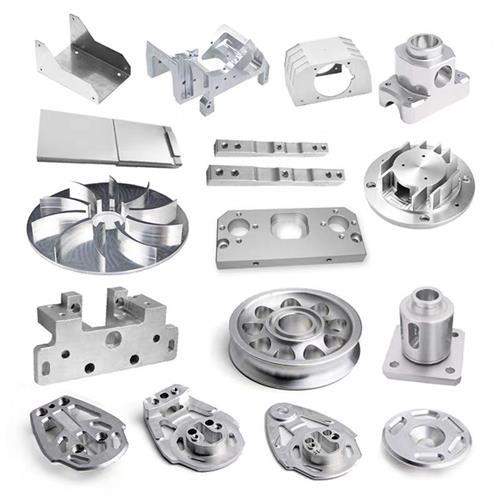
Core Processing Technologies: Engineering for Extreme Environments
Aerospace and defense parts operate in extreme conditions—temperatures from -270℃ (space) to 1,200℃ (engine cores), high G-forces, and corrosive aerospace fluids. Goldcattle’s technologies ensure parts maintain integrity in these harsh environments.
1. Ultra-Precision 5-Axis Machining
- 5-axis simultaneous milling: Machines complex geometries like turbine blades with 3D cooling channels (0.5mm diameter) and missile fin contours, achieving ±0.0005mm dimensional tolerance. A titanium aircraft frame bracket with 7 inclined holes maintained 0.001mm positional accuracy, critical for structural integrity under 9G loads.
- High-speed CNC turning: Produces engine shafts and missile guidance components with ≤0.001mm concentricity, ensuring balanced rotation at 20,000 RPM. A 30mm Inconel engine shaft achieved Ra 0.02μm surface finish, reducing friction-induced heat by 20%.
- Wire EDM cutting: Creates precision slots (0.1mm width) in hardened steel (55HRC) for missile control systems, with ±0.001mm tolerance and burr-free edges (≤0.005mm), preventing electrical interference.
2. Advanced Material Processing
- Heat-resistant alloy machining: Specializes in titanium (Ti-6Al-4V) and Inconel 718 parts, with toolpaths optimized to reduce work-hardening. A turbine blade root machined from Inconel 718 withstood 1,000℃ continuous operation without deformation.
- Ceramic matrix composite (CMC) machining: Uses diamond tools to shape CMC components (e.g., rocket nozzle liners) with 0.01mm thickness tolerance, enabling resistance to 2,800℃ re-entry temperatures.
- Lightweight aluminum alloy processing: Machines 7075-T7351 aluminum aircraft skins with 0.05mm flatness over 1m², reducing airframe weight by 8% while maintaining structural rigidity.
3. Extreme Environment Testing & Validation
- Nondestructive testing (NDT): Uses X-ray inspection (0.01mm defect detection), ultrasonic testing, and liquid penetrant inspection to identify subsurface flaws in critical parts (e.g., aircraft landing gear components). A titanium alloy bracket for fighter jets passed 100% X-ray testing, ensuring no internal porosity.
- Thermal cycling testing: Exposes parts to -270℃ (liquid nitrogen) to 1,200℃ (flame heating) for 5,000+ cycles, verifying dimensional stability (≤0.002mm change) for space satellite components.
- Vibration & shock testing: Subjects parts to 20-2,000Hz vibrations (100G peak) and 500G impact testing, simulating missile launch and aircraft turbulence—critical for guidance system reliability.
4. Precision Surface Treatment
- Aerospace-grade anodizing: Applies Type II/III anodizing to aluminum parts (e.g., satellite panels) with 5-50μm thickness control, enhancing corrosion resistance (1,500+ hours salt spray) and wear resistance.
- Plasma spray coating: Deposits ceramic coatings (ZrO₂) on turbine blades, enabling operation at 1,200℃ (300℃ higher than uncoated Inconel).
- Dry film lubrication: Applies MoS₂-based coatings to moving parts (e.g., missile hinge mechanisms) to reduce friction (coefficient ≤0.05) in vacuum or high-temperature environments.
Material Expertise: Matching Alloys to Mission-Critical Needs
Aerospace and defense parts demand materials with exceptional strength-to-weight ratios and environmental resistance—Goldcattle specializes in high-performance alloys:
Material | Key Properties | Application | Advantages |
---|---|---|---|
Titanium Alloy (Ti-6Al-4V, Ti-6Al-2Sn-4Zr-2Mo) | 895MPa tensile strength, -270℃ to 400℃ temperature range | Aircraft frames, missile bodies | 45% lighter than steel; excellent corrosion resistance in saltwater/rocket fuel. |
Nickel-Based Superalloys (Inconel 718, Hastelloy X) | 1,300MPa tensile strength, 1,200℃ peak temperature resistance | Turbine blades, rocket nozzles | Maintains strength under extreme heat; resistant to jet fuel and oxidizing environments. |
Aluminum-Lithium Alloy (2195, 2050) | 450MPa tensile strength, 10% lighter than 7075 | Satellite structures, aircraft skins | Reduces fuel consumption; high fatigue resistance (10,000+ flight cycles). |
Ceramic Matrix Composites (CMC) | 2,800℃ temperature resistance, low thermal expansion | Hypersonic vehicle components, re-entry shields | Withstands 5x higher temperatures than metal alloys; 30% lighter than Inconel. |
Aerospace & Defense Parts Manufacturing Process
- Design & DFM with MIL-STD Compliance: Engineers analyze client 3D models (STEP/IGES) against MIL-STD-882E, optimizing for:
- Redundant features (e.g., dual fastening points on aircraft brackets)
- Material removal to reduce weight (hollowed missile fins with 0.5mm walls)
- Toolpath validation to avoid stress concentrations
- Material procurement: Sources certified materials with full traceability (heat lot documentation, metallurgical reports) per AMS specifications (e.g., AMS 4928 for Ti-6Al-4V).
- Precision machining:
- Roughing: Removes 80% of material with carbide tools (100m/min feed rate for aluminum).
- Finishing: 5-axis machining with diamond tools (Ra 0.01μm surface finish) for critical features like turbine blade airfoils.
- Heat treatment: Solution annealing (titanium: 927℃) and aging (Inconel: 720℃) to achieve target hardness (35-40 HRC for structural parts).
- Surface engineering: Applies coatings per SAE AMS 2488 (anodizing) or AMS 2470 (plasma spray), with 100% adhesion testing.
- Quality validation:
- CMM inspection (±0.0005mm) with 10,000+ data points
- NDT (X-ray, ultrasonic, magnetic particle) per AMS 2632
- Environmental testing (vibration, thermal vacuum, salt fog)
Custom Aerospace & Defense Parts Application Fields
- Manned Aircraft: 718 Inconel engine mounts (withstand 900℃), 2195 Al-Li wing ribs (10% weight reduction), titanium landing gear components (100,000+ landing cycles).
- Unmanned Aerial Vehicles (UAVs): 6061-T6 surveillance camera brackets (vibration-resistant at 300km/h), CMC exhaust nozzles (stealth heat signature reduction).
- Missile & Rocket Systems: Ti-6Al-4V guidance system housings (EMP-resistant), Hastelloy X combustion chambers (1,000bar pressure tolerance).
- Space & Satellite: 2050 Al-Li satellite bus structures (low Earth orbit radiation resistance), CMC re-entry shields (withstand 15,000℃ plasma).
Customization Capabilities: From Prototypes to Low-Rate Production
Mission-critical parts require flexibility and strict compliance—Goldcattle supports defense and aerospace clients with:
- Rapid prototyping: 1-5 units in 2-3 weeks via 5-axis machining (e.g., UAV wing prototypes for wind tunnel testing).
- Low-rate initial production (LRIP): 10-100 units/year with full ITAR compliance (e.g., missile guidance components with encrypted part numbering).
- Legacy part replication: Reverse engineering of obsolete parts (e.g., 1960s fighter jet hydraulic manifolds) via 3D scanning (0.001mm accuracy) and CNC machining.
Common Processing Questions
-
Q: How to achieve 0.0005mm tolerance on a 300mm titanium aircraft bracket?
A: Use temperature-controlled machining cells (±0.1℃), 5-axis milling with real-time laser calibration, and in-process CMM checks every 5 minutes to compensate for thermal expansion (titanium expands 8.6μm/m per ℃). -
Q: What ensures parts meet ITAR and export control requirements?
A: Dedicated ITAR-compliant production lines, encrypted traceability software, and staff with DD2345 certification. All parts include tamper-evident serial numbers linked to material heat lots. -
Q: How to verify a turbine blade’s performance at 1,200℃?
A: Conduct cyclic thermal testing (1,200℃ for 10 minutes, 25℃ for 5 minutes) × 1,000 cycles, then inspect for:- Oxidation (≤5μm layer growth)
- Creep deformation (≤0.01mm length change)
- Microstructural degradation (no grain boundary cracks via SEM)
-
Q: What’s the lead time for 20 custom CMC rocket nozzle liners?
A: 4 weeks for material procurement, 6 weeks for machining/coating—total 10 weeks. Rush options for emergency defense orders cut lead time by 40% with 24/7 production.
Need Mission-Critical Aerospace & Defense Parts?
Goldcattle delivers parts that meet the most demanding aerospace and defense standards, from hypersonic vehicle components to satellite structures. Our AS9100D-certified process ensures reliability in life-or-death applications.
Upload your 3D models or specifications via our secure online portal to receive a compliance-focused feasibility report and quote within 24 hours. Our engineers will validate designs against MIL-STD and AMS requirements, ensuring mission success.
Goldcattle—Trusted by 40+ defense contractors for precision that meets the rigor of aerospace and military operations.