In the development trend of the automotive industry towards high-efficiency power, energy conservation, and long lifespan, engine die castings, with their excellent resistance to high temperatures, high strength, and complex structure forming capabilities, have become a key technical solution for constructing core components of engines. Their performance directly determines the power output, energy consumption performance, and reliability of engines, playing an irreplaceable role in both traditional fuel engines and new energy power systems.
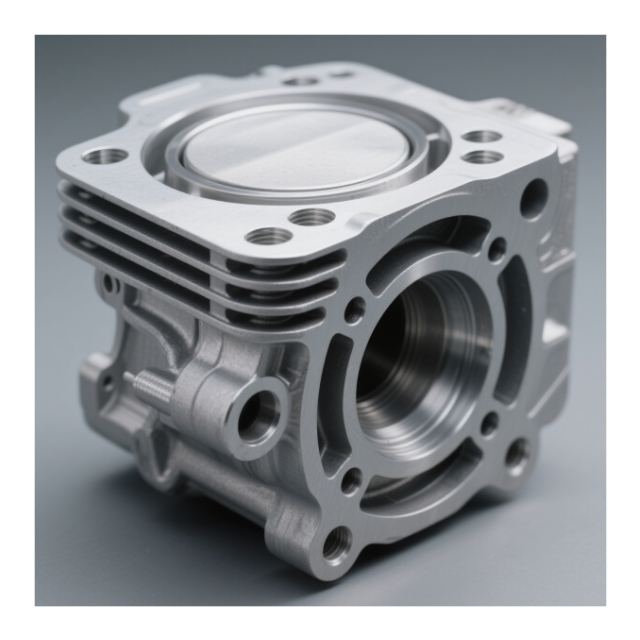
Table of Contents
- Automotive Engine Die Castings: The Core of the Power System
- Customized Material Selection: Material Solutions for Extreme Working Conditions
- Precision Manufacturing Process: The Transformation from Liquid Metal to Core Components
- Core Technological Breakthroughs: Conquering High Temperature, High Pressure, and High Load Challenges
- Full-process Quality Control: Adherence to Automotive-grade Stringent Standards
- Agile Service System: Meeting the High-efficiency Development Needs of the Automotive Industry
- Engine Die Casting FAQs: Professional Answers to Core Customization Questions
1. Automotive Engine Die Castings: The Core of the Power System
Engine die castings bear core functions such as energy conversion, heat dissipation, and lubrication, which are crucial for the stable operation of engines:
- Adaptability to Extreme Conditions: Capable of continuous operation in a high-temperature environment of 200°C – 350°C and withstanding an explosion pressure of 15 – 25MPa, key components require a tensile strength of ≥320MPa to ensure the stable operation of core components such as combustion chambers and cylinder blocks.
- Integration of Complex Structures: Through integrated die casting technology, high-precision forming of complex structures such as cooling water channels, fuel channels, and valve seats (hole diameter tolerance ±0.02mm) is achieved, reducing the welding process by 40% and improving overall sealing and reliability.
- Lightweight Requirements: Compared with traditional cast iron components, aluminum alloy die castings can achieve a weight reduction of 30% – 50%, effectively reducing engine self-weight, improving fuel efficiency by 6% – 10%, and reducing vehicle emissions.
2. Customized Material Selection: Material Solutions for Extreme Working Conditions
1. Performance and Typical Applications of Main Alloys
Alloy Type | Typical Grade | Core Performance Indicators | Engine Component Applications |
---|---|---|---|
Aluminum Alloy | A380 | Tensile strength ≥330MPa, strength retention at 300°C ≥75% | Cylinder blocks, cylinder heads, turbo casings |
Aluminum Alloy | A356-T6 | Elongation ≥8%, excellent airtightness (porosity ≤0.8%) | Oil pans, intake manifolds |
Magnesium Alloy | AZ91D | Density 1.8g/cm³, excellent damping performance (vibration attenuation rate ≥40%) | Engine mounts, timing covers |
2. Customized Material Design
- Reinforcement of High-temperature Components: Adding 0.6%Mg + 0.4%Ni to the A380 alloy increases the tensile strength by 20% at 350°C and extends the thermal fatigue life by 30%, meeting the strict requirements of turbocharged engines.
- Optimization of Sealing Components: The A356-T6 alloy undergoes precise degassing treatment to control the hydrogen content below 0.12ml/100g, ensuring the airtightness of sealing components such as oil pans, with a leakage rate ≤3cc/min.
3. Precision Manufacturing Process: The Transformation from Liquid Metal to Core Components
1. Mold Design: Micron-level Precision Control
- Optimized Design of Hot Runner: Using Moldflow for mold flow analysis, optimizing the gate position and size, reducing the filling time by 15%, and reducing the shrinkage porosity defect rate from 4% to 0.6%.
- Mold Processing Technology:
- Using slow wire electrical discharge machining for deep cavity molds, with an accuracy of ±0.003mm, ensuring the coaxiality of 12mm deep holes ≤0.015mm;
- The mold surface is treated with PVD titanium plating (film thickness 3 – 5μm), increasing the hardness to 2200HV, effectively reducing the sticking phenomenon and extending the mold life by 30%.
2. Die Casting: Exclusive Process for Engines
- Vacuum High-pressure Die Casting: Controlling the vacuum degree at ≤40mbar, with a four-stage pressure boost technology (initial pressure 80MPa → intermediate pressure 120MPa → high pressure 160MPa → final pressure 200MPa), achieving an internal density of cylinder blocks ≥99.8%, and an X-ray flaw detection defect rate <0.05%.
- Intelligent Temperature Control System: Real-time monitoring and precise control of the mold temperature (aluminum alloy mold 185±2°C), ensuring that key dimensions fluctuate ≤±0.018mm, meeting high-precision assembly requirements.
3. Post-processing: Double Improvement of Performance and Precision
- Precision Machining:
- Using a five-axis machining center to grind the cylinder block plane, with a flatness ≤0.015mm/100mm, ensuring cylinder sealing;
- After honing the oil passage holes, the surface roughness Ra≤0.3μm, reducing the oil flow resistance by 12% and improving lubrication efficiency.
- Surface Treatment Process:
- The cylinder head is treated with hard anodizing (film thickness 25μm), with a hardness ≥350HV, increasing the corrosion resistance of the coolant by 5 times;
- The turbo casing is treated with a nano-ceramic coating, increasing the high-temperature resistance to 600°C and reducing the heat conduction efficiency by 25%.
4. Core Technological Breakthroughs: Conquering High Temperature, High Pressure, and High Load Challenges
1. High-temperature Strength and Thermal Fatigue Technology
- Grain Refinement Treatment: Adding 0.3%Ti + 0.2%B to the aluminum alloy, refining the grain size to below 35μm, increasing the high-temperature fatigue strength by 35%, and being able to withstand 150,000 thermal cycles without cracks.
- Optimized Structure Design: Using topological optimization technology, lightweight design of the cylinder block, adding reinforcing ribs (thickness 1.8mm) in stress concentration areas, increasing the knock resistance by 40%.
2. Precision Cooling and Lubrication System Forming
- Micro-channel Die Casting Technology: Successfully achieving the die casting of cooling water channels with a width of 0.6mm, through the design of the mold spiral runner, increasing the filling success rate to 95% and improving the heat dissipation efficiency by 20%.
- Reinforcement of Oil Passage Sealing: Combining laser welding and vacuum helium leak detection technology to ensure the sealing of oil passages, with a leakage rate ≤1cc/min, 40% better than the industry standard.
3. Upgrade of Non-destructive Testing Technology
- CT Three-dimensional Detection: Using high-precision CT scanning technology to perform full-size three-dimensional reconstruction of the cylinder block, with a detection accuracy of 0.1mm, capable of detecting tiny internal defects, and a miss rate <0.03%.
- Ultrasonic Phased Array Detection: Performing ultrasonic phased array detection on key welds, increasing the detection sensitivity by 30%, ensuring 100% qualified welding quality.
5. Full-process Quality Control: Adherence to Automotive-grade Stringent Standards
1. Raw Material Control
- Spectral Analysis: Conducting full-element spectral detection on each batch of alloys (accuracy 0.005%), strictly controlling the Si content in A380 alloy at 12.0% – 13.2%, and Fe content ≤0.8%.
- Mechanical Property Testing: Conducting multiple mechanical property tests such as tensile, impact, and hardness on raw materials, with a batch qualification rate ≥99.9%.
2. Process Monitoring
- Intelligent Manufacturing System: Real-time collection of data such as pressure, temperature, and speed during the die casting process through IoT sensors, achieving precise control of production parameters, with an abnormal response time ≤8 seconds.
- First Article Three-inspection System: Conducting full-size inspection (measurement points ≥80), metallographic analysis, and non-destructive testing on the first article, ensuring 100% qualification before mass production.
3. Finished Product Inspection
Inspection Item | Inspection Method | Automotive-grade Standard | Compliance Rate |
---|---|---|---|
Dimensional Accuracy | Coordinate Measuring Machine | Key dimensions ±0.015mm | 99.9% |
Internal Defects | CT Scanning + Ultrasonic Testing | 0 tolerance for defects ≥0.2mm | 100% |
Airtightness Test | Helium Mass Spectrometer | Leakage rate ≤3cc/min | 99.8% |
High-temperature Performance | High-temperature Mechanical Testing | Tensile strength ≥280MPa at 300°C | 99.5% |
6. Agile Service System: Meeting the High-efficiency Development Needs of the Automotive Industry
1. Collaborative R&D
- Early Intervention in Design: Providing DFM (Design for Manufacturability Analysis) services during the customer’s product development stage, optimizing the product structure design, reducing the mold development cost by 30%, and shortening the development cycle by 20%.
- Joint Technical Research: Collaborating with customers on the research and development of new materials and processes, developing high thermal conductivity aluminum alloy materials for components such as new energy vehicle motor casings, increasing the thermal conductivity efficiency by 30%.
2. Rapid Delivery
- Rapid Prototyping Service: Combining 3D printing and simple molds, the first sample can be delivered within 7 days, shortening the prototyping cycle by 60% compared with traditional methods.
- Flexible Production Capacity: Equipped with large-scale die casting machines ranging from 800T to 2000T, with a monthly production capacity of 300,000 pieces, shortening the delivery cycle of complex engine components by 35% compared with the industry average.
3. After-sales Guarantee
- Full Lifecycle Service: Providing a full-process service from product design, manufacturing to after-sales maintenance, establishing a product quality traceability system to achieve rapid positioning and resolution of problems.
- Technical Support Team: The professional technical team responds to customer needs 24 hours a day, providing on-site technical guidance, assisting customers in solving problems such as assembly and performance optimization, with a customer satisfaction rate of 99%.
7. Engine Die Casting FAQs: Professional Answers to Core Customization Questions
Q1: What are the commonly used aluminum alloy grades for automotive engine die castings?
A: Commonly used grades include A380 (high strength, high temperature resistance), A356-T6 (high toughness, good airtightness), and A365 (high thermal conductivity). The most suitable material can be recommended according to specific usage requirements.
Q2: How to ensure the airtightness of engine cylinder blocks?
A: Vacuum high-pressure die casting technology is used to control internal air holes, combined with precision machining of the sealing surface (flatness ≤0.015mm/100mm), and 100% airtightness detection is carried out with a helium mass spectrometer to ensure that the leakage rate ≤3cc/min.
Q3: What is the mold life of custom engine die castings?
A: The standard mold life is 600,000 – 800,000 cycles. Using high-performance mold steel (such as H13) combined with surface treatment technology, the mold life can be increased to more than 1.2 million cycles, and mold maintenance services are provided.
Q3: How long does it take from drawing confirmation to mass production?
A: The standard cycle is: requirement confirmation 3 days → mold design 12 days → mold processing 35 days → trial casting 7 days → production preparation 5 days, totaling about 62 days; for urgent projects, it can be compressed to within 45 days through concurrent engineering.
Get an Exclusive Customized Solution Now
The engine, as the power heart of the vehicle, directly determines the core competitiveness of the vehicle. Whether you are a traditional car manufacturer or a new energy innovation enterprise, professionally customized engine die castings can provide you with a comprehensive solution from materials to processes. Leave your requirements now – please specify the engine type, performance requirements, and annual demand, and we will customize an exclusive technical solution and efficient delivery plan for you within 24 hours.
(Message area: Please specify the engine type, performance requirements, and annual demand in detail, and we will reply within 24 hours)