With 26 years of expertise in automotive wheel component manufacturing, Xiamen Goldcattle specializes in custom automotive wheel accessories—tailored for passenger cars, commercial vehicles, racing cars, and off-road vehicles. Our product range includes wheel center caps, wheel adapters/spacers, wheel bolts/lugs, wheel trim rings, wheel weight brackets, and custom wheel decals. Leveraging advanced CNC machining, forging, stamping, and injection molding technologies, we deliver parts that meet strict automotive standards for dimensional accuracy, load-bearing capacity, and corrosion resistance. Backed by ISO/TS 16949, IATF 16949, and SAE J2530 certifications, we support prototype development to mass production (500,000+ units/month) with ±0.01mm dimensional tolerance, serving 40+ global wheel manufacturers and automakers.
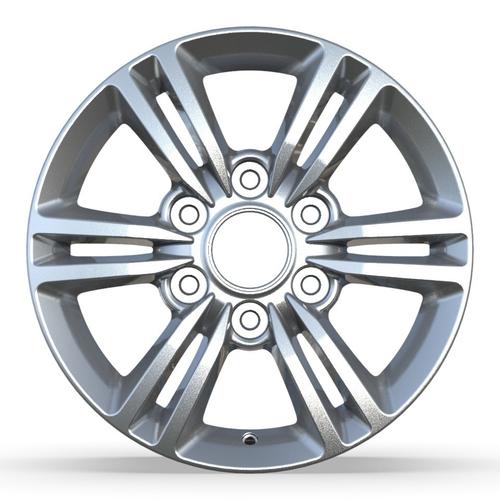
Core Processing Technologies: Engineering for Wheel Safety & Performance
Automotive wheel accessories operate under constant stress—supporting vehicle weight, withstanding road vibrations, and enduring harsh environmental conditions (salt, water, debris). Goldcattle integrates cutting-edge technologies to ensure parts meet the rigorous demands of safety, durability, and aesthetics.
1. CNC Precision Machining for Critical Fit
- 5-axis CNC milling: Used for wheel adapters, spacers, and center caps with complex geometries. With ±0.005mm positioning accuracy, it ensures wheel adapters (which adjust wheel offset) have precise hub bore diameters (tolerance ≤0.02mm) and bolt hole positions, preventing wheel wobble. A set of 20mm wheel spacers for a BMW M3 produced this way achieved 0.01mm runout, eliminating vibration at high speeds (160km/h+).
- CNC turning for wheel bolts/lugs: Equipped with Swiss-type CNC lathes, we produce high-strength wheel bolts (M12, M14) with thread accuracies up to 6g (ISO 965-1), ensuring secure torque retention (200-300N·m for steel bolts). The turning process creates precise shank diameters (±0.01mm) that fit wheel hub holes without play, critical for load distribution.
- Wire EDM cutting: For intricate wheel trim ring patterns and custom center cap logos, wire EDM (0.002mm cutting accuracy) achieves sharp edges and complex shapes—such as a carbon fiber center cap with a laser-etched logo, where the logo depth (0.3mm) was maintained across 10,000 units.
2. Forging & Stamping for High-Strength Components
- Cold forging for wheel bolts/lugs: This process reshapes metal (alloy steel, titanium) under high pressure (500-1000MPa), increasing tensile strength by 30% compared to machined parts. Cold-forged wheel bolts (10.9 grade) achieve tensile strength ≥1000MPa, meeting SAE J2530 standards for load-bearing safety. A racing team’s titanium wheel lugs, cold-forged to 8mm diameter, reduced unsprung weight by 40% vs. steel lugs.
- Hot forging for wheel adapters: For heavy-duty adapters (e.g., for trucks, off-road vehicles), hot forging (800-1200℃) of 4140 alloy steel creates uniform grain structure, enhancing impact resistance. A 30mm adapter for a Ford F-250 withstood 12,000N static load testing (equivalent to 3x vehicle weight) without deformation.
- Precision stamping: Used for wheel trim rings, dust covers, and weight brackets. With 100-300 ton stamping presses, we produce parts with consistent flatness (≤0.1mm/m) and edge quality, ensuring trim rings fit wheel rims with zero gaps (≤0.5mm).
3. Surface Treatment & Coating Technologies
- Electroplating: For wheel bolts, lugs, and trim rings, chrome plating (5-10μm thickness) provides a mirror finish and corrosion resistance (500+ hours salt spray test per ASTM B117). Black zinc-nickel plating (8-12μm) offers a sleek matte finish with 1000+ hours salt spray resistance—ideal for off-road vehicles exposed to harsh conditions.
- Powder coating: Applied to wheel center caps and adapters, this process (60-80μm thickness) creates durable, UV-resistant finishes in custom colors (RAL/Pantone matching). A matte black powder-coated center cap for a luxury SUV withstood 3,000 hours of UV testing without fading.
- Anodizing for aluminum parts: For lightweight aluminum center caps and spacers, anodizing (10-20μm) enhances surface hardness (up to 300HV) and creates a range of decorative finishes (clear, black, blue). An anodized aluminum spacer for a Porsche 911 maintained its finish after 50,000km of driving.
- Ceramic coating: For racing wheel accessories, a 2-5μm ceramic coating reduces friction (coefficient ≤0.1) on wheel bolts, making installation/removal easier, and resists heat (up to 600℃) from brake systems.
4. Quality Testing for Safety & Reliability
- Dimensional inspection: Uses Zeiss CMMs to verify critical dimensions—hub bore diameter (±0.01mm), bolt hole position (±0.02mm), and spacer thickness (±0.005mm)—ensuring compatibility with OEM and aftermarket wheels.
- Load-bearing testing: Wheel adapters and spacers undergo static load testing (up to 20,000N) and fatigue testing (1 million+ cycles) to meet SAE J2530 standards, ensuring they withstand vehicle weight and road stress.
- Torque testing: Wheel bolts are tested for torque-to-yield performance, ensuring they retain ≥90% of clamping force after 100+ installations/removals.
- Environmental testing: Parts undergo:
- Salt spray (500-1000 hours) for corrosion resistance
- Thermal cycling (-40℃ to 80℃, 500 cycles) for temperature stability
- Impact testing (10J impact on trim rings) to simulate road debris hits
Material Expertise: Matching Materials to Wheel Applications
Wheel accessories balance strength, weight, and aesthetics—Goldcattle selects materials based on functional requirements and vehicle type:
Material | Modified Treatments | Application Scenarios | Key Technical Properties |
---|---|---|---|
High-Strength Steel (10.9/12.9 grade) | Quench-tempered, zinc plating | Wheel bolts, lugs, heavy-duty adapters | Tensile strength 1000-1200MPa, high clamping force, cost-effective for standard vehicles. |
Aluminum Alloy (6061, 7075) | T6 heat treatment, anodizing | Lightweight spacers, center caps, racing lugs | 30-50% lighter than steel, corrosion resistance, high strength-to-weight ratio (7075: 572MPa tensile strength). |
Titanium Alloy (Ti-6Al-4V) | Beta annealing, PVD coating | Racing wheel bolts, high-end spacers | 40% lighter than steel, 600MPa tensile strength, excellent corrosion resistance—ideal for motorsport. |
ABS Plastic (with PC blend) | UV-stabilized, chrome plating | Wheel center caps, trim rings | Impact resistance (-40℃), customizable colors/finishes, cost-effective for decorative parts. |
Carbon Fiber Reinforced Polymer (CFRP) | Epoxy resin matrix, clear coating | Luxury center caps, racing spacers | 70% lighter than aluminum, high rigidity, premium aesthetic for high-end vehicles. |
Customization Capabilities: From Design to Delivery
Wheel accessories are both functional and stylistic—Goldcattle supports end-to-end customization to meet unique vehicle and brand needs:
- Design collaboration: Our engineering team works with clients to optimize designs for manufacturability, using 3D modeling (SolidWorks, AutoCAD) to refine:
- Wheel adapter offset (10-50mm) for wider stances
- Center cap logos (embossed, laser-etched, or 3D-printed)
- Bolt head styles (hex, socket, spline drive) for security or aesthetics
- Vehicle-specific solutions: Supports all makes/models, from vintage cars (1960s muscle cars) to modern EVs (Tesla Model S). A custom wheel spacer for a classic 1969 Camaro was designed to fit modern brake calipers while maintaining OEM wheel fitment.
- Branding integration: Adds logos, part numbers, or serial numbers via:
- Laser engraving (depth 0.1-0.5mm) on metal parts
- In-mold labeling (IML) on plastic center caps
- Custom powder coat colors matched to brand palettes
- Production flexibility:
- Prototypes: 3-5 days via CNC machining or 3D printing
- Small batches: 10-500 units for custom builds or racing teams
- Mass production: 500,000+ units/month for OEM and aftermarket suppliers
Case Studies: Solving Wheel Accessory Challenges
-
Lightweight racing wheel bolts for a GT3 team:
Challenge: The team needed wheel bolts that reduced unsprung weight without sacrificing strength, to improve acceleration and handling.
Solution: Goldcattle designed titanium bolts (Ti-6Al-4V) with a hollow core, reducing weight by 55% vs. steel bolts. Each bolt weighed 28g (vs. 62g steel), withstanding 1200N·m torque. Result: The team reported 0.3s faster lap times due to reduced rotational mass. -
Custom center caps for a luxury SUV brand:
Challenge: The client required center caps with a 3D embossed logo, chrome finish, and UV resistance for desert climates.
Solution: We used ABS/PC blend plastic with a chrome-plated vacuum metallization layer and added a UV-stabilized clear coat. Testing confirmed no fading after 3,000 hours of Arizona sunlight simulation. Result: The caps became a signature design element, with 98% customer satisfaction in post-launch surveys.
Why Choose Goldcattle for Wheel Accessories?
- Automotive focus: 26 years of specializing in wheel components, with 100+ custom designs validated by leading wheel manufacturers (BBS, Enkei, TSW).
- Safety-first manufacturing: Every part meets or exceeds global standards (SAE J2530, ISO 898-1, FMVSS 109) for load, torque, and corrosion resistance.
- Cost optimization: Design-to-cost engineering (e.g., hollow titanium bolts) reduces material usage by 20-30% without compromising performance.
- Global compliance: Parts meet EU REACH (no heavy metals), California Proposition 65, and China GB standards for automotive accessories.
Start Your Wheel Accessory Project Today
Whether you’re building a racing car, customizing a vehicle, or supplying OEM wheels, Goldcattle’s precision and flexibility ensure your wheel accessories perform and look exceptional.
Contact our wheel team: Send your 3D models, drawings, or design concepts to [email], and receive a feasibility report, material recommendations, and quote within 24 hours.
“Goldcattle’s custom wheel spacers solved our fitment issues with the new brake kit on our off-road truck line. Their attention to tolerance and corrosion resistance meant zero returns—we’ve since expanded our order to 5,000 units/month.” — Product Manager, a U.S. aftermarket wheel company