In the pursuit of engine performance enhancement, the intake manifold serves as the critical component for air distribution, directly impacting combustion efficiency, horsepower output, and fuel economy. Custom CNC intake manifold services leverage material innovation, aerodynamic optimization, and precision manufacturing to deliver end-to-end solutions for high-performance vehicles, new energy applications, and specialized equipment.
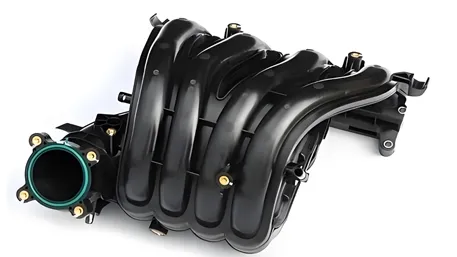
Grade |
Density (g/cm³) |
Thermal Conductivity (W/(m·K)) |
Temperature Resistance (℃) |
Applications |
Machining Parameters |
A356 |
2.7 |
150 |
≤250 |
High-RPM Engines |
5-axis milling Vc=200m/min |
6061-T6 |
2.7 |
167 |
≤180 |
Lightweight Tuning |
Anodized surface treatment |
Technical Breakthroughs:
- High-pressure die casting (HPDC) reduces porosity to 0.1%, achieving Ra≤1.6μm airway surfaces
- Integrated resonator design reduces intake pulsation by 20% via finite element analysis (FEA)
Type |
Density (g/cm³) |
Tensile Strength (MPa) |
Temperature Resistance (℃) |
Machining Technology |
Performance Advantages |
CFRP |
1.6 |
2,000 |
≤150 |
Vacuum-assisted resin transfer molding (VARTM) |
50% weight reduction, 30% modal frequency increase |
Process Innovations:
- 3D braiding technology increases fiber volume fraction to 65%
- Laser cutting achieves ±0.05mm precision on airway ports
Grade |
Density (g/cm³) |
Yield Strength (MPa) |
Temperature Resistance (℃) |
Applications |
Inconel 625 |
8.4 |
450 |
≤980 |
Turbocharged Engines |
Cutting-Edge Applications:
- Electron beam welding (EBW) achieves 90% parent material strength
- Aluminizing treatment enhances oxidation resistance
Technology:
Heidenhain iTNC 640 control enables smooth airway surface machining with ±0.003mm positioning accuracy.
Key Parameters:
- DMG MORI DMU 70 eVolution Machine
- Spindle Speed: 42,000rpm
- Positioning Accuracy: ±0.003mm
Process Advantages:
- Airway Forming:
- Ball end mills (φ8mm) achieve:
- Aluminum: Vc=180m/min, f=0.05mm/z
- ≤±1.5% cross-sectional area deviation
- Integrated Resonator Machining:
- 40% efficiency improvement with mirror surface finish
Process |
Material |
Precision (mm) |
Applications |
Selective Laser Sintering (SLS) |
Nylon |
±0.1 |
Prototype validation (120℃) |
Direct Metal Laser Sintering (DMLS) |
Aluminum |
±0.05 |
Lightweight structures (99.9% density) |
Performance Comparison:
Process |
Lead Time |
Material Utilization |
Max Wall Thickness (mm) |
Die Casting |
4 weeks |
60% |
5 |
DMLS |
5 days |
95% |
3 |
Process |
Principle |
Applications |
Parameters |
Anodizing |
Aluminum oxide film growth |
Aluminum corrosion resistance |
15-25μm thickness, HV300 hardness |
Electroless Nickel Plating |
Ni-P alloy deposition |
Carbon fiber metallization |
10-20μm thickness, HV500 hardness |
Plasma Spraying |
Ceramic coating deposition |
High-temperature oxidation resistance |
70MPa bond strength |
- Technical Input:
- Customer-provided engine specs + reverse engineering (±0.02mm scanning)
- Design Goals:
- CFD-optimized airway curvature to increase flow coefficient by 15%
- Material selection (e.g., aluminum + carbon fiber hybrid)
- CAD Modeling:
- CATIA V5 spiral airway design with ≥30mm curvature radius
- ISO 228 throttle body interface integration
- CAE Validation:
- ANSYS Fluent airflow simulation (target 120m/s velocity)
- Modal analysis to avoid 2nd-order engine vibrations
- Rapid Prototyping:
- SLS nylon (3-day delivery) + DMLS aluminum (7-day delivery)
- Testing:
- Airflow measurement (±0.5% accuracy)
- Pressure drop testing (target ≤5kPa)
- Process Parameters:
- Aluminum finishing: Vc=250m/min, f=0.08mm/z
- Carbon fiber layup optimization (±45°/0° hybrid)
- Quality Control:
- CMM inspection (≤±1% cross-sectional area deviation)
- Ultrasonic testing (φ0.5mm flaw detection)
- Modular Delivery:
- Includes sensor mounts and thermal insulation pads
- Aftersales Service:
- CFD analysis report + annual performance upgrades
- Material: A356 aluminum + carbon fiber reinforcement
- Design Features:
- Dual-stage variable length runners
- Integrated mass air flow sensor housing
- Performance Gains:
- +30hp peak power (6,500rpm)
- 20% faster throttle response
- Innovation: 3D-printed titanium alloy manifold
- Specifications:
- Weight: 1.2kg (vs 4.5kg cast iron)
- 800℃ temperature resistance
Q1: What is the minimum order quantity?
A: 50 units with modular tooling, offering 25% cost savings over traditional methods.
Q2: How is airflow consistency ensured?
A: 5-axis machining + in-process inspection achieve ≤±1% area deviation and 99.5% flow consistency.
Q3: What are new energy vehicle requirements?
A: Integrated battery cooling interfaces, 180℃ temperature resistance, and ≤3kPa pressure drop.
Q4: What is CFRP manifold lifespan?
A: Vacuum infusion + metallization treatment ensures 80,000km durability (vs industry 50,000km).
Whether for high-flow racing manifolds, hybrid integrations, or extreme environment applications, our services deliver micron-level precision and lifetime support.
Click below for a free technical consultation and quote!
- Technical Edge: German 5-axis machines + 3D printing for CFRP layup optimization
- Service Promise: 72-hour prototypes, 100% airflow testing, and lifetime maintenance
- Industry Leadership: Proven solutions for racing, EVs, marine, and industrial sectors
Let’s redefine engine performance together with cutting-edge manufacturing!