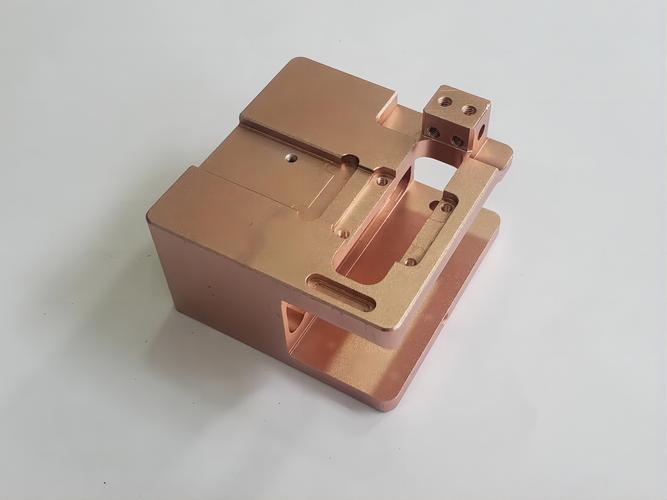
Core Processing Technologies: Engineering for Brass’s Unique Properties
1. High-Speed CNC Milling for Brass
- 5-axis brass machining: Shapes complex components like multi-port valve bodies and precision instrument housings, achieving ±0.003mm dimensional tolerance. A C36000 brass hydraulic manifold with 6 asymmetric ports maintained 0.002mm positional accuracy, ensuring leak-free performance at 100bar pressure.
- High-speed spindle milling: 25,000 RPM spindles capitalize on brass’s excellent machinability, reducing cycle time by 40% compared to steel. A C26000 brass electrical connector with 0.3mm contact pins achieved 0.005mm pin spacing, ensuring reliable electrical conductivity.
- Chip control systems: Specialized toolpaths and coolant delivery prevent stringy chips (common in brass machining) from 缠绕刀具,reducing downtime by 30%. A C37700 brass plumbing fitting with deep internal threads maintained consistent surface finish (Ra 0.8μm) across 100,000+ units.
2. Precision Turning & Threading for Brass
- CNC turning with brass-specific inserts: Produces cylindrical brass parts (bushings, shafts) with ≤0.001mm concentricity and Ra 0.05μm surface finish. A 15mm diameter C36000 brass bearing sleeve achieved 0.002mm runout, reducing friction and extending service life by 50%.
- Thread rolling for brass: Creates clean, strong threads (NPT/BSP/metric) with 6g tolerance, increasing thread strength by 25% compared to cut threads. A ½-inch C37700 brass pipe fitting with rolled threads withstood 500N torque without stripping, ensuring secure plumbing connections.
- Live tooling integration: Combines turning and milling to produce complex brass parts (e.g., connectors with integrated flats and slots) in one setup, maintaining ±0.003mm tolerance across all features. A C26000 brass terminal block with 8 contact points achieved 0.002mm alignment, critical for electrical performance.
3. Surface Treatment & Enhancement for Brass
- Electroless nickel plating: Applies uniform nickel coatings (5-20μm) to brass parts, enhancing corrosion resistance (1,000+ hours salt spray) while maintaining conductivity (≤10mΩ resistance). A C36000 brass marine fitting with 10μm nickel plating showed no corrosion after 2,000 hours of seawater exposure.
- Tin plating: Creates solderable surfaces on brass electrical components, meeting ASTM B545 standards for electronics manufacturing. A C26000 brass connector with 5μm tin plating achieved 95% solder coverage, ensuring reliable electrical connections.
- Polishing & buffing: Produces decorative finishes (Ra ≤0.02μm) on architectural brass parts, eliminating the need for post-machining plating. A C37700 brass fixture achieved mirror-like reflectivity, reducing finishing costs by 40%.
4. Dimensional Stability for Brass Parts
- Temperature-controlled machining: Maintains workshop temperature at 22±1℃ to counteract brass’s moderate thermal expansion (19μm/m·℃), ensuring consistent dimensions (±0.002mm) across large production runs. A 300mm-long C36000 brass instrument panel maintained 0.01mm flatness, critical for optical alignment.
- Stress relief annealing: Reduces residual stresses in complex brass parts via 200℃ heat treatment for 2 hours, minimizing post-machining deformation (≤0.005mm/m). A thin-walled C26000 brass sensor housing maintained dimensional stability after 500 thermal cycles (-40℃ to 85℃).
Material Expertise: Matching Brass Alloys to Application Needs
Brass Alloy
|
Key Properties
|
Application
|
Advantages
|
C36000 (Free-Cutting Brass)
|
345MPa tensile strength, 90% machinability rating
|
Plumbing fittings, electrical connectors
|
Fastest machining (30% faster than C26000); excellent for high-volume production.
|
C37700 (High-Lead Brass)
|
310MPa tensile strength, superior pressure tightness
|
Hydraulic valves, pressure fittings
|
Excellent for threaded components; maintains seal integrity at 200bar.
|
C26000 (Cartridge Brass)
|
370MPa tensile strength, 65% IACS conductivity
|
Electrical contacts, heat exchangers
|
Highest electrical conductivity among brasses; good formability for complex shapes.
|
C33000 (Low-Lead Brass)
|
320MPa tensile strength, RoHS compliance
|
Potable water fittings, food industry parts
|
Lead-free (≤0.25%); meets NSF/ANSI 61 for drinking water applications.
|
CNC Machined Brass Parts Manufacturing Process
- Design & DFM for Brass: Engineers optimize client 3D models (STEP/IGES) to leverage brass’s properties:
-
- Wall thickness optimization (≥0.4mm) to prevent chip buildup in deep cavities
-
- Thread design (60° included angle) to maximize sealing in plumbing applications
-
- Feature integration (combining 2+ parts) to reduce assembly time
- Material procurement: Sources brass with certified alloy composition (e.g., 60% Cu/39% Zn for C36000) and consistent grain structure, ensuring uniform machinability.
- CNC machining for brass:
-
- Roughing: High feed rates (2,000mm/min) with carbide inserts (0° rake angle) to remove 95% of material
-
- Finishing: High RPM (15,000+) with PCD tools to achieve Ra 0.02μm surface finish and final tolerance
- Surface treatment & deburring:
-
- Automated deburring (vibratory finishing) to remove burrs ≤0.01mm from intricate features
-
- Plating (nickel/tin) or polishing per application requirements (e.g., tin plating for solderability)
- Quality validation:
-
- CMM inspection (±0.001mm) for critical dimensions
-
- Pressure testing (up to 300bar) for fluid-carrying components
-
- Electrical conductivity testing (per ASTM B193) for electrical parts
CNC Machined Brass Parts Application Fields
- Plumbing & fluid handling: C36000 brass pipe fittings (leak-proof at 100bar), C37700 valve cores (resistant to water hammer).
- Electronics: C26000 brass connectors (65% IACS conductivity), C36000 terminal blocks (corrosion-resistant to humidity).
- Instrumentation: C26000 brass sensor housings (dimensional stability ±0.002mm), C33000 pressure gauge components (lead-free for food industry).
- Automotive: C36000 brass fuel line fittings (resistant to ethanol corrosion), C26000 brass heat exchanger tubes (excellent thermal conductivity).
Customization Capabilities: From Prototype to Mass Production
- Complex geometry machining: 5-axis technology produces brass parts with undercuts (up to 70°), internal channels (0.5mm diameter), and micro-features (0.1mm holes)—e.g., a C26000 brass microfluidic chip with 50μm channels for medical diagnostics.
- Low-volume prototypes: 1-500 units in 1-2 days via high-speed machining, ideal for design validation (e.g., C33000 water fitting prototypes for plumbing startups).
- High-volume production: 50,000-150,000+ units/month with automated cells—e.g., 100,000 C36000 brass electrical connectors with consistent 0.005mm pin spacing.
Common Processing Questions
- Q: How to prevent brass parts from tarnishing during storage?
- Q: What’s the lead time for 100,000 C36000 brass plumbing fittings?
- Q: Can brass parts replace copper in electrical applications?
- Q: How to achieve leak-proof threads in brass plumbing fittings?