In the rugged world of construction, mining, and agricultural machinery, the reliability and durability of components are non-negotiable. Custom CNC (Computer Numerical Control) construction machinery parts play a pivotal role in ensuring the efficiency, safety, and longevity of heavy equipment. As industries demand parts that can withstand extreme loads, harsh environments, and precise operational requirements, CNC machining has emerged as the definitive manufacturing solution. This article explores the technical prowess, customization process, material selection, quality control, and industry applications of custom CNC construction machinery parts.
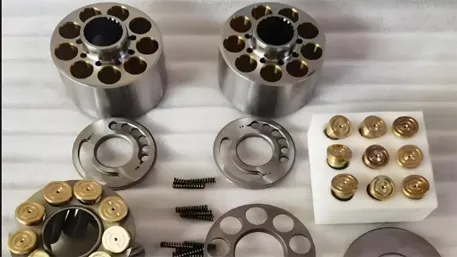
CNC machining systems are built to deliver uncompromising precision even for large-scale, high-tolerance parts. With positioning accuracy of ±0.01mm and repeat positioning accuracy of ±0.02mm, our machines handle components ranging from tiny hydraulic fittings to massive axle housings. For example, when machining boom arm pivot points for excavators, the bore diameter tolerance is controlled within ±0.015mm, ensuring smooth articulation and reduced wear. This level of precision minimizes stress concentrations, a critical factor in preventing catastrophic failures in load-bearing components.
Five-axis CNC technology excels at creating intricate geometries required for modern machinery. Whether it’s the curved surfaces of loader bucket teeth, the internal channels of hydraulic manifolds, or the tapered threads of heavy-duty bolts, five-axis machines achieve seamless integration of multiple features in a single setup. Compared to traditional methods, this reduces setup errors by 80% and shortens production time by 50%. For instance, a single five-axis machine can mill the complex profile of a bulldozer’s track link, including pin holes and wear-resistant coatings, with positional accuracy within ±0.01mm.
To tackle the challenges of machining tough materials like alloy steel and cast iron, we employ specialized techniques:
- High-Power Spindle Systems: Capable of 15,000 RPM, these spindles deliver aggressive material removal rates while maintaining stability, ideal for roughing large components like crane pedestals.
- Thermal Stability Control: Linear scales and temperature sensors compensate for thermal expansion, ensuring dimensional consistency even during prolonged machining of heat-sensitive parts.
- Hardness-Enhancing Treatments: Post-machining processes like induction hardening (up to HRC 55) and nitrocarburizing are integrated into the workflow, enhancing wear resistance in critical areas such as gear teeth and pivot surfaces.
Our team starts with a detailed consultation to understand your equipment’s operational demands—load specifications, environmental conditions, and maintenance requirements. Using CAD/CAM software, we convert concepts into 3D models, optimizing for manufacturability and performance. For example, a mining company’s request for a corrosion-resistant dragline bucket hinge led to a design incorporating stress-relief grooves and reinforced weld points, validated through finite element analysis (FEA).
We offer a range of materials tailored to harsh environments:
Material |
Key Properties |
Typical Applications |
4140 Alloy Steel |
High tensile strength (1,030 MPa), excellent fatigue resistance |
Axles, gears, hydraulic cylinder rods |
Gray Cast Iron (ASTM A48 Class 35) |
Superior damping capacity, cost-effective wear resistance |
Gearboxes, pump housings, engine mounts |
Hardox® Wear Plate |
Impact resistance (up to 500 HBW hardness), abrasion resistance |
Bucket teeth, crusher components, conveyor parts |
Once designs are approved, production begins on our fleet of CNC turning, milling, and grinding machines. Real-time monitoring via IoT sensors tracks spindle load, tool wear, and temperature, ensuring consistency across large batches. Customers access a secure portal to view progress, with automated updates on material sourcing, machining stages, and quality checks.
Every part undergoes multi-stage testing:
- Dimensional Verification: CMM scanning ensures critical dimensions meet ISO 2768-1 precision standards.
- Mechanical Testing: Tensile tests, impact tests, and hardness measurements confirm material integrity.
- Non-Destructive Evaluation (NDE): Magnetic particle inspection (MPI) and ultrasonic testing (UT) detect internal flaws in welds and castings.
- Excavators: Custom CNC-machined bucket pins (4140 steel, induction-hardened) withstand 50% higher cyclic loads than standard parts, reducing downtime by 30%.
- Crane Components: Slewing ring raceways (heat-treated to HRC 45) achieve backlash-free rotation, improving load stability in high-rise construction.
- Haul Truck Axles: CNC-turned from quenched-and-tempered 4340 steel, these axles resist deformation under 200-ton payloads, with a service life extended by 25%.
- Drill Rig Parts: Hardox®-lined auger flights maintain precision even in abrasive soil, reducing maintenance costs for mining exploration equipment.
- Tractor Transmission Gears: Hobbing and shaving processes on CNC machines achieve AGMA Quality Level 10, minimizing noise and improving power transfer efficiency by 15%.
- Combine Harvester Headers: Lightweight aluminum alloy (7075-T6) components reduce fuel consumption while withstanding impact from crop debris.
We achieve ±0.01mm on small parts and ±0.05mm on components over 1 meter, meeting or exceeding OEM specifications for fit and function.
Yes—processes like plasma spraying (for ceramic coatings) and electroplating (for hard chrome) are integrated into our workflow, with thickness control within ±5 microns.
Simple components: 5–7 days; complex assemblies with heat treatment: 10–15 days. Rush orders with 24–48-hour turnaround are available for urgent needs.
Absolutely—our team can reverse-engineer legacy parts using 3D scanning, ensuring compatibility with older equipment while improving performance through modern materials.
“CNC parts that outlast the job site.”
— John Deere Construction
“Their custom bucket teeth in Hardox® steel lasted 40% longer than stock parts in our demolition excavators. The CNC-machined geometry reduced digging resistance, improving fuel efficiency.”
“Precision that keeps mining operations moving.”
— Caterpillar Mining
“The CNC-machined dragline bearings they produced met our stringent ISO 13799 standards, with dimensional accuracy that eliminated costly on-site adjustments.”
From load-bearing structures to precision hydraulics, our custom CNC construction machinery parts are engineered to thrive in the toughest environments. Contact us today to discuss your project—we’ll deliver parts that combine rugged durability with pinpoint precision, ensuring your equipment operates at peak performance, every time.
Custom CNC Construction Machinery Parts: Built for the Heavy-Duty World.