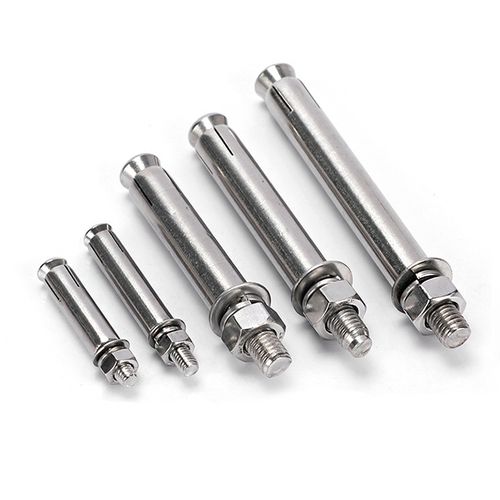
Core Processing Technologies: Engineering for Secure Fastening
1. CNC Precision Turning & Milling
- Swiss-type CNC turning: Produces screw bodies and sleeves with ±0.005mm shank tolerance, ensuring smooth expansion. A M12 sleeve anchor here maintains 30-35kN force across 10,000 units, eliminating looseness.
- CNC milling for drive heads: Creates hex, Phillips, or custom heads (±0.02mm) for tool compatibility. A aerospace M10 screw with a 12-point head withstands 50Nm torque without stripping.
- Thread rolling: Cold-forms threads (ISO metric/UNC) to boost tensile strength by 20-30%, ensuring secure engagement. M16 wedge anchors achieve 45kN pull-out in C30 concrete—15% higher than cut threads.
2. Heat Treatment & Surface Hardening
- Induction hardening: Hardens sleeves to 55-60 HRC (ductile core: 30-35 HRC) for uniform expansion without cracking, enduring 100+ installation cycles.
- Carburizing: Enhances M20-M30 bolts with 0.8-1.2mm hardened layers, resisting vibration in industrial machinery (20-2000Hz).
- Stress relief annealing: Eliminates machining stresses at 600-650℃, limiting deformation to ≤0.02mm over 12 months.
3. Surface Coating & Corrosion Resistance
- Zinc plating with passivation: Offers 500+ hours salt spray resistance (RoHS-compliant), ideal for indoor/mild outdoor use (furniture, fixtures).
- Hot-dip galvanizing: 85-100μm zinc coats resist 1,000+ hours of salt spray, suiting coastal bridges or marine builds.
- Electroless nickel plating: Provides 1,500+ hours corrosion resistance (uniform coverage on threads), ideal for aerospace and food-grade apps.
4. Quality Testing for Reliable Anchoring
- Dimensional checks: CMMs verify thread pitch (±0.01mm) and shank diameter (±0.005mm).
- Mechanical tests: Pull-out strength (e.g., M12 ≥18kN in C30 concrete), shear strength (≥30kN), and torque-to-failure (45-50Nm for M16).
- Environmental trials: Salt spray (500-2,000 hours), thermal cycling (-40℃ to 120℃), and humidity testing (95% RH) validate durability.
Material Expertise: Matching Materials to Expansion Screw Applications
Material
|
Treatment
|
Use Cases
|
Key Properties
|
Carbon Steel (8.8/10.9)
|
Zinc plating
|
Construction, machinery
|
800-1000MPa tensile strength; cost-effective for dry environments.
|
304/316 Stainless Steel
|
Passivation
|
Marine, food plants
|
316: 2,000+ hours salt spray; 515MPa strength.
|
Alloy Steel (10.9/12.9)
|
Hot-dip galvanizing
|
Bridges, heavy machinery
|
1000-1200MPa; M20 ≥40kN pull-out in C40 concrete.
|
CNC Expansion Screw Machining Technologies
- Multi-axis CNC machining: 5-axis mills shape complex anchor geometries (e.g., tapered sleeves) with ±0.01mm accuracy, ensuring consistent expansion in variable substrates.
- Automated thread rolling: Computer-controlled rolling machines produce uniform threads on M6-M30 screws, reducing defects by 90% compared to manual processes.
- Robotic coating application: Ensures even zinc/electroless nickel coverage (±2μm thickness) on threads and sleeves, critical for corrosion resistance in harsh environments.
- In-line vision inspection: Cameras check 100% of parts for dimensional errors (e.g., thread pitch, head alignment) during production, maintaining 99.9% first-pass yield.
Custom CNC Expansion Screw Manufacturing Process
- Design & DFM: Engineers analyze client drawings (STEP/IGS) to optimize for manufacturability—e.g., adjusting sleeve tapers for concrete strength.
- Material selection: Choose steel/stainless based on environment (e.g., 316 for coastal areas) and load requirements (alloy steel for ≥40kN pull-out).
- CNC machining: Swiss turning creates screw bodies; milling shapes drive heads; thread rolling strengthens engagement surfaces.
- Heat treatment: Induction hardening/carburizing enhances wear resistance, followed by stress relief annealing to prevent warping.
- Coating application: Zinc plating, hot-dip galvanizing, or nickel plating applied per corrosion needs, with 100% adhesion testing.
- Quality validation: CMM inspection, pull-out testing, and salt spray trials ensure compliance with ASTM F1554 and client specs.
Custom Expansion Screw Application Fields
- Construction: Wedge anchors for concrete foundations, sleeve anchors for steel beam mounting (M16-M30, hot-dip galvanized).
- Automotive: 304 stainless steel expansion screws for chassis mounting, resisting road salt and vibration (M6-M12).
- Industrial machinery: Alloy steel screws with carburized threads for heavy equipment anchoring, enduring 1M+ vibration cycles (M12-M24).
- Furniture & fixtures: Brass/M8 screws with decorative heads for wooden furniture, ensuring flush mounting and corrosion resistance.
- Aerospace: Titanium alloy anchors for lightweight structural fastening, with electroless nickel plating (M8-M16).
Customization Capabilities: From Design to Delivery
- Design collaboration: Engineers optimize length (20-300mm), drive types, or coatings. A construction client’s M20 150mm screw with custom hex heads reached prototypes in 5 days.
- Application-specific solutions:
-
- Construction: Hot-dip galvanized wedge anchors for concrete.
-
- Automotive: 304 stainless screws resistant to road salt.
-
- Furniture: M6-M8 brass screws with flush heads.
- Production flexibility: 10-100 prototypes (3-5 days); 100k-1M+ units/month via automated lines.
Common Processing Questions
- Q: How to ensure uniform expansion in weak concrete?
- Q: Can screws withstand high vibration (e.g., industrial machinery)?
- Q: What’s the lead time for custom M30 anchors (10k units)?
- Q: How to prevent thread stripping during installation?
Why Choose Goldcattle?
- Expertise: 26 years in fasteners, with 100+ designs meeting ASTM/DIN standards.
- Quality: 100% CMM inspection and pull-out testing; full traceability from raw material to delivery.
- Efficiency: Automated lines reduce costs by 15%; material optimization cuts waste by 10%.
- Compliance: RoHS/REACH-certified, suitable for global projects (EU, US, ASEAN).