In the intricate world of mechanical power transmission, gear chains play a crucial role in ensuring smooth, efficient, and reliable operation across a wide range of industries. From industrial machinery and automotive applications to robotics and agricultural equipment, the demand for high – performance gear chains has been on the rise. As industries strive for enhanced precision, durability, and customized solutions, CNC (Computer Numerical Control) machining has emerged as the go – to technology for manufacturing custom gear chains. This article will explore the technical capabilities, customization process, material selection, quality control, and industry applications of custom CNC gear chains.
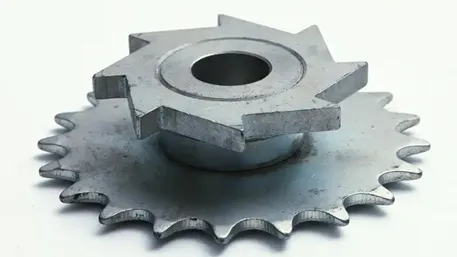
I. Technical Excellence: Redefining Gear Chain Manufacturing
(A) Unrivaled Machining Precision
CNC machining systems are engineered to offer uncompromising accuracy. With positioning accuracy reaching ±0.005mm and repeat positioning accuracy of ±0.01mm, we can fabricate gear chains with extremely tight tolerances. For instance, when manufacturing sprockets for high – speed conveyor systems, the pitch diameter and tooth profile can be maintained within ±0.005mm. This level of precision is essential for minimizing chain slippage, reducing vibration, and ensuring consistent power transfer. It also significantly extends the service life of the gear chain, reducing maintenance and replacement costs.
(B) Complex Design Execution
Five – axis CNC machining technology enables the creation of gear chains with complex geometries. Whether it’s sprockets with unique tooth shapes, multi – stage gear assemblies, or chains with specialized link designs, the five – axis system can execute these designs in a single setup. Compared to traditional machining methods, which often require multiple setups and are more prone to errors, five – axis CNC machining reduces setup – related errors from ±0.03mm to within ±0.01mm. Moreover, it boosts production efficiency by over 60%, significantly shortening the production cycle. This allows for faster turnaround times for custom gear chain orders, meeting the urgent needs of businesses.
(C) Advanced Process Optimization
During the machining of gear chains, challenges such as material deformation, surface roughness, and tooth wear need to be addressed. We deploy a comprehensive set of advanced techniques to overcome these challenges. By carefully selecting cutting parameters, optimizing toolpaths, and implementing real – time monitoring and control systems, we can minimize material deformation. Additionally, the use of high – speed machining and advanced finishing processes results in gear chains with a superior surface finish. A smooth surface finish reduces friction between the chain links and sprocket teeth, enhancing the efficiency of power transmission and further extending the lifespan of the gear chain.
II. End – to – End Customization: Tailoring Gear Chains to Your Exact Requirements
(A) In – Depth Requirement Analysis and Design Conceptualization
When you approach us with your gear chain requirements, our experienced engineering team engages in detailed discussions to understand your application, performance expectations, and design preferences. Using state – of – the – art CAD/CAM software, we generate multiple design concepts. We then collaborate closely with you, refining the designs until they perfectly align with your vision. Whether you need a gear chain for a standard industrial application with specific torque requirements or a completely new design for a cutting – edge robotic system, we have the expertise to bring your ideas to life.
(B) Strategic Material Selection and Cost Evaluation
Based on the finalized design, we recommend the most suitable materials for your gear chains. We consider factors such as the application environment, load – bearing capacity, and cost – effectiveness. For high – load applications in industrial machinery, we might recommend alloy steels like 4140, which offer excellent strength and wear resistance. For applications where corrosion resistance is crucial, such as in marine or food processing industries, stainless steels like 316L are ideal. Simultaneously, we conduct a detailed cost analysis, factoring in material costs, machining complexity, and production volume, to provide you with a transparent and competitive quote.
(C) Precision Manufacturing and Order Tracking
Once you approve the design and quote, production commences. You can monitor the progress of your order in real – time through our dedicated online tracking platform. Our skilled technicians adhere to strict manufacturing standards, using advanced CNC machines to produce gear chains that meet the highest quality benchmarks. We keep you informed at every stage of the production process, from raw material procurement to the final machining operations, ensuring complete transparency.
(D) Rigorous Quality Assurance and Timely Delivery
After production, each gear chain undergoes a rigorous quality inspection. Only gear chains that meet our exacting standards are shipped to you. We perform dimensional inspections using coordinate measuring machines (CMMs) to ensure that all critical dimensions, such as pitch, tooth size, and link dimensions, are within ±0.005mm. Surface roughness is also measured to ensure that the surfaces are smooth enough for efficient operation. In addition, we conduct mechanical and fatigue tests to validate the performance of the gear chain. We also offer comprehensive after – sales support, addressing any concerns you may have during the product’s lifecycle.
III. Strategic Material Selection: Choosing the Right Material for the Job
(A) Alloy Steels: High – Strength and Durable
Alloy steels, such as 4140, are popular choices for gear chains in high – load applications. 4140 steel contains alloying elements like chromium, molybdenum, and manganese, which enhance its strength and hardenability. After heat treatment, it can achieve a high hardness, making it highly resistant to wear and fatigue. With a tensile strength of up to 1030 MPa and a yield strength of around 860 MPa, 4140 alloy steel is suitable for gear chains used in heavy – duty industrial machinery, such as mining equipment and large – scale manufacturing plants.
(B) Stainless Steels: Corrosion – Resistant and Reliable
Stainless steels, especially grades like 316L, are ideal for applications where corrosion resistance is essential. 316L stainless steel contains molybdenum, which provides enhanced resistance to chloride – induced corrosion. It has a tensile strength of ≥485 MPa, a yield strength of ≥170 MPa, and good formability. This makes it suitable for gear chains used in marine environments, food processing facilities, and pharmaceutical industries, where exposure to corrosive substances is common.
(C) Aluminum Alloys: Lightweight and Cost – Effective
Aluminum alloys, such as 6061 – T6, can be used for gear chains in applications where weight reduction is a priority. 6061 – T6 aluminum alloy has good machinability and a relatively low density compared to steels. It offers a balance of strength and cost – effectiveness, with a tensile strength of around 310 MPa and a yield strength of 276 MPa. This makes it suitable for gear chains in applications like robotics and some automotive components, where reducing weight can improve energy efficiency and overall performance.
IV. Stringent Quality Control: Ensuring Top – Tier Gear Chains
(A) Raw Material Inspection
All incoming raw materials for gear chains are subject to strict quality checks. We use spectroscopic analysis to verify the chemical composition of metals, ensuring that they meet the required standards. For example, when using 4140 alloy steel, we confirm that the chromium, molybdenum, and manganese contents are within the specified ranges. Additionally, hardness testing and metallographic analysis are performed to ensure the material’s integrity. For aluminum alloys, we check for alloy purity and mechanical properties such as tensile strength and yield strength.
(B) In – Process Monitoring
Throughout the manufacturing process, we employ statistical process control (SPC) techniques to monitor key manufacturing parameters. Regular sampling and data collection help us identify and correct any potential issues promptly. We monitor parameters such as cutting forces, spindle speeds, and feed rates during machining. If any parameter deviates from the set values, we can adjust the machining process in real – time to ensure consistent product quality.
(C) Final Product Validation
Before shipping, each gear chain undergoes a comprehensive inspection. We use CMMs to verify dimensional accuracy, ensuring that all critical dimensions are within ±0.005mm. Surface roughness measurements are taken to ensure that the surfaces are smooth enough for proper operation. In addition, we conduct mechanical tests, such as torque testing and fatigue testing, to validate the performance of the gear chain under real – world conditions. Only gear chains that pass all these tests are considered ready for delivery.
V. Diverse Industry Applications: Empowering Multiple Sectors
(A) Industrial Machinery
In the industrial machinery sector, custom CNC gear chains are used in a wide range of equipment, including conveyors, power – transmission systems, and manufacturing machinery. The high precision and durability of these gear chains ensure smooth operation, reduce downtime, and improve overall productivity. For example, in a large – scale manufacturing plant, custom gear chains can be designed to handle high – torque loads, enabling the efficient operation of heavy – duty machinery.
(B) Automotive Industry
In the automotive industry, gear chains are used in various applications, such as timing chains in engines and drive chains in power – take – off systems. Custom CNC – manufactured gear chains can be optimized for specific engine performance requirements, providing better synchronization, reduced noise, and increased fuel efficiency. They also offer enhanced durability, which is crucial for the long – term reliability of automotive components.
(C) Robotics
In the field of robotics, gear chains are used for precise motion control. Custom gear chains can be designed to meet the specific torque, speed, and positioning requirements of robotic systems. Their high precision ensures accurate movement of robotic arms and joints, enabling robots to perform complex tasks with greater accuracy and efficiency. This is especially important in industries such as electronics manufacturing and medical robotics.
(D) Agricultural Equipment
In agricultural equipment, gear chains are used in applications like tractor PTO systems, combine harvesters, and irrigation systems. Custom CNC gear chains can be designed to withstand the harsh operating conditions of the agricultural environment, including dirt, moisture, and high – torque loads. Their durability and reliability contribute to the efficient operation of agricultural machinery, increasing productivity on farms.
VI. Frequently Asked Questions (FAQ)
(A) What is the typical precision of custom CNC gear chains?
Our CNC machining can achieve a dimensional tolerance of ±0.005mm, ensuring that the gear chains are manufactured to the highest precision standards.
(B) How do I choose the right material for my gear chain?
The choice depends on your application’s requirements. For high – load applications, alloy steels like 4140 are recommended. For corrosion – resistant applications, stainless steels such as 316L are ideal. If weight reduction is important, aluminum alloys like 6061 – T6 can be considered.
(C) What is the lead time for custom gear chains?
Lead times vary depending on the complexity of the design and order quantity. Simple designs can be completed in 3 – 5 days, while more complex ones may take 7 – 10 days. Rush orders are available upon request.
(D) Can CNC machining handle complex gear chain designs?
Absolutely. Our five – axis CNC machines can fabricate gear chains with intricate geometries, including unique tooth shapes and multi – stage assemblies, meeting even the most demanding design requirements.
(E) How much does it cost to customize a gear chain?
Costs are determined by factors such as material, design complexity, precision requirements, and order quantity. While small – batch customization may be relatively costly, economies of scale can significantly reduce per – unit costs for larger orders.
VII. Customer Testimonials
An industrial manufacturing company approached us to develop custom gear chains for their high – speed conveyor system. Our team used five – axis CNC machining to achieve the required precision of ±0.005mm. The gear chains not only met the strict quality standards of the industrial sector but also improved the efficiency of the conveyor system. As a result, the company was able to increase their production output and reduce maintenance costs.
A leading automotive manufacturer needed custom gear chains for a new line of high – performance engines. We implemented advanced machining techniques and rigorous quality control measures to ensure that the gear chains met the highest automotive standards. The customer reported a significant reduction in engine noise and improved fuel efficiency, leading to enhanced product performance and customer satisfaction.
Reach Out Now for Your Custom CNC Gear Chains!
Regardless of your industry or application, our team of experts is ready to collaborate with you. We offer a seamless end – to – end service, from design to delivery. Contact us today to discuss your project requirements and take the first step towards getting top – quality custom CNC gear chains.