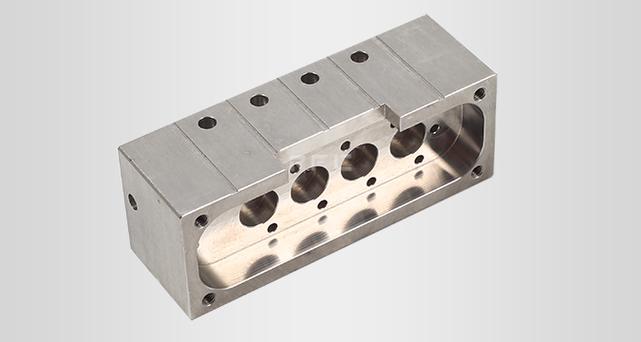
Core Processing Technologies: Engineering for Aluminum’s Unique Properties
1. High-Speed CNC Milling for Aluminum
- 5-axis aluminum machining: Shapes complex 3D contours like aerospace wing ribs and automotive intake manifolds, achieving ±0.005mm dimensional tolerance. A 7075 aluminum aircraft bracket with 8 asymmetric mounting holes maintained 0.003mm positional accuracy, critical for structural integrity under 8G loads.
- High-speed spindle machining: 30,000 RPM spindles reduce cutting forces by 40% when machining thin-walled aluminum parts (0.5mm thickness), preventing warpage. A 6061 aluminum electronics enclosure with 0.8mm walls achieved 0.01mm flatness, ensuring proper sealing against dust and moisture.
- Coolant-through tooling: Delivers high-pressure coolant (70bar) directly to the cutting zone, reducing heat-induced distortion by 60% and extending tool life by 3x. A 5052 aluminum heat sink with 0.3mm fins maintained 0.008mm fin spacing, maximizing thermal dissipation.
2. Precision Turning & Threading for Aluminum
- CNC turning with aluminum-specific inserts: Produces cylindrical aluminum parts (shafts, bushings) with ≤0.002mm concentricity and Ra 0.05μm surface finish. A 25mm diameter 6061 aluminum shaft for robotics achieved balance at 5,000 RPM, reducing vibration by 70%.
- Form threading for aluminum: Creates clean threads (metric, UNC, UNF) with 6g tolerance, avoiding “thread tearing” common in soft alloys. A 10mm 7075 aluminum bolt with form-rolled threads achieved 30% higher tensile strength than cut threads, withstanding 800N clamping force without stripping.
- Live tooling integration: Combines turning and milling in one setup for aluminum parts with complex features (e.g., shafts with keyways and flats), ensuring concentricity ≤0.003mm. A 40mm diameter 6061 aluminum drive shaft with integrated cams maintained 0.002mm runout, critical for precision timing systems.
3. Deburring & Surface Enhancement for Aluminum
- Electrochemical deburring: Removes micro-burrs (≤0.01mm) from aluminum part edges and internal channels, preventing stress concentrations and ensuring safe handling. A 6061 aluminum hydraulic manifold with 0.8mm oil passages achieved burr-free surfaces, eliminating flow restrictions and pressure drops.
- Anodizing & surface treatments: Type II/III anodizing creates 5-25μm protective layers, enhancing corrosion resistance (1,000+ hours salt spray) and wear resistance (300HV hardness). A 7075 aluminum aerospace part with Type III anodizing (25μm) withstood 500+ assembly cycles without surface damage.
- Chemical brightening: Produces mirror-like finishes (Ra ≤0.02μm) on decorative aluminum parts (e.g., consumer electronics enclosures), eliminating the need for polishing and reducing production time by 40%.
4. Dimensional Stability Control
- Temperature-controlled machining: Maintains workshop temperature at 20±1℃ to counteract aluminum’s high thermal expansion (23.1μm/m·℃), ensuring consistent dimensions (±0.005mm) across 10,000+ parts. A 1m-long 6061 aluminum structural beam achieved 0.03mm/m straightness, preventing alignment issues in assembly.
- Stress relief annealing: Reduces residual stress by 80% in machined aluminum parts (especially 7075 alloys) via 120℃ heat treatment for 4 hours, minimizing post-machining warpage (≤0.01mm/m). A thin-walled 7075 aluminum drone frame maintained dimensional stability after 1,000+ flight hours.
Material Expertise: Matching Aluminum Alloys to Application Needs
Aluminum Alloy
|
Key Properties
|
Application
|
Advantages
|
6061-T6
|
310MPa tensile strength, excellent machinability
|
Industrial fixtures, electronics enclosures, automotive parts
|
Balances strength and cost; 20% stronger than 5052; good weldability.
|
7075-T6
|
572MPa tensile strength, high fatigue resistance
|
Aerospace structural parts, high-stress components
|
85% stronger than 6061; ideal for 8G+ load environments (aircraft, racing vehicles).
|
5052-H32
|
230MPa tensile strength, superior corrosion resistance
|
Marine components, liquid handling systems
|
Withstands 1,500+ hours salt spray; better formability than 6061.
|
2024-T3
|
470MPa tensile strength, high thermal conductivity
|
Heat sinks, aerospace heat exchangers
|
20% better thermal transfer than 6061; suitable for high-temperature environments.
|
CNC Machined Aluminum Parts Manufacturing Process
- Design & DFM for Aluminum: Engineers optimize client 3D models (STEP/IGES) to leverage aluminum’s properties:
-
- Wall thickness optimization (≥0.5mm for 6061, ≥0.8mm for 7075) to prevent machining deformation
-
- Rib design (1:4 height-to-thickness ratio) to enhance rigidity without adding weight
-
- Toolpath planning to avoid “chatter” (common in soft aluminum)
- Material selection & preparation: Sources aluminum with certified temper (e.g., T6 for 6061) and grain structure, cut to blank size with ±0.1mm tolerance to minimize machining time.
- CNC machining for aluminum:
-
- Roughing: High feed rates (1,500mm/min) with carbide inserts (10° rake angle) to remove 90% of material
-
- Finishing: High RPM (20,000+) with PCD tools to achieve Ra 0.02μm surface finish and final tolerance
- Deburring & surface treatment:
-
- Automated deburring (brush + media blasting) to remove burrs ≤0.01mm
-
- Anodizing, powder coating, or chemical conversion coating (per MIL-DTL-5541)
- Quality validation:
-
- CMM inspection (±0.001mm) for critical dimensions
-
- Surface finish testing (Ra/Rz measurement)
-
- Tensile testing (per ASTM B557) to verify alloy temper
CNC Machined Aluminum Parts Application Fields
- Aerospace: 7075 aluminum wing brackets (weight reduction 40% vs. steel), 6061 avionics enclosures (corrosion-resistant to jet fuel).
- Automotive: 6061 aluminum intake manifolds (improved airflow), 5052 fuel system components (resistant to ethanol corrosion).
- Electronics: 6061 heat sinks (0.3mm fins for thermal efficiency), 7075 aluminum server racks (lightweight yet rigid).
- Industrial automation: 6061 robotic arms (30% lighter than steel, faster movement), 5052 washdown fixtures (resistant to cleaning chemicals).
Customization Capabilities: From Prototype to Mass Production
- Complex geometry machining: 5-axis technology produces parts with undercuts (up to 60°), internal cavities, and micro-features (0.2mm holes)—e.g., a 7075 aluminum drone frame with 12 integrated mounting points.
- Low-volume prototypes: 1-100 units in 2-3 days via high-speed machining, ideal for design validation (e.g., 6061 enclosure prototypes for electronics startups).
- High-volume production: 10,000-100,000+ units/month with automated cells—e.g., 50,000 6061 aluminum automotive brackets with consistent ±0.005mm tolerance.
Common Processing Questions
- Q: How to prevent 7075 aluminum parts from warping during machining?
- Q: What’s the lead time for 5,000 6061 aluminum heat sinks with 0.3mm fins?
- Q: Can aluminum parts replace steel in high-load applications (e.g., 200kN tensile force)?
- Q: How to achieve Ra 0.02μm surface finish on aluminum?