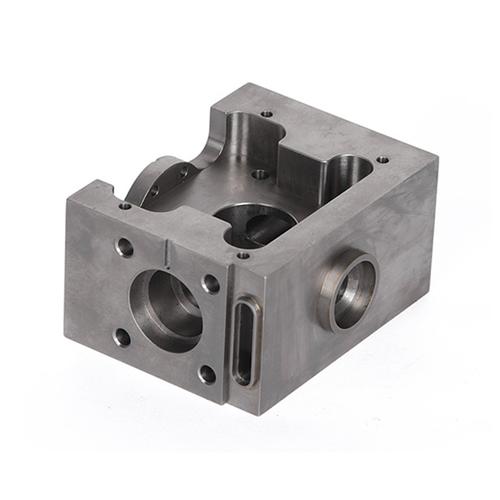
I. Core Properties of Titanium and Machining Challenges
(A) Performance Advantages Driving High-End Applications
- Lightweight & High Strength: With a density 60% that of steel and a specific strength exceeding 200 MPa·cm³/g, ideal for lightweight designs of UAV frames and aerospace engine blades.
- Extreme Environment Adaptability: Operates reliably from -253°C (liquid hydrogen) to 500°C (high-temperature turbine), with a dense oxide film ensuring no corrosion in seawater/salt spray for over 1,000 hours.
- Biological Safety: Zero cytotoxicity and bone integration interface strength ≥ 30MPa, meeting safety standards for medical implants (joint prostheses, dental implants).
(B) Machining Difficulties and Technical Countermeasures
Property
|
Machining Challenge
|
Key Technical Solutions
|
Poor Thermal Conductivity
|
Heat accumulation causing rapid tool wear
|
High-speed machining (70% heat carried away by chips) + high-pressure internal cooling (5-10MPa)
|
High Chemical Reactivity
|
Formation of hard/Brittle metamorphic layer at high temperatures
|
TiAlN-coated tools + inert gas protection
|
Low Elastic Modulus
|
Vibration-induced deformation in thin-wall machining
|
5-axis machining + vibration-damping fixtures
|
II. Analysis of Five Core Machining Technologies
(A) 5-Axis Machining: Precision Forming for Complex Surfaces
- Technical Advantages:
-
- Completes 95% of machining features in one setup, with positioning accuracy ±5″ and surface profile accuracy ±0.02mm (vs. ±0.1mm for 3-axis).
-
- German DMG/Mazak machines support 0.1μm-level interpolation, increasing aerospace blade machining efficiency by 57%.
- Typical Applications: Complex surfaces for aerospace engine integrated blisks and medical joint stems.
(B) High-Speed Cutting (HSC): Efficient Thin-Wall Machining
- Process Parameters:
-
- Cutting speed 100-300m/min, feed rate 500-2000mm/min, surface roughness Ra ≤ 0.8μm.
-
- High-pressure internal cooling maintains cutting zone temperature ≤150°C, extending tool life to 60 minutes (20 minutes for steel).
- Application Scope: Titanium thin-wall parts with length-width ratio >5 (wall thickness ≥1mm), material removal rate ≥85%.
(C) Specialized Machining Technology Combinations
Technology Type
|
Machining Capability
|
Precision Index
|
Typical Applications
|
EDM (Electrical Discharge Machining)
|
0.05mm micro-holes / 0.02mm narrow slots
|
Dimensional accuracy ±0.005mm
|
Medical implant porous layers (100-500μm)
|
Laser Machining
|
Cutting ≤5mm thin plates / 0.1mm welding
|
Heat-affected zone <0.3mm
|
Aerospace skins / electronic heat sinks
|
ECM (Electrochemical Machining)
|
Stress-free machining of 0.3mm ultra-thin parts
|
Surface roughness Ra ≤0.2μm
|
Aerospace bulkheads / medical mirror components
|
III. Full-Procedure Customization Solutions
(A) Design and Material Engineering
- Multi-Format Data Compatibility:
-
- Supports 2D drawings (CAD/DWG), 3D models (STEP/IGES), and reverse-engineering point cloud data (accuracy ±0.01mm).
-
- Completes design for manufacturability (DFM) analysis within 72 hours to optimize structural designs for machining.
- Precision Material Selection:
-
- High-temperature scenarios: Ti-6Al-4V ELI alloy with 300°C strength ≥650MPa, 12% higher than standard grades.
-
- High-load scenarios: β-type titanium alloy (Ti-10V-2Fe-3Al) with yield strength ≥1,200MPa.
- Preprocessing Techniques:
-
- 3,000-ton hydraulic forging (deformation ≥40%) refines grain size to ≤50μm, improving mechanical property uniformity by 30%.
-
- Surface treatments: Hard anodizing (5-25μm for aerospace wear resistance) / micro-arc oxidation (50-100μm for medical bone integration).
(B) Production and Quality Control
- Flexible Manufacturing Capabilities:
-
- Rapid Prototyping: Delivers 1-10 samples within 7-10 days with Zeiss CMM inspection reports (accuracy ±0.0015mm).
-
- Mass Production: 100+ CNC machines (including 10 5-axis units) produce 3,000 complex parts monthly, material utilization ≥90%.
- Stringent Quality System:
-
- Testing Capabilities: Spectral analysis (chemical composition ±0.01%), ultrasonic flaw detection (0.1mm internal defect resolution), and ISO 10993 biocompatibility certification for medical parts.
-
- Traceability System: Full-procedure tracking from raw material heat numbers to machining parameters, enabling 48-hour issue part localization and recall.
IV. Multi-Industry Application Scenarios
(A) Aerospace Industry
- Structural Parts: Achieves 20%-30% weight reduction, with titanium accounting for 15% of Boeing 787 airframe weight, improving fuel efficiency by 15%.
- Engine Components: Blade surface profile accuracy ±0.02mm, flange parallelism ≤0.03mm, fatigue life ≥10⁷ cycles.
(B) Medical Device Industry
- Joint Prostheses: Pure Ti TA2 material with micro-arc oxidation achieves 92% bone integration rate, clinical service life >20 years, and taper fit accuracy at 0.001mm level.
- Dental Implants: EDM-processed 150μm micro-holes promote osteoblast adhesion, initial stability torque ≥35N·cm, cell viability ≥95% in cytotoxicity tests.
(C) Energy and Marine Engineering
- Fuel Cell Bipolar Plates: 0.2mm titanium thin plate laser cutting (accuracy ±0.03mm), corrosion resistance 3x higher than stainless steel.
- Seawater Desalination Equipment: Titanium heat exchangers with surface roughness Ra ≤0.6μm, heat transfer efficiency 40% higher than stainless steel, service life extended by 3-5 years.
V. Technology Selection and Cost Optimization
Requirement Type
|
Preferred Technology Combination
|
Core Indicators
|
Low-Volume Precision Parts
|
EDM + Laser Machining
|
Prototyping cycle ≤10 days, design iteration support
|
Medium-High Volume Parts
|
HSC + 5-Axis Machining
|
Unit cost reduced by 15%-20%, tool life ≥80 parts per edge
|