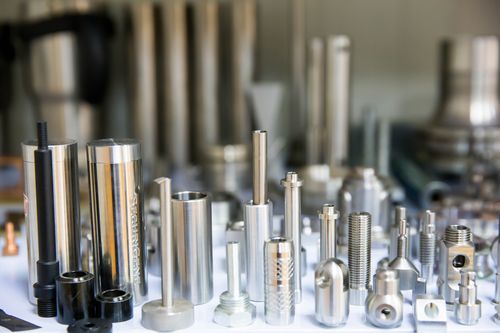
Core Processing Technologies: Engineering for Unique Requirements
1. Flexible Multi-Axis Machining
- 5-axis CNC machining: Handles complex 3D contours and undercuts (e.g., automation robot end-effectors with 30° tilted grippers) in a single setup, reducing alignment errors by 95%. A custom conveyor system bracket with 6 irregular mounting points achieved ±0.005mm positional accuracy, ensuring seamless assembly.
- 3+2 axis machining: Optimizes production of semi-complex parts (e.g., special-purpose gearboxes) by fixing multi-angle features, cutting cycle time by 40% vs. 3-axis methods. A 250mm-long steel gearbox housing with 4 inclined oil ports maintained ±0.01mm dimensional stability.
- CNC turning with live tooling: Produces non-standard shafts with integrated features (e.g., keyways, threads, and flats) in one operation, ensuring concentricity ≤0.003mm. A 40mm diameter drive shaft with 3 asymmetric cams maintained balance at 2,500 RPM, reducing vibration by 50%.
2. Adaptive Machining for Irregular Blanks
- 3D scanning & offset machining: Scans uneven castings or forgings (e.g., 10mm thickness variation) to create digital models, then programs CNC machines to adjust toolpaths dynamically—ensuring consistent final dimensions (±0.01mm). A custom valve body from a cast iron blank with 5mm warpage achieved 0.008mm tolerance after machining.
- Force-sensing machining: Sensors detect material hardness variations in heat-treated parts (e.g., 40-50HRC steel), adjusting feed rates in real-time to prevent tool breakage. A non-standard hardened steel camshaft with localized hard spots was machined without defects, maintaining Ra 0.8μm surface finish.
3. Precision Workholding for Odd Shapes
- Custom fixture design: Engineers create dedicated jigs with modular clamping (±0.002mm locating accuracy) for irregular parts—e.g., a “C-shaped” automation bracket was secured with 4 adjustable clamps, ensuring ≤0.003mm runout during machining.
- Magnetic clamping: Holds ferrous parts (e.g., steel plates with curved edges) without mechanical pressure, reducing distortion by 70% vs. traditional vises. A 500mm × 300mm curved steel panel for industrial machinery achieved 0.02mm flatness after machining.
- Contour clamping: Uses 3D-printed soft jaws (custom-shaped to match part contours) to secure delicate non-standard parts (e.g., thin-walled plastic housings), preventing deformation during high-speed milling.
4. Quality Validation for Custom Geometries
- 3D dimensional inspection: CMMs with 5-axis probes verify 1,000+ data points on non-standard parts, comparing results to client 3D models (deviation ≤0.01mm acceptable). A custom medical device frame with free-form surfaces achieved 99.8% geometric conformity.
- Functional testing: Validates part performance under real-world conditions—e.g., a non-standard hydraulic manifold underwent 100bar pressure testing with zero leakage, and a custom gripper mechanism completed 10,000 cycle tests without failure.
- Reverse engineering verification: For parts replicated from samples (no CAD files), 3D scans of finished components are overlain with original sample scans, ensuring ±0.02mm replication accuracy.
Material Expertise: Matching Materials to Non-Standard Applications
Material
|
Key Properties
|
Application
|
Advantages
|
Carbon Steel (45#, 4140)
|
High tensile strength (600-1,200MPa), cost-effective
|
Custom gearboxes, structural brackets
|
Ideal for high-load (≤300kN) industrial applications; easy to weld.
|
Stainless Steel (304, 316L)
|
Corrosion resistance, 515MPa tensile strength
|
Food processing equipment, marine non-standard parts
|
Withstands 1,000+ hours salt spray; suitable for washdown environments.
|
Aluminum Alloy (6061-T6, 7075-T6)
|
Lightweight, 310-572MPa tensile strength
|
Automation components, lightweight brackets
|
30% lighter than steel; achieves Ra 0.05μm surface finish.
|
Engineering Plastics (PA6+GF30, POM)
|
Low friction, chemical resistance
|
Wear parts, non-metallic gears
|
Self-lubricating; reduces noise by 20% in moving assemblies.
|
Custom CNC Mechanical Non-Standard Parts Manufacturing Process
- Design & DFM for Manufacturability: Engineers analyze client requirements (3D models or physical samples) to optimize:
-
- Part geometry (e.g., adding 0.5mm draft angles to deep cavities for easier tool access)
-
- Material selection (e.g., 316L stainless for wet environments)
-
- Feature integration (e.g., combining 2 parts into 1 to reduce assembly)
- 3D scanning (if applicable): For legacy parts or physical samples, 3D scanning (0.005mm accuracy) creates digital models for CNC programming, ensuring replication fidelity.
- CNC programming: CAM software generates adaptive toolpaths, accounting for:
-
- Irregular blank dimensions
-
- Thin-walled features (≥1mm thickness)
-
- Critical tolerances (e.g., ±0.005mm for mating surfaces)
- Multi-process machining: 5-axis milling shapes complex contours; CNC turning creates rotational features; live tooling adds details (threads, keyways); high-speed spindles refine surfaces (Ra 0.8μm).
- Post-processing: Deburring (≤0.01mm edge radius), heat treatment (for metal parts), and surface coating (painting, plating) applied per requirements.
- Quality validation: CMM inspection, functional testing (e.g., load testing for brackets), and 3D model overlay analysis ensure compliance with client specs.
Custom CNC Mechanical Non-Standard Parts Application Fields
- Industrial automation: Custom robot end-effectors (grippers, tool changers), non-standard conveyor components (guides, rollers).
- Manufacturing machinery: Special-purpose gearboxes, custom fixtures for CNC machines, non-standard cams and linkages.
- Food & beverage: 316L stainless steel custom mixers, non-standard transfer chutes with easy-clean contours.
- Material handling: Heavy-duty steel lifting brackets, custom pallet stops, non-standard pulley systems.
Customization Capabilities: From Prototype to Production
- Complex geometry customization: Machines parts with undercuts (up to 45°), internal cavities, and integrated features (e.g., a custom valve manifold with 8 internal flow channels).
- Low-volume production: 1-500 units via 5-axis machining, ideal for:
-
- Custom machine upgrades
-
- Replacement parts for obsolete equipment
-
- Pilot production testing
- High-volume scalability: 500-30,000+ units/month with dedicated fixtures and automated cells (e.g., 10,000 custom aluminum automation brackets).
Common Processing Questions
- Q: How to ensure a custom bracket with 5mm thin walls doesn’t deform during machining?
- Q: What’s the lead time for 200 custom steel gearbox housings with complex 3D features?
- Q: Can you replicate a 30-year-old non-standard part with no drawings?
- Q: How to reduce cost for low-volume non-standard parts?