In the field of medical device manufacturing, the precision, biocompatibility, and corrosion resistance of stainless – steel parts directly affect the safety of surgeries, the lifespan of equipment, and the rehabilitation effect of patients. With the development of medical technology towards minimally invasive and intelligent directions, CNC (Computer Numerical Control) processing technology, with its excellent precision manufacturing capabilities and material adaptability, has become the core technical support for customizing medical stainless – steel parts. This article will systematically analyze the technical logic and engineering value of custom CNC medical stainless – steel parts services from dimensions such as technical advantages, materials engineering, processing technology, quality control, and industry applications.
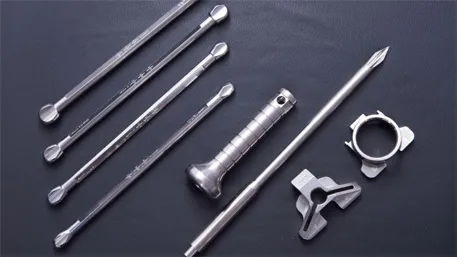
CNC technology provides three core supports for the processing of medical stainless – steel parts through digital control and multi – axis linkage capabilities:
The positioning accuracy of CNC machine tools can reach ±0.005mm, the repeat positioning accuracy is ±0.01mm, and the surface roughness Ra≤0.4μm. For example, when processing precision shaft – type parts of surgical instruments, the roundness error can be controlled within ±0.002mm, ensuring the stability and precision of instrument operation.
Five – axis CNC equipment can achieve the processing of spatial curved surfaces, thin – wall structures (wall thickness ≤ 0.3mm), and micro – features (such as micro – holes with a diameter of 0.1mm) that are difficult to complete by traditional processes. For example, the special – shaped jaws of minimally invasive surgical instruments can be formed in one – step through five – axis milling, avoiding the accumulation of errors in multiple processes.
CNC technology is compatible with medical – grade stainless – steel materials such as 316L and 304. For the characteristics of 316L stainless steel (carbon content ≤ 0.03%, molybdenum content ≥ 2%), the cutting parameters can be optimized: adopt a low – speed (500 – 800r/min), high – feed (0.1 – 0.15mm/z) strategy, and cooperate with high – pressure internal – cooling tools to reduce material hardening, and the tool life can be extended by 3 times.
Material selection is a key link in customizing medical stainless – steel parts and needs to be combined with clinical requirements and material characteristics:
- 316L stainless steel: It contains molybdenum elements, has excellent resistance to chloride ion corrosion (PREN value ≥ 25), and its biocompatibility has passed the ISO 10993 certification. It is suitable for implants and surgical instruments.
- 304 stainless steel: It has a lower cost and good corrosion resistance. It is suitable for non – implant components such as medical device casings and brackets.
- The surgical tool handle is made of 316L stainless steel (tensile strength ≥ 515MPa). After CNC milling and surface hardening treatment, the hardness reaches above HV200, ensuring no deformation during long – term use.
- Implant screws use cold – forged 316L stainless steel. After grain refinement, the yield strength is ≥ 205MPa, improving fatigue resistance.
To meet the special needs of medical stainless – steel parts, the CNC processing technology achieves a double breakthrough in efficiency and quality through the following technological innovations:
Through five – axis linkage, complex curved surfaces can be processed in one clamping. For example, for the bionic contact surface of knee joint implants, the processing efficiency is increased by 70%, and the surface roughness Ra≤0.4μm, promoting bone tissue integration.
When processing 316L stainless steel, use integral carbide tools (such as a 1.0mm diameter ball – nose milling cutter) in combination with high – pressure internal – cooling technology. The cutting temperature is reduced by 30%, and the tool life is extended by 2 times.
High – speed cutting (HSC) technology is used for the processing of medical device casings. The rotation speed is 10000r/min, and the feed rate is 1500mm/min, increasing the efficiency by 40%.
- Electropolishing: The surface roughness Ra≤0.2μm, reducing bacterial adhesion, which is suitable for surgical instruments.
- Passivation treatment: An oxide film is formed on the surface of 316L stainless steel to improve corrosion resistance. The salt – spray test can reach 1000 hours without rust.
To ensure that products meet the strict standards of the medical industry, custom CNC medical stainless – steel parts need to go through a strict quality control process:
- Coordinate Measuring Machine (CMM) conducts full – size scanning, and the tolerance of key dimensions (such as the opening and closing degree of instrument jaws) is controlled within ±0.01mm.
- Geometric tolerance detection: Flatness ≤ 0.02mm/m, coaxiality ≤ 0.01mm, ensuring the assembly accuracy of instruments.
- Spectral analysis confirms the composition of 316L stainless steel (such as nickel content ≥ 10%, molybdenum content ≥ 2%).
- Mechanical property testing: Tensile strength ≥ 515MPa, elongation ≥ 40%, ensuring the safety of implants.
- Cytotoxicity test (ISO 10993 – 5): No cytotoxic reaction.
- Sterilization treatment: Through ethylene oxide (EO) sterilization or irradiation sterilization to ensure a sterile state.
- The 316L stainless – steel intervertebral fusion device, processed by five – axis CNC milling, has a controllable porosity (30% – 50%), promotes bone growth, and has a mechanical strength of ≥ 150MPa.
- Minimally invasive surgical forceps, after CNC precision processing and electropolishing, have a surface roughness Ra≤0.1μm, reducing tissue damage.
- The 304 stainless – steel medical trolley frame, after CNC pipe bending and welding, has a dimensional tolerance of ±0.05mm, a load – bearing capacity of up to 200kg, and is corrosion – resistant and easy to clean.
- The 316L stainless – steel infusion pump gear has a tooth – shape accuracy of ISO 6 level and a transmission noise of ≤ 40dB, ensuring the quiet operation of the equipment.
- The 316L stainless – steel artificial hip joint stem, after CNC turning and surface sandblasting, has a roughness Ra≤1.6μm, promotes bone integration, and has a service life of more than 15 years.
- Cold – forged 316L stainless – steel bone – connecting screws have a thread accuracy of ±0.01mm and a shear strength of ≥ 450MPa.
CNC processing can achieve a dimensional tolerance of ±0.005mm, a repeat positioning accuracy of ±0.01mm, and a surface roughness of Ra≤0.4μm, meeting the high – precision requirements of surgical instruments and implants.
Choose 316L stainless steel for implants (excellent biocompatibility), and 304 stainless steel for non – implant components (lower cost). It needs to be evaluated according to specific application scenarios.
The production cycle depends on the complexity of the parts and certification requirements. Simple parts usually take 7 – 10 days, and complex implants may take 15 – 30 days. Urgent customization is supported.
Yes, the service complies with the ISO 13485 medical device quality management system, provides material certifications, test reports, and sterilization verifications, and can assist customers in obtaining certifications such as FDA and CE.
The cost is affected by materials, processing complexity, and certifications. The cost of small – batch customization is relatively high, but CNC technology reduces the unit cost through process optimization. In the long run, the cost – performance ratio is better than that of traditional processes.
Inquire now and get your exclusive customized solution!
Whether it is the precision components of minimally invasive surgical instruments, the highly reliable components of medical equipment, or the bionic structures of orthopedic implants, our professional team will rely on the high – precision advantages of CNC technology, combined with medical materials engineering and process innovation, to provide you with a full – process customization service from design, processing to sterilization. Click to leave a message, and let us use a rigorous technical system and reliable quality assurance to customize high – performance and high – safety stainless – steel part solutions for your medical projects, helping you create greater value in the field of life and health!