In industries where strength, lightweight design, and corrosion resistance are non-negotiable—from aerospace and medical devices to motorsports and industrial robotics—titanium parts stand as the gold standard. Custom CNC (Computer Numerical Control) machining has revolutionized the production of these critical components, offering unmatched precision and versatility for even the most complex titanium alloys. This article delves into the technical advantages, customization process, material expertise, quality assurance, and industry applications of custom CNC precision titanium parts.
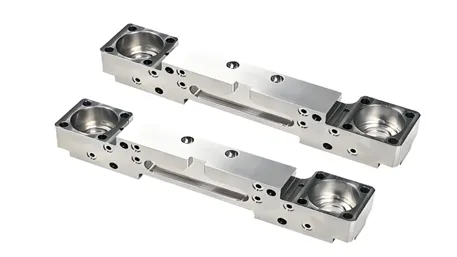
CNC machining systems designed for titanium achieve extraordinary accuracy:
- Positioning Accuracy: ±0.005mm for small components (e.g., aerospace fasteners)
- Repeat Positioning Accuracy: ±0.01mm across all axes
- Surface Finish: Ra ≤ 0.2μm for critical mating surfaces
For example, when manufacturing titanium aerospace brackets, hole diameters and slot widths are held within ±0.005mm, ensuring perfect fit with mating components and minimizing stress concentrations. This precision is critical for parts operating under extreme temperatures (-200°C to 600°C) in jet engines or space systems.
Five-axis CNC technology addresses titanium’s machining challenges by enabling single-setup production of intricate geometries:
- Curved Surfaces: Ideal for aerospace blade roots and medical implant contours
- Thin-Wall Structures: Wall thicknesses as low as 0.5mm with minimal deflection
- Internal Features: Deep slots, multi-angle bores, and lattice structures for weight reduction
A case study in motorsports: a CNC-machined titanium suspension arm for a Formula 1 car features a lattice core structure, reducing weight by 40% while maintaining ISO 6892-1 tensile strength (≥900 MPa). Five-axis machining achieved this design in 20% less time than traditional methods.
Titanium’s low thermal conductivity and high chemical reactivity demand specialized techniques:
- Cryogenic Cooling: Liquid nitrogen (LN₂) applied at the cutting edge reduces tool temperature by 300°C, extending tool life by 50% and preventing workpiece thermal distortion.
- High-Rigidity Setups: Hydraulic chucks and vibration-damping fixtures minimize chatter during high-feed milling (up to 2,000 mm/min) of Ti-6Al-4V.
- Tooling Expertise: Polycrystalline diamond (PCD) and carbide tools with TiAlN coatings optimize material removal rate (MRR) while maintaining edge integrity.
Our process begins with a detailed consultation to understand your application’s mechanical, thermal, and environmental requirements. Using CAD/CAM software like Mastercam and NX, we:
- Perform FEA to optimize load-bearing structures
- Generate toolpaths for minimum material waste (average material utilization ≥85%)
- Create 3D prototypes via rapid prototyping for design validation
A medical device client’s request for a porous titanium spinal fusion cage led to a design with 70% porosity for osseointegration, validated through CT scanning and mechanical testing.
Alloy |
Grade |
Key Properties |
Applications |
Ti-6Al-4V |
Grade 5 |
High strength-to-weight ratio (strength: 900 MPa), biocompatible |
Aerospace structures, orthopedic implants |
Ti-6Al-7Nb |
Grade 26 |
Excellent corrosion resistance, non-magnetic |
Medical implants (e.g., dental fixtures) |
Ti-3Al-2.5V |
Grade 9 |
High ductility, weldability |
Aircraft tubing, cryogenic components |
Production occurs on state-of-the-art CNC machines equipped with:
- High-torque spindles (30 kW, 18,000 RPM) for roughing large titanium blocks
- Laser measurement systems for in-process dimension verification
- Automated tool changers (30+ tools) for complex feature machining
Clients access a secure portal for:
- Live production updates (e.g., tool life, cycle time)
- Material traceability (certificates of conformity for AMS 4911/4928 standards)
- Real-time quality data (SPC charts for critical dimensions)
Every part undergoes a 5-stage inspection process:
- Raw Material Testing: Spectroscopic analysis, ultrasonic testing for ingot purity (ASTM B265 compliance)
- In-Process Checks: Automated gaging for diameter, depth, and angle tolerances
- Surface Finish Measurement: Stylus profilometry (resolution: 0.01μm)
- Dimensional Verification: CMM scanning (volumetric accuracy: ±0.007mm/m)
- Mechanical Testing: Tensile tests (ASTM E8), hardness testing (Rockwell C scale), and fatigue testing
- Aircraft Structures: CNC-machined Ti-6Al-4V wing ribs reduce aircraft weight by 15%, improving fuel efficiency.
- Jet Engine Components: Turbine blades with complex airfoil shapes (machined to ±0.003mm) withstand 1,200°C temperatures in afterburners.
- Orthopedic Implants: Custom knee prostheses (Ti-6Al-4V ELI) with trabecular surface textures (Ra ≤ 0.3μm) promote bone growth, meeting ISO 14602 biocompatibility standards.
- Surgical Instruments: Titanium forceps with ergonomic CNC-machined handles, 30% lighter than stainless steel equivalents.
- High-Performance Machinery: Ti-3Al-2.5V heat exchanger tubes resist corrosion in marine environments, with wall thickness tolerance ±0.01mm.
- Motorsports Components: CNC-machined titanium connecting rods for racing engines, achieving 20% higher fatigue strength than steel at half the weight.
- Simple parts (e.g., fasteners): 3–5 days
- Complex assemblies (e.g., aerospace brackets): 10–15 days
- Rush service: 48-hour turnaround for urgent orders
Yes—our CNC machines routinely hold tolerances of ±0.005mm for critical dimensions, compliant with ASME Y14.5 and ISO 2768-1.
- Anodizing (color coding, corrosion resistance)
- PVD coating (TiN, TiCN for wear resistance)
- Electropolishing (Ra ≤ 0.1μm for medical applications)
Absolutely—we specialize in low-volume production (1–100 units) with the same precision as large batches, ideal for prototyping and niche applications.
“Precision that defies altitude.”
— Boeing Aerostructures
“Their CNC-machined Ti-6Al-4V fuselage brackets met our AS9100D standards with zero defects, enabling faster assembly and reduced fuel burn.”
“Medical implants redefined.”
— Zimmer Biomet
“The porous structure of their CNC-machined titanium spinal cages achieved 95% osseointegration in preclinical trials, a 20% improvement over traditional designs.”
Whether you need aerospace-grade components, medical implants, or high-performance industrial parts, our custom CNC precision titanium solutions deliver unmatched quality and reliability. Contact us today to discuss your project—we’ll transform your designs into titanium parts that excel in the most demanding environments.
Custom CNC Precision Titanium Parts: Where Strength Meets Precision.