In fields such as mechanical manufacturing, construction engineering, and automotive industry, stainless – steel threaded rods are indispensable connecting and transmission components. Their quality directly affects the safety, stability, and service life of equipment or structures. As the manufacturing industry’s demand for high – precision and high – performance parts continues to grow, CNC (Computer Numerical Control) machining technology, with its unique technical advantages, has become the preferred process for producing customized stainless – steel threaded rods. The following article will comprehensively analyze the value of custom CNC stainless – steel threaded rods from the aspects of technical advantages, customization process, material selection, quality control, and industry applications.
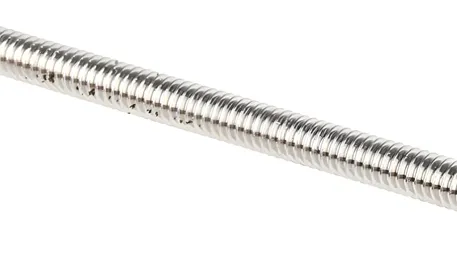
I. Technological Innovation: Redefining Threaded Rod Machining Standards
(A) Ultra – High Thread Precision
CNC machining equipment, relying on advanced numerical control systems, achieves a positioning accuracy of ±0.005mm and a repeat positioning accuracy of ±0.01mm. It can control the pitch error of thread machining within a minimal range. Taking the M16×2 standard thread as an example, by precisely adjusting CNC machining parameters, the pitch error can be stably controlled within ±0.01mm, and the half – angle error of the thread profile can be controlled within ±10′. This ensures high – precision thread matching, effectively enhancing the reliability of connections and reducing the risk of failures caused by thread loosening during equipment operation.
(B) Complex Structure Machining Capability
Five – axis CNC machining technology breaks through the limitations of traditional machining. It can complete the machining of stainless – steel threaded rods with variable pitches, multi – start threads, special – shaped threads, and complex shaft structures in one clamping. Compared with traditional multi – process machining, five – axis machining reduces the number of clampings, lowering the positioning error from ±0.03mm to within ±0.01mm. This not only significantly improves machining accuracy but also increases machining efficiency by more than 60%, greatly shortening the production cycle.
(C) Optimized Machining Process
During the machining of stainless – steel threaded rods, to address issues such as thread deformation and surface quality caused by cutting force and cutting heat, we adopt a series of optimized processes. By reasonably selecting tool paths and cutting parameters, and coordinating with a high – precision cooling system to regulate the machining temperature in real – time, the thread deformation is controlled within a minimal range. At the same time, advanced thread milling technology is used instead of traditional turning processes, improving the surface quality of threads and extending the service life of tools.
II. Full – Chain Customization: Meeting Diverse Customer Demands
(A) Requirement Communication and Solution Design
Once customers put forward customization requirements, our professional technical team will communicate with them in depth to fully understand key information such as the application scenarios, performance requirements, and precision standards of the threaded rods. With rich industry experience, the team uses professional CAD/CAM software to design solutions and provides multiple options for customers to choose from. The solutions are optimized based on customer feedback until the customers are satisfied.
(B) Material Matching and Cost Calculation
According to the determined design solutions, we select the most suitable materials for customers, considering the characteristics of different stainless – steel materials. Meanwhile, we conduct accurate cost calculations by comprehensively considering factors such as material costs, machining complexity, and production cycle, providing customers with clear and reasonable quotations.
(C) Precision Machining and Progress Tracking
After customers confirm the design solutions and quotations, production begins officially. Customers can track the order progress in real – time through an exclusive online platform. During the production process, our technicians strictly follow the process standards and use advanced CNC machining equipment to ensure that every threaded rod meets high – precision requirements.
(D) Quality Inspection and Delivery Service
After the products are machined, they undergo strict quality inspection processes to ensure that they meet design requirements and quality standards. Qualified products are delivered to customers in a timely manner, and we provide comprehensive after – sales services to solve any problems customers encounter during use.
III. Scientific Material Selection: Adapting to Diverse Application Scenarios
(A) 304 Stainless Steel: The All – Round Choice
304 stainless steel has a density of 7.93g/cm³ and excellent comprehensive properties. Its tensile strength is ≥515MPa, yield strength is ≥205MPa, and elongation is ≥40%. This material strikes a good balance among corrosion resistance, machinability, and cost, making it widely used in the manufacturing of threaded rods for general industrial equipment, architectural decoration, and other fields.
(B) 316L Stainless Steel: The Corrosion – Resistant Pioneer
316L stainless steel has a density of 7.98g/cm³. Due to the addition of 2 – 3% molybdenum, its corrosion resistance, especially against chloride ions, is significantly enhanced. Its tensile strength is ≥485MPa, yield strength is ≥170MPa, and elongation is ≥40%. It is suitable for industries with high requirements for corrosion resistance, such as marine engineering, chemical equipment, and food processing.
(C) 2205 Duplex Stainless Steel: The New Favorite for High – Strength and Corrosion Resistance
2205 duplex stainless steel combines the advantages of austenitic and ferritic stainless steels, featuring high strength and good corrosion resistance. Its tensile strength is ≥620MPa, yield strength is ≥450MPa, and elongation is ≥25%. It is often used in scenarios where both high strength and corrosion resistance are required, such as the petrochemical industry and bridge construction.
IV. Stringent Control: Forging Exceptional Quality
(A) Raw Material Inspection
All stainless – steel raw materials used in production undergo strict inspections. Spectroscopic analysis is used to detect the chemical composition of the materials, ensuring that they meet the corresponding standards, such as the specified range of alloying elements in 316L stainless steel. In addition, hardness tests and metallographic analyses are carried out to ensure the stability of raw material quality.
(B) Process Control
During the machining process, statistical process control (SPC) technology is used to monitor key processes in real – time. Products are randomly inspected in each batch, processing data is recorded, and control charts are drawn to promptly identify and correct abnormal situations during the processing, ensuring the consistency of product quality.
(C) Finished Product Inspection
Finished products undergo comprehensive inspections. A coordinate measuring machine (CMM) is used to detect dimensional accuracy, ensuring that the tolerances of key dimensions such as the diameter and thread length of the threaded rods are controlled within ±0.005mm. Comprehensive thread inspections are conducted, including parameters such as pitch, half – angle of the thread profile, and thread pitch diameter, to ensure that the thread accuracy meets the standards. In addition, hardness tests, tensile tests, and salt – spray tests are carried out to ensure that the products meet design requirements.
V. Diverse Applications: Driving Industry Forward
(A) Construction Engineering Field
In construction engineering, customized 304 stainless – steel threaded rods are used in scenarios such as curtain wall installation and steel structure connections. Their high – precision thread matching ensures the reliability of connections, and their good corrosion resistance extends the service life of building structures, reducing maintenance costs.
(B) Automotive Industry
In automotive manufacturing, stainless – steel threaded rods are used for connecting key components such as engines and chassis. Custom CNC stainless – steel threaded rods, with their high precision and strength, meet the strict requirements of automotive connecting components under high – speed driving and complex working conditions, improving the safety and reliability of vehicles.
(C) Chemical Equipment
In chemical equipment, 316L stainless – steel threaded rods operate stably in strongly corrosive media environments due to their excellent corrosion resistance. They ensure the tightness and stability of the equipment, effectively preventing leakage accidents caused by corrosion and safeguarding production safety.
VI. Frequently Asked Questions (FAQ)
(A) What level of precision can custom CNC stainless – steel threaded rods achieve?
Our CNC machining can achieve a dimensional tolerance of ±0.005mm, a pitch error of ±0.01mm, and a half – angle error of the thread profile of ±10′, meeting the requirements of various high – precision equipment.
(B) How do I choose the right stainless – steel material?
The choice should be based on the product’s application environment, performance requirements, and cost budget. For general industrial environments, 304 stainless steel can be selected; for corrosive environments, 316L stainless steel is suitable; and for scenarios with high requirements for both strength and corrosion resistance, 2205 duplex stainless steel is a good option.
(C) How long is the production cycle for custom stainless – steel threaded rods?
The production cycle depends on the complexity of the threaded rods and the order quantity. Simple threaded rods can usually be completed in 3 – 5 days, while complex ones may take 7 – 10 days. We also offer rush customization services to meet customers’ urgent needs.
(D) Can CNC machining achieve the processing of complex thread structures?
Certainly. Our five – axis CNC machining technology can accurately realize various complex thread shapes and shaft structures according to customers’ design drawings, meeting customers’ personalized customization requirements.
(E) How much does it cost to customize stainless – steel threaded rods?
The cost is affected by factors such as materials, machining complexity, precision requirements, and order quantity. The cost of small – batch customization is relatively high, but through process optimization and large – scale production, the unit cost can be effectively reduced.
VII. Customer Testimonials
A construction engineering company needed a batch of high – precision 304 stainless – steel threaded rods for curtain wall installation when undertaking a large – scale commercial complex project. Our team not only controlled the thread accuracy within the standard range through precise parameter adjustment but also used five – axis machining technology to solve the problem of machining the special – shaped heads of the threaded rods. After delivery, all indicators met the requirements as inspected by the customer, ensuring the smooth progress of the project and shortening the project duration.
A chemical enterprise commissioned us to process 316L stainless – steel threaded rods during equipment upgrades. Since the equipment needed to operate in a strongly corrosive environment, there were extremely high requirements for the corrosion resistance and precision of the threaded rods. We adopted advanced machining processes and surface treatment technologies to ensure the quality of the threaded rods. After being put into use, the batch of threaded rods performed well under actual working conditions, effectively reducing the equipment maintenance costs and winning high recognition from the customer.
Contact Us Now for a Tailored Solution!
Whether you are a construction engineering company, automotive manufacturer, or chemical equipment producer, our professional team will leverage the high – precision advantages of CNC technology, combined with stainless – steel material engineering and process innovation, to provide you with a full – process customization service from solution design, machining production, to quality inspection. Click to leave a message. Let’s work together to create high – quality stainless – steel threaded rods and help your business gain a competitive edge in the market!