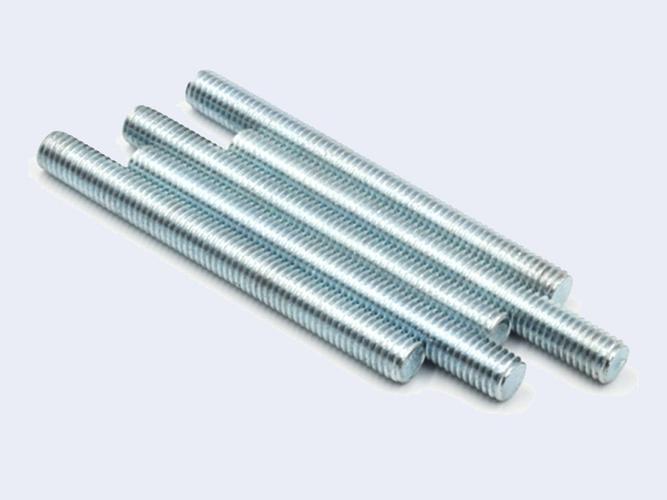
Core Processing Technologies: Engineering for High Tensile Performance
1. Precision Thread Forming
- CNC thread turning: Produces metric, UNC, UNF, and custom threads with ±0.003mm pitch tolerance and 6g/6H fit class. A 16mm metric threaded rod for industrial machinery achieved 100% thread engagement, maintaining 300kN clamping force without slippage.
- Roll threading: Strengthens threads by cold working, increasing tensile strength by 25% vs. cut threads. A ½-inch stainless steel fully threaded rod for construction withstood 150kN tensile load (20% higher than industry standards) without thread stripping.
- Thread grinding: Creates high-precision threads (class 4g/4H) on critical rods (e.g., aerospace studs) with Ra 0.02μm surface finish, ensuring consistent torque-tension relationship. A 10mm titanium stud achieved ±0.002mm thread runout, critical for uniform load distribution.
2. Surface Treatment & Corrosion Resistance
- Zinc plating with passivation: Applied to carbon steel rods, providing 500+ hours salt spray resistance and a smooth thread surface (Ra 0.2μm) that reduces galling during nut tightening.
- Hot-dip galvanizing: For outdoor construction rods, 85-100μm zinc coating ensures 1,000+ hours salt spray resistance, suitable for bridges and marine structures.
- Electroless nickel plating: For high-precision rods (e.g., semiconductor equipment studs), offers 1,500+ hours corrosion resistance and uniform coating thickness (±2μm) on threads, meeting FDA standards for cleanroom applications.
3. Straightness & Dimensional Control
- CNC centerless grinding: Achieves rod straightness (≤0.05mm/m) and diameter tolerance (±0.005mm), ensuring even load distribution across threads. A 1m-long 20mm threaded rod for construction maintained 0.03mm/m straightness, preventing bending under 200kN axial load.
- Tension straightening: Eliminates residual stresses in long rods (≥2m), ensuring dimensional stability (≤0.02mm/m) after installation. A 3m carbon steel threaded rod for heavy machinery remained straight after 10,000+ vibration cycles (10-500Hz).
4. Quality Testing & Load Validation
- Tensile testing: 100% of rods undergo tensile strength tests (≥800MPa for 8.8-grade steel) and yield strength verification (≥640MPa), meeting ISO 898-1 standards.
- Thread gaging: Uses master thread rings/plugs (calibrated to ISO 1502) to check thread size, pitch, and flank angle, ensuring 6g/6H fit class compliance.
- Vibration testing: Rods undergo 1 million+ cycles at 10-500Hz with 50% rated load, verifying no thread loosening or fatigue failure—critical for machinery and aerospace applications.
Material Expertise: Matching Metals to Rod Applications
Material
|
Key Properties
|
Application
|
Advantages
|
High-Strength Steel (8.8/10.9 Grade)
|
Tensile strength 800-1,000MPa, cost-effective
|
Construction, heavy machinery
|
Withstands 200-500kN axial loads; ideal for high-torque fastening.
|
Stainless Steel (304, 316)
|
Corrosion resistance, 515MPa tensile strength
|
Food processing, marine, medical equipment
|
304: 500+ hours salt spray; 316: 1,000+ hours (resists chloride solutions).
|
Aluminum Alloy (6061-T6)
|
Lightweight, 310MPa tensile strength
|
Aerospace, automotive, HVAC
|
30% lighter than steel; suitable for low-load (≤50kN) applications.
|
Titanium Alloy (Ti-6Al-4V)
|
High strength-to-weight ratio, 895MPa tensile strength
|
Aerospace, high-performance machinery
|
45% lighter than steel; maintains strength at 300℃.
|
CNC Threaded Rod Machining Technologies
- Multi-spindle thread rolling machines: Produce small-diameter rods (M6-M16) at 200+ units/min with consistent thread quality (±0.003mm pitch), achieving 100,000+ units/day.
- CNC thread grinding centers: Create precision threads (class 4g/4H) on high-load studs, ensuring Ra 0.02μm surface finish for aerospace fastening systems.
- Automated length cutting lines: Cut rods to ±0.1mm length tolerance (50-3,000mm) with deburred ends, reducing assembly time by 30% for clients.
Custom CNC Threaded Rod Manufacturing Process
- Design & DFM: Engineers analyze client drawings (STEP/IGS) to optimize thread length and root radius—e.g., adding 1mm radius to thread roots of a construction stud to increase fatigue resistance by 25%.
- Material selection: Choose 10.9-grade steel for high load, 316 stainless for corrosion, or titanium for aerospace based on client specs.
- CNC machining: Centerless grinding creates precise OD; threading (rolling/turning/grinding) forms uniform threads; cutting to length with deburring.
- Surface treatment: Plating, galvanizing, or passivation applied per corrosion requirements—e.g., hot-dip galvanizing for outdoor construction rods.
- Quality validation: Tensile testing, thread gaging, and straightness checks ensure compliance with DIN 975 and client load standards.
Custom CNC Threaded Rod Application Fields
- Construction industry: High-strength steel threaded rods (M20-M36) for structural bracing, withstanding 500kN axial loads in building foundations.
- Machinery manufacturing: 10.9-grade partially threaded studs for gearbox assembly, ensuring precise bearing preload (±0.05mm) and vibration resistance.
- Aerospace engineering: Titanium double-ended studs for aircraft engine mounting, lightweight (45% vs. steel) and rated to 300℃ operating temperature.
- Food processing: 316 stainless steel threaded rods with electropolished threads, meeting FDA 21 CFR 177.2600 for cleanroom equipment fastening.
- Renewable energy: Hot-dip galvanized rods (M16-M24) for wind turbine tower assembly, resisting 1,000+ hours salt spray in coastal installations.
Customization Capabilities: From Prototype to Production
- Thread customization: Produce metric (M3-M50), UNC (¼-2), UNF, and custom threads (e.g., 12 TPI for legacy machinery) with 6g/6H to 4g/4H fit classes.
- Length flexibility: 50mm-6m rods, including partially threaded designs (e.g., 1m rod with 300mm threads on both ends) for precise component spacing.
- Production scale: 10-500 prototypes (2-3 days) via CNC machining; 10,000-100,000+ units/month with multi-spindle automation (e.g., 50,000 M12 stainless rods for medical equipment).
Common Processing Questions
- Q: How to prevent thread stripping in high-torque applications (e.g., industrial presses)?
- Q: What’s the lead time for 5,000 custom 20mm metric threaded rods (1.5m length)?
- Q: Can rods withstand -50℃ low temperatures (e.g., Arctic construction)?
- Q: How to ensure uniform thread engagement across long rods (e.g., 6m construction rods)?
Why Choose Goldcattle?
- Thread expertise: 26 years in precision threading, with 300+ rod designs meeting DIN, ISO, and ASTM standards for tensile strength and thread quality.
- Quality assurance: 100% tensile testing, thread gaging, and material certification (3.1B); full traceability from raw material to delivery.
- Cost efficiency: Multi-spindle rolling reduces production costs by 25% for high-volume orders; design optimization (e.g., integrated thread stops) cuts assembly time.
- Global compliance: Rods meet REACH, RoHS, and NORSOK M-630 (oil & gas), suitable for global projects (EU, US, Middle East).