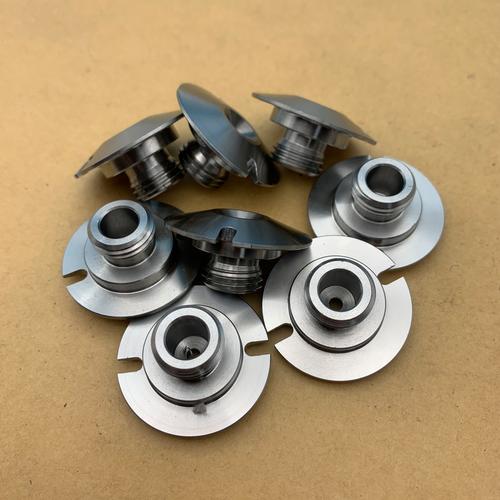
Core Processing Technologies: Engineering for Integrated Precision
1. Multi-Axis Turn-Mill Machining
- 7-axis simultaneous machining: Produces parts with intersecting rotational and milled features—e.g., a titanium aerospace shaft with integrated gear teeth, 4 radial holes, and a threaded end, all machined in one cycle with ±0.002mm positional accuracy. This eliminated 3 assembly steps and reduced cumulative tolerance stack-up by 80%.
- Sub-spindle synchronization: Enables backworking operations (drilling, threading) on the opposite end of parts while the main spindle performs milling, cutting cycle time by 40% compared to traditional turning + milling. A stainless steel medical connector with features on both ends achieved 0.001mm concentricity between main and sub-spindle operations.
- Live tooling with Y-axis: Adds off-center features (e.g., inclined holes at 30°) to cylindrical parts without re-fixturing, ensuring ±0.003mm angular tolerance. A 4140 steel hydraulic valve spool with 6 radial ports at 60° increments maintained 0.002mm port-to-port positional accuracy, critical for flow control.
2. Precision Machining of Hybrid Features
- Turn-mill threading & milling: Combines thread turning (metric/UNC/UNF) with milled flats and keyways on the same part, ensuring 0.002mm alignment between threads and prismatic features. A brass electrical connector with M12 threads and a 12mm hex flat achieved 0.001mm runout between features, preventing cross-threading during assembly.
- Contour milling on rotational parts: Creates complex 3D profiles (e.g., cam lobes, eccentric shafts) with 0.005mm contour accuracy using C-axis interpolation. A 6061 aluminum camshaft for automotive actuators achieved 0.003mm follower contact surface tolerance, reducing vibration by 25%.
- Micro-drilling in turn-mill centers: Produces small holes (0.5-3mm diameter) with ±0.002mm positional tolerance on rotating parts, ideal for fluidic components. A medical stainless steel manifold with 12 × 1mm holes achieved 0.005mm hole-to-hole spacing, ensuring uniform flow distribution.
3. Process Optimization for Turn-Mill Parts
- Toolpath synchronization: CAM software optimizes the sequence of turning, milling, and drilling operations to minimize spindle stops, increasing machine utilization by 35%. A complex 4140 steel gearbox component with 15 features was completed in 8 minutes—50% faster than sequential machining.
- Chip management systems: High-pressure coolant (100bar) and segmented toolpaths prevent chip entanglement in multi-feature parts, reducing manual intervention by 60%. A titanium aerospace part with deep holes and external threads maintained consistent surface finish (Ra 0.8μm) across 10,000 units.
- In-process gaging: Laser probes measure critical dimensions (diameters, lengths) during machining, making real-time tool offsets to maintain ±0.002mm tolerance. A production run of 50,000 aluminum shafts achieved 99.98% conformance to 12mm diameter specification.
4. Dimensional Stability & Quality Control
- Thermal error compensation: Sensors monitor machine temperature fluctuations (±0.5℃), applying real-time offsets to maintain ±0.003mm tolerance for large turn-mill parts (300mm+ length). A 400mm steel linear actuator shaft maintained 0.01mm straightness across the entire length.
- 3D scanning inspection: Captures full part geometry of complex turn-mill components, comparing to CAD models with color-coded deviation maps (≤0.005mm acceptable). A hybrid aluminum/steel medical device component achieved 99.9% geometric conformity, ensuring proper function in surgical applications.
- Functional testing: Verifies integrated features work together—e.g., a turn-mill gearshaft underwent 1 million rotation cycles with meshing gears, showing no abnormal wear due to precise feature alignment.
Material Expertise: Matching Materials to Turn-Mill Requirements
Material
|
Key Properties
|
Application
|
Advantages
|
Alloy Steel (4140, 4340)
|
800-1200MPa tensile strength, good chip control
|
Hydraulic components, gear shafts
|
Maintains sharp edges in milling; achieves Ra 0.05μm surface finish in turning.
|
Titanium Alloy (Ti-6Al-4V)
|
895MPa tensile strength, high strength-to-weight ratio
|
Aerospace turn-mill parts, medical instruments
|
45% lighter than steel; suitable for 7-axis complex geometries.
|
Aluminum Alloy (6061-T6, 7075-T6)
|
310-572MPa tensile strength, excellent machinability
|
Automotive components, electronics
|
30% faster turn-mill cycle time than steel; ideal for high-volume production.
|
Stainless Steel (304, 316L)
|
515MPa tensile strength, corrosion resistance
|
Medical devices, marine components
|
Withstands 1,000+ hours salt spray; maintains precision in both turning and milling.
|
CNC Turn-Mill Parts Manufacturing Process
- Design & DFM for Turn-Mill Integration: Engineers analyze client 3D models (STEP/IGES) to optimize:
-
- Feature arrangement (placing milled features within live tooling reach)
-
- Wall thickness (≥0.8mm) to withstand both turning and milling forces
-
- Tool access (avoiding overhangs >5× diameter to prevent vibration)
- CAM programming: Develops synchronized toolpaths for:
-
- Main spindle turning (OD/ID features)
-
- Live tool milling (holes, flats, keyways)
-
- Sub-spindle operations (back-end features)
- Turn-mill machining:
-
- Roughing: High-speed turning (500m/min) and milling (1,500mm/min) to remove 90% of material
-
- Finishing: Precision turning (Ra 0.02μm) and milling (±0.002mm) with PCD/carbide tools
- Post-processing:
-
- Deburring (automated robotic cells for complex geometries)
-
- Heat treatment (e.g., carburizing for 4140 steel parts)
-
- Surface coating (anodizing, plating) per application requirements
- Quality validation:
-
- CMM inspection with 5-axis probing (±0.001mm)
-
- Functional testing (assembly fit, pressure/vibration resistance)
-
- Material certification (3.1B) and traceability documentation
CNC Turn-Mill Parts Application Fields
- Aerospace: Titanium engine shafts with integrated flanges (reduced part count by 4), 7075 aluminum actuator components (±0.003mm tolerance).
- Automotive: 4140 steel transmission parts (combined 3 components into 1), 6061 aluminum fuel injectors (with 8 milled features on a turned body).
- Medical: 316L stainless steel surgical tool shafts (with milled gripping features), titanium orthopedic implants (complex 3D contours + threads).
- Industrial automation: 304 stainless steel robotic arm joints (integrated bearings + drive features), 4140 steel linear motion shafts (threads + keyways).
Customization Capabilities: From Prototype to Mass Production
- Complex feature integration: Combines 5+ features (turning, milling, drilling, threading) into one part—e.g., a 7-axis aerospace bracket with rotational base, milled mounting lugs, and internal threads.
- Low-volume prototypes: 1-500 units in 3-5 days via 7-axis turn-mill centers, ideal for design validation (e.g., medical device prototypes with integrated features).
- High-volume production: 10,000-80,000+ units/month with automated loading systems—e.g., 50,000 aluminum automotive connectors with consistent ±0.003mm tolerance.
Common Processing Questions
- Q: How to maintain ±0.003mm tolerance on a 300mm-long turn-mill part?
- Q: What’s the maximum number of integrated features possible in one turn-mill cycle?
- Q: What’s the lead time for 10,000 turn-mill steel components with 15 features?
- Q: How does turn-mill machining reduce assembly costs?
-
- Fastener costs (screws, bolts)
-
- Assembly labor (30-50% reduction)
-
- Tolerance stack-up issues (90% reduction in fit problems)