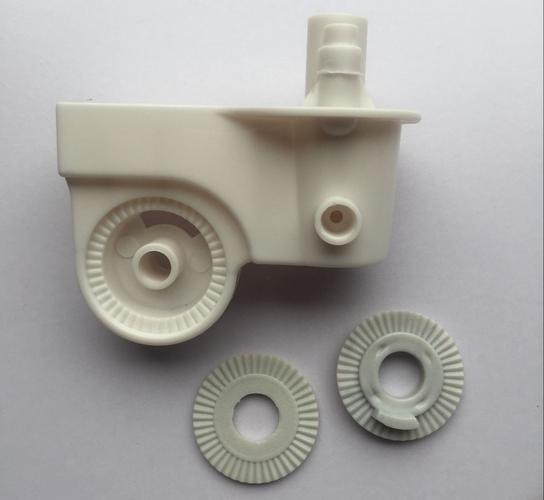
Core Processing Technologies: Engineering for Fan Performance
1. High-Precision Injection Molding
- Multi-cavity mold design: 4-32 cavity molds for fan blades/bases, achieving ±0.01mm dimensional tolerance. A 16-cavity ABS fan blade mold produces 10,000 units/day with uniform weight (±0.5g), ensuring balanced rotation and low vibration.
- Gas-assisted injection: For thick-walled parts (e.g., motor housings), this reduces warpage by 40% and cuts material usage by 15%. A PP fan base produced this way withstands 10kg load without deformation.
- In-mold decoration (IMD): Integrates logos/colors during molding, eliminating post-painting. A household fan control panel with IMD achieved scratch resistance (3H pencil test) and colorfastness (ΔE ≤1 after 1,000 hours UV test).
2. Mold Flow Analysis & Structural Optimization
- CAE simulation: Uses Moldflow to predict filling patterns, optimizing fan blade geometry for 10% higher airflow and 5dB lower noise. A 12-inch industrial fan blade redesign reduced turbulence via streamlined contours.
- Vibration analysis: FEA software ensures parts (e.g., motor housings) endure 5,000+ hours of 20-50Hz vibration without cracking, meeting IEC 60335 safety standards.
3. Surface Treatment & Functional Coating
- Anti-UV coating: Applied to outdoor fan grilles (PC material), resisting 3,000 hours of sunlight without yellowing or brittleness.
- Anti-static treatment: For industrial fans, reduces dust buildup on blades by 60% via 10^6-10^9Ω surface resistance, maintaining airflow efficiency.
- Texture finishing: Mold texturing (Ra 0.8-1.6μm) on bases and panels enhances grip and hides scratches, ideal for commercial fans in high-traffic areas.
4. Quality Testing for Fan Safety & Efficiency
- Dimensional inspection: CMM checks critical dimensions—blade thickness (±0.02mm), grille hole spacing (±0.1mm)—ensuring no airflow blockage or safety hazards.
- Balancing test: Fan blades undergo dynamic balancing (≤0.5g·mm imbalance), eliminating vibration and noise at 1,200rpm.
- Mechanical testing:
-
- Impact resistance (10J for grilles, no cracks)
-
- Heat resistance (80℃ for 1,000 hours, no deformation)
-
- Chemical resistance (cleaner/UV exposure for 24 hours)
Material Expertise: Matching Plastics to Fan Components
Material
|
Key Properties
|
Application
|
Advantages
|
ABS
|
High impact (20kJ/m²), easy coloring
|
Fan blades, control panels
|
Balances strength and aesthetics; ideal for household fans.
|
PP
|
Heat resistance (100℃), low cost
|
Bases, motor housings
|
Chemical resistance; suitable for humid environments (bathroom fans).
|
PC
|
Transparency (89% light transmittance), UV resistance
|
Grilles, light-integrated fans
|
Shatterproof; meets safety standards for child-accessible areas.
|
PBT + 30% GF
|
High rigidity, heat resistance (150℃)
|
Motor brackets, internal components
|
Withstands motor heat; reduces noise via vibration damping.
|
Electric Fan Plastic Parts Machining Technologies
- Precision mold making: CNC EDM (±0.002mm) crafts complex blade contours, ensuring aerodynamic efficiency. A 3D-printed prototype mold for a new fan blade design cut development time by 40%.
- Automated injection cells: Robotic part removal and in-line weighing (±0.1g) maintain consistency, with 99.8% first-pass yield for mass production.
- Ultrasonic welding: Bonds multi-piece parts (e.g., grille frames) with 0.1mm seam accuracy, replacing screws to reduce assembly time by 30%.
Custom Electric Fan Parts Manufacturing Process
- Design & DFM: Engineers optimize client drawings (STEP/IGS) for moldability—e.g., adding draft angles to fan blades for easy demolding.
- Mold fabrication: CNC machining creates multi-cavity molds, with Moldflow validation to prevent defects like air traps.
- Injection molding: Automated machines produce parts with precise temperature/pressure control (e.g., 220℃ for ABS, 180℃ for PP).
- Post-processing: Surface coating, ultrasonic welding, or assembly (e.g., attaching blades to motor hubs).
- Quality validation: CMM inspection, balancing tests, and safety compliance checks (IEC 60335) ensure performance.
Custom Fan Plastic Parts Application Fields
- Household fans: ABS blades (12-16 inches), PP bases, IMD control panels for table/standing fans.
- Industrial fans: PC grilles (anti-UV), PBT motor housings for high-temperature environments (factories, warehouses).
- Commercial fans: Anti-static blades, stainless steel-reinforced bases for offices, shopping malls.
- Specialty fans: Waterproof PP parts for bathroom fans, flame-retardant ABS for kitchen exhaust fans.
Customization Capabilities: From Design to Delivery
- Design collaboration: Engineers refine blade curvature for maximum airflow (CFD-tested) or adjust base weight for stability (≥1.5x fan weight).
- Material flexibility: Choose between standard (ABS/PP) or premium (flame-retardant PC, anti-microbial PP) materials.
- Production scale: 100-500,000+ units/month—prototypes in 5 days, mass production in 2-3 weeks. A European client received 10,000 custom fan grilles in 15 days.
Common Processing Questions
- Q: How to reduce fan noise caused by plastic parts?
- Q: Can parts withstand high humidity (e.g., bathroom fans)?
- Q: What’s the lead time for a new fan blade mold (10k units)?
- Q: How to ensure grille safety for children?
Why Choose Goldcattle?
- Expertise: 26 years in fan parts, with 50+ custom designs meeting IEC/UL standards.
- Quality: 100% balancing tests and CMM inspection; 5-year warranty on material defects.
- Efficiency: Multi-cavity molds and automation cut costs by 20% vs. small-scale manufacturers.
- Sustainability: Recyclable materials (PCR PP/ABS) and energy-efficient machines reduce carbon footprint by 30%.