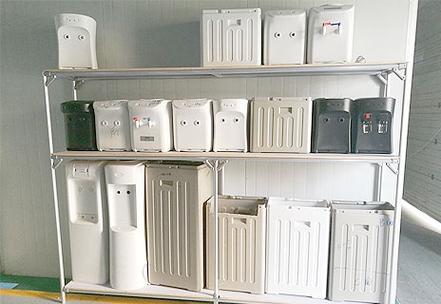
I. Core Material Properties and Application Advantages
(A) Comparison of Mainstream Material Properties
Material Type
|
Density (g/cm³)
|
Temperature Range (°C)
|
Core Advantages
|
Typical Certifications
|
Acrylonitrile Butadiene Styrene (ABS)
|
1.03–1.07
|
-20 to 80
|
High strength, high toughness, easy molding
|
UL94 V-0 Flame Retardant Certification
|
Polycarbonate (PC)
|
1.20–1.22
|
-40 to 130
|
High light transmittance, impact resistance, dimensional stability
|
UL746C Material Certification
|
Polyphenylene Oxide (PPO)
|
1.06–1.07
|
-40 to 155
|
Excellent insulation, chemical corrosion resistance
|
UL94 V-1 Flame Retardant Certification
|
Polybutylene Terephthalate (PBT)
|
1.31–1.53
|
-40 to 150
|
Low hygroscopicity, high wear resistance, arc resistance
|
IEC 60243 Dielectric Strength Certification
|
Nylon (PA)
|
1.12–1.15
|
-40 to 180
|
Self-lubrication, fatigue resistance, high temperature resistance
|
ISO 1873 Mechanical Property Certification
|
(B) Driving Forces of Customization Core Requirements
- Electrical Safety:
-
- Insulation resistance ≥ 10¹²Ω (test voltage 500V), dielectric strength ≥ 20kV/mm.
-
- Flame retardancy grade must reach UL94 V-0 (1.6mm thickness) or UL94 5VA (strict industrial standard).
- Environmental Adaptability:
-
- Temperature resistance: Home appliance casings must pass the -20°C ~ 70°C thermal cycle test (no cracking after 50 cycles).
-
- Weather resistance: Outdoor electrical parts need UV aging resistance (color difference ΔE ≤ 3 after QUV-A 1000 hours irradiation).
- Functional Integration:
-
- Snap-fit structures should withstand a pulling force of ≥ 50N (no failure after 1000 opening and closing tests).
-
- Heat dissipation components with surface roughness Ra ≤ 1.6μm to ensure heat transfer efficiency.
II. Analysis of Four Core Processing Technologies
(A) Injection Molding: High-Precision Structural Part Processing
- Technical Advantages:
-
- Dimension accuracy ±0.05mm, supporting insert molding (positioning accuracy of metal inserts ±0.1mm).
-
- Multi-cavity molds (64 – 128 cavities per mold), production efficiency of 3000 – 8000 pieces per hour, suitable for 5 – 200g parts.
- Process Parameters:
-
- Injection pressure 120 – 180MPa, mold temperature 60 – 100°C, cooling time 12 – 25 seconds.
-
- Shrinkage control: 0.4% – 0.7% for ABS, 1.2% – 1.8% for PBT, ensuring assembly tolerance ≤ 0.03mm.
(B) Two-Color Injection Molding: Integration of Function and Appearance
Process Type
|
Typical Application Scenarios
|
Technical Advantages
|
Two-Color Co-injection
|
Buttons of smart devices, switch panels
|
One-step molding of parts with different colors/materials, eliminating secondary assembly
|
Overmolding (Soft-Hard Combination)
|
Handle grips, shock-absorbing pads
|
Composite of soft rubber (TPU) and hard plastic (PC) to enhance ergonomic experience
|
- Technical Highlights:
-
- Bonding strength at the interface of two-color materials ≥ 15MPa, passing 1000 bending tests without delamination.
-
- Multi-component injection molding machines support simultaneous molding of 4 materials to meet complex functional requirements.
(C) 3D Printing: Rapid Prototyping and Small-Batch Customization
- Process Advantages:
-
- Direct manufacturing of hollow heat dissipation structures and special-shaped snap-fits, with a minimum detail size of 0.3mm.
-
- Nylon 12CF (carbon fiber reinforced) material with a strength of 180MPa, suitable for high-strength prototypes.
- Application Scenarios:
-
- Rapid verification of structural designs during new product R&D (samples delivered in 3 days).
-
- Customized parts for small batches (order quantity ≤ 500 pieces), shortening the delivery cycle by 60%.
(D) In-Mold Decoration (IMD): Integration of Appearance and Function
- Technical Features:
-
- Integration of film printing, molding, and decoration within the mold, with surface hardness ≥ 3H.
-
- Supports texture designs (brushed, leather patterns) and anti-scratch coatings (withstand 1000 friction cycles without scratches).
- Typical Applications:
-
- High-end home appliance panels (reducing fingerprint residue by 80%).
-
- Smart device casings (electromagnetic shielding efficiency ≥ 50dB).
III. Full-Process Customization Solutions
(A) Design and Material Engineering
- Multi-Dimensional Design Support:
-
- Structural Optimization: Analyze the position of weld lines through Moldflow simulation to avoid electrical weak points.
-
- Functional Customization:
-
-
- Heat dissipation grilles: Optimize the opening ratio to 40%, reducing air resistance by 25% (verified by CFD fluid simulation).
-
-
-
- Waterproof components: Adopt IP67 – level sealing structures, passing the 2kPa pressure test without leakage.
-
- Precise Material Selection:
-
- Casings of small home appliances: Select UL94 V-0 grade ABS, which does not ignite during the glow wire test (850°C).
-
- Components of high-voltage electrical appliances: Use PPO material with a volume resistivity ≥ 10¹⁶Ω·cm, meeting the GB/T 1410 insulation standard.
- Pre-Processing Technology:
-
- Raw material drying: Control the moisture content of PA material ≤ 0.1% to avoid molding bubble defects.
-
- Modification treatment: Add antistatic agents (surface resistance ≤ 10⁹Ω) for 3C product parts to prevent static adsorption.
(B) Production and Quality Control
- Flexible Manufacturing Capability:
-
- Rapid Prototyping: 3D printed samples delivered in 48 hours, aluminum mold development cycle of 10 – 15 days (steel mold 30 – 45 days).
-
- Mass Production:
-
-
- High-speed injection lines: Equipped with Fanuc robots, with a daily production capacity of 50,000 pieces per machine (64-cavity mold).
-
-
-
- Automated production lines: Achieve fully unmanned processes from injection molding, assembly to inspection, with a yield rate ≥ 99.2%.
-
- Comprehensive Testing System:
-
- Electrical Properties:
-
-
- Dielectric strength test: Withstand 25kV/mm voltage for 1 minute without breakdown.
-
-
-
- Insulation resistance: Tested at 500V DC, with a resistance value ≥ 10¹³Ω.
-
-
- Mechanical Properties:
-
-
- Impact test: Withstand a 2J energy impact without cracking at -20°C (ISO 179 standard).
-
-
-
- Fatigue test: Button life ≥ 100,000 presses, with a stroke change ≤ 0.1mm.
-
-
- Certification Support: Provide international certification test reports such as UL, CE, and RoHS to ensure compliance with global market regulations.
IV. Multi-Field Application Scenarios
(A) Home Appliances
- Refrigerator drawers: Made of PBT + 30%GF material, resistant to low temperatures (-30°C) and impact, with a load-bearing capacity of 15kg without deformation.
- Air conditioner casings: PC/ABS alloy material, with a UV resistance level of 4, without fading after 3 years of outdoor exposure (GB/T 16422.3).
(B) 3C Products
- Mobile phone middle frames: Carbon fiber reinforced nylon material, with a bending strength of 240MPa, and a drop test (1.5m) pass rate ≥ 98%.
- Laptop heat dissipation grilles: IMD-processed parts with a 55% hollow rate, improving heat dissipation efficiency by 18%, and surface hardness of 4H.
(C) Industrial Electrical Equipment
- Insulating parts of high-voltage switches: PPO material encapsulated with epoxy resin, with an arc resistance ≥ 180 seconds (ASTM D495 test).
- Servo motor protective covers: UL94 5VA grade PA66, with a Glow Wire Flammability Index (GWFI) of 960°C.
(D) Smart Home
- Smart door lock casings: Two-color injection molded PC + TPU, with a fingerprint recognition area wear resistance level of 5 (ISO 1518-2 standard).
- Sensor protective covers: Waterproof IP68 grade PBT, without corrosion after 96 hours of salt spray test.
V. Technology Selection Guide
Requirement Type
|
Preferred Technology
|
Weight Range
|
Core Indicators
|
Delivery Cycle
|
R&D Verification and Small Batches
|
3D Printing + Injection Molding
|
1 – 200g
|
Rapid iteration, complex structures
|
Prototype in 3 days, batch in 15 days
|
Medium-Large Batch Standardization
|
Injection Molding + IMD
|
5 – 500g
|
High precision, decorative appearance
|
Prototype in 7 days, batch in 20 days
|
Functionally Composite Parts
|
Two-Color Injection Molding
|
10 – 300g
|
Multi-material integration, one-step molding
|
Prototype in 10 days, batch in 25 days
|