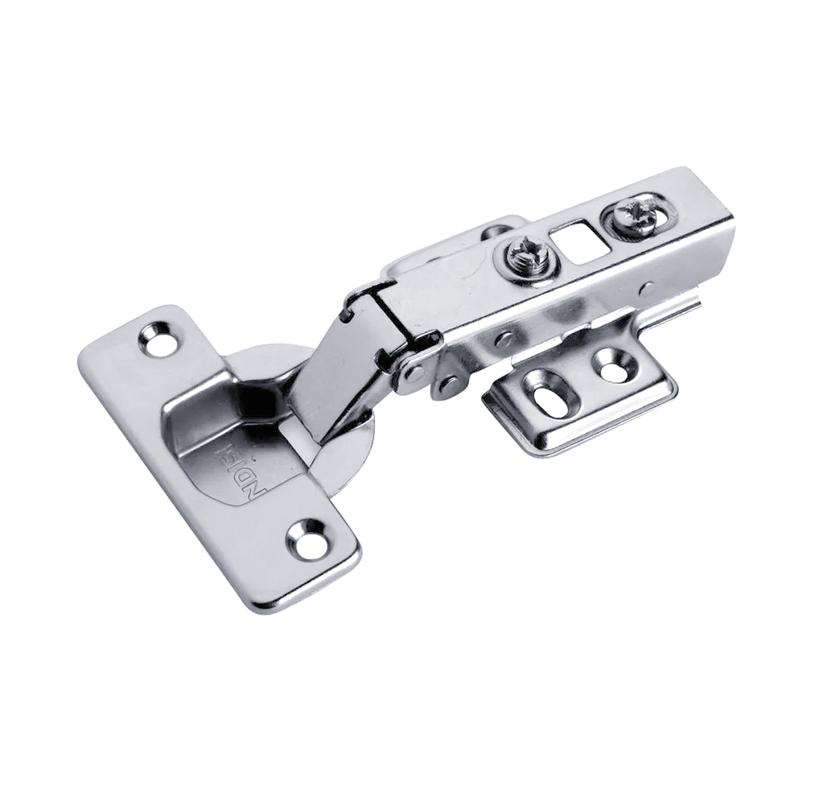
I. Core Material Propertiesand Application Advantages
(A) Comparison of Mainstream Material Properties
Material Type
|
Density (g/cm³)
|
Tensile Strength (MPa)
|
Hardness (HV)
|
Salt Spray Resistance (h)
|
Core Advantages
|
Typical Certifications
|
Stainless Steel (304)
|
7.93
|
520–720
|
130–180
|
≥1000
|
High strength, corrosion resistance, rust prevention
|
ISO 316L Food-Grade Certification
|
Aluminum Alloy (6061)
|
2.70
|
205
|
95
|
≥500
|
Lightweight, easy to form, good weather resistance
|
GB/T 3190 Alloy Standard
|
Cold-Rolled Steel (SPCC)
|
7.85
|
375–500
|
110–130
|
≥200 (galvanized)
|
Low cost, easy to process, suitable for spraying
|
ASTM A1011 Standard Certification
|
Brass (H65)
|
8.40
|
390
|
100
|
≥800 (nickel-plated)
|
Good wear resistance, excellent electrical/thermal conductivity
|
EN 124 Copper Product Certification
|
Zinc Alloy (ADC12)
|
6.60
|
230
|
80
|
≥720 (chrome-plated)
|
Good die-casting performance, diverse shapes
|
RoHS Environmental Certification
|
(B) Driving Forces of Customization Requirements
1. Mechanical Performance Requirements
- Load-Bearing Capacity: Static load per hinge ≥50kg (furniture hinges), dynamic load ≥30kg (100,000 cycle opening/closing test).
- Service Life: ≥50,000 cycles without jamming under standard test conditions (20kg load, QB/T 1254 standard).
- Torque Stability: Torque fluctuation of damping hinges ≤±5% (20–50N·m adjustment range).
2. Environmental Adaptability
- Corrosion Resistance: Neutral salt spray test ≥48 hours without rust (outdoor hinges ≥1000 hours).
- Temperature Resistance: Opening/closing torque change ≤10% in -40℃~80℃ (automotive hinge requirement).
- Surface Hardness: Plating layer hardness ≥200HV, scratch resistance passing 3H pencil test without marks.
3. Installation and Precision Requirements
- Hole Position Accuracy: Mounting hole pitch tolerance ±0.2mm, compatible with standard cabinets (e.g., 32mm system holes).
- Opening Angle: Supports 0–180° positioning with ±1° accuracy (hydraulic hinges).
II. Analysis of Four Core Processing Technologies
(A) Die Casting: High-Precision Processing for Complex Structures
- Technical Advantages
-
- Enables one-step forming of complex components with damping structures and hidden mounting plates, dimensional accuracy ±0.1mm.
-
- Mold life ≥100,000 cycles (zinc alloy), suitable for 5–200g medium-small parts with production efficiency 300–800 pieces/hour.
- Process Parameters
-
- Die casting pressure 50–100MPa, mold temperature 180–220℃ (zinc alloy), cooling time 10–30 seconds.
-
- Demolding draft angle 3°–5° to ensure thin-wall forming (wall thickness ≥1.5mm).
(B) Stamping: High-Efficiency Production for Standardized Parts
Process Type
|
Typical Application Scenarios
|
Technical Highlights
|
Progressive Die Stamping
|
Hinge plates, connecting panels
|
Multi-process continuous forming, material utilization ≥90%
|
Precision Stamping
|
Micro hinges (≤10g)
|
Dimensional accuracy ±0.05mm, burr height ≤0.02mm
|
- Technical Advantages
-
- Automated production line realizes full-process processing from coil to finished product, daily capacity up to 50,000 pieces (8-cavity mold).
-
- Bending angle accuracy ±0.5° to ensure uniform force during opening/closing (e.g., 110° self-closing hinges).
(C) Surface Treatment Technologies
- Functional Coatings
-
- Dacromet Coating: Thickness 8–12μm, salt spray resistance ≥1000 hours, chromium-free environmental protection (for outdoor hinges).
-
- Electrophoretic Painting: Film thickness 15–25μm, adhesion ≥5B grade, surface roughness Ra≤0.4μm (furniture hinges).
- Decorative Treatments
-
- Vacuum Titanium Plating: Titanium layer thickness 3–5μm, hardness ≥200HV, achieving high-end finishes like rose gold and gunmetal.
-
- Powder Coating: Coating thickness 60–100μm, weather resistance grade 4 (QUV aging test 2000 hours, color difference ΔE≤3).
(D) CNC Precision Machining: Customization for High-End Hinges
- Process Advantages
-
- Machining accuracy ±0.02mm, suitable for aerospace-grade hinges (e.g., aircraft door hinges) with high-precision holes and curves.
-
- Supports difficult-to-machine materials like titanium alloy and stainless steel, achieving 0.1mm-level thin walls (e.g., hidden hinges for smart furniture).
- Key Parameters
-
- Spindle speed 8000–15000rpm, feed rate 500–2000mm/min, surface roughness Ra≤0.8μm.
III. Full-Process Customization Solutions
(A) Design and Material Engineering
1. Multi-Dimensional Design Support
- Structural Optimization
-
- ANSYS simulation analyzes hinge pin stress, optimizing fillet radius R≥2mm to reduce stress concentration by 30%.
-
- Damping hinges use vortex oil path design, controlling opening/closing buffer time at 0.8–1.2 seconds (compliant with QB/T 2697 standard).
- Functional Customization
-
- Self-Closing Hinges: Dual spring clip structure enables disassembly in ≤5 seconds, adapting to fast installation needs.
-
- Smart Hinges: Integrated angle sensors (accuracy ±0.5°) support IoT device status monitoring.
- Installation Adaptation
-
- 3D Adjustable Hinges: Adjustment range of front-back ±2mm, up-down ±3mm, left-right ±1mm, compatible with non-standard cabinets.
2. Precise Material Selection
- Furniture Hinges: Zinc alloy/cold-rolled steel (cost-effective), surface electroplating for daily rust resistance.
- Outdoor Door/Window Hinges: 304 stainless steel + Dacromet coating, salt spray resistance ≥1000 hours, suitable for coastal high-humidity environments.
- Automotive Hinges: 6061 aluminum alloy + anodizing, 40% lighter than steel hinges, temperature resistance -40℃~80℃.
3. Pre-Processing Technology
- Raw Material Leveling: Plate flatness error ≤0.1mm to ensure stamping accuracy.
- Mold Polishing: Molding surface roughness Ra≤0.4μm to reduce demolding resistance and surface defects.
(B) Production and Quality Control
1. Flexible Manufacturing Capability
- Rapid Prototyping
-
- 3D printed samples delivered in 48 hours, simple mold development cycle 10–15 days (steel mold 30–45 days).
-
- Supports small-batch customization (MOQ 500 pieces) for sample testing and non-standard requirements.
- Mass Production
-
- Intelligent production lines: ABB robots handle assembly and inspection, daily capacity 10,000 pieces for complex hinges.
-
- Error-proofing system: Visual inspection of hole position 偏差 (deviation), automatic rejection of non-conforming products (accuracy ≥99.8%).
2. Comprehensive Inspection System
- Mechanical Performance
-
- Load Test: 1.5x rated load for 24 hours, deformation ≤0.5mm (GB/T 12606 standard).
-
- Fatigue Test: 50,000 cycle opening/closing simulation, wear amount ≤0.3mm (QB/T 3874 standard).
- Environmental Performance
-
- Thermal Cycling: -40℃~80℃ cycling 50 times, torque change ≤15% (automotive industry standard).
-
- Chemical Resistance: 5% hydrochloric acid immersion for 24 hours, no surface corrosion (additional requirement for outdoor hinges).
- Precision Inspection
-
- CMM Measurement: Key dimension accuracy ±0.03mm, angle deviation ±0.5° (precision hinge standard).
- Certification Support: Provides ISO 9001, IATF 16949, BS EN 1935, and other certification reports.
IV. Multi-Scenario Application Solutions
(A) Furniture Manufacturing
- Cabinet Hinges
-
- Cold-rolled steel substrate + galvanized treatment, load-bearing 30kg, standard damping buffer function, opening/closing noise ≤30dB.
-
- 3D adjustable design adapts to 16–22mm panels, 32mm standard hole pitch system, occupying over 70% market share.
- Wardrobe Hinges
-
- Hidden zinc alloy hinges, door panel coverage 2mm, supports 180° full opening, electrophoretic surface treatment to prevent clothing scratches.
(B) Construction and Doors/Windows
- Curtain Wall Hinges
-
- 316 stainless steel, salt spray test ≥1500 hours, load-bearing 80kg, adapts to 10–15mm glass curtain walls.
-
- Friction positioning design supports arbitrary angle hovering (0–90°), compliant with GB/T 29034 standard.
- Fire Door Hinges
-
- Cast steel + high-temperature coating (300℃ fire resistance for 1 hour), GA 93 fire certification, load-bearing ≥100kg.
(C) Automotive and Transportation
- Vehicle Door Hinges
-
- 6061-T6 aluminum alloy + lightweight design, single hinge weight ≤200g, vibration resistance (10–2000Hz, 5g) with no looseness.
-
- Self-lubricating bushing design, service life ≥10 years (150,000 cycles), compliant with ISO 16750-3 standard.
- Trunk Hinges
-
- Stainless steel + memory spring structure, supports damping buffer and automatic closing, opening force change ≤15% at low temperature (-40℃).
(D) Industrial Equipment
- Heavy Machinery Hinges
-
- 45# steel quenched treatment, tensile strength ≥600MPa, load-bearing 500kg, adapts to high-temperature metallurgical environments (150℃ resistance).
-
- Dustproof design: Sealing ring protection grade IP65, preventing dust from entering hinge moving parts.
- Medical Device Hinges
-
- 304 stainless steel + mirror polishing (Ra≤0.2μm), ISO 13485 certified, suitable for cleanroom equipment (e.g., medical cabinets).
V. Technology Selection Guide
Requirement Type
|
Preferred Technology Combination
|
Material Selection
|
Core Indicators
|
Delivery Cycle
|
High-Load Industrial Hinges
|
Die Casting + Stainless Steel
|
304 Stainless Steel
|
Load-bearing ≥200kg, temperature resistance 150℃
|
Prototype in 7 days, mass production in 30 days
|
Lightweight Automotive Hinges
|
Stamping + Aluminum Alloy
|
6061 Aluminum Alloy
|
40% weight reduction, vibration resistance 5g
|
Prototype in 5 days, mass production in 25 days
|
Large-Scale Furniture Hinges
|
Progressive Die Stamping + Cold-Rolled Steel
|
SPCC Cold-Rolled Steel
|
Cost ≤$0.20/piece, service life 50,000 cycles
|
Prototype in 5 days, mass production in 20 days
|
High-End Decorative Hinges
|
CNC Machining + Brass
|
H65 Brass
|
Surface hardness ≥200HV, salt spray 800h
|
Prototype in 7 days, mass production in 35 days
|