As industrial manufacturing shifts toward higher precision, lightweight designs, and intelligence, custom industrial plastic parts have become core components in machinery, electronics, automotive, and energy sectors, thanks to their material performance, processing flexibility, and cost-effectiveness. This article systematically analyzes the technical logic and industrial value of industrial plastic parts, covering material selection, processing technology, customization processes, and quality control, providing professional guidance for industrial enterprises.
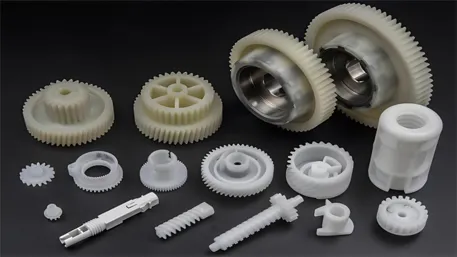
Materials for custom industrial plastic parts must balance mechanical strength, temperature resistance, chemical resistance, and processability. Key properties and typical applications of common engineering plastics are as follows:
Material |
Tensile Strength (MPa) |
Heat Deflection Temperature (℃) |
Chemical Resistance |
Typical Applications |
Acetal (POM) |
60-70 |
110-136 (0.45MPa) |
Resistant to organic solvents, high wear resistance |
Precision gears, bearings, valve components |
Nylon (PA) |
70-150 (glass-filled) |
180-220 (GF-PA) |
Oil-resistant, fatigue-resistant |
Automotive intake manifolds, industrial transmission parts |
Polyphenylene Sulfide (PPS) |
65-85 |
260 (1.82MPa) |
Resistant to strong acids/alkalis, high temperature |
Chemical pump impellers, electronic connectors |
Polyetheretherketone (PEEK) |
90-100 |
343 (melting point) |
Radiation-resistant, biocompatible |
Aerospace structural parts, medical implants |
Carbon Fiber Reinforced Nylon (CFRP) |
180-220 |
150 |
High strength, low density |
Drone frames, automotive lightweight components |
Through mechanical property testing (e.g., impact strength, fatigue life) and environmental adaptability verification (e.g., high/low-temperature cycles, salt spray corrosion), parts are ensured to operate stably in temperatures ranging from -60℃ to 300℃ and harsh chemical environments.
Process |
Precision (mm) |
Daily Capacity (pcs) |
Suitable Scenarios |
Typical Parts |
Injection Molding |
±0.05 |
5,000-50,000 |
Mass production of complex structures |
Gears, connectors, housings |
CNC Machining |
±0.01 |
50-500 |
High-precision small batches |
Precision bushings, optical brackets |
3D Printing (SLS) |
±0.1 |
10-50 |
Rapid prototyping, custom irregular parts |
Medical device components, mold cores |
Extrusion |
±0.2 |
10,000+ |
Continuous production of profiles/tubing |
Industrial guides, seals |
- Mold Optimization Technology:
- Mold flow analysis (Moldflow) predicts melt flow, controlling sink marks below 0.3% and warpage ≤0.08 mm/m.
- Conformal cooling mold design reduces cooling time by 30%, increasing production efficiency by 25%.
- Surface Treatment Processes:
- Wear-resistant coatings (e.g., molybdenum disulfide): Friction coefficient reduced to 0.05, doubling gear life.
- Conductive modification: Carbon nanotube addition lowers surface resistance ≤10⁶ Ω, meeting ESD requirements for electronic components.
- Technical Parameter Confirmation: Clarify part usage (e.g., transmission/sealing/insulation), operating environment (temperature/humidity/medium), and precision requirements (e.g., IT7 tolerance, surface roughness Ra≤0.4 μm).
- Cost Evaluation: Provide material proposals (e.g., POM parts ¥8/piece, PEEK parts ¥150/piece) and process recommendations (injection molding for mass production, CNC for small batches) within 3 days.
- 3D Modeling and Simulation: Use UG/NX for structural design, optimizing stress distribution via finite element analysis (FEA) to ensure gear root stress ≤50 MPa.
- Sample Production:
- Rapid prototyping (3D printing): First sample delivered in 3 days for assembly verification.
- Silicone mold small batch (50 pieces minimum): Cost 40% lower than steel molds, suitable for functional testing.
- Mold Materials:
- Precision molds: S136 tool steel (HRC52 hardness), lifespan ≥500,000 cycles, core precision ±0.005 mm.
- Quick molds: Aluminum alloy for fast small-batch delivery (development cycle reduced by 50%).
- Smart Machining: 5-axis CNC machining for mold cavities, surface roughness Ra≤0.2 μm, ensuring complex surface forming precision.
- Production Parameters:
- Injection molding: PPS material at 300±5℃, holding pressure 80 MPa, cooling time 20 seconds, daily capacity 3,000 pieces per mold.
- CNC machining: Precision controlled at ±0.01 mm, processing time reduced by 20% via tool path optimization.
- Quality Standards:
- Dimensional inspection: Full-size scanning via CMM, critical dimensions CPK≥1.67.
- Reliability testing: Gears undergo 10⁶ fatigue cycles, bearings pass 1,000-hour wear test (wear ≤0.01 mm).
- Packaging Solution: Anti-static pearl cotton + wooden crates, compliant with ISTA 2A transportation standards, damage rate ≤0.1%.
- After-Sales Support: 7×24-hour technical service, 48-hour quality issue response, 1-year warranty (under normal use).
- Transmission Systems: POM injection-molded gears reduce weight by 40% and noise by 15 dB, suitable for high-precision drives.
- Sealing Components: Silicone rubber seals pass IP68 water resistance test, leak-free under 20 MPa pressure for hydraulic systems.
- Connectors: LCP injection-molded high-frequency connectors with dielectric constant Dk=2.9, signal loss ≤3 dB for 5G equipment.
- Insulators: Epoxy compression-molded insulators with voltage resistance ≥10 kV for high-voltage electrical devices.
- Lightweight Components: CFRP injection-molded car brackets reduce weight by 50% and increase strength by 30%, adapting to new energy vehicle lightweight designs.
- Engine Parts: PA66-GF30 injection-molded intake manifolds resist 150℃ heat and engine oil, reducing costs by 40% compared to aluminum parts.
- Corrosion-Resistant Parts: PPS injection-molded valves resist 98% sulfuric acid and temperatures ≤200℃, reducing weight by 60% versus stainless steel.
- Photovoltaic Components: PC injection-molded PV junction boxes withstand 1,000 hours of UV aging, insulation resistance ≥10¹² Ω for safe power systems.
Smart Manufacturing Upgrades
- AI algorithms optimize injection parameters, reducing trial molds by 60% and increasing yield to ≥98%.
- IoT real-time equipment monitoring reduces downtime by 30% via predictive maintenance.
Lightweight and Sustainable Materials
- Bio-based PEEK (30% plant-derived content): 25% lower carbon emissions, suitable for medical and aerospace applications.
- Recycled engineering plastics (rPA): Recycling rate ≥50%, compliant with EU CE circular economy standards.
Functional Integration Innovations
- Multi-material composite molding: Embedding metal inserts during injection for integrated conductive and insulating functions.
- Micro-nano structure processing: Laser etching creates micrometer-scale anti-slip textures, increasing friction coefficient by 20%.
Q1: What is the minimum order quantity for custom industrial plastic parts?
A: The minimum order for regular injection molding is 5,000 pieces. Small batches (100-1,000 pieces) can use 3D printing or silicone molds, with unit costs 30%-50% higher than mass production.
Q2: How to ensure part performance in high-temperature environments?
A: High-temperature-resistant materials (e.g., PPS, PEEK) are selected, and HDT testing ensures dimensional change ≤0.5% at target temperatures.
Q3: What dimensional accuracy can precision parts achieve?
A: CNC machining achieves ±0.01 mm precision, while injection molding controls critical dimensions within ±0.05 mm, meeting IT7 precision requirements.
Q4: Do you provide material certifications and test reports?
A: We offer ISO 9001 quality certification, ROHS/REACH compliance reports, and third-party testing for mechanical properties and environmental adaptability.
“For a 20,000-piece order of high-precision POM gears, the team completed design to delivery in just 35 days. Parts met ±0.03 mm dimensional tolerance, with no fractures after 10⁶ fatigue cycles, and wear resistance 20% better than expected. Proactive mold cooling optimization shortened the production cycle by 15%, with a defect rate as low as 0.05%. Their professional material selection and process control provided us with reliable core components for mechanical drives.” ——Technical Director of an Industrial Equipment Manufacturer
Whether you need high-wear mechanical parts, high-temperature chemical components, or lightweight automotive parts, we offer:
- Free Technical Consultation: Senior engineers recommend optimal materials and processes based on your application, with detailed performance comparison charts.
- End-to-End Quality Control: Rigorous testing at every stage ensures parts meet ISO 2768 precision tolerances and industry standards.
- Flexible Services: Support small-batch prototyping, urgent orders, with the fastest 72-hour sample delivery and 45-day mass production turnaround.
Click below to share your industrial plastic part requirements and let every component become a reliable cornerstone of efficient manufacturing!