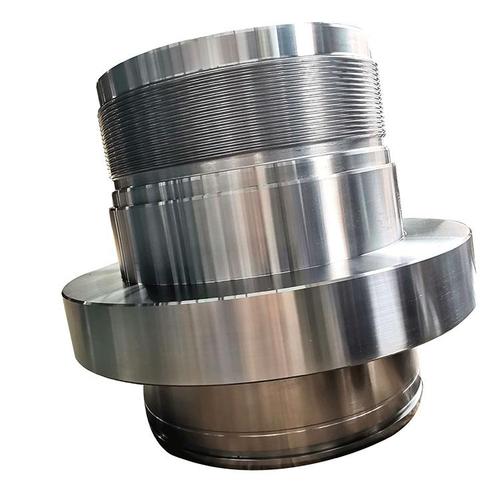
Core Processing Technologies: Engineering for Machinery Durability
1. High-Precision CNC Machining
- 5-axis CNC milling: Shapes complex components (e.g., hydraulic manifolds with multi-axis ports) with ±0.005mm accuracy, ensuring fluid flow efficiency (pressure loss ≤5%). A 6-inch hydraulic manifold for industrial presses achieved 0.01mm port alignment, eliminating leaks.
- CNC turning with live tooling: Produces shafts, bushings, and collars with tight concentricity (≤0.002mm), critical for high-speed rotating parts. A 30mm drive shaft for conveyor systems maintained balance at 3,000 RPM, reducing vibration by 60%.
- Wire EDM cutting: Creates precision gears and keyways (tolerance ±0.003mm) in hardened steel, ensuring mesh accuracy (backlash ≤0.05mm) for gearboxes.
2. Heat Treatment & Material Strengthening
- Carburizing & quenching: Hardens gear teeth and bearing surfaces to 58-62 HRC, with a ductile core (30-35 HRC) for impact resistance. A 40-tooth industrial gear treated this way endured 10 million cycles without wear.
- Nitriding: Enhances surface hardness of hydraulic components (e.g., valve spools) to 1,000HV, reducing friction and extending service life by 3x in oil-rich environments.
- Stress relief annealing: Eliminates internal stresses in large parts (e.g., 1m-long conveyor frames), preventing warpage under continuous load (≤0.02mm/m deformation).
3. Surface Coating & Corrosion Resistance
- Hard chrome plating: Applied to hydraulic rods and piston shafts, providing 0.05-0.1mm thick wear layers (65 HRC) and corrosion resistance (500 hours salt spray).
- Powder coating: For structural parts (e.g., machine frames), offers 80-120μm thick layers with UV resistance, ideal for outdoor agricultural machinery.
- PTFE coating: Reduces friction on sliding components (e.g., linear guide rails) by 40%, ensuring smooth operation in food processing equipment (compliant with FDA 21 CFR 177.1550).
4. Quality Testing for Industrial Reliability
- Dimensional inspection: CMMs verify critical features—bearing seat tolerance (H7), gear pitch (±0.01mm), and shaft straightness (≤0.05mm/m).
- Mechanical testing: Tensile strength (≥600MPa for structural parts), impact resistance (-40℃, ≥27J), and fatigue testing (10 million cycles at 80% load) ensure durability.
- Pressure testing: Hydraulic manifolds and valves undergo 3x working pressure tests (e.g., 300bar for industrial hydraulics) with zero leakage.
Material Expertise: Matching Metals to Machinery Needs
Material
|
Key Properties
|
Application
|
Advantages
|
Alloy Steel (4140, 4340)
|
High tensile strength (800-1,200MPa), wear resistance
|
Gearboxes, drive shafts, hydraulic cylinders
|
Withstands high torque; ideal for heavy machinery.
|
Stainless Steel (304, 316)
|
Corrosion resistance, hygiene compliance
|
Food processing equipment, marine machinery
|
500+ hours salt spray resistance; easy to clean.
|
Cast Iron (Gray, Ductile)
|
Vibration damping, low cost
|
Bearing housings, machine bases
|
Absorbs 30% more vibration than steel; economical for large parts.
|
Aluminum Alloy (6061-T6)
|
Lightweight, high thermal conductivity
|
Conveyor components, precision manifolds
|
30% lighter than steel; reduces energy consumption in moving parts.
|
Machinery Parts Machining Technologies
- Multi-axis CNC machining: 5-axis mills produce complex hydraulic manifolds with intersecting ports (±0.01mm position tolerance), eliminating assembly leaks in industrial presses.
- Precision grinding: Cylindrical grinding achieves Ra 0.02μm surface finish on bearing seats, reducing friction and extending bearing life by 50%.
- Automated production cells: Robotic loading/unloading and in-line CMM inspection ensure 99.9% consistency for high-volume parts (e.g., 10,000 conveyor rollers/month).
Custom Machinery Parts Manufacturing Process
- Design & DFM: Engineers analyze client CAD files (STEP/IGS) to optimize for load distribution—e.g., adding fillets to gear teeth to prevent fatigue failure.
- Material selection: Choose alloy steel for high-torque parts (e.g., 4140 for drive shafts) or 316 stainless for corrosive environments (e.g., chemical processing equipment).
- CNC machining: Milling/turning creates base features; wire EDM adds precision details (keyways, gear teeth); grinding refines bearing surfaces.
- Heat treatment: Carburizing/quenching enhances surface hardness, followed by stress relief to prevent warping under load.
- Surface coating: Chrome plating or powder coating applied per environment (e.g., food-grade coatings for 304 parts).
- Quality validation: CMM inspection, pressure testing, and fatigue trials ensure compliance with ISO 9001 and client specs.
Custom Machinery Parts Application Fields
- Industrial machinery: Gearboxes, hydraulic manifolds, and bearing housings for injection molding machines, presses, and robotics (alloy steel, 4140).
- Agricultural equipment: wear-resistant steel plow components, stainless steel irrigation system parts (resistant to fertilizer corrosion).
- Food processing: 304 stainless steel conveyor belts, hydraulic cylinders with FDA-compliant coatings (easy to sanitize).
- Construction machinery: Ductile iron bearing housings, high-strength steel bucket teeth (withstand 500+ hours of rock impact).
- Medical equipment: Aluminum alloy precision manifolds for diagnostic machines (lightweight, corrosion-resistant).
Customization Capabilities: From Prototype to Production
- Design optimization: FEA analysis ensures parts (e.g., crane hooks) withstand 2x working load without deformation, meeting OSHA standards.
- Low-volume flexibility: 1-1,000 units via CNC machining for prototype testing (e.g., agricultural gearbox prototypes in 5 days).
- High-volume production: 10,000+ units/month with multi-cavity tooling and automated lines (e.g., 50,000 conveyor rollers for logistics systems).
Common Processing Questions
- Q: How to ensure gearboxes handle 10,000Nm torque without failure?
- Q: What’s the lead time for 500 hydraulic manifolds (4140 steel)?
- Q: Can parts withstand -40℃ temperatures (e.g., cold storage machinery)?
- Q: How to reduce vibration in high-speed machinery (3,000 RPM)?
Why Choose Goldcattle?
- Industrial expertise: 26 years in machinery parts, with 200+ designs meeting ISO 9001/OSHA standards for heavy equipment.
- Quality assurance: 100% CMM inspection, pressure testing, and fatigue trials; full material traceability (heat codes, certificates).
- Cost efficiency: Design-to-cost engineering (e.g., integrating 3 parts into 1) reduces assembly time by 40% for clients.
- Global compliance: Parts meet EU CE, US OSHA, and food-grade FDA standards, suitable for multinational machinery brands.