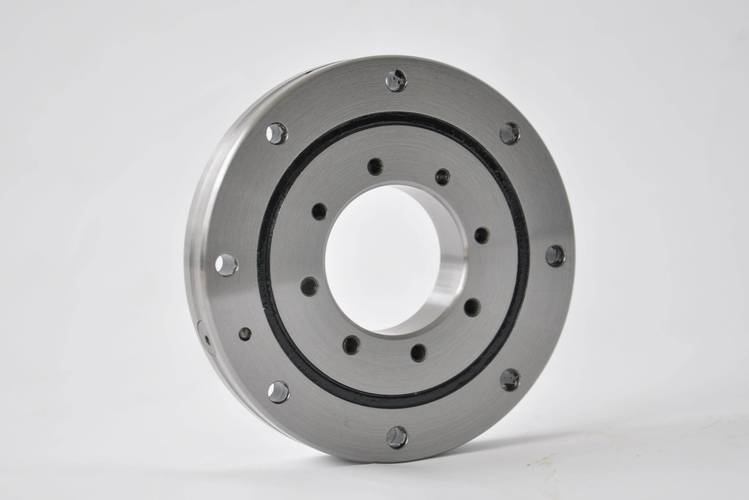
Core Processing Technologies: Engineering for Bearing Performance
1. Precision Grinding & Superfinishing
- CNC cylindrical grinding: Produces bearing rings with ±0.001mm outer diameter tolerance and 0.002mm concentricity, critical for radial clearance control (≤0.01mm). A 60mm deep-groove bearing ring achieved Ra 0.02μm surface finish, reducing friction by 15% compared to standard grinding.
- Superfinishing: Polishes raceways to Ra 0.01μm, eliminating micro-irregularities that cause wear. A tapered roller bearing treated this way extended service life by 2x in heavy machinery applications.
- Centerless grinding: Creates precision rollers (diameter tolerance ±0.0005mm) with perfect roundness (≤0.001mm), ensuring uniform load distribution in spherical roller bearings.
2. Heat Treatment & Material Hardening
- Through-hardening: Hardens bearing rings and rollers to 60-64 HRC (Rockwell), with uniform hardness depth (2-5mm) for wear resistance. A 40mm ball bearing ring endured 50 million rotations without measurable wear.
- Case hardening: For bearing cages and adapter sleeves, carburizing creates a hard surface (58-62 HRC) with a ductile core (35-40 HRC), balancing strength and impact resistance. A steel cage treated this way survived 100+ assembly/disassembly cycles without deformation.
- Stress relief annealing: Eliminates residual stresses in large bearing rings (≥200mm OD), preventing dimensional changes under continuous load (≤0.001mm/1000 hours).
3. Surface Coating & Lubrication Enhancement
- Tribological coatings: DLC (Diamond-Like Carbon) coating on bearing rings reduces friction coefficient by 40%, enabling operation without lubrication in food/medical equipment (compliant with FDA 21 CFR 175.300).
- Corrosion-resistant plating: Zinc-nickel plating on stainless steel bearing parts provides 1,000+ hours salt spray resistance, ideal for marine and chemical processing applications.
- Solid lubricant embedding: Molybdenum disulfide (MoS₂) embedded in cage surfaces ensures emergency operation (up to 1,000 cycles) during lubrication failure, preventing catastrophic equipment damage.
4. Quality Testing for Bearing Reliability
- Dimensional inspection: Uses laser micrometers and CMMs to verify critical dimensions—raceway diameter (±0.001mm), roller length (±0.002mm), and cage pocket tolerance (±0.003mm).
- Fatigue testing: Bearings undergo 100 million+ rotation cycles at 120% rated load, ensuring compliance with ISO 281 fatigue life standards (L10 life ≥10,000 hours).
- Vibration analysis: Spectrometers detect abnormal vibration patterns (≤1.0mm/s) in assembled bearings, indicating defects like uneven raceways or misaligned rollers.
Material Expertise: Matching Materials to Bearing Applications
Material
|
Key Properties
|
Application
|
Advantages
|
High-Carbon Chromium Steel (SUJ2, 52100)
|
60-64 HRC hardness, excellent wear resistance
|
Industrial bearings, automotive wheel bearings
|
Cost-effective; ideal for high-load (≤50kN) applications.
|
Stainless Steel (440C, 316)
|
Corrosion resistance, 58-60 HRC hardness
|
Food processing, marine, medical equipment
|
Withstands 1,000+ hours salt spray; suitable for washdown environments.
|
Ceramic (Silicon Nitride)
|
Lightweight, high temperature resistance (up to 1,200℃)
|
High-speed spindles, aerospace bearings
|
40% lighter than steel; low thermal expansion; resists magnetic fields.
|
Brass (C36000)
|
Ductility, low friction
|
Bearing cages, retainers
|
Prevents roller skidding; compatible with lubricants in high-speed (10,000+ RPM) applications.
|
Mechanical Bearing Parts Machining Technologies
- 5-axis grinding centers: Enable complex bearing geometries (e.g., angular contact raceways) to be machined in one setup, reducing alignment errors by 95%.
- Automated superfinishing lines: Robotic loading and computer-controlled polishing ensure consistent Ra 0.01μm finishes across 10,000+ parts/day.
- Eddy current testing: 100% inspection of heat-treated parts detects subsurface defects (e.g., cracks, inclusions) that cause premature failure, maintaining 99.99% defect-free rate.
Custom Mechanical Bearing Parts Manufacturing Process
- Design & DFM: Engineers analyze client CAD files (STEP/IGS) to optimize raceway geometry—e.g., adjusting curvature radius for 10% higher load capacity.
- Material selection: Choose SUJ2 steel for industrial bearings, 440C stainless for corrosion resistance, or ceramic for high-temperature applications.
- CNC machining: Turning creates rough shapes; cylindrical/centerless grinding refines dimensions; superfinishing polishes raceways.
- Heat treatment: Through-hardening or case hardening enhances hardness, followed by tempering to reduce brittleness.
- Surface treatment: DLC coating or zinc plating applied per environment (e.g., 316 stainless with passivation for food-grade bearings).
- Quality validation: CMM inspection, fatigue testing, and vibration analysis ensure compliance with ABMA and ISO 15242 standards.
Custom Mechanical Bearing Parts Application Fields
- Industrial machinery: Angular contact bearings for machine tool spindles (SUJ2 steel, precision class P4).
- Automotive: Wheel bearings, transmission bearings (high-carbon steel with through-hardening).
- Food & beverage: 440C stainless steel bearings with seals (resistant to cleaning chemicals and water).
- Aerospace: Ceramic hybrid bearings for jet engine auxiliary systems (withstand 800℃ and 15,000 RPM).
- Renewable energy: Large-diameter (≥500mm) spherical roller bearings for wind turbine main shafts (SUJ2 steel, superfinished raceways).
Customization Capabilities: From Prototype to Production
- Design optimization: FEA analysis simulates load distribution, adjusting raceway profiles to extend L10 life by 30% in heavy-duty applications.
- Low-volume flexibility: 1-5,000 units via CNC grinding for prototype testing (e.g., custom ceramic bearings for aerospace R&D).
- High-volume production: 100,000+ units/month with automated lines (e.g., automotive wheel bearing rings for OEM manufacturers).
Common Processing Questions
- Q: How to ensure bearings operate at 15,000 RPM without overheating?
- Q: What’s the lead time for 1,000 custom 440C stainless bearing rings (60mm OD)?
- Q: Can bearings withstand extreme cold (-50℃) in Arctic machinery?
- Q: How to reduce noise in precision bearings (e.g., medical equipment)?
Why Choose Goldcattle?
- Bearing expertise: 26 years in precision bearing components, with 150+ designs meeting ABMA, ISO, and JIS standards.
- Quality assurance: 100% inspection via CMM, eddy current testing, and fatigue trials; full traceability from raw material to delivery.
- Technical innovation: In-house R&D team develops custom solutions (e.g., hybrid ceramic-steel bearings) for unique applications like high-speed spindles.
- Global compliance: Parts meet FDA, REACH, and aerospace standards, suitable for multinational clients in automotive, medical, and industrial sectors.