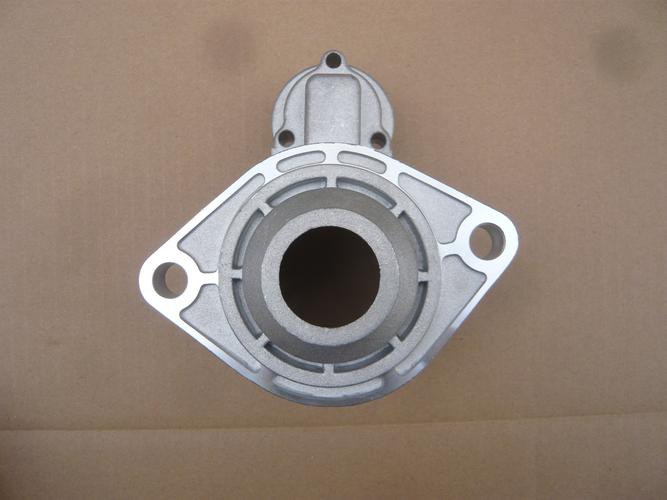
Table of Contents
- Metal Die Castings: The Universal Component Carrier in Industrial Manufacturing
- Custom Material Selection: Decoding the Material Adaptation Logic for Metal Parts
- Precision Manufacturing Processes: From Blueprint to Finished Product with Surgical Precision
- Core Technological Breakthroughs: Conquering Multi-Scenario Application Challenges
- Full-Process Quality Control: Excellence Defined by Details
- Agile Service System: Matching Diverse Order Requirements
- Metal Die Casting FAQs: Professional Answers to Key Customization Questions
1. Metal Die Castings: The Universal Component Carrier in Industrial Manufacturing
- Complex Structure Forming: Capable of producing 0.5mm thin-walled parts, deep cavities (height-to-diameter ratio ≤5:1), and multi-directional undercuts, meeting precision needs like electronic connectors (hole diameter ±0.02mm) and furniture hinges (opening/closing life ≥50,000 cycles).
- Material Diversity: Alloys like zinc (Zamak 3), aluminum (ADC12), and copper (CuZn39Pb3) adapt to different scenarios, balancing strength (tensile strength 150-400MPa), electrical conductivity (copper ≥30% IACS), and corrosion resistance (salt spray test ≥48 hours).
- Cost-Effectiveness: With a mold life of 500,000-1,000,000 cycles, single-process forming reduces machining costs by 30%-50%, ideal for rapid small-to-medium batch production (minimum order quantity 500 pieces).
2. Custom Material Selection: Decoding the Material Adaptation Logic for Metal Parts
1. Main Alloy Properties and Typical Applications
Alloy Type
|
Representative Grade
|
Core Advantages
|
Industry Applications
|
Zinc Alloy
|
Zamak 3
|
Dimensional accuracy CT4 level (±0.03mm), excellent electroplating adhesion
|
Electrical sockets, locks, decorative parts
|
Aluminum Alloy
|
ADC12
|
Lightweight (density 2.7g/cm³), high thermal conductivity (180W/(m·K))
|
Heat sinks, mechanical structures, sports equipment
|
Copper Alloy
|
C3604
|
High electrical conductivity (≥85% IACS), wear resistance (hardness ≥70HB)
|
Electrical terminals, gears, bathroom hardware
|
Magnesium Alloy
|
AZ91D
|
Ultra-lightweight (density 1.8g/cm³), seismic resistance (damping coefficient 0.05)
|
Drone frames, laptop hinges
|
2. Custom Material Design
- Electronic Hardware: Adding 0.01% rare earth elements to zinc alloy increases electroplating adhesion to 7N/cm (cross-cut test), achieving 96 hours of salt spray testing without white rust.
- Mechanical Hardware: Controlling Fe≤0.8% in aluminum alloy and using T6 heat treatment boosts tensile strength to 350MPa, meeting high-load gearbox requirements.
3. Precision Manufacturing Processes: From Blueprint to Finished Product with Surgical Precision
1. Mold Design: 0.01mm-Level Precision Mastery
- DFM Manufacturability Analysis: Simulating filling paths via Moldflow to optimize gate positions (≥2mm from assembly surfaces), reducing flash occurrence from 8% to 1.5% and extending core life by 20%.
- Precision Machining:
-
- Slow wire EDM for 0.3mm micro-holes (accuracy ±0.005mm), suitable for high-precision connector pin holes;
-
- PVD titanium plating (3-5μm thickness) increases mold surface hardness to 2000HV, reducing sticking-induced surface defects (occurrence rate ≤0.5%).
2. Die Casting: Material-Specific Processes
- Zinc Alloy Hot-Chamber Casting: Injection speed 5-8m/s, mold temperature controlled at 180±5℃, achieving 95% yield for 0.8mm thin-walled parts (industry average 85%).
- Aluminum Alloy Cold-Chamber Casting: Vacuum degree ≤100mbar, injection pressure 100-150MPa, reducing internal porosity to ≤1% for airtight parts (leakage rate ≤5cc/min).
3. Post-Processing: Dual Enhancement in Function and Aesthetics
- Precision Machining: CNC milling with flatness ≤0.05mm/100mm, drilling positional accuracy ±0.03mm, suitable for high-precision assembly (e.g., flange connection surfaces).
- Surface Treatment Matrix:
-
- Electroplating: Zinc plating (8-12μm) passing 48-hour salt spray test, nickel plating (15-20μm) with hardness ≥500HV;
-
- Powder Coating: 80-100μm thickness, adhesion grade 0, supporting full RAL color customization;
-
- Anodizing: Aluminum alloy anodic oxidation film 5-25μm thick, weather resistance ≥1000 hours without chalking.
4. Core Technological Breakthroughs: Conquering Multi-Scenario Application Challenges
1. Precision Forming Technologies
- Micro-Cavity Forming: Successfully casting 0.5mm wall thickness and 10mm deep cavities (height-to-diameter ratio 20:1), increasing filling success rate to 92% via auxiliary exhaust slots (0.03mm depth) and high-speed injection (60m/s).
- Multi-Slider Mold Design: One-step forming of 4-directional undercuts (e.g., drawer slide components), reducing secondary processes and improving dimensional consistency by 40%.
2. Surface Treatment Technologies
- Nanoscale Electroplating: Pulse electroplating enhances coating uniformity by 30%, with microporosity ≤5 per cm², suitable for optical-grade surfaces (roughness Ra≤0.2μm).
- Chromium-Free Passivation: Compliant with RoHS 2.0, salt spray performance 20% better than traditional processes, meeting EU export requirements for hardware.
3. Automated Production
- Robotic Part Picking: Positioning accuracy ±0.1mm, picking cycle ≤5 seconds, reducing surface scratches from manual intervention (defect rate from 3% to 0.3%).
- Intelligent Quality Inspection: AI visual inspection identifies defects ≥0.1mm² with 99.8% accuracy, 漏检率 ≤0.01%, suitable for zero-defect electronic hardware.
5. Full-Process Quality Control: Excellence Defined by Details
1. Raw Material Control
- Spectral Analysis: Batch material composition testing (accuracy 0.01%), ensuring Zn alloy Pb+Cd+Hg≤0.005%, Al alloy Si content fluctuation ≤0.2%, eliminating material deviations at the source.
- Mechanical Testing: Tensile test (Zn alloy ≥250MPa), hardness test (Cu alloy ≥60HB), batch qualification rate 99.7%.
2. Process Monitoring
- IoT Data Collection: Real-time monitoring of injection pressure (fluctuation ≤3%), mold temperature (deviation ±2℃), cycle time (error ≤1 second), with automatic alarm and shutdown for anomalies (response time ≤10 seconds).
- First Article Inspection: CMM measurement of 20+ critical dimensions (Cpk≥1.33), X-ray flaw detection for defects ≥0.5mm, ensuring 100% first-article pass rate before mass production.
3. Finished Product Inspection
Inspection Item
|
Inspection Method
|
Metal Hardware Standard
|
Compliance Rate
|
Dimensional Accuracy
|
Coordinate Measuring Machine
|
Critical dimensions ±0.03mm, thread accuracy 6H
|
99.5%
|
Surface Defects
|
AI Visual Inspection System
|
0 tolerance for burrs/blisters ≥0.1mm
|
100%
|
Salt Spray Testing
|
Neutral Salt Spray Chamber
|
Zn alloy ≥72 hours, Al alloy ≥200 hours
|
99.2%
|
Torque Testing
|
Electronic Torque Tester
|
Screw hole torque ≥5N·m (M4 specification)
|
100%
|
6. Agile Service System: Matching Diverse Order Requirements
1. Rapid Prototyping
- Simple Molds: Aluminum/resin molds deliver first samples in 7 days, supporting 3D printed prototype verification, reducing prototyping costs by 40% and cycles by 50%.
- Design Collaboration: Providing DFM reports (20+ manufacturability suggestions), helping customers optimize structures (e.g., 20% wall thickness reduction, 15% mold cost savings).
2. Flexible Production
- Small-Batch Support: 500-piece minimum order, intelligent scheduling balancing multi-variety needs (simultaneous production of up to 20 products), order change response time ≤24 hours.
- Mass Production: Equipped with 100-1000T die casting machines, monthly capacity 5 million pieces, delivery cycle for complex hardware 30% shorter than industry average.
3. After-Sales Assurance
- Quality Traceability: Unique traceability code for each batch, linked to mold number, production parameters, and test data, enabling 10-second problem source 定位.
- Technical Support: Providing electroplating/assembly process guidance, assisting customers in resolving surface treatment and assembly tolerance issues, customer satisfaction 98%.