In the wave of the intelligent and precision transformation of the manufacturing industry, the custom metal stamping parts service is becoming a core tool for enterprises to break through technical bottlenecks and achieve differential competition. This article will analyze how to provide high – precision and high – reliability metal stamping solutions for different fields through customized services from the dimensions of material innovation, process upgrading, parameter control, etc., combined with cutting – edge industry practices.
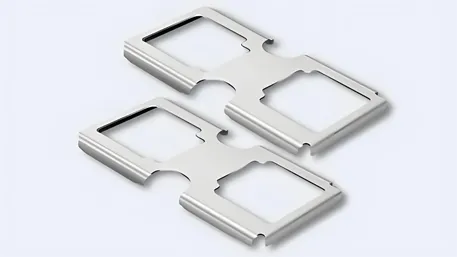
The core value of metal stamping parts is first reflected in material selection. In addition to conventional materials such as steel and aluminum alloys, the current industry pays more attention to achieving scenario – based adaptation through materials science optimization:
- High – strength and lightweight alloys: For example, the automotive industry uses new magnesium – aluminum alloy stamping parts, which can reduce the vehicle body weight by 15% – 20% while meeting collision safety standards.
- Corrosion – resistant composite materials: For the medical device field, through the stamping process of titanium alloy and polymer composites, the biocompatibility and corrosion resistance are both improved.
- Conductive and heat – conductive modified materials: In the stamping parts of 5G base station heat sinks, the application of copper – aluminum laminated materials increases the thermal conductivity by more than 40%.
Based on the latest process optimization practices in 2025, modern custom metal stamping services have formed a full – chain technical closed – loop:
- Intelligent Mold Design
- The use of an AI – driven mold simulation system can predict the material flow state at the design stage, shortening the mold debugging cycle by more than 50%.
- Modular mold component design supports rapid model changeovers to meet the production needs of small batches and multiple varieties.
- Control of the Stamping Process
- The introduction of servo press dynamic compensation technology enables fine – tuning of the stamping speed at the level of 0.01mm/s, ensuring that the forming accuracy of complex structural parts reaches ±0.02mm.
- An online laser detection system monitors the deformation of stamping parts in real – time and automatically feeds back to adjust process parameters.
- Innovation in Surface Treatment
- The application of nano – coating technology on the surface of home appliance stamping parts increases wear resistance by 3 times and achieves antibacterial functions.
- The micro – arc oxidation process provides 2000 – hour salt – spray test protection for aerospace stamping parts.
- Structural Parts for New Energy Vehicles
- Breakthroughs in the integrated battery tray stamping technology, one – time forming of 10 – mm – thick aluminum alloy sheets through multi – station progressive dies, reducing the number of welding points by 80%.
- The motor stator and rotor punching sheets use ultra – thin silicon steel sheets (0.2mm thickness), reducing iron loss to less than 1.2W/kg.
- Precision Components for Consumer Electronics
- The folding – screen mobile phone hinge stamping parts go through 18 precision forming processes to achieve zero failures in 100,000 folding tests.
- The antenna stamping parts of smart wearable devices use LDS (Laser – Direct – Structuring) technology, increasing integration by 60%.
- Core Components of High – end Equipment
- The vacuum chamber stamping parts of semiconductor equipment apply an ultra – high – cleanliness polishing process, with a surface roughness Ra ≤ 0.1μm.
- The flexible wheel of the harmonic reducer of industrial robots uses progressive stamping hardening technology, with a fatigue life exceeding 20,000 hours.
By constructing a multi – dimensional parameter control model, a shift from experience – driven to data – driven is achieved:
- Dynamic pressure compensation: Real – time compensation for material springback during the stamping process, narrowing the tolerance band to 1/3 of that of traditional processes.
- Temperature gradient control: In the deep – drawing process, a zonal heating technology is used to eliminate crack defects caused by stress concentration.
- Mold life prediction: A prediction model is established based on data such as the number of stampings and material hardness, reducing mold maintenance costs by 35%.
- Green Manufacturing Technologies
- Develop water – soluble stamping oil agents, reducing wastewater emissions in subsequent cleaning processes by 90%.
- The waste intelligent sorting system achieves a metal recovery rate of over 99.2%.
- Applications of Digital Twin
- Establish a digital twin of the stamping process, shortening the new product development cycle to within 72 hours.
- Blockchain technology is used to trace the process parameters and quality inspection data of each batch of stamping parts.