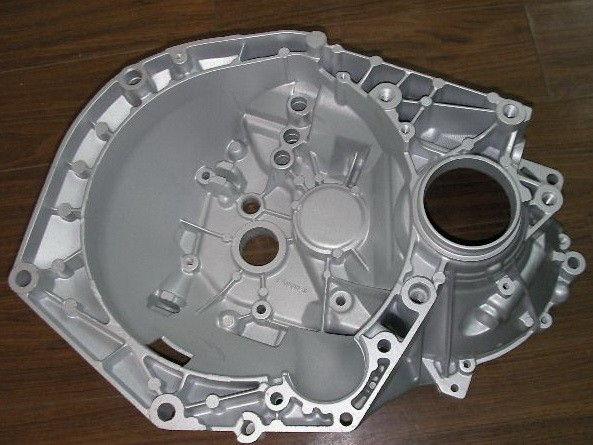
Table of Contents
- Motorcycle Die Castings: The Core of Performance Upgrades in Two-Wheeled Industry
- Custom Material Selection: Decoding the Material Code for Motorcycle Core Components
- Precision Manufacturing Process: The Transformation from Liquid Metal to High-Performance Parts
- Core Technological Breakthroughs: Overcoming Complex Working Condition Challenges for Motorcycles
- Full-Process Quality Control: Reliable Quality under Harsh Environments
- Agile Service System: Matching the High-Efficiency Needs of the Motorcycle Industry
- Motorcycle Die Casting FAQs: Professional Answers to Key Customization Questions
1. Motorcycle Die Castings: The Core of Performance Upgrades in Two-Wheeled Industry
- Urgent Lightweight Demand: Achieve 30%-50% weight reduction compared to steel components. For example, aluminum alloy wheels are 40% lighter than steel wheels, improving acceleration by 5% and fuel efficiency by 8%, while reducing suspension load and enhancing driving stability.
- Complex Structure Forming: Integrated die casting realizes complex curved surface forming (curvature radius ≤3mm) for engine blocks and frame main beams, reducing welding processes by 60% and improving part consistency (dimensional tolerance ±0.03mm).
- Harsh Condition Adaptation: Maintain stable performance in the temperature range of -30℃~120℃, with corrosion depth ≤10μm after 500 hours of salt spray testing, suitable for complex environments like off-road and long-distance motorcycle travel.
2. Custom Material Selection: Decoding the Material Code for Motorcycle Core Components
1. Main Alloy Selection and Performance Advantages
Alloy Type
|
Typical Grade
|
Core Performance Indicators
|
Typical Applications
|
Aluminum Alloy
|
ADC12/A380
|
Tensile strength ≥300MPa, density 2.7g/cm³, thermal conductivity ≥180W/(m·K)
|
Engine blocks, cylinder heads, wheels
|
Zinc Alloy
|
Zamak 3
|
Dimensional accuracy CT4 level (±0.03mm), electroplating adhesion ≥5N/cm
|
Handlebar risers, brake pump housings
|
Magnesium Alloy
|
AZ91D
|
Density 1.8g/cm³, excellent damping performance (vibration attenuation rate ≥30%)
|
Lightweight frame components, rear swingarms
|
2. Custom Material Design
- Engine Components: Adding 0.5% Mg to aluminum alloy for high-temperature resistance in cylinder blocks, maintaining tensile strength ≥250MPa at 180℃, a 15% increase over conventional alloys.
- Suspension Systems: Controlling Pb+Cd ≤0.005% in zinc alloy, achieving 720 hours of salt spray testing without white rust after electroless nickel plating, suitable for high-humidity regions.
3. Precision Manufacturing Process: The Transformation from Liquid Metal to High-Performance Parts
1. Mold Design: 0.01mm-Level Precision Control
- DFM Manufacturability Analysis: Simulating filling pressure (80-120MPa for aluminum alloy) via Moldflow, optimizing gate position (≥5mm from cooling fins), reducing shrinkage porosity from 1.5% to 0.6%.
- Mold Machining:
-
- Core processed by slow wire EDM (accuracy ±0.005mm), ensuring 0.8mm thin-wall hole forming (tolerance ±0.02mm);
-
- Mold surface mirror-polished (Ra≤0.4μm) for “flawless” aluminum alloy wheel surfaces, reducing subsequent grinding processes.
2. Die Casting: Motorcycle-Exclusive Processes
- Vacuum Die Casting Technology: Vacuum degree ≤80mbar, reducing internal porosity of engine blocks to below 0.8%, with airtightness test leakage rate ≤10cc/min (20% better than industry standard).
- Precise Mold Temperature Control: Intelligent temperature control system (accuracy ±3℃) ensures uniform cooling of wheel spokes, reducing casting stress-induced cracks (occurrence rate from 10% to 1.5%).
3. Post-Processing: Dual Enhancement in Function and Aesthetics
- Precision Machining: Five-axis CNC machining for engine cylinder bores (roundness ≤0.01mm), combined with honing (roughness Ra≤0.2μm), ensuring piston ring sealing.
- Surface Treatment Matrix:
-
- Anodizing: 20μm oxide film on wheel surfaces, hardness ≥200HV, scratch resistance increased by 3 times;
-
- Powder Coating: 80-100μm coating on frame components, adhesion cross-cut grade 0, weather resistance ≥1,000 hours without color change.
4. Core Technological Breakthroughs: Overcoming Complex Working Condition Challenges
1. Lightweight and Strength Balance Technology
- Topology Optimization Design: Removing 30% redundant material via Altair Inspire, adding triangular reinforcing ribs (1.2mm thickness) in stress-concentrated areas of frame main beams, achieving 25% weight reduction with 20% increased bending strength.
- Thin-Wall Forming: Breaking through 1.2mm wall thickness limit, achieving 1.0mm thin-wall yield ≥92% (industry average 80%) via high-speed filling (speed ≥50m/s) and conformal mold cooling.
2. Heat Dissipation and Fatigue Resistance Technology
- Heat Dissipation Structure Optimization: 5mm-high cooling fins (3mm spacing) on engine blocks, reducing cylinder temperature by 15℃ via Flotherm simulation, extending engine life by 10%.
- Fatigue Strengthening Treatment: Shot peening for suspension components (shot diameter 0.3mm, 100% coverage), increasing surface fatigue strength by 30%, with 实测 fatigue life exceeding 500,000 cycles without cracks.
3. Precision Assembly Technology
- Integrated Datum Design: Directly forming assembly bosses in molds (height tolerance ±0.01mm), reducing CNC secondary positioning error, ensuring brake pump mounting hole positional accuracy ≤0.03mm to avoid braking deviation.
5. Full-Process Quality Control: Reliable Quality under Harsh Environments
1. Raw Material Control
- Spectral Analysis: Batch alloy composition testing (accuracy 0.01%), controlling Si content in aluminum alloy at 11.5%-13.5% and Al content in zinc alloy at 3.5%-4.5% for stable performance.
- Mechanical Testing: Tensile test (aluminum alloy tensile strength ≥320MPa), hardness test (zinc alloy ≥80HB), batch qualification rate ≥99.8%.
2. Process Monitoring
- IoT Data Collection: Real-time monitoring of injection pressure (fluctuation ≤2%) and mold temperature (deviation ±3℃), archiving per-cycle data for 5 years to enable rapid problem tracing.
- First Article Three-Inspection System: First article must pass full-dimensional inspection (100+ test points), X-ray flaw detection, and airtightness test; any non-compliance triggers mold maintenance.
3. Finished Product Inspection
Inspection Item
|
Inspection Method
|
Motorcycle-Grade Standard
|
Compliance Rate
|
Dimensional Accuracy
|
Coordinate Measuring Machine
|
Key dimensions ±0.03mm, flatness ≤0.05mm
|
99.6%
|
Internal Defects
|
X-ray Flaw Detection
|
0 tolerance for 气孔 ≥0.5mm
|
100%
|
Salt Spray Testing
|
Neutral Salt Spray Chamber
|
No red rust after 500 hours
|
99.2%
|
Fatigue Life
|
Vibration Fatigue Tester
|
500,000 cycles without cracks
|
100%
|
6. Agile Service System: Matching High-Efficiency Needs of Motorcycle Industry
1. Rapid Collaborative R&D
- Early Design Involvement: Participating in customer product development, providing wall thickness optimization (recommended 1.5-3mm) and demolding draft suggestions (2°-3°), reducing mold modification costs by 40%.
- Rapid Prototyping: Aluminum simple molds deliver first samples in 7 days, supporting fast verification for complex components like engine blocks (traditional cycle 15 days).
2. Flexible Production Capacity
- Small-Batch Support: Minimum order quantity 500 pieces, intelligent scheduling balancing multi-variety needs, order change response time ≤24 hours.
- Mass Production: Equipped with 200-800T die casting machines, monthly capacity 500,000 pieces, 24-hour continuous production for key components, delivery cycle 25% shorter than industry average.
3. After-Sales Guarantee
- On-Site Technical Service: Providing heat treatment deformation correction for large-displacement motorcycle customers, increasing yield from 85% to 97%;
- Long-Term Quality Tracking: Establishing component life 档案,regular 回访 (quarterly), optimizing 23 designs to reduce after-sales failure rate by 15%.