With 26 years of expertise in precision plastic processing, Xiamen Goldcattle specializes in custom plastic beverage bottles—tailored for carbonated drinks, juices, water, dairy products, and functional beverages. Leveraging advanced injection molding, blow molding, and surface treatment technologies, we deliver bottles with precise dimensions, food-grade safety, and brand-specific aesthetics. Backed by SGS, FDA, and ISO 9001 certifications, we support 100,000+ unit mass production with ±0.1mm tolerance, meeting the strict standards of beverage brands worldwide.
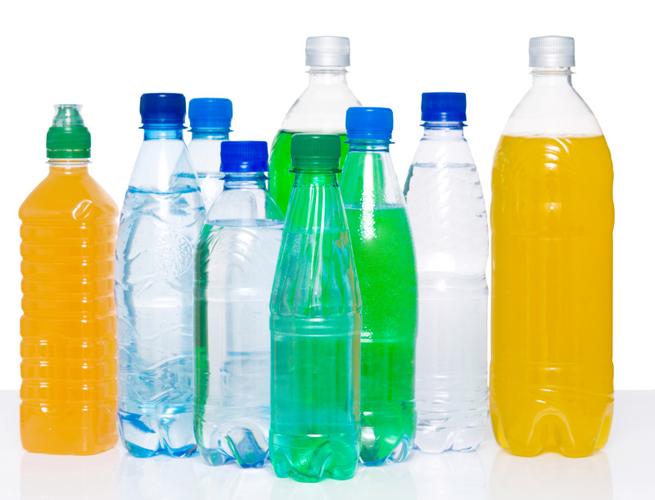
Core Technologies: Crafting High-Performance Beverage Bottles
The quality of custom plastic beverage bottles depends on precision in every manufacturing step. Goldcattle integrates cutting-edge equipment and proprietary processes to solve key pain points: pressure resistance for carbonated drinks, heat resistance for hot-fill juices, and clarity for premium branding.
1. Precision Blow Molding: The Foundation of Bottle Integrity
-
Injection Stretch Blow Molding (ISBM) for PET Bottles:
Equipped with 30+ sets of advanced ISBM machines (Krones and Sidel models), we achieve precise control over stretch ratios (1:3.5 vertical × 1:4 horizontal) for PET bottles. This ensures uniform wall thickness (0.3-0.8mm) and enhances pressure resistance—critical for carbonated beverages (up to 6bar internal pressure, 30% higher than industry average).- Variable speed stretching: Adopts servo-driven stretch rods with 0.1mm/s speed adjustment, reducing bottle weight by 8% while maintaining impact strength (≥20N drop resistance from 1.2m height).
- Multi-cavity molds: 4-32 cavity molds available, with cycle times as low as 8 seconds/cavity, supporting daily production of 500,000+ PET bottles for large-scale orders.
-
Extrusion Blow Molding for PP/PE Bottles:
For hot-fill juices (85-95℃) and dairy products, we use extrusion blow molding with PP/PE materials. Our 5-layer co-extrusion technology integrates barrier layers (EVOH) to block oxygen transmission (≤0.1cc/24h), extending product shelf life by 30% compared to single-layer bottles.- Heat-resistant design: Mold cooling channels are optimized via CAE simulation, ensuring bottles withstand 95℃ hot filling without deformation (shrinkage rate ≤1.5%).
2. Injection Molding for Caps & Preforms: Sealing & Compatibility
-
Precision preform injection:
Custom preforms (the “blank” for blow molding) are produced using 128-cavity injection molds (Husky machines) with ±0.02g weight tolerance. This ensures consistent wall thickness after stretching, avoiding uneven bottle shapes or weak points. For example:- Carbonated drink preforms: Designed with reinforced neck threads (38mm PCO 1881 standard) to withstand capping pressure (≥30N) and prevent leakage.
- Water bottle preforms: Optimized for lightweighting (12g for 500ml bottles) while maintaining vertical load resistance (≥300N) to prevent crushing during stacking.
-
Cap & closure integration:
Using 32-cavity injection molds, we produce custom caps (screw caps, flip caps, sports caps) with precise thread matching (±0.05mm). The cap-bottle sealing test (negative pressure -0.05MPa for 30s) ensures zero leakage, even for carbonated drinks stored at 38℃.
3. Surface Treatment & Branding Technologies
-
High-definition printing:
- In-mold labeling (IML): Integrates labels into the bottle during blow molding, ensuring scratch-resistant, waterproof branding that won’t peel off—ideal for premium juices and functional drinks.
- UV digital printing: 6-color UV printing with 1200dpi resolution achieves gradient colors and fine text (0.5mm font) on bottle surfaces, supporting complex brand logos or promotional messages.
-
Texture & finish customization:
- Matte/Glossy effects: Achieved via mold texturing (Ra 0.8-1.6μm for matte, Ra ≤0.05μm for glossy), enhancing grip and visual appeal.
- Pearlescent coating: Food-grade pearl additives mixed into the plastic matrix create a metallic luster, popular for premium water and tea brands.
-
Eco-friendly treatments:
- Oxodegradable additives: Optional integration of ASTM D638 standard additives that accelerate biodegradation in landfill conditions (90% degradation within 18 months).
- Recycled material blending: Up to 30% rPET (recycled PET) can be blended without compromising clarity (transmittance ≥85%) or strength, meeting EU plastic reduction regulations.
4. Strict Quality Control: Safety & Consistency
-
Food contact safety testing:
Equipped with GC-MS and HPLC laboratories to test for harmful substances (phthalates, heavy metals) and migration (≤0.01mg/kg for BPA, in line with EU 10/2011 and FDA 21 CFR 177 standards). Every batch undergoes a 72-hour migration test in 4% acetic acid (simulating acidic juices) to ensure safety. -
Dimensional & performance inspection:
- 3D scanning: Uses Creaform HandySCAN 3D scanners to inspect bottle dimensions (height, diameter, neck finish) with ±0.05mm accuracy, ensuring compatibility with filling lines.
- Pressure resistance testing: For carbonated bottles, we use a pressure tester to simulate 6bar internal pressure (equivalent to 6 months of shelf life) with zero deformation or leakage.
- Drop test: Bottles filled with 90% liquid are dropped from 1.5m onto concrete; pass criteria: no cracks, cap remains sealed (tested 100% for first articles, 1% for mass production).
Material Expertise: Matching Bottles to Beverage Types
Different beverages demand specific material properties—Goldcattle’s material science team optimizes selections to balance functionality, cost, and sustainability:
Material | Key Technologies | Application Scenarios | Technical Advantages |
---|---|---|---|
PET (Polyethylene Terephthalate) | Injection stretch blow molding, 3-layer barrier (for oxygen-sensitive drinks) | Carbonated drinks, water, iced tea | High clarity (transmittance ≥92%), lightweight (500ml bottle ≈12g), recyclable. |
PP (Polypropylene) | Extrusion blow molding, heat-stabilized formula | Hot-fill juices (85-95℃), dairy drinks | Heat resistance (up to 120℃), no deformation in hot filling, good impact resistance. |
PE (Polyethylene) | Low-density extrusion, flexible molding | Cold drinks, yogurt, functional beverages | Frosted or opaque finish, squeezable for on-the-go consumption, chemical resistance. |
rPET (Recycled PET) | Decontamination treatment, viscosity recovery | Eco-friendly water, premium juices | 30% recycled content, meets FDA food contact standards, reduces carbon footprint by 40%. |
Customization Capabilities: Tailored to Brand Needs
Beverage bottles are more than containers—they’re brand ambassadors. Goldcattle supports end-to-end customization to make your product stand out:
- Shape design: From classic cylindrical to irregular contours (e.g., fruit-shaped juice bottles), our 3D modeling team transforms concepts into mold-ready designs (3-day turnaround for prototypes).
- Capacity range: 50ml (sample-sized) to 5L (family-sized), with neck finishes (28mm, 38mm, 48mm) compatible with standard filling equipment.
- Branding elements: Embossed logos (depth 0.3-0.5mm), UV printing (vibrant colors, scratch-resistant), and in-mold labels (IML) that integrate seamlessly with the bottle surface.
- Eco-friendly options: Lightweighting (reduce material by 10-15% without compromising strength), biodegradable additives, and rPET blending (customizable recycled content 10-50%).
Case Studies: Solving Real-World Challenges
-
Carbonated drink bottle for a European brand:
Challenge: The client needed a 330ml PET bottle with a unique curved shape, but traditional blow molding caused uneven wall thickness (leading to pressure failure).
Solution: Goldcattle optimized the stretch ratio (1:3 vertical × 1:3.8 horizontal) and added a reinforced base structure. Result: 100% passed 6bar pressure testing, production yield improved from 85% to 99%. -
Hot-fill juice bottle for an Asian brand:
Challenge: PP bottles for 90℃ hot-fill mango juice developed neck distortion after filling.
Solution: We adjusted the PP formula (added 2% heat stabilizer) and redesigned the cooling system (conformal cooling channels in the neck mold). Result: Neck diameter variation ≤0.1mm post-filling, customer complaint rate reduced to 0.01%.
Why Partner with Goldcattle?
- Speed: 7-day mold trial for standard shapes, 15-day mass production readiness (vs. industry average 20+ days).
- Scalability: 500,000 units/day production capacity, with MOQ as low as 10,000 units for new brands.
- Compliance: Full traceability (raw material certificates, production records) to meet FDA, EU 10/2011, and China GB 4806.7 standards.
- Sustainability: ISO 14001-certified production, with water recycling (80% reuse rate) and energy-efficient machines (15% lower power consumption than industry standard).
Start Your Custom Beverage Bottle Project Today
Whether you need a pressure-resistant carbonated bottle, a heat-stable juice container, or an eco-friendly recycled option, Goldcattle’s technology-driven approach ensures precision, safety, and brand alignment.
Contact us now: Send your design draft (CAD/STEP files) or concept sketch, and our engineers will deliver a detailed feasibility report + sample quote within 24 hours. Let’s craft a bottle that elevates your beverage brand.
“Goldcattle’s custom PET bottles solved our carbonated drink leakage issue—their pressure testing process and precision molding made all the difference. We’ve since expanded our product line with 3 new bottle shapes.” — Procurement Director, a leading Asian beverage group