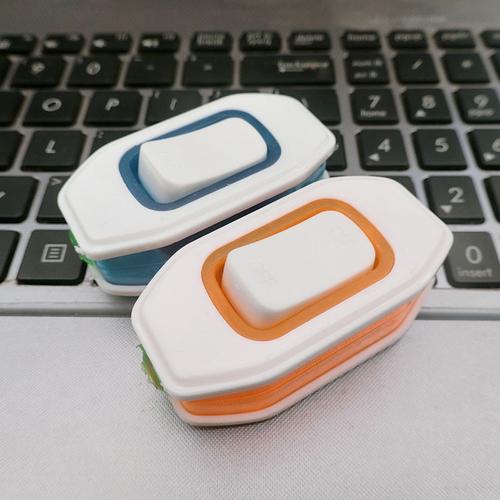
I. Core Material Properties and Application Advantages
(A) Comparison of Mainstream Material Properties
Material Type
|
Density (g/cm³)
|
Temperature Range (℃)
|
Flammability Rating (UL94)
|
Insulation Resistance (Ω)
|
Core Advantages
|
Typical Certifications
|
Acrylonitrile Butadiene Styrene (ABS)
|
1.05
|
-20~80
|
V-0 (1.6mm)
|
≥10¹²
|
Easy molding, cost-effective, high design flexibility
|
IEC 60695-2-11 Glow Wire Test Certification
|
Polycarbonate (PC)
|
1.20
|
-40~130
|
V-2
|
≥10¹³
|
High transparency, impact resistance, dimensional stability
|
UL 746C Material Certification
|
Polybutylene Terephthalate (PBT)
|
1.31
|
-40~150
|
V-0 (0.8mm)
|
≥10¹⁴
|
Low hygroscopicity, chemical resistance, high wear resistance
|
IEC 60243 Dielectric Strength Certification
|
Nylon 66 (PA66)
|
1.14
|
-40~180
|
V-2
|
≥10¹³
|
Self-lubrication, fatigue resistance, high strength
|
RoHS Environmental Certification
|
PC/ABS Alloy
|
1.15
|
-30~120
|
V-0
|
≥10¹³
|
Balanced high strength and toughness
|
REACH SVHC Compliance
|
(B) Driving Forces of Customization Requirements
1. Safety Performance Requirements
- Flammability rating must meet UL94 V-0 (0.8–3.0mm thickness), no sustained combustion in glow wire test (850℃).
- Insulation resistance ≥10¹²Ω (500V DC), dielectric strength ≥25kV/mm to prevent electric leakage.
2. Functional Performance Requirements
- Key life ≥50,000 presses (GB 16915.1 standard), contact resistance ≤50mΩ with stability error ≤5%.
- Waterproof switch parts must achieve IP65 rating (water jet protection), dustproof rating IP5X (complete dust resistance).
3. Environmental Adaptability Requirements
- Weather resistance: QUV aging test for 1000 hours, color difference ΔE ≤3, strength retention ≥80%.
- Low-temperature resistance: Key force change ≤10% at -40℃, suitable for cold northern regions.
II. Analysis of Four Core Processing Technologies
(A) Injection Molding: High-Precision Structural Processing
- Technical Advantages
-
- Supports thin-wall design (wall thickness 0.8–2.0mm), enabling ultra-thin switch panels (thickness ≤3mm).
-
- Multi-cavity molds (32–64 cavities per mold) with production efficiency of 1500–3000 pieces/hour, compatible with Mainstream specifications like 86-type and 118-type switches.
- Process Parameters
-
- Injection pressure 100–160MPa, mold temperature 60–90℃, cooling time 10–20 seconds.
-
- Shrinkage control: ABS 0.4%–0.7%, PBT 1.0%–1.5%, ensuring mounting hole accuracy ±0.1mm.
(B) Surface Treatment Technologies
Process Type
|
Typical Application Scenarios
|
Technical Highlights
|
Flame Retardant Coating
|
Socket housings, high-temperature switches
|
Nano-scale flame retardant coating, oxygen index ≥28%, thickness 50–100μm
|
Insulation Spraying
|
Insulation isolation for conductive parts
|
Epoxy resin coating, insulation resistance increased 10x, thickness 20–30μm
|
Laser Engraving
|
Key characters, indicator markings
|
Laser precision ±0.05mm, supports 0.5mm ultra-fine fonts, friction resistance ≥1000 cycles
|
Electroplating
|
High-end switch decorative parts
|
Chrome plating thickness 8–12μm, salt spray test ≥500 hours, glossiness ≥90GU
|
(C) Secondary Processing: Functional Enhancement
- Structural Reinforcement
-
- Metal insert molding (e.g., copper terminals), pull-out force ≥50N to ensure wiring reliability.
-
- Snap-fit structure design, disassembly force controlled at 8–15N to prevent accidental detachment.
- Touch Optimization
-
- Silicone key overmolding, press force controlled at 15–25N, rebound force error ≤±2N.
-
- Sandblasting treatment (roughness Ra 1.6–3.2μm), anti-slip performance improved by 30%.
(D) 3D Printing: Rapid Prototyping and Small-Batch Customization
- Process Advantages
-
- Rapid validation of irregular structures (e.g., curved switch panels, smart sensor housings), samples delivered in 48 hours.
-
- Nylon 12 material with 80MPa strength for functional testing (e.g., waterproof sealing tests).
- Application Scenarios
-
- Custom smart switch housings (order quantity ≤500 pieces), delivery cycle reduced by 40%.
-
- Reverse engineering for obsolete parts (3D scanning error ≤0.08mm).
III. Full-Process Customization Solutions
(A) Design and Material Engineering
1. Multi-Dimensional Design Support
- Structural Optimization
-
- ANSYS simulation analyzes key stress distribution to ensure deformation ≤0.3mm after 50,000 presses.
-
- Anti-misoperation design: Key travel controlled at 3–4mm, edge chamfer R≥2mm to reduce misoperation probability.
- Functional Customization
-
- Smart switches: Pre-installed sensor slots (accuracy ±0.05mm) for Wi-Fi module and LED indicator integration.
-
- Explosion-proof switches: PBT + 30%GF material, shell strength increased by 40%, compliant with IEC 60079 explosion-proof standard.
2. Precise Material Selection
- Residential Switches: ABS + flame retardant (cost-effective, meets daily fire safety needs).
- Industrial Control Switches: PBT material (120℃ long-term resistance, oil pollution resistance).
- Smart Switches: PC/ABS alloy (high transparency for uniform LED backlighting).
3. Pre-Processing Technology
- Raw material drying: PBT moisture content controlled ≤0.03% to avoid post-molding hydrolysis cracking.
- Color matching: Pantone color accuracy ΔE ≤0.8, supports personalized colors like matte white and champagne gold.
(B) Production and Quality Control
1. Flexible Manufacturing Capability
- Rapid Prototyping
-
- 3D printed samples delivered in 24 hours, aluminum mold development cycle 10–15 days (steel mold 30–40 days).
-
- Supports minimum order quantity of 100 pieces for small-batch customization.
- Mass Production
-
- Automated production lines with KUKA robots, daily capacity 50,000 pieces (86-type switch panels).
-
- Intelligent inspection: Machine vision system detects defects like short shots and flash, accuracy ≥99.5%.
2. Comprehensive Testing System
- Electrical Performance
-
- Dielectric withstand test: 2000V AC for 1 minute without breakdown, leakage current ≤0.5mA.
-
- Contact resistance: Dynamic test for 50,000 cycles, resistance fluctuation ≤10% (GB/T 14048.5 compliant).
- Environmental Performance
-
- Thermal cycling: -40℃~70℃ for 50 cycles, dimensional change rate ≤0.2%.
-
- Chemical resistance: 5% sodium chloride solution immersion for 24 hours, no corrosion or discoloration.
- Certification Support: Provides CCC, CE, UL, and other certification reports for global market access.
IV. Multi-Scenario Application Solutions
(A) Residential Switch Applications
- Wall Switch Panels: ABS material + electroplated decorative strips, surface hardness ≥2H, supports 86/118/120-type specifications, mounting hole pitch accuracy ±0.5mm.
- Smart Socket Housings: PC/ABS alloy + laser-engraved characters, transmittance ≥85%, compatible with USB-C/Lightning interfaces, fire rating V-0.
(B) Industrial Control Applications
- Explosion-Proof Switch Parts: PBT + glass fiber material, explosion mark Ex d IIB T6, suitable for high-risk environments like petroleum and chemical industries.
- Machine Tool Operation Panels: PA66 material + silicone keys, oil resistance (48-hour immersion without swelling), key life ≥100,000 cycles.
(C) Smart Device Applications
- IoT Switch Modules: Ultra-thin PC housing (1.5mm thickness), supports NFC sensing area design, antenna signal attenuation ≤5dB.
- New Energy Vehicle Switches: Low-temperature resistant TPU material (-40℃ impact strength ≥25kJ/m²), waterproof rating IP67, adapted to vehicle vibration (10–2000Hz frequency).
(D) Special Scenario Applications
- Medical Device Switches: ABS + antibacterial treatment (bacteriostasis rate ≥99%), smooth surface for easy cleaning, compliant with ISO 13485 medical standard.
- Aviation Switch Parts: Titanium-reinforced PA material, tensile strength ≥100MPa, passed RTCA DO-160G vibration test.
V. Technology Selection Guide
Requirement Type
|
Preferred Technology
|
Material Choice
|
Core Indicators
|
Delivery Cycle
|
R&D Validation & Small Batches
|
3D Printing + Injection Molding
|
ABS/PC
|
Rapid iteration, irregular structures
|
Prototype in 3 days, batch in 15 days
|
High Safety & Temperature Resistance
|
Injection Molding + PBT
|
PBT
|
Flammability V-0, 150℃ temperature resistance
|
Prototype in 7 days, batch in 25 days
|
Large-Scale Standardized Production
|
High-Speed Injection Molding + ABS
|
ABS
|
Low cost, high production efficiency
|
Prototype in 5 days, batch in 20 days
|
Smart Integration Needs
|
Secondary Processing + PC/ABS
|
PC/ABS Alloy
|
Transmittance ≥80%, sensor compatibility
|
Prototype in 7 days, batch in 30 days
|