Driven by lightweight design, chemical resistance, and cost-effectiveness, PP (polypropylene) has emerged as a mainstream material in industrial manufacturing and consumer goods due to its excellent comprehensive properties. This article systematically explores the technical logic of custom PP plastic parts, covering material characteristics, processing technologies, customization processes, and application scenarios, to provide efficient solutions for industries such as automotive, home appliances, and medical devices.
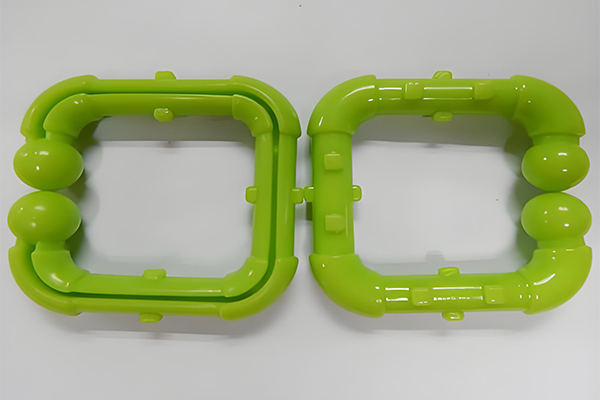
1. Material Characteristics: The Perfect Balance of Lightweight and Functionality
PP (polypropylene) forms a diverse material system through homopolymer/copolymer modification and filler reinforcement, with core properties and application advantages as follows:
1. Base Properties and Modification Directions
Property | Typical Parameters (Homopolymer PP) | Copolymer PP (20% Ethylene) | Modified PP (30% Glass Fiber) | Core Advantages | Application Value |
---|---|---|---|---|---|
Density | 0.90-0.91 g/cm³ | 0.89 g/cm³ | 1.05 g/cm³ | Lowest density among general plastics, ideal for lightweighting | Automotive lightweight components, packaging materials |
Melting Point | 165-170℃ | 150-160℃ | 165℃ | High temperature resistance (120℃ long-term use) | Microwave tableware, automotive engine components |
Tensile Strength | 30-35 MPa | 25-30 MPa | 50-60 MPa | Adjustable strength for different loads | Structural parts (modified PP), flexible components (copolymer PP) |
Low-Temperature Impact | -10℃ brittle | -30℃ no brittle fracture | -40℃ tough | Cold resistance of copolymer PP for outdoor/cold chain | Frozen food packaging, automotive low-temperature parts |
Chemical Resistance | Excellent to acids/alkalis/oils | Same as homopolymer | Same as homopolymer | Solvent resistance, food-contact safe | Pharmaceutical packaging, chemical containers |
2. Modification Technologies for Expanded Applications
- Glass Fiber Reinforcement (GF-PP):
Adding 30% glass fiber increases tensile strength by 60% and heat deflection temperature from 100℃ to 135℃, suitable for automotive battery brackets and air conditioning compressor parts. - Antistatic Modification:
Incorporating carbon black or conductive masterbatch reduces surface resistance to 10⁶-10⁹Ω, meeting ESD protection requirements (10⁸Ω) for electronic component turnover boxes. - Weather Resistance Modification:
UV absorber (e.g., UV-770) ensures tensile strength retention ≥85% after 500 hours of outdoor aging, ideal for equipment enclosures.
2. Processing Technology: Diverse Molding and Surface Treatment Solutions
1. Core Molding Process Comparison
Process | Precision (mm) | Daily Capacity (pcs) | Suitable Scenarios | Typical Parts | Key Parameter Control |
---|---|---|---|---|---|
Injection Molding | ±0.05 | 10,000-50,000 | Complex structures (gears, housings) | Automotive door handles, home appliance parts | Material temp 220-250℃, mold temp 40-60℃, shrinkage 1.0%-1.5% |
Extrusion | ±0.1 | 20,000+ | Pipes, sheets, profiles | Infusion tubes, strapping, pallets | Screw speed 30-60rpm, traction speed 5-15m/min |
Blow Molding | ±0.2 | 8,000-30,000 | Hollow containers, films | Laundry detergent bottles, hollow seats | Blowing pressure 0.5-1.0MPa, cooling time 10-20s |
Thermoforming | ±0.3 | 5,000-15,000 | Thin-walled packaging, transparent covers | Food trays, electronic screen protectors | Heating temp 160-190℃, forming pressure 0.3-0.8MPa |
2. Surface Treatment and Functional Enhancement
- Printing Processes:
- Silk/Pad Printing: Corona treatment increases adhesion 3x, passing 3M tape test (peeling ≤5%) for logo customization and labeling.
- Painting Processes:
- Polyolefin-specific paint with 50±5μm film thickness, 1000-hour QUV aging resistance (ΔE≤3) for automotive exterior color customization.
- Composite Molding:
- Two-shot injection (PP+TPE): Forms hard-soft composite structures like tool handles (PP body + TPE anti-slip layer), increasing grip force by 20%.
3. Customization Process: End-to-End Control for Efficient Delivery
1. Requirement Diagnosis (1-2 Business Days)
- Application Definition: Clarify part use (structural/aesthetic/functional), environmental conditions (temperature/humidity/contact media), and precision level (general tolerance ±0.1mm or precision ±0.03mm).
- Material Selection: Provide material proposals within 1 business day, e.g., cold-resistant copolymer PP (-30℃ impact resistance) for low-temperature use, reinforced PP for load-bearing (60% strength increase), with cost comparison (common PP $0.08-$0.16/piece, modified PP $0.20-$0.40/piece).
2. Design and Validation (5-7 Business Days)
- Structural Optimization:
Moldflow simulation optimizes filling for PP shrinkage, designing ribs (spacing ≤15mm) and uniform wall thickness (1.5-3mm recommended), controlling warpage ≤0.15mm/m. - Rapid Prototyping:
- 3D Printing (FDM): 24-hour PP prototype delivery with ±0.2mm precision for assembly verification.
- Silicone Mold Small Batch (100-piece minimum): Replicates final material properties for low-temperature impact testing (-20℃, 3 drops without damage).
3. Mass Production and Quality Inspection
- Process Control:
- Injection Molding Smart Monitoring: Pressure fluctuation ≤5%, temperature fluctuation ≤2℃, mold temperature controlled via chiller (error ±1℃) to reduce sink marks (depth ≤0.2mm).
- Extrusion Line: Online thickness gauge maintains uniformity error ≤2%, ensuring load stability for packaging materials.
- Inspection System:
Inspection Item Standard Requirements Equipment/Method Pass Criteria Dimensional Accuracy Critical dimensions ±0.05mm Coordinate Measuring Machine CPK≥1.33 Low-Temperature Performance -20℃ impact strength ≥25 kJ/m² Low-temperature impact tester 100% compliance Food Contact Safety Migration ≤0.1mg/kg HPLC analyzer FDA 21 CFR 177.1520 compliant
4. Application Scenarios: Custom Solutions for All Industries
1. Automotive Industry
- Lightweight Components:
- GF-PP engine covers with 1.05g/cm³ density, 40% lighter than aluminum, 55MPa tensile strength, and 120℃ long-term resistance for engine bays.
- Copolymer PP bumper frames with -40℃ impact strength 30kJ/m², passing GM 9506P weathering certification, 5-year outdoor durability.
- Interior Parts:
Low-gloss PP instrument panels with surface roughness Ra≤1.6μm, 500-cycle abrasion resistance, and VOC compliance (formaldehyde ≤0.1ppm).
2. Home Appliances & Consumer Electronics
- White Goods:
Heat-resistant PP washing machine drums with 35MPa tensile strength, 90℃ hot water resistance, and 500-cycle detergent corrosion resistance. - 3C Products:
Antistatic PP electronic housings with 10⁸Ω surface resistance, passing ESD ±8kV contact discharge testing to protect internal components.
3. Medical & Food Packaging
- Medical Devices:
Medical-grade PP syringes compliant with ISO 10993 biocompatibility, ≥85% transmittance, stable after gamma sterilization, and impurity particles ≤5μm (100x microscopy). - Food Packaging:
Heat-resistant PP microwave trays compliant with GB 4806.7, 121℃ autoclave resistance, and water vapor transmission ≤5g/(m²·24h) for extended food freshness.
4. Industrial & Agricultural
- Industrial Equipment:
Acid/alkali-resistant PP chemical pipes compliant with HG/T 20539, transporting 98% sulfuric acid (60℃), 15+ year lifespan, 60% cost reduction vs. stainless steel. - Agriculture:
Weather-resistant PP seedling trays with UV-531 absorber, 70% strength retention after 3 years outdoors, and hole anti-fracture force ≥50N for mechanized sowing.
5. Industry Trends & Technological Innovations
1. Sustainability and Green Development
- Bio-Based PP:
Sugarcane-derived bio-based PP with 30% bio-content, 25% lower carbon emissions, suitable for degradable packaging and eco-friendly consumer goods. - Circular Economy:
Post-consumer recycled PP (PCR-PP) retains ≥80% performance for non-food contact parts like automotive battery boxes and industrial pallets, compliant with EU CE.
2. High-Performance Modification Breakthroughs
- High Melt Strength PP:
Metallocene-catalyzed PP with 2x melt strength for thin-wall injection (0.8mm thickness), reducing material usage by 20% in lightweight food packaging. - Conductive PP:
Carbon nanotube-modified PP with surface resistance ≤10⁶Ω and shielding effectiveness ≥40dB (1GHz), replacing metal for 5G EMI shields with 70% weight reduction.
3. Intelligent Manufacturing Upgrades
- Digital Twin Molds:
AI-optimized gate location reduces trial molds by 50%, shortens mold development to 18 days, and improves dimensional accuracy to ±0.03mm. - Green Production:
Electromagnetic induction heating saves 30% energy, with 95% scrap recycling rate, compliant with ISO 14001 environmental management.
6. Frequently Asked Questions (FAQ)
Q1: What is the temperature range for PP parts?
A: Homopolymer PP withstands ≤120℃ long-term, copolymer PP ≤100℃, GF-PP up to 135℃, with short-term resistance up to 160℃—suitable for most industrial and consumer applications.
A: Homopolymer PP withstands ≤120℃ long-term, copolymer PP ≤100℃, GF-PP up to 135℃, with short-term resistance up to 160℃—suitable for most industrial and consumer applications.
Q2: How to improve printability on PP surfaces?
A: Corona treatment (surface tension ≥38dyn/cm) or flame treatment, combined with polyolefin-specific inks, achieves adhesion grade 4B (ISO 2409).
A: Corona treatment (surface tension ≥38dyn/cm) or flame treatment, combined with polyolefin-specific inks, achieves adhesion grade 4B (ISO 2409).
Q3: What certifications are needed for food-grade PP?
A: Requires FDA 21 CFR 177.1520, EU EU 10/2011, and China GB 4806.7, ensuring total migration ≤10mg/dm² for food contact.
A: Requires FDA 21 CFR 177.1520, EU EU 10/2011, and China GB 4806.7, ensuring total migration ≤10mg/dm² for food contact.
Q4: What’s the minimum order quantity for small batches?
A: 500 pieces minimum, using quick aluminum molds (7-day lead time), 15% higher cost than steel molds—ideal for samples and small-scale trials (e.g., 1,000 pieces at ~$0.16/piece).
A: 500 pieces minimum, using quick aluminum molds (7-day lead time), 15% higher cost than steel molds—ideal for samples and small-scale trials (e.g., 1,000 pieces at ~$0.16/piece).
7. Customer Testimonial
“Collaborating with the team for 30,000 automotive copolymer PP 卡扣 (clips), we achieved delivery in just 35 days. Parts retained 95% clamping force at -30℃, with dimensional tolerance ±0.04mm, passing 800-hour weathering testing for automotive OEMs. Mold cooling optimization shortened cycle time by 20%, yielding 98% good parts. Their professional material selection and fast delivery provided a reliable lightweight solution for our new project!” ——An Automotive Parts Supplier
Start Your Customization Journey Today
Whether for automotive lightweight components, food-grade packaging, or weather-resistant industrial parts, we leverage PP material expertise and intelligent processes to deliver end-to-end solutions. Contact us for a tailored proposal and unlock the versatile potential of PP parts—where lightweight meets reliability.