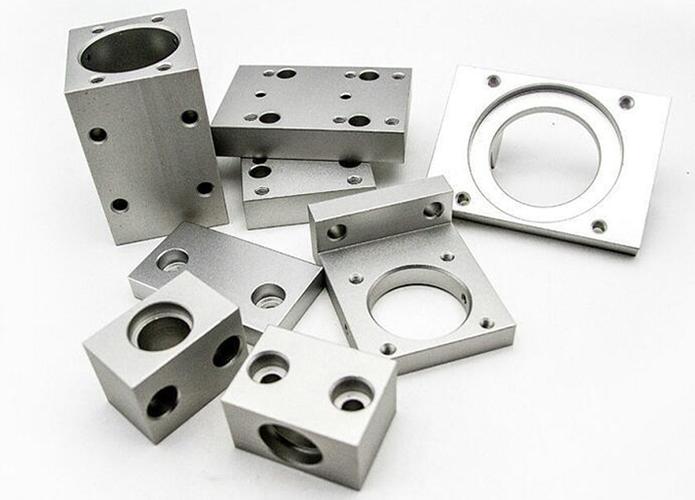
Core Processing Technologies: Engineering for Micron-Level Precision
1. Multi-Axis CNC Milling
- 5-axis simultaneous milling: Machines complex 3D surfaces and undercuts (e.g., aerospace turbine blades with 12° tilted cooling holes) in one setup, reducing alignment errors to ≤0.002mm. A medical device housing with 7 asymmetric mounting points achieved ±0.003mm position tolerance, ensuring perfect component fit.
- 3+2 axis milling: Optimizes production of semi-complex parts (e.g., automotive engine brackets) by fixing multi-angle features, cutting cycle time by 35% vs. 3-axis methods. A 200mm-long aluminum bracket with 5 inclined holes maintained ±0.005mm dimensional stability.
- High-speed CNC milling: 40,000 RPM spindles machine thin-walled features (0.3mm thickness) on titanium parts without deformation, achieving Ra 0.05μm surface finish—critical for lightweight aerospace components.
2. Precision Workholding & Fixturing
- Custom jig design: Engineers create dedicated fixtures with ±0.001mm locating accuracy to secure irregularly shaped parts during milling. A stainless steel valve body fixture ensured ≤0.002mm runout, maintaining consistent port alignment across 10,000+ units.
- Vacuum clamping: Holds thin-walled plastic and metal sheets (0.5-2mm thickness) flat during milling, reducing warpage by 80% vs. mechanical clamping. A 300mm × 200mm aluminum panel for electronics achieved 0.01mm flatness after machining.
- Pallet systems: Automated 100+ station pallet changers enable 24/7 unmanned production of small parts (e.g., sensor housings), with ≤0.003mm repeatability between setups.
3. High-Precision Cutting Tools & Strategies
- Micro-grain carbide tools: Maintain sharp edges during high-speed milling of hardened steel (up to 50HRC), achieving Ra 0.02μm surface finish on bearing seats. A 50mm-diameter stainless steel bearing race produced this way required no post-polishing.
- Adaptive machining: Sensors adjust feed rates and depths of cut in real-time when milling uneven material blanks (e.g., castings), ensuring consistent dimensional accuracy (±0.005mm) across 1,000+ parts.
- Trochoidal milling: Reduces tool wear by 50% when machining tough materials (e.g., Inconel 718), extending tool life to 300+ parts per edge for cost efficiency.
4. Metrology & Quality Control
- In-process CMM inspection: Coordinate measuring machines with 5-axis probes verify critical dimensions during machining, catching deviations early (±0.001mm tolerance) and reducing scrap rates to ≤0.1%.
- Laser scanning: Captures 3D surface data of complex parts (e.g., turbine impellers) with 0.005mm point spacing, comparing results to CAD models for full surface analysis. A 150mm-diameter impeller achieved 99.9% geometric conformity.
- Surface finish testing: Profilometers measure Ra (0.01-1.6μm) and Rz values to ensure functional performance—e.g., Ra 0.05μm on hydraulic valve spools to minimize friction and pressure loss.
Material Expertise: Matching Materials to Machining Requirements
Material
|
Key Properties
|
Application
|
Advantages
|
Aluminum Alloy (6061-T6, 7075-T6)
|
Excellent machinability, 310-572MPa tensile strength
|
Aerospace brackets, automotive components
|
Achieves Ra 0.05μm surface finish; 30% lighter than steel.
|
Stainless Steel (304, 316L)
|
Corrosion resistance, 515MPa tensile strength
|
Medical devices, marine hardware
|
Withstands 1,000+ hours salt spray; suitable for hygienic environments.
|
Titanium Alloy (Ti-6Al-4V)
|
High strength-to-weight ratio, 895MPa tensile strength
|
Aerospace parts, high-stress components
|
45% lighter than steel; maintains strength at 300℃.
|
PEEK (Engineering Plastic)
|
Heat resistance (260℃), chemical resistance
|
Medical instrument parts, insulators
|
Machines to Ra 0.1μm; biocompatible (ISO 10993).
|
Precision CNC Milled Parts Manufacturing Process
- Design & DFM: Engineers analyze client 3D models (STEP/IGS) to optimize toolpaths and fixturing—e.g., adding 0.2mm radii to sharp corners of a medical part to prevent tool breakage and improve fatigue resistance.
- Programming: CAM software generates high-precision toolpaths with 0.001mm stepover for 3D surfaces, simulating machining to detect collisions and optimize cutting parameters.
- CNC machining:
-
- Roughing: Removes 90% of material with high feed rates (1000mm/min) to reduce cycle time.
-
- Finishing: Uses micro-grain tools at high RPM (30,000+) to achieve final dimensions and surface finish.
- Post-processing: Deburring (≤0.01mm edge radius), heat treatment (for metal parts), and surface coating (anodizing, plating) applied per requirements.
- Quality validation: CMM inspection (±0.001mm), laser scanning, and functional testing ensure compliance with ISO 2768-1 (fine grade) and client specs.
Custom Precision CNC Milled Parts Application Fields
- Aerospace industry: 7075 aluminum aircraft structural brackets (±0.002mm tolerance), titanium engine components (withstand 300℃).
- Medical equipment: 316L stainless steel surgical instrument parts (Ra 0.02μm surface finish), PEEK MRI-compatible components.
- Automotive sector: 6061 aluminum transmission housings (leak-proof at 10bar), stainless steel sensor mounts (vibration-resistant).
- Electronics: Aluminum heat sinks (±0.01mm flatness for thermal contact), PEEK insulators (electrical isolation).
Customization Capabilities: From Prototype to Mass Production
- Complex geometry customization: Machines parts with undercuts (up to 45°), thin walls (≥0.3mm), and micro-features (0.1mm holes) via 5-axis technology—e.g., a microfluidic chip with 50μm channels for medical diagnostics.
- Material-specific machining: Optimizes parameters for each material (e.g., 150m/min cutting speed for aluminum vs. 50m/min for titanium) to balance efficiency and tool life.
- Production scalability: 1-100 prototypes (2-3 days) via high-speed milling; 1,000-50,000+ units/month with automated cells (e.g., 30,000 aluminum brackets for automotive suppliers).
Common Processing Questions
- Q: How to achieve 0.001mm tolerance on a 200mm-long aluminum part?
- Q: What’s the lead time for 1,000 precision titanium parts with complex 3D contours?
- Q: Can you machine parts with both metal and plastic components (hybrid assemblies)?
- Q: How to reduce surface roughness on stainless steel parts below Ra 0.05μm?